Registration of public notification
If you register your e-mail address, we will notify you when the latest issue is published. If you wish, please register from the registration form. To delete your registration, please visit here.
April 2025 No.100
At Sumitomo Electric Industries, Ltd., the Industrial Materials Group is only one of five business segments that was organized according to our product category: materials, rather than market. Therefore, it is difficult to find consistency in customers, market, application, and research and development (R&D) direction in each business area. On the other hand, there is a commonness in that each industrial materials division tries to make the materials and their quality unique and thus to differentiate these materials from the products of our competitors. In the development of new materials, the responsible divisions are also common in approaching the R&D projects scientifically and efficiently by employing computational science, machine learning, and other tools, which will be discussed later. At the occasion of the publication of this special issue on industrial materials, I briefly describe the history and future direction of development in each of our businesses with a focus on materials.
1.5 MB
High-strength materials like titanium alloys and heat-resistant alloys are difficult-to-cut materials. They are used in industries such as aerospace and medical sectors, where the demand for high-quality processing and efficiency is increasing. For these demands, we have developed next-generation ultrafine-grained cemented carbide for difficult-to-cut materials. We successfully improved the interface strength between hard-phase particles to prevent damage from particle detachment and reduce wear in high-efficiency machining by enhancing the binder phase strength. By integrating these two technologies, we have achieved longer tool life in cutting difficult-to-cut materials. At the occasion of the publication of this special issue on industrial materials, I briefly describe the history and future direction of development in each of our businesses with a focus on materials.
6.3 MB
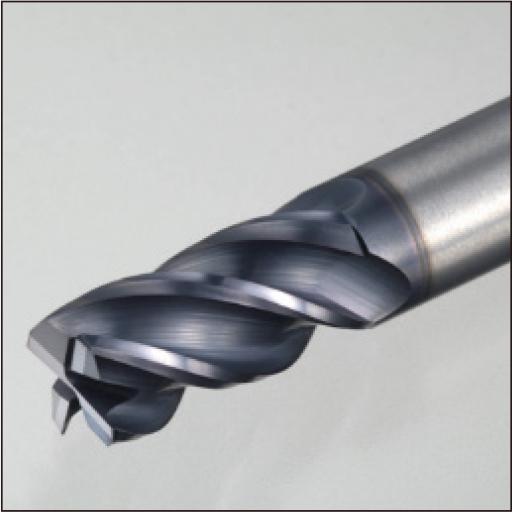
6.3 MB
During cutting processes, cutting edges cannot be directly observed, leading to reliance on skilled workers' intuition and experience for optimizing cutting conditions. In recent years, sensors equipped in machine tools have been utilized to comprehensively monitor machining conditions including cutting forces. However, their sensitivity and accuracy are insufficient due to distance between the cutting point and measurement position. To address this challenge, we have developed “Sumi Force,” a sensing tool that measures cutting forces in real-time by embedding strain sensors in the tool holder, where inserts, drills, or end mills are held, closest to the cutting point. The measured data is wirelessly transmitted outside the machine tool, enabling easy integration to various machines and production lines used by customers. This paper introduces a new solution service that utilizes “Sumi Force” to optimize machining processes for customers, and discusses the development of techniques to detect anomalies such as tool wear and breakage based on changes in cutting force.
3.8 MB
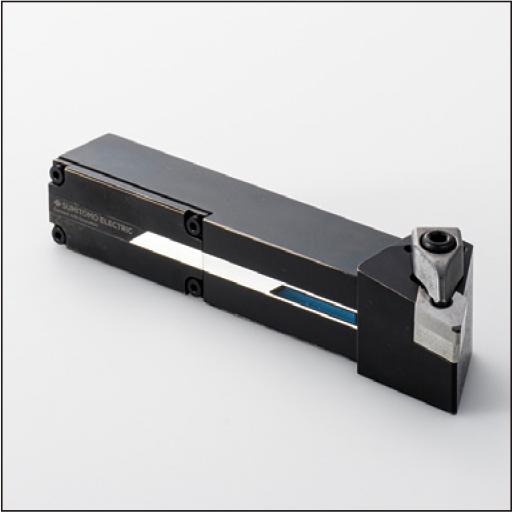
3.8 MB
Cutting tool requirements change from year to year. In the automotive industry, the shift to electrification is increasing the demand for lightweight tools that enable highly efficient machining of aluminum alloy components. In the aerospace industry, the use of difficult-to-machine materials such as nickel-based alloys and titanium alloys to reduce engine noise and fuel consumption is increasing, as is the need for through-coolant tools that can efficiently cool cutting edges when machining these materials. In response to these shifting market demands, we are employing additive manufacturing (AM) to develop innovative cutting tools. This time, by utilizing AM to form a complex internal structure, we have realized a lightweight cutter for aluminum machining that maintains the rigidity of the cutting edge while reducing the weight. Additionally, we have developed a cutter for difficult-to-cut materials that enables uniform cooling of the entire cutting edge by optimizing the internal flow path.
