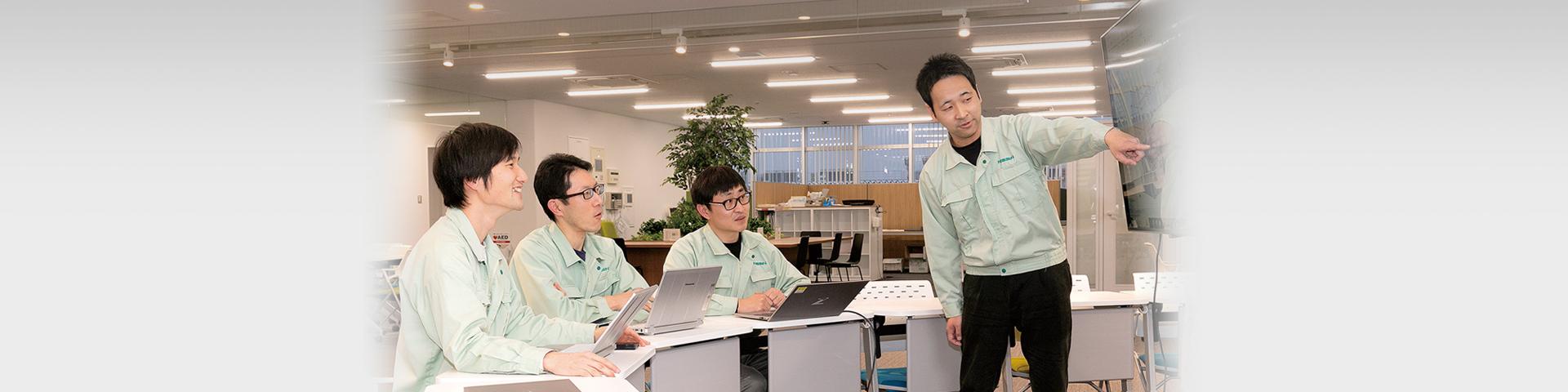
Creation and Evolution: The Inherited Spirit of the Development Staff
Reaching out to the next generation with a desire to contribute to society
The Birth of IMPHEAT and IMPHEAT-II
After completing the first model for research, the technical team pursued continued development to further improve the model. In 2010, they took part in a development project run by the New Energy and Industrial Technology Development Organization (NEDO) and completed an automated transport system for 6-inch SiC wafers. Furthermore, in response to customer requests, they optimized the transport sequence, improved temperature uniformity across the wafer surface, and mounted a high-frequency plasma flood gun to prevent charge-up (problems caused by static electricity or discharge). In 2013, the company launched IMPHEAT, the industry’s only mass-produced ion implanter for SiC power devices at the time. Subsequently, in the context of the increasing need for energy conservation, power saving, and environmental performance, the market for SiC power devices was expected to expand, so they took on a new challenge. Based on IMPHEAT, the technical team made a number of improvements, including optimizing the structure of the automated transport system, adding a pre-heating process to heat SiC wafers to a high temperature in a short period of time, dualizing the transfer arm, and doubling the ion beam, thereby achieving a reduction in processing time. Moreover, they succeeded in improving the ion source to double the ion beam current, with the aim of improving the stability of the ion beam and increasing the beam intensity. As a result, the number of wafers processed per hour increased to 100, approximately three times the previous level. This was IMPHEAT-II, which was highly praised from all quarters. It was announced in 2019 and deliveries began in 2020.
Taking on the Challenge of Next-Generation Ion Implanters
Young engineers are being trained to carry on the aspirations of the technical team involved in the development of the first model. Currently, development is under way mainly by young engineers on a next-generation ion implanter, which can be considered an upgraded version of IMPHEAT-II. NIC’s ion implanters have continued to evolve through continuous improvements and refinements. In fact, however, the issues that must be resolved have not changed since the first model was produced. The challenges are further optimization of the automated transport system, further shortening the time it takes to heat up to high temperatures, and stably producing high ion beam currents for a long period of time. It can be said that these improvements have been an ongoing effort since the first model was developed. Yuya Hirai is taking on the challenge of developing a new ion source.
