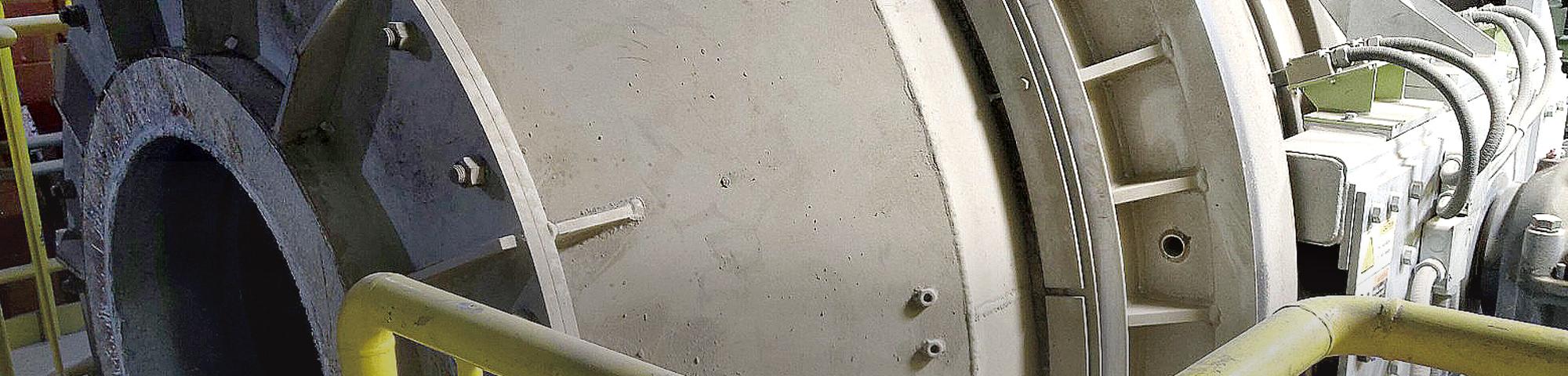
Tungsten Recycling to Start in the U.S.
To establish a global recycling system
Tungsten trioxide (WO3) manufacturing facility operated by Sumitomo Electric
In 2014, the Sumitomo Electric Group launched a business to refine tungsten ore and recycle scrap in the U.S. This business is operated by Niagara Refining LLC (NIRE), a joint venture between Sumitomo Electric U.S.A. Holdings, Inc., a wholly owned subsidiary of Sumitomo Electric and New York Tungsten, LLC, a subsidiary of Buffalo Tungsten Inc. (a tungsten powder manufacturer in the U.S.). NIRE produces WO3, which is used to manufacture raw materials for cemented carbide tools and other products.
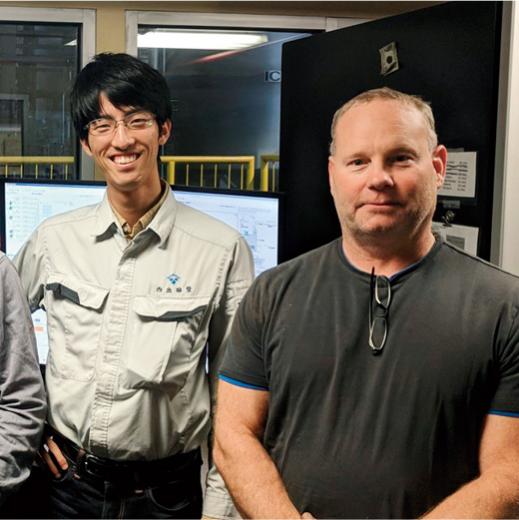
Previously, WO3 was procured by A.L.M.T., one of the Group companies, from overseas, including China, to manufacture WC powder, which was used as the raw material for cemented carbide tools. With the establishment of NIRE, the raw material can be procured within the Sumitomo Electric Group. NIRE produces WO3 by using both ore from tungsten mines and scrap collected from the market as raw materials. WO3 is then delivered to A. L.M.T. and used as the raw material for manufacturing WC. The WO3 production company was established in the U.S. for two reasons. First, the volume of scrap available was abundant from the viewpoint of deploying the recycling business globally. Second, the utility costs, including electricity, gas and water, could be reduced. Yuto Nishide currently serves as manager of the analysis department at NIRE. Previously, he had been assigned to A.L.M.T. to take care of the recycling operations. Subsequently, he acquired overall knowledge about the recycling of tungsten. In 2019, he was transferred to NIRE, whose recycling business had been accelerated by the arrival of Nishide. He was a process engineer of the manufacturing department. He was in charge of the recycling system when he assumed his position at NIRE, which was working to establish molten salt dissolution technology at that time. It should be noted that many issues remained unresolved.
A problem in the filtration process to separate impurities
“It is extremely difficult to pulverize the scrap of cemented carbide tools into fine powder for recycling. A severe environment is created to dissolve the powder at high temperature. In Japan, NaNO3, whose oxidizability is high, is used for dissolution. At Sumitomo Electric, sodium sulfate (Na2SO4) is used by focusing on the ease of handling and safety. The Na2WO4 solution is prepared in the same process as that used in Japan. The Na2WO4 solution contains impurities that remain undissolved, which must be separated in the filtration process. The first hurdle we had to overcome was the time required for the filtration process. We planned to complete the process in three hours, but it took from half a day to a whole day. The production volume was only a quarter of what we had planned. There must have been a bottleneck somewhere,” said Nishide.
