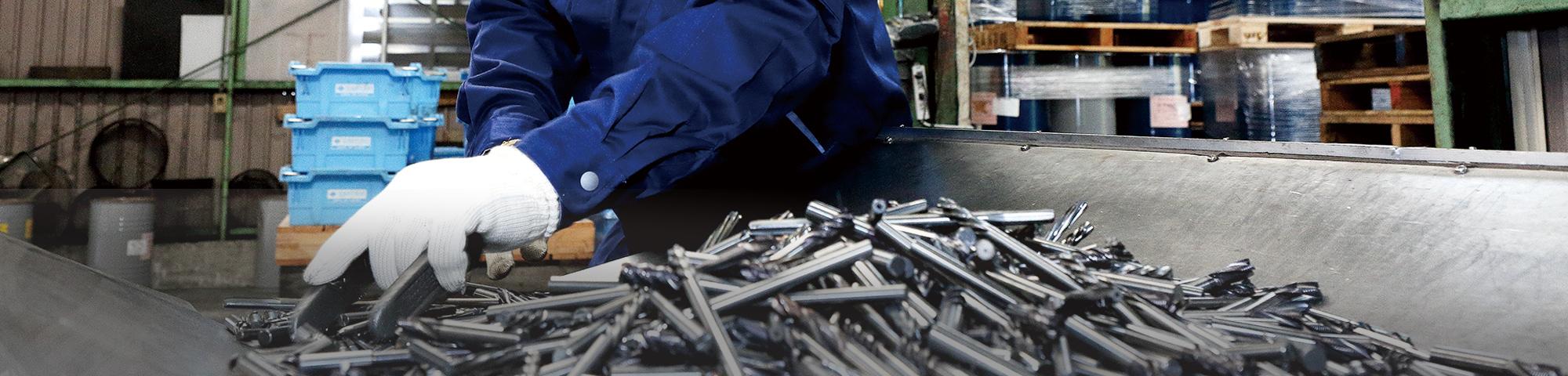
A Challenge to Build a Tungsten Recycling System
Achieving a stable supply, which has been a pressing issue
Securing rare metals, the top-priority national issue
Japan depends on imports for most of its energy and mineral resources. At present, there are no mines in Japan that produce rare metals, including tungsten. For this reason, ensuring the stable supply of energy and mineral resources is one of most important national issues. Against this backdrop, the Ministry of Economy, Trade and Industry formulated the New National Energy Strategy in 2006. It mentioned the need to step up efforts to promote recycling of metallic mineral resources. The Guidelines for Securing Resources, which were established in 2008, set out a policy to support the acquisition of important resources, including rare metals. In the following year, the Strategy to Secure Rare Metals was published. In 2012, five minerals— neodymium, dysprosium, tantalum, cobalt and tungsten—were selected as priority minerals to be recycled. A national project is under way to secure these rare metals.
Why are rare metals so important? Although they are consumed in small quantities, they are indispensable materials in the manufacture of LCD TVs, mobile phones and vehicles. In fact, they are essential in maintaining and strengthening the international competitiveness of Japan’s manufacturing industry. Notably, global demand for rare metals is expected to increase in the fields of nextgeneration vehicles, motors and storage batteries, which are expected to come into widespread use in the building of a low-carbon society. In terms of the use of tungsten, cemented carbide accounts for about 61% of the global market on average. In Japan, the percentage of cemented carbide is particularly high (about 76%).* Derived by mixing WC with cobalt (Co), cemented carbide achieves high hardness, high wear resistance, and high heat resistance. Cemented carbide tools, such as drills, and cemented carbide inserts for cutting tools have achieved high-speed machining and revolutionized the operation of manufacturing and machining sites. In Japan, the Sumitomo Electric Group has become one of the pioneering companies of this technology. Cemented carbide tools are crucial for many manufacturers. It is safe to say that these tools are the lifeline of manufacturing and machining. Tungsten is an essential material in the production of these tools.
* Source: Statistical Report 2013 published by the International Tungsten Industry Association (ITIA)
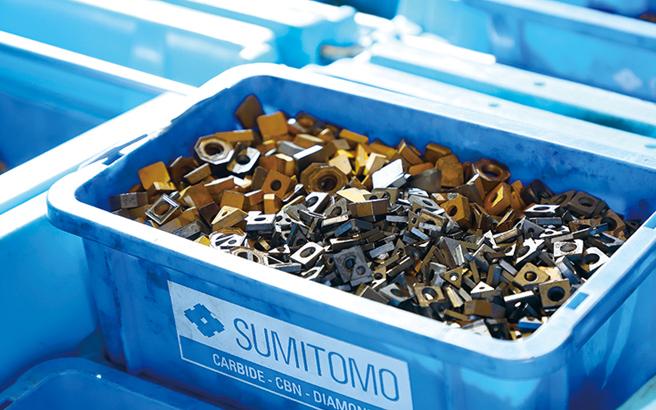


Expansion of scrap collection and processing capacity required to meet the goal
The Japanese government has set the procurement of rare metals as a national project due to changes in the environment surrounding rare metals. From the latter half of the 20th century to date, the framework of the global economy has changed significantly due to the rise and development of emerging countries, including China. Global production and consumption have accelerated, resulting in the expansion of consumption of rare metals. Against this backdrop, there has been a rising tide of resource nationalism (the belief that the resources available in a country should be managed and developed by that country) among producing countries. Tungsten is no exception. Previously, Japan imported much of its tungsten from China, which accounted for more than 80% of the global production volume. Today, tungsten is a mineral subject to export control in China. The production volume in other countries, including Vietnam and Russia, is limited. It is evident that tungsten will be depleted in the near future.