“What I am constantly striving to do is to increase the beam current and operate the beam stably. This will be a major factor in differentiating us from our competitors. By changing the materials and process gases, we have successfully doubled the beam current. Furthermore, as there was a need to implant ions deep into the wafer without destroying the crystal, we also proceeded with the development of equipment that could measure the crystal orientation,” emphasizes Hirai.
Shinsuke Inoue is responsible for the control design for the automated transport system.
“Achieving stable transportation has been under consideration for many years, but we are still only halfway there. Of course, transportation is now more stable than ever before. However, time is still lost during heating, and deformation, distortion, and cracks still occur due to heat. The goal is to have zero rejected wafers. In addition to the electrostatic chuck, a mechanical clamp that uses jaws to hold the wafer is also employed. We would like to utilize our know-how and knowledge of control, mechanical structure, and physics to achieve stable automated transport,” says Inoue.
Jian Wang is working on the mechanical design of automated transport systems.
“When transported, wafers are vacuum-held on the robot hand on the atmospheric side. However, hightemperature ion implantation causes the wafer to warp, which creates a gap between the robot’s suction part and the wafer placed on it, making it impossible to transport the wafer using vacuum suction. What I am currently working on is to develop a suction pad that is highly heat resistant and flexible. A flexible pad can adjust itself according to the warp, which helps prevent gaps from occurring,” explains Wang.
Koyu Ueno has worked on a range of tasks, from determining the specifications, to the assembly and delivery of equipment for each customer. Recently, from the perspective of his specialty in mechanical design, he has been seeking improvement in the number of wafers processed per hour with the automated transport system, which is a key point in differentiation from competitors, while also undertaking new development projects.
“Until now, we have grown together with semiconductor manufacturers that have been leading the way with SiC in the domestic market, but from now on, we will also aim to develop equipment with layouts that are well received by overseas manufacturers, such as those in Europe, the U.S., and China, where growth is notable," says Ueno.
As a result of these efforts, the next-generation system is nearing completion. The plan is to complete an in-house machine this fiscal year, conduct further testing, and release it to the market next year.
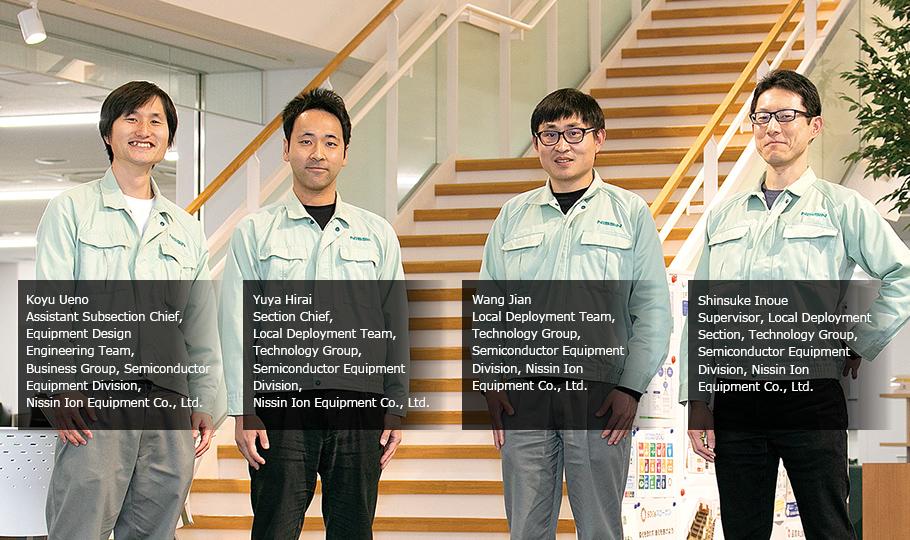
Constantly Taking on New Challenges Leads to Contributing to Society and the World
They speak about their passion for developing ion implanters and what fascinates them about it:
“It’s a continuous challenge to develop new technologies that will generate new value and be used by people all over the world. That’s the best part of this development work, and what makes it so interesting.” (Hirai)
“The ion implanter may not stand out, but it works behind the scenes to create new value for customers. We would like to expand our market share while maintaining our competitive advantages.” (Inoue)
“All sciences, including chemistry, physics, and engineering, are applied to ion implantation. I enjoy that in itself. I also feel that it is rewarding to develop something that will make the world a better place, such as contributing to carbon neutrality.” (Ueno)
“Using existing technology and my own ideas to make a better system means I can give shape to my ideas and thoughts, and I feel that it is the most rewarding job for an engineer.” (Wang)
Given these thoughts of the technical team, what kind of market strategies are actually being pursued? You will see that in the final chapter.