6.2 MB
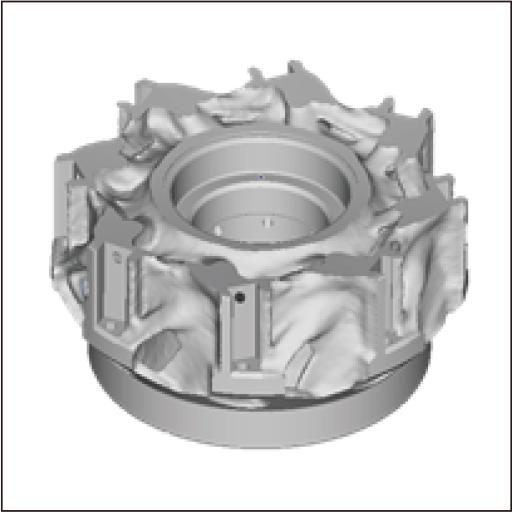
6.2 MB
In recent years, various industries, including the automotive sector, have been advancing their initiatives toward achieving green transformation (GX) by reducing CO2 emissions in cutting processes. Decreasing CO2 emissions involves cutting machine power consumption, leading to a rising demand for high-efficiency machining tools that reduce machine cycle time. To meet these requirements, we have developed the MULTIDRILL MDA Series for aluminum drilling and the MULTIDRILL MDH Series for steel and cast iron drilling. The MDA series enables high-precision, high-efficiency aluminum machining, while the MDH series delivers high-efficiency machining with reduced cutting force and power consumption for steel and cast iron processing. These tools contribute to power-saving in hole making processes.
6.1 MB
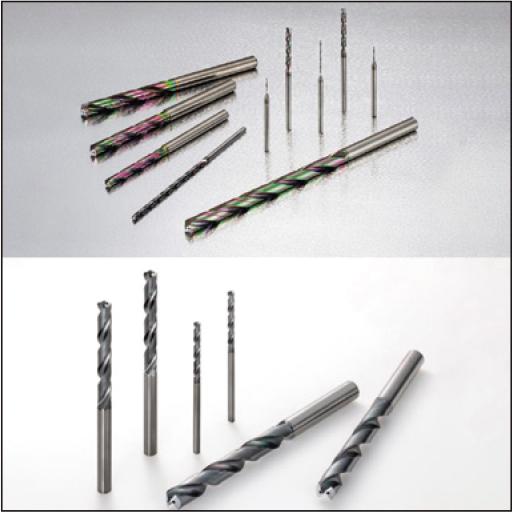
6.1 MB
Efforts are underway in the steel machining, particularly in the automotive industry, to reduce the environmental impact and to enhance resource efficiency. We introduced the AC8000P series for steel turning in 2016, featuring the new chemical vapor deposition (CVD) coating technology “Absotech,” and have since expanded our product range. In recent years, there has been a growing trend in steel turning especially toward reducing machining time and transitioning to dry cutting without the use of cutting fluids. In response to this trend, we have developed AC8115P, a new steel turning carbide grade designed for high-efficiency and dry cutting applications. AC8115P demonstrates outstanding performance by addressing the challenges of high cutting-edge temperatures, effectively minimizing tool wear and plastic deformation. This grade’s enhanced resistance characteristics are key to reducing machining costs and environmental impact in steel turning operations.
7 MB
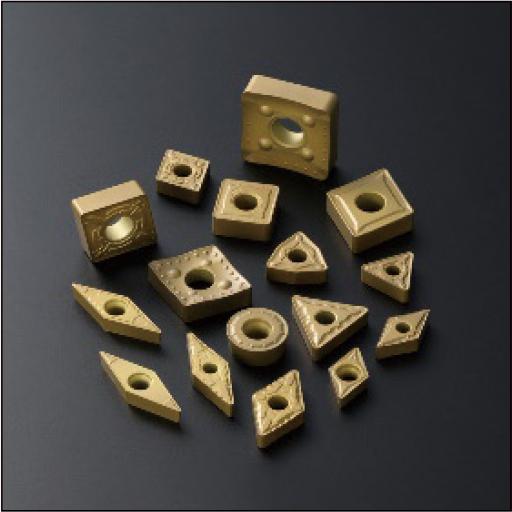
7 MB
Titanium alloys are widely used for equipment and parts in the aerospace industry due to their lightweight, high strength and excellent corrosion resistance. Additionally, these alloys are also used in the medical field because of their high biocompatibility. In recent years, both industries have experienced significant growth, leading to a marked increase in demand for cutting tools for these alloys. However, when machined, titanium alloys are prone to adhesion due to chemical reactions with tools and heavy wear resulting from low thermal conductivity, leading to a significant reduction in cutting tool life. Thus, the demand for cutting tools with stable performance and a long tool life has been increasing. The newly developed "AC9115T" and “AC9125T” are designed to improve wear resistance by applying a new physical vapor deposition (PVD) coating. These coated carbide grades help reduce the frequency of cutting edge replacement and tool consumption by extending the tool life, contributing to the reduction of machining costs.