Under these circumstances, the Sumitomo Electric Group has embarked on the recycling of tungsten. This is a challenging project to free the company from dependence on imports and achieve a stable supply by recycling tungsten. The Administrative Dept. of the Advanced Materials Business Unit is responsible for procuring metallic materials for cutting tools, including tungsten. General Manager Yoshimitsu Okamori is one of the members who have led the efforts to recycle tungsten.
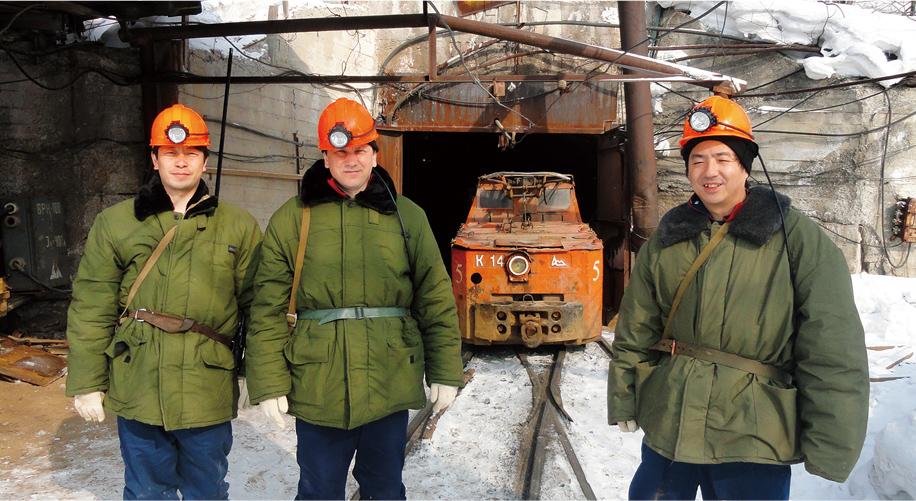
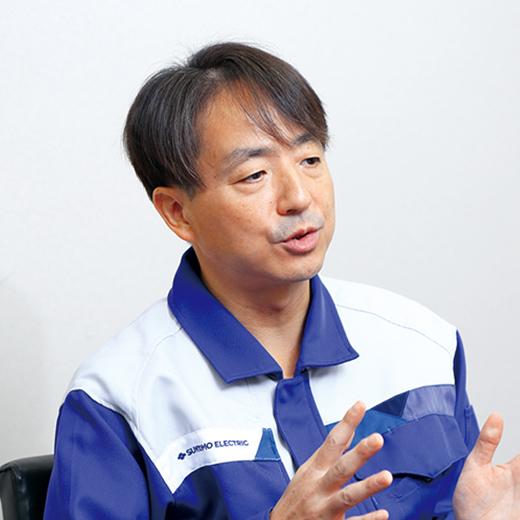
“One of the tasks of our department is to strengthen the material flow from ore and scrap to the manufacture of cemented carbide tools, which are the final products. Our solution was to establish a recycling technology and a recycling center in the U.S. [discussed below]. The Sumitomo Electric Group started recycling tungsten in the 1980s. At that time, a recycling process called the “zinc process” was used to recycle scrap into raw material powder while retaining its constituents. In 2011, Sumitomo Electric developed a new chemical process to recycle scrap into tungsten trioxide (WO3), making great strides in recycling. Today, the recycled volume is equivalent to the weight of the cemented carbide tools sold by the Sumitomo Electric Group in Japan. However, this does not necessarily mean that Sumitomo Electric products accounted for 100% of the collected scrap. Part of the scrap was exported as valuables or melted with steel scrap. Of the total scrap generated in Japan, an estimated 30% is returned to our group. As the first step, we hope to increase the percentage to about 50%. To this end, we must expand both the collection capacity and the processing capacity. In terms of achieving stable supply, we are studying the possibility of investing to acquire interests in mines in addition to promoting recycling,” said Okamori.
