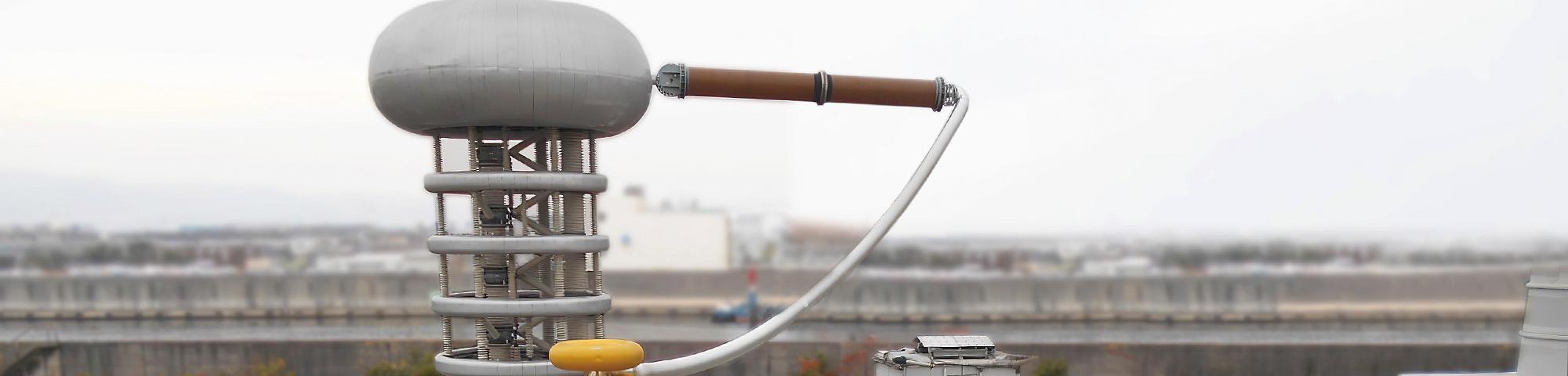
Devotion to the Development of DC XLPE Cables
An Inside Story on the Development of a Special Filler Material
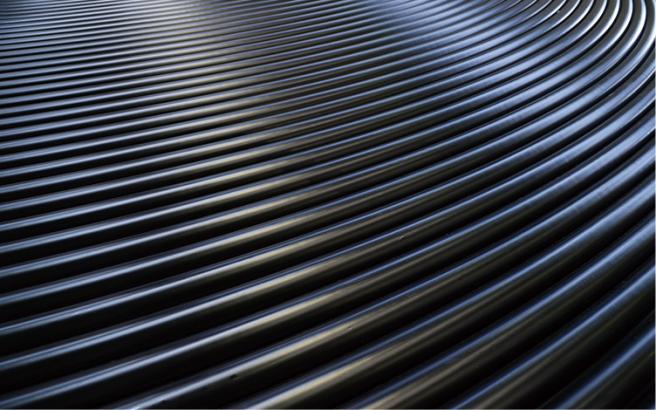
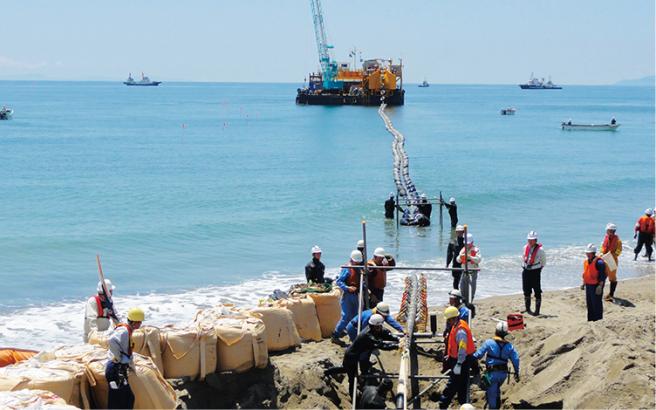
Obstacle posed by space charge
In 1979, J-POWER completed the first-stage submarine cable for the Hokkaido-Honshu HDVC Link, which connected Hokkaido with Mainland Japan, and started operation. However, the installed cable was the oil-impregnated insulation type. Thus, the company hoped to use the DC XLPE cable for expansion or renewal from the viewpoint of environmental protection. Mitsumasa Asano of J-POWER (at that time), who worked on the development with Sumitomo Electric, looked back on the situation and said, “I felt the passion of Sumitomo Electric’s development team members, who showed extraordinary perseverance to accomplish the project whatever it might take.”
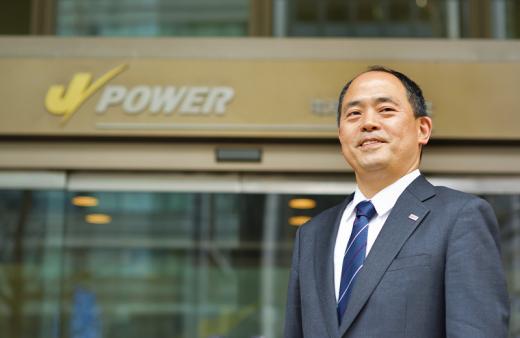
“The biggest obstacle was how to suppress the space charges. Electric charges, which are invisible, refer to the amount of electricity with which an object is charged. The electric charges that accumulate in an insulating material when DC voltage is applied are referred to as ‘space charges.’ These prevent an insulating material from fully demonstrating its performance. Electrical breakdown* may result when a power transmission system is hit by lightning. This was the biggest factor that prevented application of XLPE cables to DC. When we conducted various tests to eliminate the space charges, Sumitomo Electric made an unconventional proposal. ‘Even if the electric charges are present, electrical breakdown may not occur when the electric charges are evenly and uniformly scattered in an insulating material.’ Thus, we decided to use a method of adding a filler material to the cross- linked polyethylene,” said Asano.
