Quality and Customer Satisfaction Improvements
Basic Concept
The Sumitomo Electric Group aims to provide safe, reliable and high-quality products to customers in a stable manner as a fundamental principle based on customer-oriented and quality-oriented policies. To continue to achieve this, our group works to strengthen its underlying manufacturing competence and continuously makes steady efforts to systematize daily duties as a mechanism, implement them soundly and further improve the mechanism.
The Company set up the Monozukuri development committee as a Group-wide organization to enhance the manufacturing competence and promotes activities under its basic policies including participation of all employees and continuous improvement.
As part of the efforts to systematize quality-related operations, we established the Sumitomo Electric Group Quality Management Global Standards, which are basic rules on quality to be applied to all divisions in the Group. Our divisions continue to strive to develop their quality assurance systems and strengthen quality assurance functions in line with those rules.
Structure
Matters related to quality in the Sumitomo Electric Group are discussed and decided upon by the Corporate Quality Control Committee. The resolutions are discussed at the CQO* Conference and the QR-1 Promotion Conference organized by the Quality Management Division and then disseminated to divisions and affi¬liates in Japan and overseas through the chief quality offi¬cers (CQO). In collaboration with the CQO of each division, we will promote the strengthening of quality-related governance, the development of a quality assurance system and the enhancement of quality assurance functions in the Group.
*CQO: CQO stands for Chief Quality Officer, who is a person representing each division to be responsible for quality assurance (and also serves in the Quality Management Division). In principle, the General Manager of the Quality Assurance Department in the hub of the business unit assumes the position.
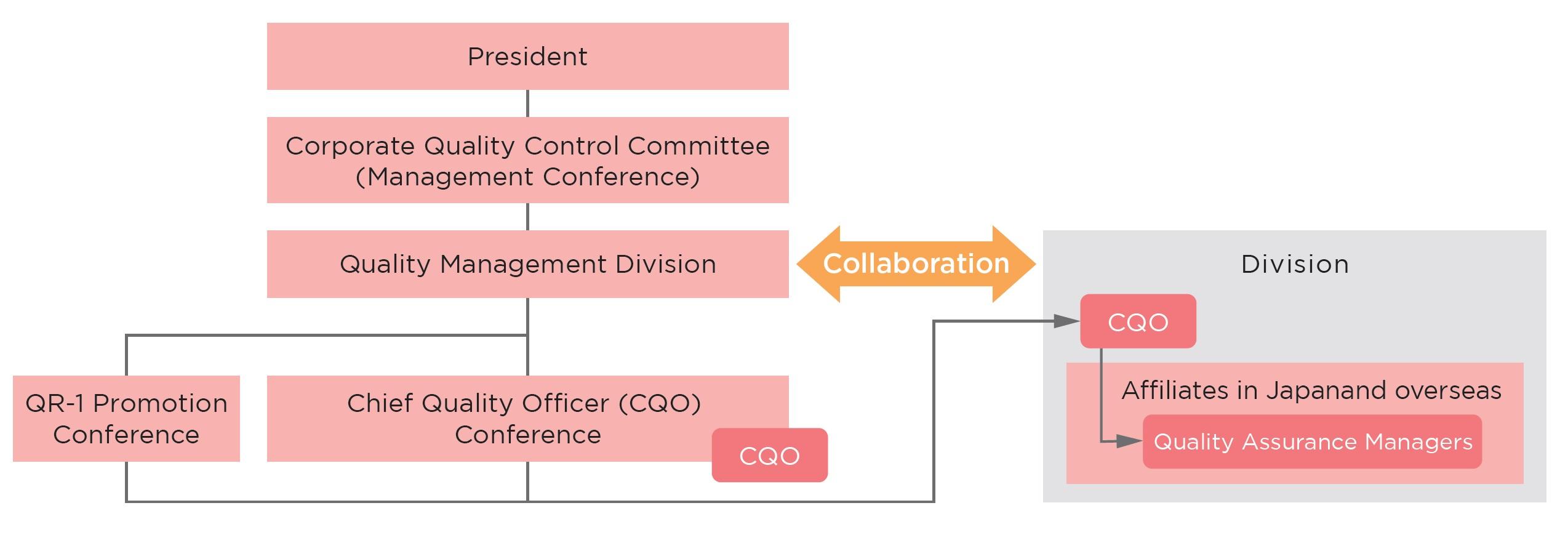
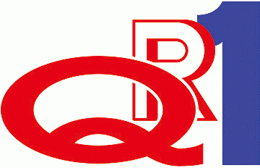
Development of QR-1 Campaign
As customer demands for quality become more and more stringent, the Sumitomo Electric Group is developing the QR-1Campaign, a company-wide quality improvement activity, under the slogan “Aim to be the number one company for our customers by reviewing our overall operations from the customer’s perspective and improving our Q (quality) and R (reliability) structure.” In this campaign, the QR-1 Promotion Council discusses, sets and works on priority issues for the Group that correspond to the current situation.