Spaces that allow for open and flexible thinking
The Shiga Works, commonly known as “Link Square”* of Nissin Ion Equipment Co., Ltd., was built as a cutting-edge R&D center for ion implantation technology. The plant is carefully designed to stimulate communication and foster an environment that will encourage innovation in order to create new value. An open, bright space where spontaneous communication is ensured fosters imagination, initiative, and teamwork.
* Link Square is named after the idea of a town where people, things and events connect with each other. The name also conveys the hope that it will be a place of learning (L), innovation, inspiration, and interaction (IN), and knocking (K) on the next door to the future.
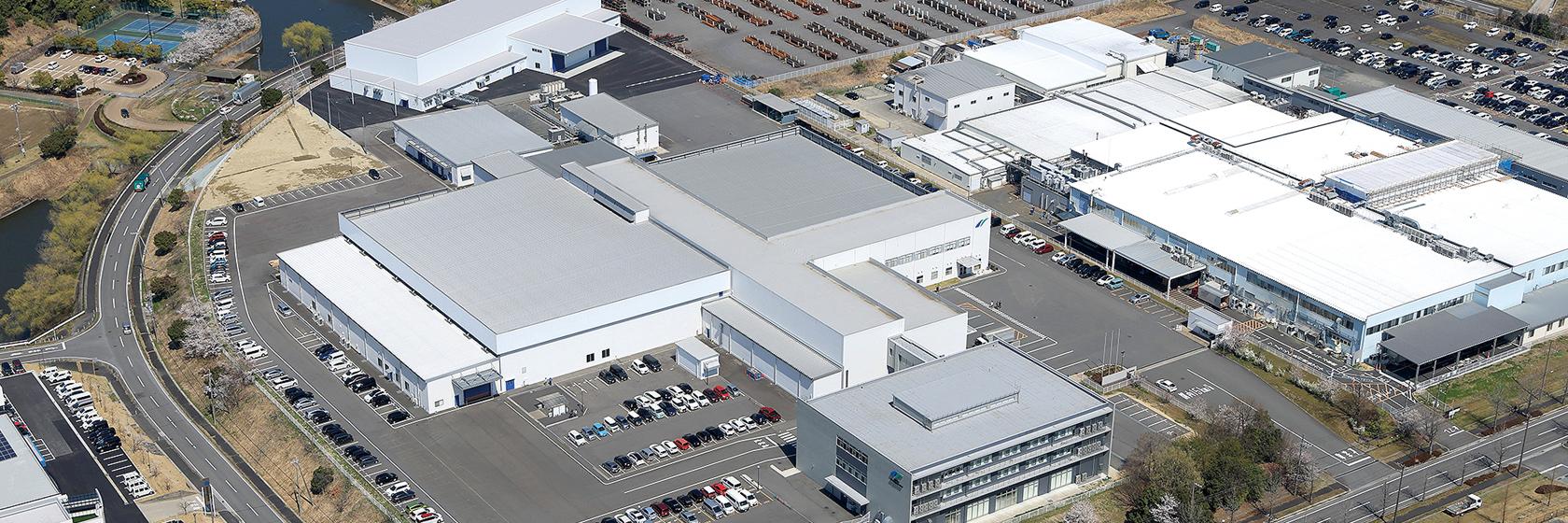
NEXT
Growing Global Expectations for Ion Implanters
- Promoting global strategies in the SDGs era -