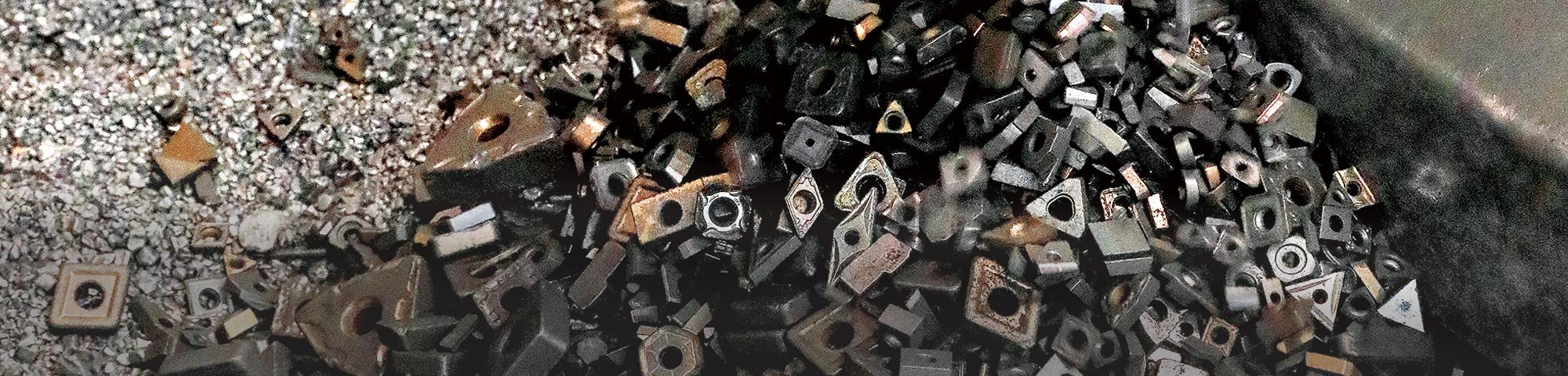
New Technology That Achieved an Innovative Recycling System
A bold challenge to achieve the oxidation wet-chemical process
A path toward the recycling and stable supply of tungsten
In recycling of cemented carbide tools, a direct process called the “zinc process” had previously been used. In this process, which the Sumitomo Electric Group carried out for many years, solid hard scrap is heated and melted together with zinc. Subsequently, only zinc is removed to obtain spongy cemented carbide, which is pulverized and recovered as recycling powder. Simply put, the constituents are directly recycled into powder. The zinc process is beneficial in that its consumption of chemicals and energy is small. However, it has a big problem. Specifically, it can remove impurities that volatilize in a hightemperature process, but it cannot increase the purity or adjust the size of the powder particles, resulting in limited scope for reuse. Under these circumstances, the Sumitomo Electric Group took on the challenge of achieving the complete recycling of cemented carbide. The objective was to obtain raw materials, which were equivalent to those derived from ore refinement, from collected scrap. If this could be achieved, recovered cemented carbide would be usable for various purposes, opening the way toward the stable supply of tungsten. It was therefore necessary to develop a new tungsten recycling technology to replace the zinc process.
High-purity recycling to obtain widely usable raw materials
The challenge to develop a new technology was launched in response to the surging price of tungsten in 2005. The price had almost quadrupled from the previous year. The risk of dependence on China materialized. The development a new tungsten recycling technology started in 2007 through participation in a project under the auspices of Japan Oil, Gas and Metals National Corporation (JOGMEC) named the “project to develop a highly efficient system to recover rare metals, etc.” Sumitomo Electric, Sumitomo Electric Hardmetal Corp., A.L.M.T. Corp., and Nagoya University participated in the joint research project, which aimed to develop a new recycling technology capable of highly efficient processing even on a small scale by focusing on cemented carbide scrap. A.L.M.T., a Sumitomo Electric Group company in the industrial materials segment, took on the leadership role. The company focuses on two businesses: the refinement, manufacture and processing of high-melting-point metallic materials, such as tungsten and molybdenum, and the manufacture and precision machining of diamond precision tools. Minoru Tsunekawa, who was a member of the project to develop a new recycling technology and is currently Engineering General Manager of the Powder Alloy Division & Hard Metal Division of A.L.M.T. , said that the ultimate goal of the new recycling technology was to obtain high-purity WO3.
