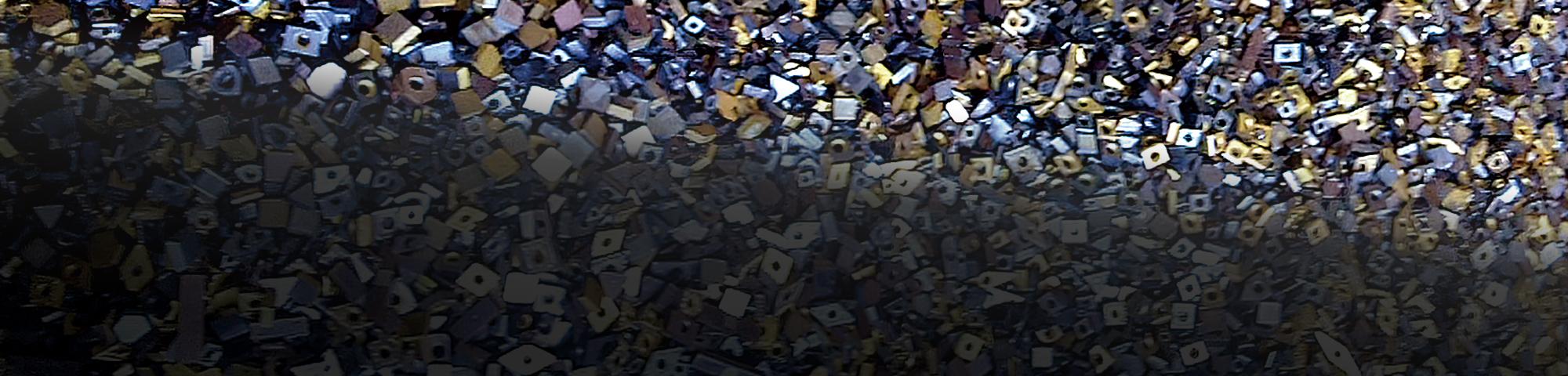
Toward a future where tungsten is recycled 100%
Recycling system developed by Toyota and Sumitomo Electric
Removing the procurement risk of materials by promoting recycling
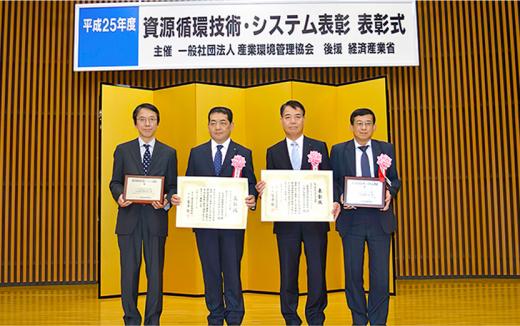
In 2013, there was a landmark event as a result of tungsten recycling promoted by the Sumitomo Electric Group. The recycling system for cemented carbide tools in Japan, which was established through collaboration between Sumitomo Electric and Toyota Motor Corporation, which is the user of the tools, was recognized with the Rare Metal Recycling Award in the Awards for Resources Recirculation Technologies and Systems, under the auspices of the Japan Environmental Management Association for Industry. Cemented carbide tools are considered a source of competitiveness for Japanese automakers, including Toyota.
Their stable quality and price have underpinned the auto industry. However, tungsten, a raw material of cemented carbide tools, is difficult to substitute with other substances. Dependence on imports also posed a risk for automakers as users of such tools. Ayami Imakiire, who was mainly in charge of the procurement of cemented carbide tools at Toyota, was quite concerned about securing materials. At that time, the Sumitomo Electric Group made a proposal to build a recycling mechanism together.
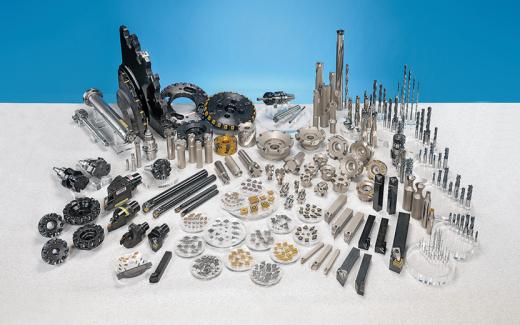
“The Sumitomo Electric Group is one of our main suppliers. We received a proposal from a person in charge to collaborate in recycling around 2011. We learned that they had developed a new recycling technology (the abovementioned oxidation-wet chemical process) and that high-purity tungsten could be recovered from scrap by using the technology. It was a very interesting and attractive proposal. One of the issues faced by the Sumitomo Electric Group was that it could not collect a large amount of scrap. They thought that we could collect a certain amount of scrap. This developed into a project to build a recycling mechanism. Previously, we sold scrap, but we launched collaboration in recycling with the Sumitomo Electric Group with a view to significantly reducing the procurement risk of materials by recycling and contributing to the SDGs,” said Imakiire.
Extensive sorting by Toyota
Toyota was quick to take action. The Materials & Facilities Purchasing Div. grasped the social circumstances and quickly identified the needs. It asked for cooperation from plants as well as the relevant departments, including the production engineering and environment departments, and launched company-wide efforts. However, recycling efforts do not produce results immediately. The division worked hard to spread awareness and win support from many employees.
“To build a recycling system, workers at the respective sites must work on sorting. We patiently explained the overall economic advantages and social mission of this activity to the relevant personnel in the company and won their support gradually,” said Imakiire.
