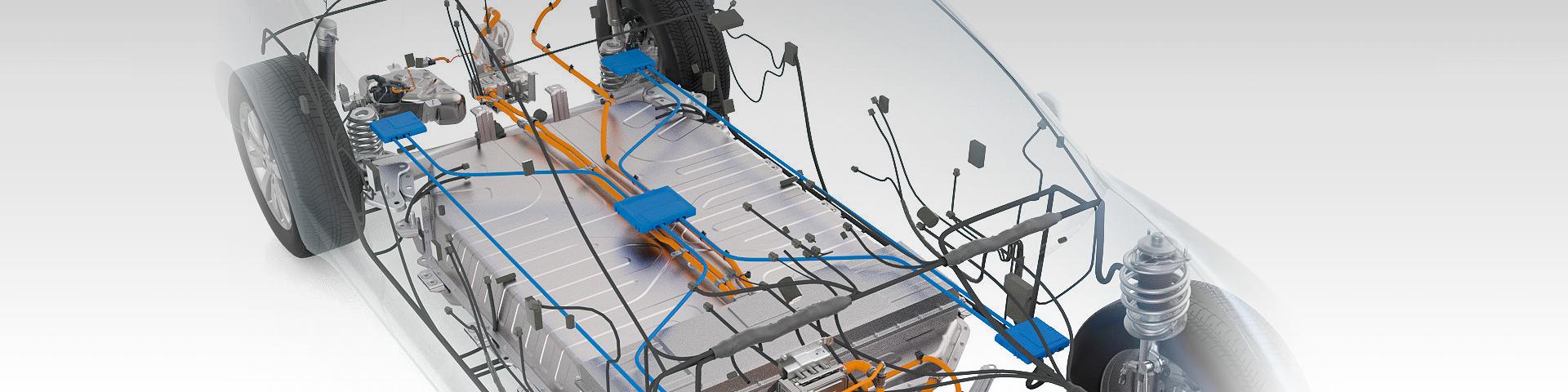
Mission of Wiring Harness in the CASE Era
Commitment to Manufacturing, Changes in Manufacturing
Wiring harness required in the CASE era
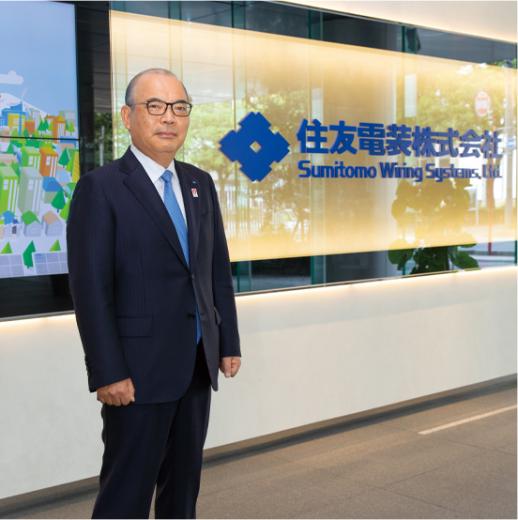
Sumitomo Wiring Systems, Ltd. (Sumitomo Wiring Systems) develops and manufactures the wiring harness, which is the core business in the mobility area of the Sumitomo Electric Group. The most distinctive feature of wiring harnesses is the fact that they are mostly handmade, labor-intensive products. Sumitomo Wiring Systems has production sites in about 30 countries around the world, with approximately 230,000 employees in total. Product quality hinges upon individual employee’s technical expertise and skills. This means that the quality may vary depending on the region and the personnel involved. The Sumitomo Electric Group started addressing the challenges at an early stage. The Group aimed to achieve a globally common best quality and practiced Pika Pika (brilliant) manufacturing through Pika Pika Activity (brilliant mind, actions, skills, equipment, and worksites) unique to Sumitomo Wiring Systems. As a result, its high reliability has been recognized by automakers around the world, which served as a driving force to achieve the world’s top market share.
“Evolution of the wiring harness is required in the CASE era. To respond to requests for vehicle weight reduction, we developed the aluminum wiring harness several years ago. Aluminum wires have helped reduce the total vehicle weight by about 12% and improve fuel efficiency, contributing to the reduction of CO2 emissions. We will also provide products that meet the needs of the CASE era for society,” said Kenichi Urushibata, President and Chief Executive Officer of Sumitomo Wiring Systems.