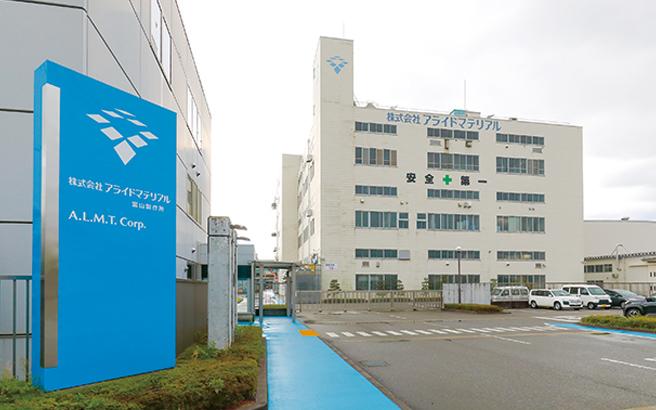
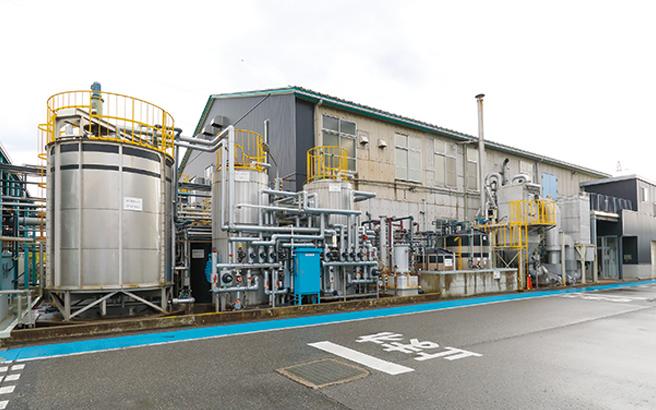
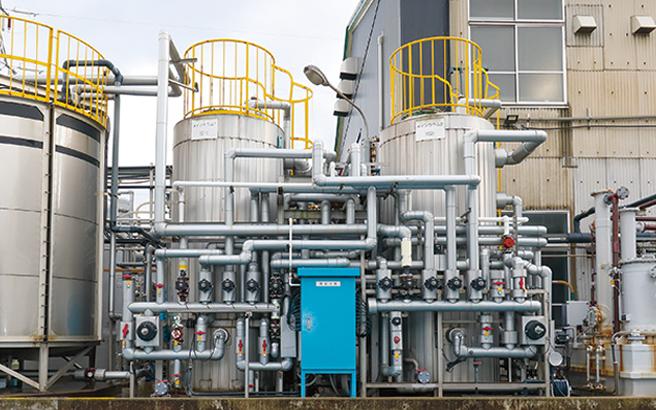
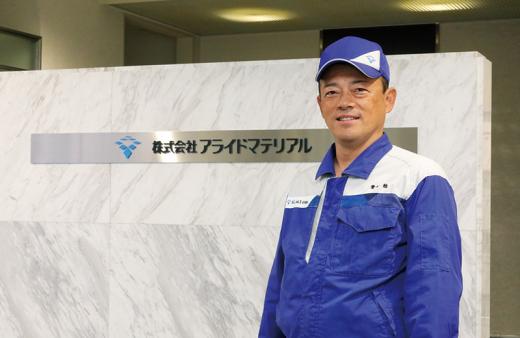
“The usage of recycled powder derived from the zinc process was limited. The powder was only usable as a raw material for cemented carbide. Thus, recycling in a broad sense had not been achieved. Recycling means obtaining raw materials that can be used flexibly and widely. It was necessary to restore the condition before the material had been processed into WC. The objective was to obtain a raw material whose quality was equivalent to that of refined ore (namely, high-purity WO3). It was also necessary to handle various types of scrap. The new recycling technology to achieve the goal is an oxidation-wet chemical process, whereby scrap is chemically dissolved and melted to recover its constituents. We faced difficulties in establishing the technology,” said Tsunekawa.