7.9 MB
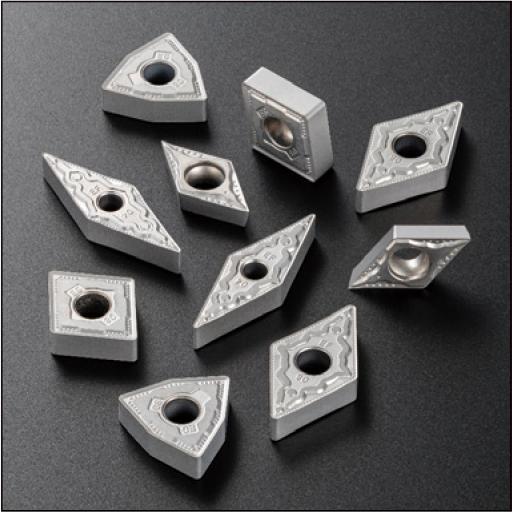
7.9 MB
The cubic boron nitride (CBN) cutting tool “SUMIBORON” is made of sintered cBN particles, which have high hardness and thermal conductivity next to diamond and low reactivity with ferrous metals, bonded with a metal and/or ceramic binder. It has contributed to the improvement of machining efficiency and cost reduction in processing hard-to-cut hardened steel, and in machining of cast iron and sintered alloy where high-precision machining is required. In recent years, the machining of cast iron and sintered alloy parts—key components in automotive and construction machinery—has seen increasing demand for stability, long tool life, and high efficiency. In addition to high dimensional accuracy and surface quality, there is also a growing need for manpower savings in production lines and the manufacturing of high-precision parts. In response to the demand, we have developed CBN cutting tools SUMIBORON BN7115 and BN7125. BN7115 is designed for finishing, offering improved chipping resistance for stable, high-quality surface machining, while BN7125 is designed for general-purpose use, with enhanced breakage resistance for stable, long tool life even under heavy cutting loads. This report describes the features and performance of BN7115 and BN7125.
2.7 MB
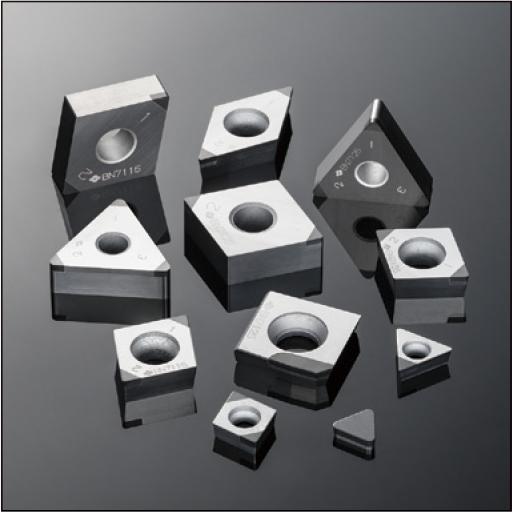
2.7 MB
SUMIBORON is a cutting tool that utilizes cubic boron nitride (CBN) sintered bodies formed from cBN particles and ceramic or metal bonding materials. Specifically, coated SUMIBORON has an expanded application range as a cutting tool for hardened steel in automotive parts. Recently, manufacturing sites have become aware of variable-volume production due to the diversification of parts and the importance of environmental considerations. Two trends have emerged: reducing CO2 emissions by lowering equipment power consumption and establishing automated product lines to address price competition. Cutting tools require higher efficiency and longer tool life. To meet customer requests, we developed four new grades in the BNC2100 series: BNC2105, BNC2115, BNC2125, and BNC2135.
2.8 MB

2.8 MB
The tensioning process of prestressing steel strands involves introducing the required prestressing force into concrete structures, which is a critical step affecting the structure's durability. Traditionally, this process involved manual operation of tensioning equipment for prestressing steel strands and visual readings of analog gauges for recording, leading to challenges such as labor-intensive processes, measurement errors, and the need for proximity to tensioning equipment. The automatic tension control system automates these tasks using control devices and digital measuring instruments, contributing to reduced manual labor, enhanced accuracy, and improved safety. This paper provides an overview of the wireless automatic tension control system that eliminates the need for communication cable wiring, along with examples of its application and benefits.