Nishide listed the possible factors and practiced PDCA to tackle the causes one by one. However, there were more diverse causes than expected. There was a bottleneck in each piece of equipment, such as the filtration system, the pump, the pipe, and the tank. Nishide involved engineers and the respective departments, including equipment, analysis and manufacturing, and resolved the issues through close cooperation. The equipment department worked to eliminate a bottleneck in the pipe and pump by selecting a new pump. The analysis department worked to identify impurities, which posed a bottleneck in the filtration system. It abolished a process whereby impurities were generated, and developed a new process. Process engineers worked to eliminate a bottleneck in the tank by changing the time of starting the filtration process as a kaizen measure in the process technology. The longterm kaizen efforts, which took several months, successfully attained the planned production volume. Nishide’s initiative had a significant impact on NIRE. Almost all the employees were involved in resolving the issue. This helped build a sense of unity in the company and gave strong motivation to the employees to promote the recycling business.
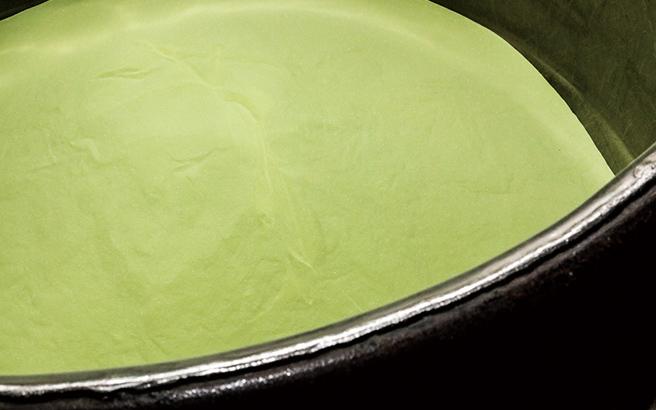
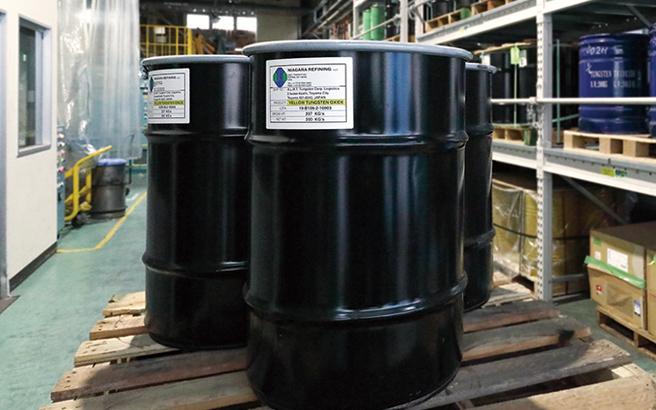
Design and construction of mass production equipment to commence in FY2022
The recycling plant that is currently in operation is a prototype. The project is still in the experimental phase. We asked Naohiro Toda, Vice President of NIRE, about the current situation and the future outlook.
“The recycling business in the U.S. faces many issues. For example, the furnace deteriorates due to chemicals used in the molten salt dissolution process. Impurities other than tungsten dissolved in the water also cause corrosion of the furnace. The series of processes is performed in an ultrahigh- temperature environment. Safety devices are activated when there are risks, resulting in frequent suspension of operation. Efforts have been made to tackle these issues based on various ideas and arrangements. We will promote kaizen by further accumulating technologies. The current production volume of WO3 is about 75% of the recycling target. The actual production volume is lower than this value partly because we are still in the experimental phase. We will establish recycling technology by the end of FY2021 and design and construct mass production equipment by the end of FY2022, which will go into full operation in 2023. A global recycling system for integrated production from raw materials to the finished products of cemented carbide tools will be completed through recycling within the Sumitomo Electric Group. We will pursue synergies by optimizing production through collaboration within the Group,” said Toda.
Achieving both stable supply and sustainability
Tungsten is not the only material that NIRE aims to recycle. While tungsten accounts for about 90% of cemented carbide tools, cobalt accounts for about 10%. Cobalt is also one of the rare metals. In Japan, it is one of the five priority minerals to be recycled. Efforts have been made to extract only cobalt from impurities, which had previously been difficult. Working hard at the recycling site, Nishide talked about the future vision.
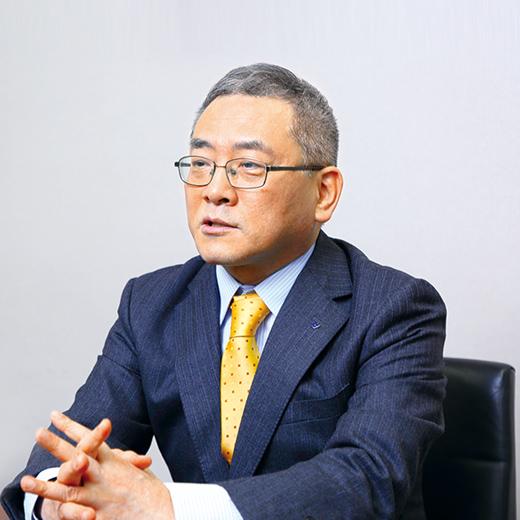
“At present, the main business of NIRE is ore refinement. We will increase the production volume through two specific measures. One is to simplify the process and create an environment where employees can work easily and promote equipment maintenance activity in order to eliminate error and trouble in the existing recycling system. The other is to develop new scrap processing technology and introduce new equipment. The environmental impact of the ore refinement business is high because waste is generated in the refining process. The recycling business is environmentally friendly and therefore has a significant advantage. It contributes to the stable supply of raw materials. We must promote the business because sustainability has become increasingly important. I hope to develop the recycling business into the core business of NIRE,” said Nishide.
NEXT
Toward a future where tungsten is recycled 100%
Recycling system developed by Toyota and Sumitomo Electric