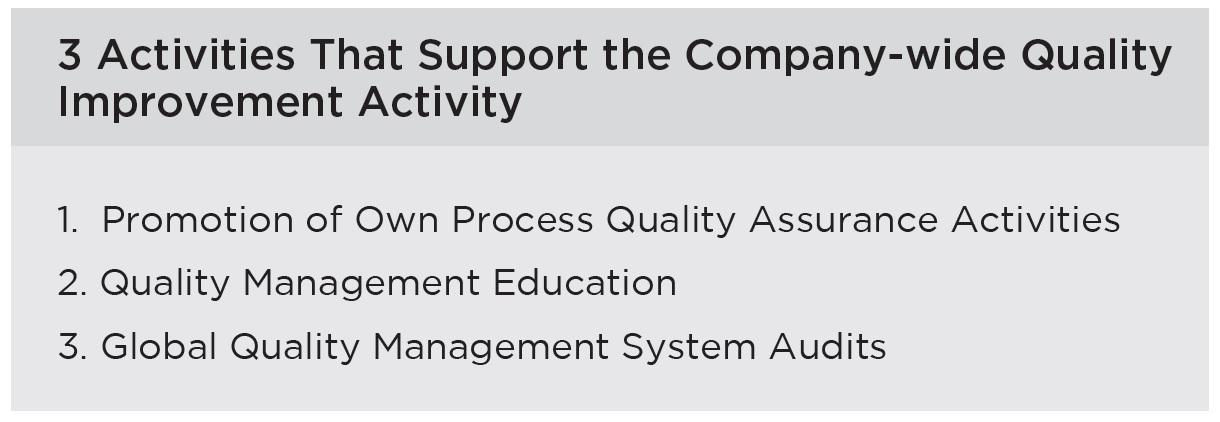
1.“Own Process Quality Assurance Activities” Aiming for Zero Complaints
Own Process Quality Assurance Activities are comprehensive efforts to prevent defects in each process from being produced or passed down to the following process. As part of these initiatives, defect-free process conditions (necessary conditions to produce defect-free products) are established at the design stage and the conditions are maintained through process management at the mass production stage. In case that any defect still occurs, we work to identify the cause and improve the quality in the pursuit of defect-free process conditions. Each division of the Sumitomo Electric Group is committed to Own Process Quality Assurance Activities for its products.
2. Enhancement of “Quality Management Education”
The Sumitomo Electric Group provides employees with training on quality control at the SEI University ensure the quality of products and services at higher levels. We have worked to improve various education programs, such as position-based training for all employees, nomination-based training in accordance with specialized jobs and special issues and optional training to learn relevant knowledge, along with practical education including QR-J*, MKP* and GKP*. Overseas, we have conduct Monozukuri Committee activities by area (4 regions: Americas, Europe & Africa, Southeast Asia & Australia, and Greater China) and organized education and exchange meetings on Own Process Quality Assurance Activities in Asia.
*QR-J: “Own Process Quality Assurance practitioner training course” to develop key persons for the Own Process Quality Assurance activities in each division.
*MKP: Abbreviation of “MONOZUKURI-KAKUSHIN professional training Program” that is the practical training program to develop candidates for future plant managers and key personnel for manufacturing.
*GKP: Abbreviation of “GENBA-KAIZEN professional training Program” that is the practical training program to develop key-personnel who are to manage and supervise manufacturing fields and promote shop-floor improvement.
3. Global Quality Management System Audits
We systematically conduct Global Quality Management System Audits to evaluate the quality control initiatives of each division in light of the Sumitomo Electric Group Quality Management Global Standards from the perspective of customers. In these audits, we identify weaknesses of each division in terms of management, design, manufacturing and functions as a hub to provide an opportunity to improve its quality assurance system and support its follow-up activities to reinforce the structure.
Quality Compliance
Supply of products that surely have the quality required by customers in compliance with laws and rules is an absolute foundation for companies to grow in a sustainable manner. The Group operates internationally and complies with local (country) laws. We also takes the measures mentioned below to ensure quality compliance.
Customer Satisfaction Activities by the Sales Group
The business activities of the Sumitomo Electric Group consist mainly of business-to-business transactions, and we therefore believe that the proper identification of the opinions and demands of customers (companies) through daily sales activities and the provision of solutions to their problems will lead to greater customer satisfaction and it will eventually increase our purpose as a company.
To enhance the quality of our sales activities, we conduct customer satisfaction surveys regularly and provide feedback to all sales staff. We cooperate with external consultants and provide training for sales staff on methodologies for understanding customer problems and proposing solutions as well as training for management staff on how to manage and instruct their subordinates. Thus, we strive to improve the quality of our sales and service so that we can be recognized by our customers as a true business partner.
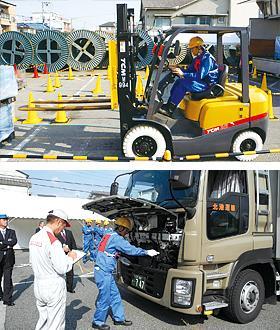
Activities for the Improvement of Logistics Quality
Sumitomo Electric is committed to the improvement of logistics quality in concert with transport companies carrying our products, in order to prevent product damage, fouling and other accidents during transportation and ensure to carry our products to customers without any accidents.
In particular, nearly half of the accidents of products during transportation are damage caused by a forklift truck. To reduce such accidents, we prepared a visual training text, which presents the issues to be considered on the basic operation of forklift trucks, and distributed it to not only our company and our group companies, but also transport companies.
We also work on various measures such as having qualified personnel irregularly check and provide guidance on on-site work as part of our “Forklift Basic Operation Compliance Activities.”