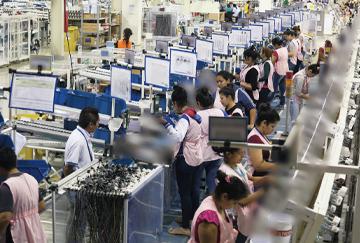
As Urushibata pointed out, the trends of CASE have opened a new phase of the wiring harness. For example, since EVs require a high current, enlargement of the diameter of cables, which consist of several thousand elemental wires arranged in a complex manner, is inevitable. Cables with longer service life and higher reliability are required to avoid disconnection and other defects. In addition, achieving “Connected” requires higher-frequency signals to enable higher-speed and largercapacity communications. The key is connectors. The connector shape must be optimal to ensure smooth highfrequency signal throughput. Thus, the impact of CASE on the wiring harness is not small.
Manufacturing turns the corner to a new business model
Urushibata also indicated that the manufacture of wiring harness is reaching a critical turning point.
“Conventional business models are no longer valid due to the influence of the global semiconductor shortage and the COVID-19 pandemic. As one of the measures to break through the difficulties, we aim at local production for local consumption. Wire harnesses used in the U.S. should not be produced in ASEAN countries but in North America. However, we had a big problem. Since wiring harnesses are mostly handmade, the quality depends on the individual employees’ skills,” said Urushibata.
They have ensured globally common best quality by improving employees’ skills and knowledge in each region through steady efforts to improve skills, such as Pika Pika activity. That is because automated manufacturing of wiring harness was supposed to be impossible. However, the development group has started efforts toward automation to solve the problem. One of the outcomes is the set operation, which automatically sets cutting and crimping wires. The lead time for set operation is 2 hours, a significant reduction compared to 1.5 days for manual operation. Furthermore, they have achieved revolutionary automation.
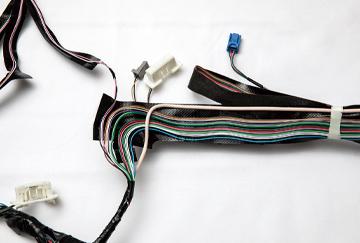
“We implemented assembly automation using e-STEALTH W/H®. In addition, we aim at highvariety production with smaller part numbers by integrating e-STEALTH W/H® with a process that automatically assembles downsized harnesses, and changing the shape of the harness. Although the automation is now limited to specific areas, we will address local production for local consumption and preparation of a business continuity plan through these efforts and commonality of facilities to establish a new paradigm in manufacturing,” said Urushibata.
The Sumitomo Electric Group is casting an eye on manufacturing in the CASE era.
Changing manufacturing worksites through DX promotion
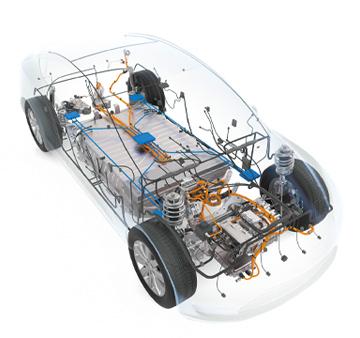
DX promotion has the potential to drastically change the business model.
“First, we will digitize design work. To reduce lead time, we have relied on individual know-how and skills; however, digitization is essential to radically reduce lead time. Making full use of tools, such as 3D CAD and VR, we will promote digitization. I want to digitize all of our design work in the 2030s. Vietnam is one of the countries that have produced excellent results in manufacturing. We are also trying to use AI for analyzing work and data to design the optimal worksite layout, allowing employees around the world to learn the best practice. Production management is more important. We will reduce waste and improve efficiency by centrally managing and visualizing the processes of order taking, production, storage, and delivery. These efforts will help change our conventional business scheme and make our corporate structure more sustainable, and are part of our efforts to keep up with manufacturing in the CASE era,” said Urushibata.
The wiring harness business of the Sumitomo Electric Group will maintain the top market share, fulfill the supplier's responsibilities, and continue to create high added value using technical and manufacturing expertise that is becoming the de facto standard in the CASE era.
NEXT
Great Challenges Toward Improving Automotive Value and Creating New Value
– CASE-Related Products Using the Group’s Integrated Power –