Notably, a sorting method was established with recycling in mind in collaboration with the Sumitomo Electric Group, which undertakes the post-process of recycling. Sorting was conducted properly at respective plants of Toyota: not just major classification of “cemented carbide tools” and “dies and molds,” but also in-depth sorting of scrap, including cutting tips and drills (detailed classification of cemented carbide tools). Subsequently, the first recycling system in Japan was established on a commercial basis in collaboration with recycling companies, achieving 100% collection and recycling of tungsten from scrap of cemented carbide products.
“At present, the recycling system is operating smoothly. The system has been well established. In the future, we hope to build a recycling mechanism not only for hard scrap but also for sludge. I hope that the Sumitomo Electric Group will improve its recycling technology, which can ensure the economy of rare metals and achieve the recycling of rare metals other than tungsten in Japan,” said Imakiire.
The Sumitomo Electric Group is expected to expand its recycling business to meet Toyota’s expectations.
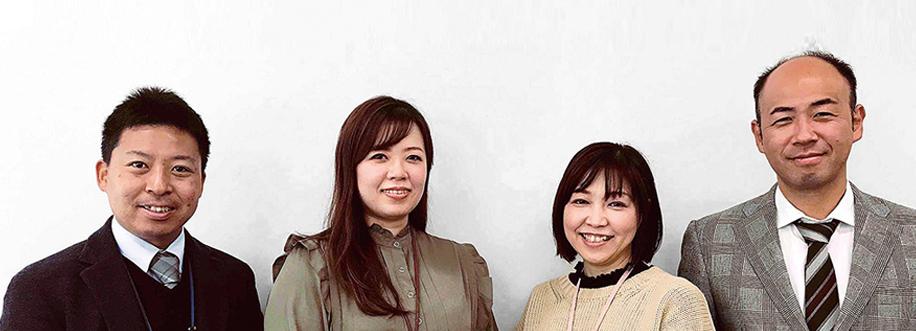
Evolution of recycling and a challenge to promote innovation
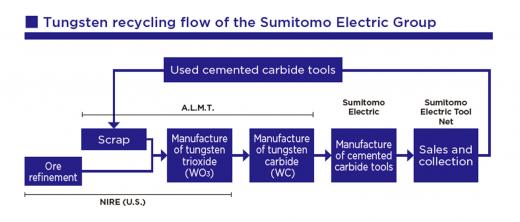
With the completion of the recycling system in Japan, achieved in collaboration with Toyota, the Sumitomo Electric Group’s recycling efforts attracted considerable public attention. Tungsten recycling in Japan, including efforts made by the Sumitomo Electric Group, has been accelerating gradually. However, complete recycling has only partially been achieved. Under these circumstances, what action will the Sumitomo Electric Group take? Toshiyuki Sahashi, Managing Director of Sumitomo Electric and Deputy General Manager of the Advanced Materials Business Unit, stated as follows regarding the recycling business in the future:
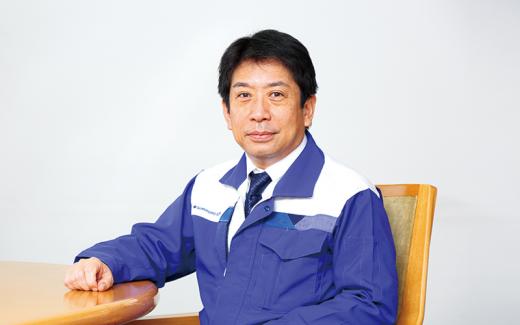
“The development of the chemical process at A.L.M.T. and the establishment of NIRE in the U.S. have made it possible to handle the entire process from raw materials in the upstream (ore refinement and scrap) to cemented carbide tools, the final products. This is the strength of our group. Ore refinement poses many risks because it depends on overseas mines. Thus, it is necessary to promote the hard metal (cemented carbide) business with a focus on recycling. This requires technological perfection to achieve cost reduction while maintaining high quality. We must establish recycling technology quickly at NIRE and pursue higher technology at A.L.M.T. Given the uncertainty of the international situation, recycling is inevitably important. There are also risks from the viewpoint of business continuity planning (BCP).
At present, we have only one company, located in Hokkaido, that manufactures cutting tips, which are the main products of cemented carbide tools. We would suffer tremendous damage if this company were to become inoperable due to a disaster. I was stationed at Sumitomo Electric Carbide, Inc., which invested in NIRE, as an expatriate when NIRE was established, so I have a strong commitment to NIRE’s business. Now that NIRE is in place, a production system encompassing the production of tungsten trioxide (WO3), tungsten carbide (WC), and the final products should be built in a different cycle. This is my future vision,” said Sahashi.
It has been 10 years since the Sumitomo Electric Group developed the oxidation-wet chemical process as a new technology and started the recycling business. While the Group has steadily worked on the recycling of tungsten, the business environment and people’s awareness of recycling have changed significantly. Namely, there has been a paradigm shift from “recycling is good” to “recycling is necessary.” With the spread of the SDGs, many people have become aware of the importance of recycling and have started to take action in their daily lives. Under these circumstances, the Sumitomo Electric Group has produced significant results by developing an innovative recycling technology and building a mechanism to a certain extent in order to secure tungsten, one of the scarce resources. Efforts are being made on an ongoing basis. To seek a next-generation recycling model, the Sumitomo Electric Group has embarked on a new challenge toward further evolution and innovation.