The insight was right. After trial and error, the space charges were finally suppressed by adding a newly developed special filler material. R&D proceeded from Stage 1 (1988 to 1995), which aimed to attain 250 kV, to Stage 2 (1993 to 2001), which aimed to attain 500 kV. All the targets were achieved.
This coincided with the deterioration of the first cable installed for the Hokkaido-Honshu HDVC Link. In 2012, the DC XLPE cable was finally put to practical application for the first time in the world to meet the replacement needs.
“In the actual manufacturing operations, it was necessary to fabricate a long-distance cable. This posed difficulties in maintaining uniform quality compared to the prototype production. It was highly meaningful to hold discussions between the two companies about the quality control and manufacturing process,” said Asano.
Asano also remembered what impressed him during the installation work.
“The offshore cable had to be connected with the onshore cable manually. Accidents were likely to occur at this point in the cable construction project. This process required high engineering capabilities. Sumitomo Electric’s workers were reliable in terms of both skills and construction management,” said Asano.
The project was accomplished thanks to Sumitomo Electric’s overall capabilities: development engineers who perseveringly pursued outstanding specifications, in-depth quality control at the manufacturing site, careful construction work which took full advantage of the quality, and passion to attain high levels on all aspects.
* When the strength of an electric field that applies to an insulating material exceeds a threshold, the insulating material electrically breaks down, resulting in a rapid decrease in electrical resistance and allowing a large current to flow.
A revolutionary idea to mix an additive
Let’s meet a legendary person who has focused on DC XLPE cables throughout his research career. Shoshi Katakai is affiliated with the Electric Wire & Cable Energy Business Unit. He has been devoted to R&D of DC XLPE cables since the 1980s, when he entered the industry.

“I spent frustrating years. However, many customers waited for the practical application of cables capable of large-capacity power transmission with minimal environmental impact, so R&D never stopped,” said Katakai.
The development of 500 kV AC XLPE cables was in full swing when Katakai started to work on research. Cross-linked polyethylene (XLPE), which is the key insulating material, significantly improved the properties of polyethylene at high temperature by cross- linking, which is a method of changing the molecular structure.
“To make XLPE an insulating material capable of coping with higher voltages, R&D members were expected to prevent defects, by entering no defects, producing no defects, and being able to prove no defects existed. The ideal was to develop the purest possible polyethylene without mixing additives,” said Katakai.
This approach was considered to be applicable to the insulating material of DC power transmission cables. However, a new problem, which did not arise in the AC power transmission cables, emerged. Conventional XLPE attained the electrical breakdown strength far below the expectations for the DC voltage due to accumulation of the space charge, which was discussed above. In other words, AC XLPE cables made from pure polyethylene could not be used as they were for DC. Thus, Katakai came up with the idea of mixing an additive and decided to use a filler material. He made steadfast efforts to carefully identify potential filler components one by one to cope with high voltages and finally determined the components and blending to resolve the problem. Efforts to achieve further miniaturization and higher purification and distribution led to a special filler material. A material with superb DC insulation characteristics was completed by uniformly distributing the components in XLPE. This is the proprietary XLPE that underpins HVDC power transmission cables currently manufactured by Sumitomo Electric. The accomplishment was derived from doubting the conventional wisdom and seeking the truth with perseverance.
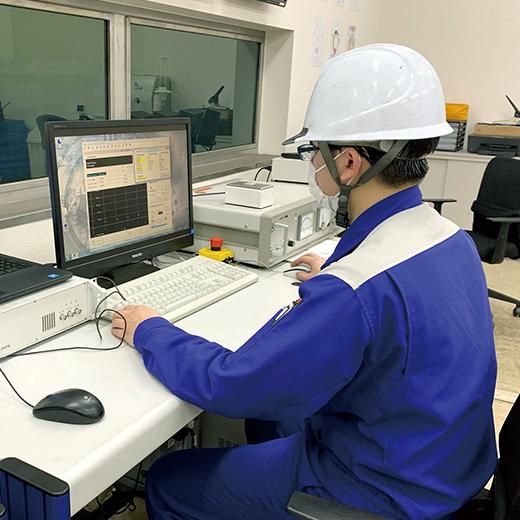
“‘Seek the Truth’ – I have only followed the teaching in good faith from my teacher when I was a student,” said Katakai with deep emotion. In the 2000s, a consortium was organized with a university to publicly evaluate the results. Preparations were made toward commercialization. However, there was no project to use DC XLPE cables. It took some more time until practical application. The situation changed in the 2010s. After the Great East Japan Earthquake in 2011, there was a growing need for electric power interchange between electric power companies. Coincidentally, the DC XLPE cable went into operation in the Hokkaido-Honshu HDVC Link in 2012.
At present, Katakai focuses on training younger engineers as a fellow of Sumitomo Electric, but he remains highly motivated to work on the development.
“Interconnectors have been expanded worldwide, but more of them are needed,” said Katakai.
The Japanese government has announced a plan to construct a next- generation grid to send electric power derived from renewable energy sources, such as offshore wind power, from Hokkaido to Tohoku and Tokyo as part of its clean energy strategy. In Europe, where the electric power market has been liberalized, construction of an international grid called “super grid” is underway as the first project of its kind in the world. The development of international interconnectors has been spurred by the growing need to introduce renewable energy. Full-scale efforts have been launched by regions and countries to achieve carbon neutrality. The supply of DC XLPE cables, which were developed by Katakai and other Sumitomo Electric engineers, will be accelerated for interconnector projects in and outside Japan.
NEXT
Connecting Regions for Stable Supply of Electric Power
– New Hokkaido-Honshu DC Seikan Tunnel Project –