Safety and Health
Basic Concept
The Sumitomo Electric Group has placed safety as one of the most important managerial issues, and it has continued making efforts to eliminate occupational accidents, including activities led by the safety and health organization, promotion of equipment safety measures, and establishment of a safety and health education system. Recognizing that ensuring the health and safety of employees is essential for continuous business operations and is also part of our corporate social responsibility, we established “Safety Philosophy,” and “Principles of Safety Activities” in fiscal 2019, in addition to “Occupational Safety & Health Guidelines.” Aiming to be the safest company in the world, the entire group is making a concerted effort in performing health and safety activities.
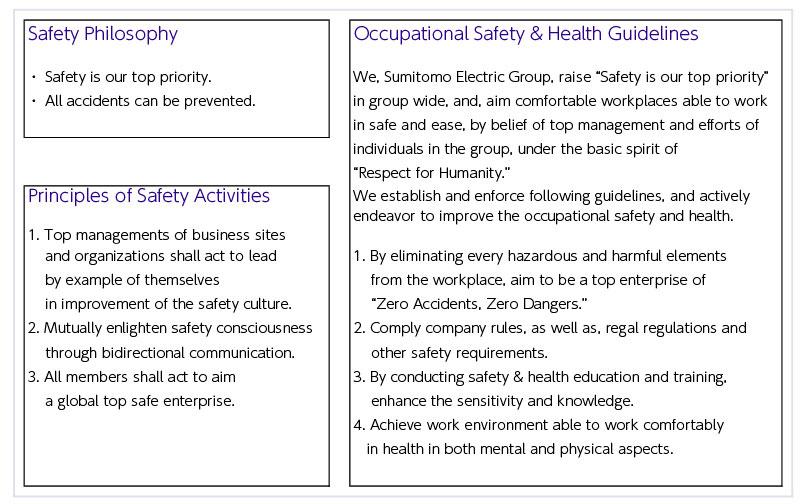
Promotion System for Safety and Health
Promotion of Occupational Safety and Health Management and Strengthening of Risk Assessment Practice
To achieve perfect occupational safety, it is essential to eliminate risk factors, and thus it is important to promote introduction of an occupational safety and health management system and strengthen risk assessments. An occupational safety and health management system is a system for taking measures before an accident occurs by identifying and evaluating hazard sources and harmful elements latent in field work. The Ministry of Health, Labour and Welfare recommends its introduction as part of activities to eliminate occupational accidents, and activities to promote this system are carried out internationally.
The Sumitomo Electric Group is promoting introduction of the occupational safety and health management system and actively working to carry out risk assessments based on the system (identification and evaluation of hazard sources at work), thereby reducing risk levels in a planned manner.
Initiatives for Safety and Health
Creating a Corporate Culture Where “Safety Comes First”
The Safety Philosophy gives top priority to safety, and the President conveys safety messages directly to all employees at the Group-wide safety conventions (held twice a year) and via internal safety broadcasts (carried twice a year) to ensure compliance with the Policy. It is crucial that top management demonstrates a clear policy. The safety policy and targets for each business unit are disseminated via the safety commitment of the general manager.
To create a corporate culture where “Safety comes first,” we are continuously promoting safety activities involving all employees and various forms of safety education with resolute honesty.
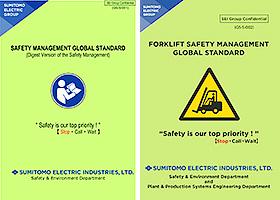
Group Global Safety Assessment
Under the Industrial Safety and Health Law, we must manage appropriate working environments for dangerous or harmful operations, provide legally required education, take equipment safety measures. To check that domestic affiliates appropriately fulfill these requirements, and to check the progress of their voluntary management activities, we are rolling out Group Global Safety Diagnosis in manufacturing sectors and affiliates in Japan and overseas.
In the Group Global Safety Diagnosis, in addition to checking various management activities, the auditors tour the plants and give instructions in order to ensure that segments with potential risks are identified and appropriate measures are taken. In particular, the safety measures on equipment are also evaluated in the facilities which involve especially high risks.
We also carry out a point-based evaluation of the system in place when procuring equipment using a checklist, and we identify the strengths and weaknesses of each department and affiliated company that has been inspected, and we provide traceability and support to ensure that appropriate measures are implemented.
We have established and are operating “SAFETY MANAGEMENT GLOBAL STANDARD” and “FORKLIFT SAFETY MANAGEMENT GLOBAL STANDARD,” which are standards to be observed by each section and affiliate of our group to promote unified safety and health management.
Safety and Health
Education
With the goal of achieving perfect occupational safety, the Sumitomo Electric Group regards safety education important and provides legally required education and educational sessions that enable employees to gain necessary safety and health knowledge according to their positions in a systematic and planned manner by incorporating such training programs into the curriculum of SEI University.
Since safety and manufacturing are closely related, we have established the Technical Training Center as an educational base for manufacturing. In the center, we have set up a facility where we can experience the hazards associated with work, providing safety training that appeals to the five senses.
Furthermore, we provide the KKP (KIBAN KYOHKA training Program), which consists of lectures, exercises and reporting assignments about practical themes for mid-level employees in Japan and overseas, and repetitive position-based educational sessions to prevent occupational accidents for employees who have not received safety education for a certain period of time, thereby enhancing safety education programs.
Safety Performance
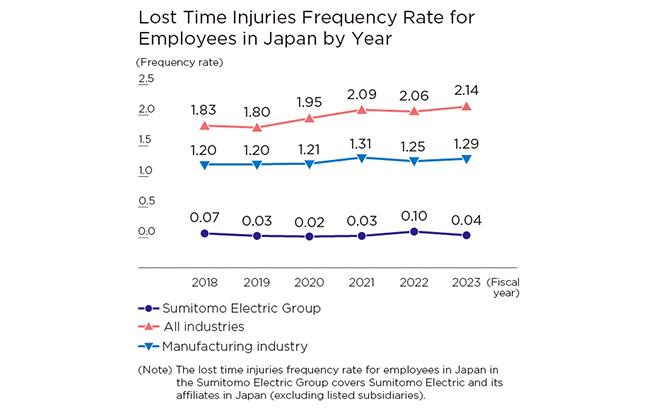
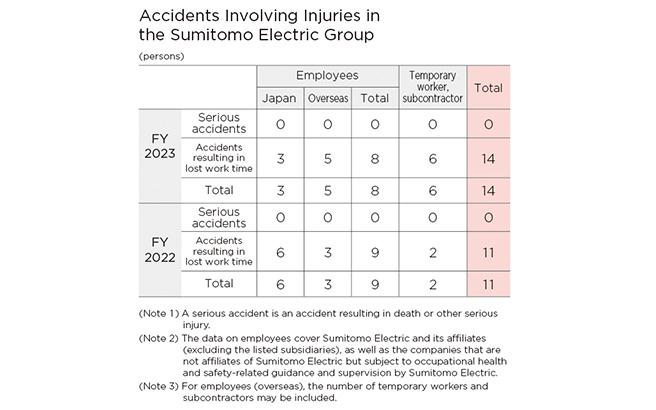