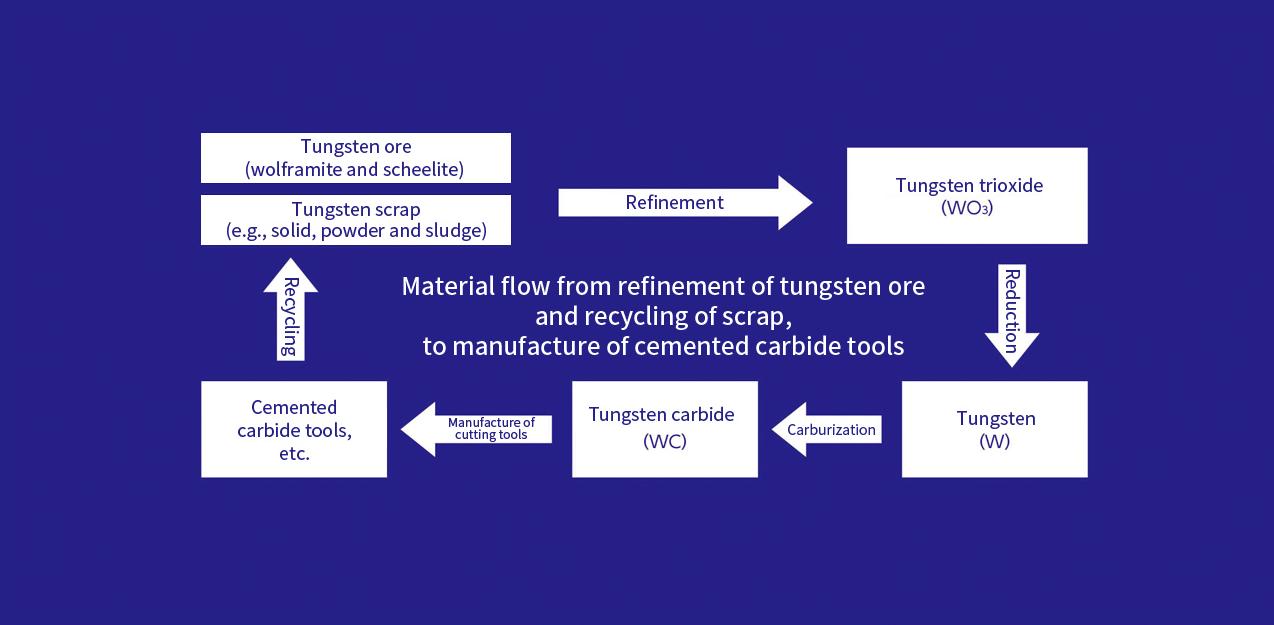
Systematic scrap collection
Cemented carbide scrap is classified into two main categories: solid hard scrap and powdery soft scrap. The former includes used or defective cutting tips, drills and dies/molds, while the latter refers to powder sludge generated during grinding and polishing at manufacturers of cemented carbide materials and cemented carbide tools. The sorting and collection of such scrap are crucial processes in the completion of a recycling system. When Sumitomo Electric started to recycle scrap in the 1980s, it also started to collect scrap. Recycling collection boxes are made available to customers, which use cemented carbide tools. The boxes, which are used to sort cemented carbide tools and other materials, are collected periodically. The company also accepts scrap from competitors’ products. It has also started collection by using a home delivery service. All the cemented carbide scrap collected is transported to the Igetalloy Scrap Center for sorting. The entire collection process is undertaken by Sumitomo Electric Tool Net, Inc., which sells cemented carbide tools. Shinji Nakao, General Manager of the Environment and Resources Sales Dept. of Sumitomo Electric Tool Net, has been engaged in the collection from the outset.
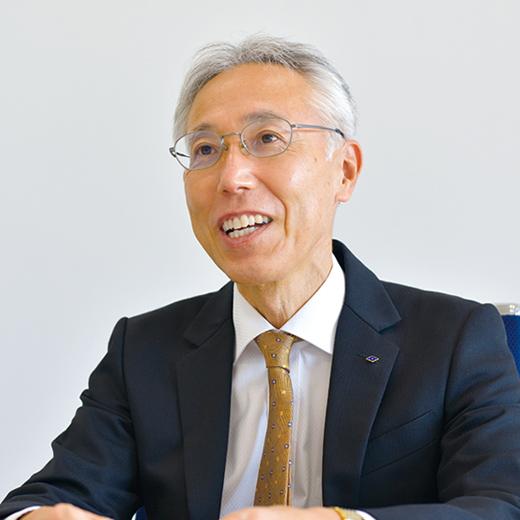
“Recycling of cemented carbide scrap is important partly because it is highly effective in terms of environmental conservation. The percentage of tungsten contained in ore is less than 1%. Meanwhile, the percentage of tungsten contained in cemented carbide tools is about 85%. From the viewpoint of refining efficiency, it is far more environmentally friendly to extract tungsten from the scrap of cemented carbide tools. It should also be noted that global tungsten reserves are estimated at about 3.2 million tons. Thus, the resource is likely to be depleted in the near future. Global competition for tungsten will intensify. We must further expand the scope of recycling to protect Japan’s manufacturing industry. While such efforts partly reflect our business strategy to encourage customers to use Sumitomo Electric products, we will publicize the importance of recycling through activities to foster motivation and raise awareness with the SDGs in mind,” said Nakao.
NEXT
New Technology That Achieved an Innovative Recycling System
– A bold challenge to achieve the oxidation wet-chemical process –