5.6 MB
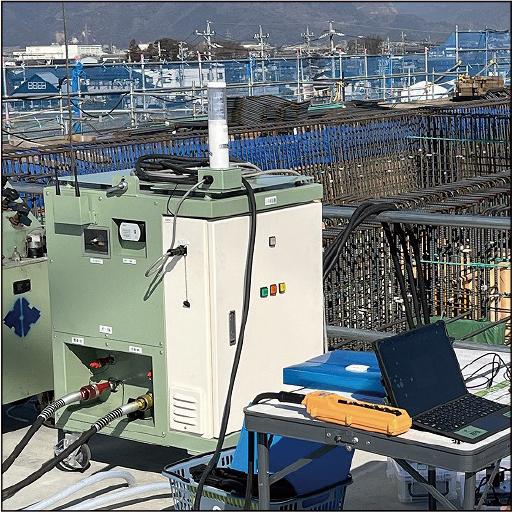
5.6 MB
Steel cords, used as reinforcement in rubber products, are essential components for automotive tires that require high standards of fuel efficiency, durability, handling stability, and noise reduction. Conventionally, the development process involved repeated experiments, evaluations, and modifications to ensure the steel cords meet the required tire performance levels. However, this approach posed challenges such as extended development periods due to the time and effort required for evaluations, difficulties in achieving sustainable society due to tire waste, and the influence of tire design factors on tire performance. To address these issues, we developed a performance prediction technology that incorporates steel cord features. This technology enables efficient and accurate examination, specification refinement, and narrowing-down and evaluation of technical interpretation in tire design involving steel cords. The technology not only enhances tire performance but also contributes to achieving the Sustainable Development Goals, earning high praise from our customers.
3 MB
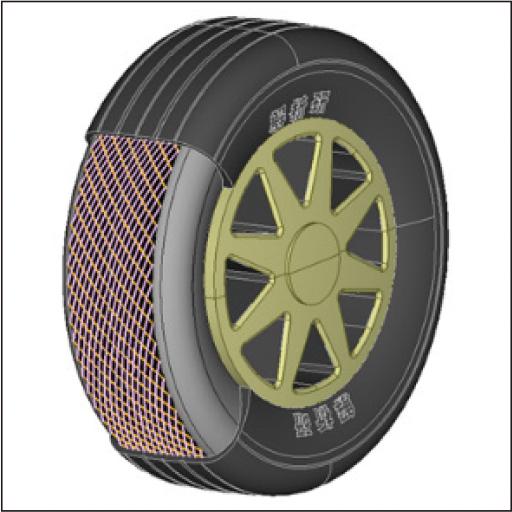
3 MB
We assessed the application of high-strength steel wires (spring wires) for creating safe and efficient blades for grass cutters. Utilizing our specially shaped wires, blades were produced and tested in the fields of the National Agriculture and Food Research Organization (NARO) using both grass trimmers and remote-controlled grass mower. By changing the steel wire's cross-sectional shape from a simple square to a pentagon with sharp apexes, we achieved cutting performance comparable to traditional chip saws. The remote-controlled grass mower successfully showed its performance in cutting down bushes and woody plants with diameters over 10 mm, which was impossible with nylon cords. Introducing a freely rotating attachment for the cutting blade prevented fatigue failure of the steel wire blade and eliminated the risk of “kickbacks.” However, during stone skipping tests, significant stone scattering occurred, and the attachment part showed weakness in impact resistance against hard objects, prompting us to propose solutions for these challenges.
9.4 MB
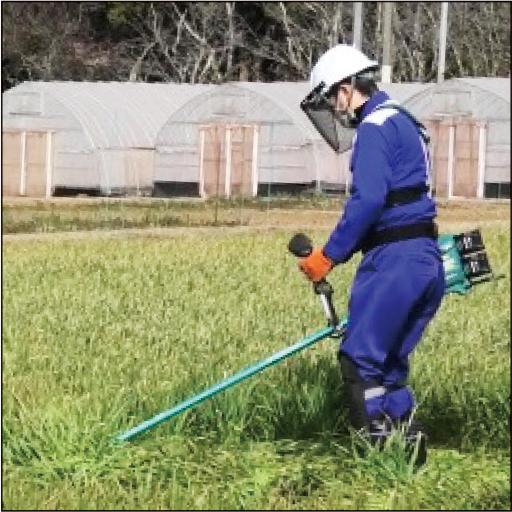
9.4 MB
To achieve carbon neutrality, it is necessary to reduce CO2 emissions and increase the amount of CO2 absorption simultaneously. One method to increase CO2 absorption is through carbon recycling, which involves the production of functional materials and iron carbonate (trademark: metacol), using iron and CO2, which have an affinity with our manufacturing sites. This paper reports on this method. We aim to utilize iron carbonate in our own products, incorporating the emitted CO2 into material circulation and continuously isolating it from the atmosphere. Through principle verification, functional evaluation, equipment design, factory verification, and intellectual property protection, we will proceed to validate customer value. We will confirm achieving a negative CO2 balance and profitability, and aim to contribute to carbon neutrality through carbon recycling.