High efficiency achieved by the ion exchange resin process
One of the difficulties that Tsunekawa mentioned was the development of molten salt dissolution technology. To obtain WO3, it is necessary to perform oxidizing roasting of scrap of cemented carbide tools and then to chemically dissolve the product to prepare a solution. However, this process cannot oxidize the insides of scrap materials. The processing cost is high because reoxidation is required. Tsunekawa and other members tackled this issue.
“In our development technique, we dissolved sodium nitrate (NaNO3), whose oxidizability is high, together with scrap of cemented carbide tools, and allowed the solution to react with sodium while performing oxidation. This technique had the advantage that the oxidation processing reached the insides of the scrap materials. However, it posed a big problem. The oxidation reaction was accompanied by the generation of a large amount of heat. We had to consider how to control the rapid exothermic reaction and ensure safety. After conducting an in-depth study, we optimized the supply volume of NaNO3 (molten salt), making it possible to control the reaction,” said Tsunekawa.
In the next phase, it was necessary to convert the resulting sodium tungstate (Na2WO4) solution into an ammonium tungstate ((NH4)2WO4) solution. Tsunekawa and the other members aimed to achieve highly efficient conversion. They chose the ion exchange process, whereby the solution was allowed to flow through a resin tower filled with ion exchange resins. The tungstate ions contained in the Na2WO4 solution were adsorbed by the ion exchange resins, and were eluted by ammonium salt to obtain the (NH4)2WO4 solution.
“The question was how to achieve high efficiency. While working on selecting optimal resins, we focused on the pH value, which represents acidity or alkalinity. We found a solution to achieve high efficiency by carefully controlling the pH value. We increased the efficiency of the ion exchange process to two- to three-fold that of the conventional technology. In other words, the tungsten adsorption volume increased two- to three-fold, so we were able to reduce the size of the equipment due to higher efficiency,” said Tsunekawa.

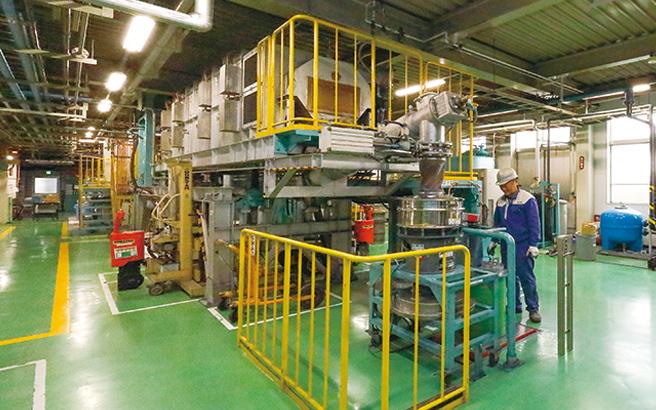
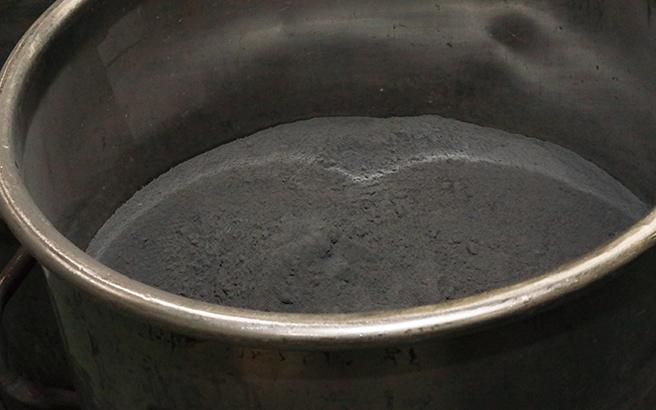
Expansion of the recycling business while seeking new solutions
The tungsten recycling system was completed after resolving various issues, including treatment of the exhaust gas, the development of an ammonia recovery and reuse system, and the study of appropriate recycling of powder scrap. The plant equipment started operation in 2010. After making improvements, commercial operation commenced in the latter half of 2011.
“We remain thoroughly committed to quality at every stage from obtaining scrap, which is the raw material, to the final process. We will further expand the recycling business. There isn’t enough space available to increase production at the Toyama Works, which currently serves as the production center, so we will study new methods,” said Tsunekawa.
The efforts to expand the recycling business, which Tsunekawa mentioned, are under way in the U.S. The next chapter will focus on the recycling project in the U.S., which is based on the oxidation-wet chemical process.