1.2 MB
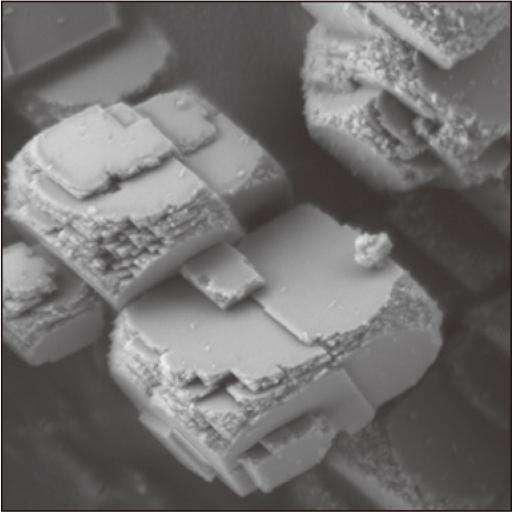
1.2 MB
Iron-based sintered parts have traditionally been used as structural components across various fields due to their ability to be efficiently net-shaped into complex shapes using powder compacting technology, leveraging the excellent balance of strength and cost that iron offers. In recent years, the demand for smaller, lighter, high-strength, non-magnetic materials has been on the rise in sensing technology required for further advancements like electric vehicles, high-performance appliances, and smart factories. In response to these trends, we have developed a new non-magnetic, high-strength iron-based sintered material that goes beyond existing materials. This paper discusses the characteristics and benefits of this newly developed material.
1.7 MB
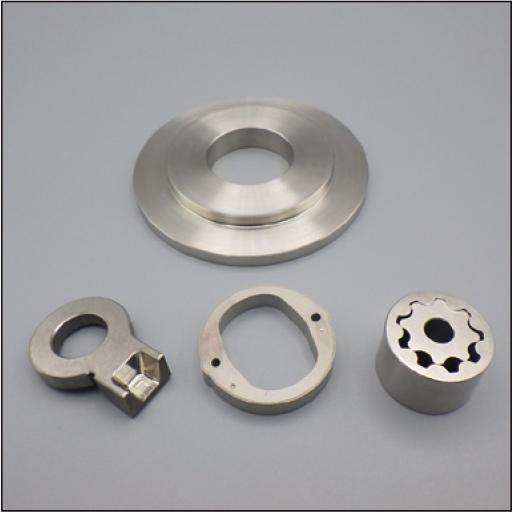
1.7 MB
We have developed soft magnetic composites (SMCs) and an axial flux machine (AFM) utilizing SMCs to contribute to the advancement of a sustainable society. The estimated CO2 emissions from SMC manufacturing are approximately one-quarter of those produced during magnetic steel sheet manufacturing. Additionally, we have developed a recycling technology that allows for the reuse of powdered motor stator as raw material for SMCs while demonstrating consistent magnetic properties before and after recycling. Furthermore, our innovative design of a 75 kW-class AFM with a power density of 12.6 kW/kg illustrates the effectiveness of SMCs and AFM in reducing material usage. Finally, we have confirmed that our 20 kW-class AFM, which incorporates low CO2 emission ferrite magnets, matches the size, power, and efficiency of a radial flux machine utilizing Nd sintering magnets.
4.7 MB
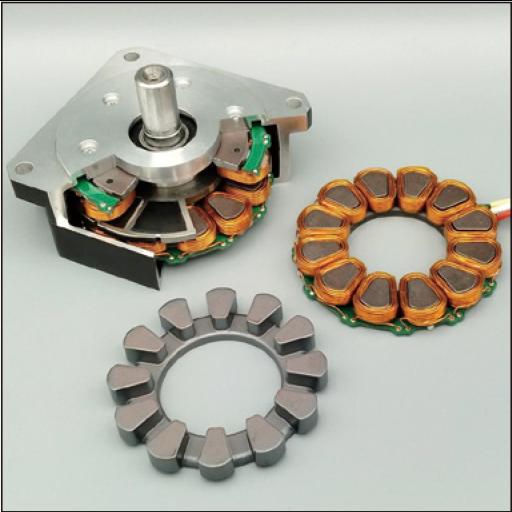
4.7 MB
Powder metallurgy involves compressing powder in a mold and sintering it to strengthen compact parts. Through innovative mold designs, near-net-shape compacts that closely resemble the final product can be achieved. Parking support parts are found in various vehicle types, including hybrids and electric cars as well as gasoline cars, and are crucial components used in parking lock systems to prevent wheel rotation during parking, with diverse shapes. We successfully developed parking support parts utilizing the shape flexibility of powder metallurgy, contributing to the growth of the sintering market. Our development includes examples like adjusting density balance by removing excess powder, compacting two different shapes, creating horizontal grooves, and integrating multiple components. Additionally, the use of partial laser hardening has enabled precise production while promoting environmentally friendly manufacturing practices.
2.2 MB
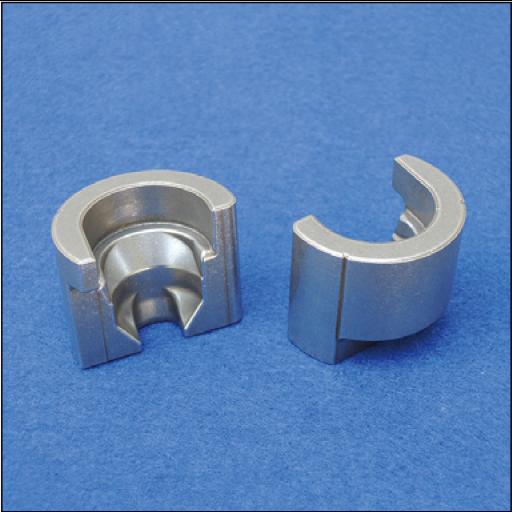
2.2 MB
Research on fusion energy, a key contender for achieving decarbonization, is becoming increasingly active. Tungsten (W) is used in the divertor of fusion reactors, which is exposed to extreme temperatures exceeding 2000°C. The DEMO-Reactor, designed to demonstrate power generation, is expected to operate for extended periods, requiring increased mechanical durability from W materials used in fusion reactors. In collaboration with universities and other institutions, A.L.M.T Corp. has evaluated various materials and has found the effectiveness of potassium (K)-doped W. Aiming to apply the findings to plasma-facing components, we have developed K-doped W thick plates tailored for this specific application. This paper reports the evaluation results of the main characteristics of these materials.
3.3 MB
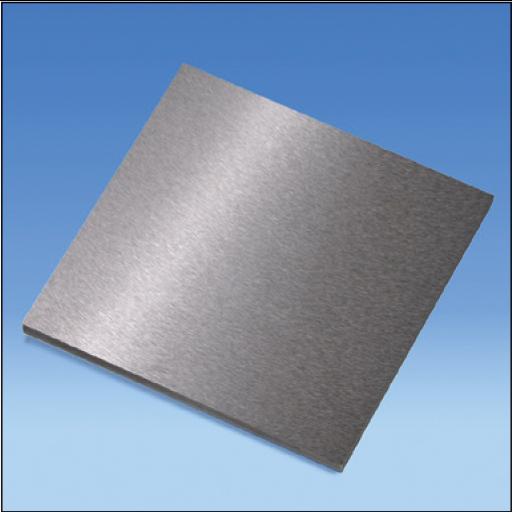
3.3 MB
Sumitomo Riko Company Limited has successfully developed a water-soluble coating material with a high filling of "silica aerogel," a highly insulating material, and created a thin film high insulation material. This material has the highest level of insulation performance through air insulation and can exhibit its performance even when the thickness is 1 mm or less. In recent years, there has been a growing trend of increasing heat generation density in electronic devices and batteries due to their high integration and miniaturization. Therefore, we are considering applying this material to contribute to thermal management. Additionally, it is attracting attention as a product that can enhance the thermal efficiency of factory facilities and contribute to the reduction of energy consumption such as fuel and electricity, thanks to its easy application. It has already been adopted in the manufacturing industry.
2.8 MB
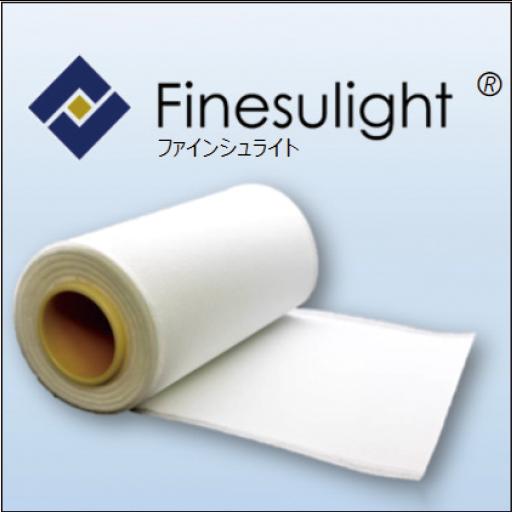
2.8 MB
In the U.S., the increase in pedestrian fatalities has led to a rising demand for pedestrian detection sensors in systems aimed at preventing traffic accidents. However, many existing sensors lack sufficient vertical detection range since they are typically installed at high positions in actual intersections, creating blind spots directly below them. In cases where the installation point is adjacent to a pedestrian crossing, there are instances where parts of the crosswalk or waiting area may go undetected. To address this issue, we have prototyped a fusion sensor combining radar with a camera. The fusion sensor eliminates blind spots below it by detecting pedestrians at the spots with the camera. Furthermore, using object recognition AI with camera images enables the sensor to identify the type of detection targets, a challenge for radar alone. This paper introduces the prototyped fusion sensor configuration and presents the results of performance verification experiments.
7.3 MB
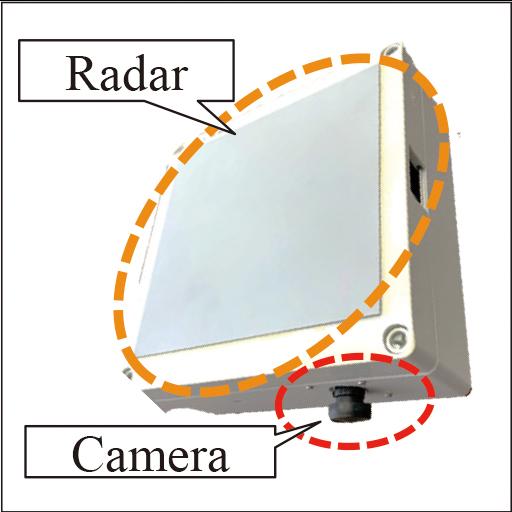
7.3 MB
Our company is developing Analog Radio-over-Fiber (A-RoF) technology for wireless signal transmission, enabling the transmission of radio waves through optical fiber while maintaining their waveform for 5G and 6G wireless communication. This paper introduces our efforts in developing A-RoF technology, focusing on enabling the economically viable deployment of millimeter-wave (mmWave) radio communication systems , which are essential for broadband wireless communication in the eras of 5G and 6G. Additionally, we showcase the application of A-RoF technology in the 5G millimeter-wave distributed antenna system (DAS) and industrial 5G terminals supporting millimeter-wave communications.
2.1 MB
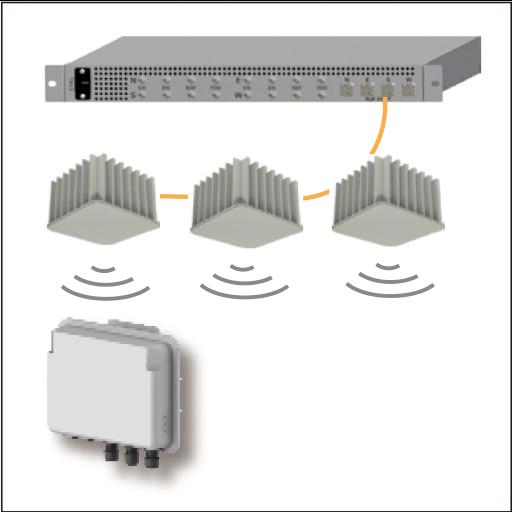
2.1 MB
Nisshin Ion Equipment Co., Ltd. has pioneered the development of “KYOKA,” the world's first mass-production material modification equipment for semiconductor device manufacturing. By combining our high-current large-area ion source technology with advancements in low-energy ion beam transport efficiency and the development of stable metal ion sources, we have successfully developed this innovative equipment. The use of this equipment is expected to advance semiconductor microfabrication technology and enhance device performance. This paper provides an overview of the demand for material modification, the structure and features of the equipment, and presents experimental results utilizing the equipment.
1.2 MB
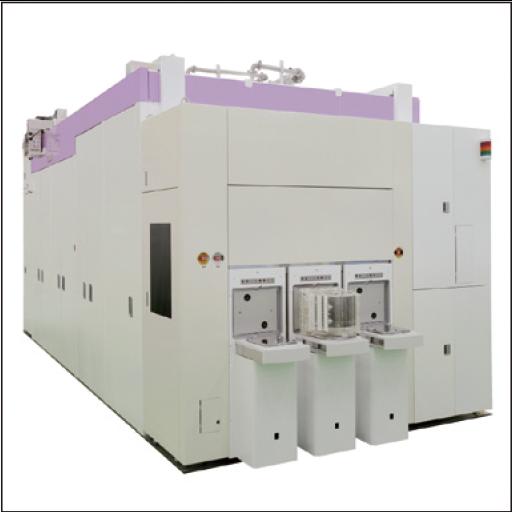
1.2 MB
Fluoropolymers have excellent properties such as heat resistance, chemical resistance, and low friction. However, their susceptibility to wear has been a significant drawback. The cross-linked fluoropolymer FEX, developed using electron beam crosslinking technology, has significantly enhanced wear resistance and paved the way for its use as a sliding material. In the past, application to general molded products was challenging due to the requirement for electron beam irradiation in a molten state exceeding the resin's melting point, causing to deformation of the molded shape. This paper presents recent insights into the utilization of FEX technology for such molded applications.
4.2 MB
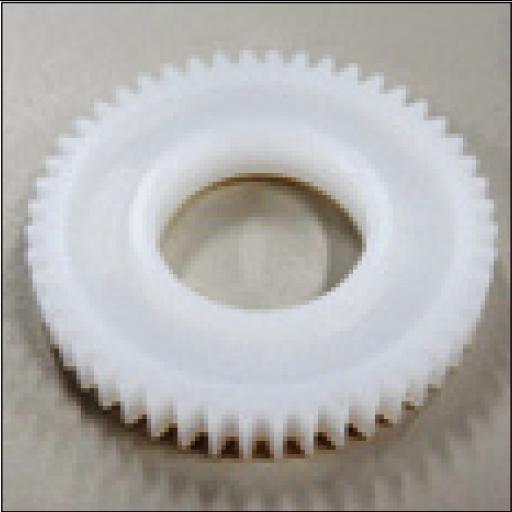
4.2 MB
Evaluating the performance of electric cable products under external forces, such as bending, is crucial for assessing their behavior in real-world environments. We utilize a cutting-edge X-ray computed tomography (XCT) system to observe the effects of external forces and employ various data analysis techniques to enhance our understanding of how cable products respond dynamically to these forces. The first part of this paper introduces XCT observation results of some samples, including a bent cable and a large 1-meter sample, which were previously difficult to evaluate with former XCT systems. The latter part focuses on image analysis techniques for bent cable products, highlighting our unique technology. Through a combination of advancements in hardware and software, we can improve design processes and solve quality issues by clarifying the dynamic behavior of various cable products under external forces.
3.5 MB
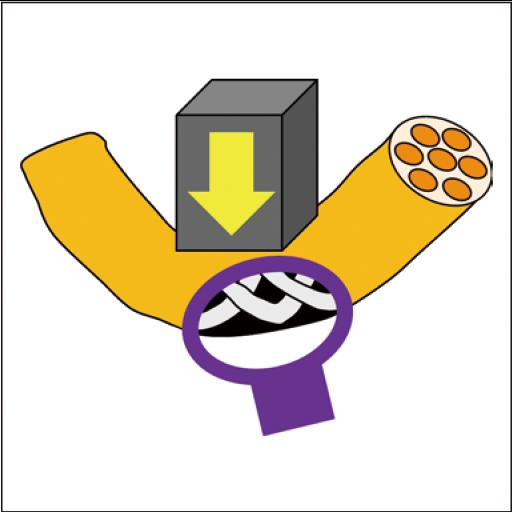
3.5 MB
For the first time for a local power utility established by a municipality, a redox flow battery system was delivered to Kashiwazaki Ideal & Realistic Energy Co., Ltd. located in Kashiwazaki City, Niigata Prefecture. As the introduction of renewable energy expands, it is expected that the introduction of long-duration energy storage (LDES) with a capacity of 6 hours or more will accelerate in the future. This installation is an example of an LDES connected directly to the power grid.
1.5 MB
In the firing process of magnets, ceramics, and other materials, many setter plates for firing, which are manufactured from molybdenum plates and rods, as well as heaters and reflectors for high-temperature furnaces are used. To improve the quality of fired products, there is an increasing demand for molybdenum mesh (mesh material) for venting during firing and preventing the sticking of the setter plate to the fired products. This mesh material is fabricated using wires of 0.5 mm or less in diameter. This paper introduces “mesh with edge folded” and “mesh with improved resistance to breakage,” both designed to address the problems of “fraying” and “breakage due to high-temperature use” observed in practical applications, as along with standard molybdenum mesh.
1.3 MB
Copyright of the paper contained in SUMITOMO ELECTRIC TECHNICAL REVIEW belongs to Sumitomo Electric Industries, Ltd.
The paper is to be used solely for private, reference purpose, and reproduction without the permission of the copyright holder is prohibited.
Meet the Authors of the SUMITOMO ELECTRIC TECHNICAL REVIEW
We at Sumitomo Electric Group are driven to pursue technological innovations to create value for a better world.
Learn more