14 May 2021
Sumitomo Electric Develops High-Accuracy Temperature Distribution Control System for Single-Wafer Film Deposition
In January 2021, Sumitomo Electric Industries, Ltd. developed SumiTune™, a high-accuracy temperature distribution control system for the front-end process of semiconductor manufacturing, in which circuits are formed on silicon wafers. This system consists of a heater and a power controller. Development of this system has made it possible to improve uniformity of temperature distribution on the surface in the wafer deposition process. The temperature uniformity of conventional single-wafer semiconductor deposition systems has been insufficient for the realization of recent advanced semiconductor devices. SumiTune™ has increased the deposition quality while ensuring high-speed deposition processing, which is characteristic of the single-wafer semiconductor film deposition system.
Semiconductor products are widely used in our society, including electric home appliances and social infrastructure. More recently, they have also been used for the 5G next-generation communication standard, artificial intelligence (AI)-enabled autonomous driving technology and large capacity storage for data centers. To improve the performance of semiconductor products, major global semiconductor manufacturers have been competing to develop technologies for miniaturization and multilayer arrangement of semiconductor device. To meet the demand for these cutting-edge devices, heaters for various temperature ranges are required to heat the wafer surface in the deposition process, in which a thin film is formed on wafers.
There are mainly two types of semiconductor deposition systems for thermal chemical vapor deposition (CVD) to form a high-purity thin film: the batch deposition system, which is capable of processing about 25 to 100 wafers at the same time and achieving highly homogeneous film thickness, and the single-wafer deposition system, which is capable of processing wafers one by one at high speeds and achieving high productivity.
Semiconductor device manufacturers take advantage of the characteristics of both the batch deposition system and single-wafer deposition system for different steps. Previously, the batch deposition system had an advantage in performance from the viewpoint of temperature uniformity. As a result, the single-wafer deposition system was not so commonly adopted in steps that required high precision.
However, the single-wafer deposition system, which is capable of high-speed processing, has attracted attention due to the increasing complexity of the semiconductor processes in recent years. In addition, there has been growing demand to achieve high-quality deposition using the single-wafer deposition system. It was an important challenge to improve temperature distribution uniformity on the wafer surface during the deposition processing.
In conventional single-wafer deposition heaters, zones were arranged concentrically to control the temperature. However, there were limitations in coping with the slight temperature distribution unevenness in the circumferential direction attributed to various environmental factors in the system. To overcome these limitations, the SumiTune™ high-accuracy temperature distribution control system has been developed.
SumiTune™ consists of a heater that has six zones (SumiTune Heater) and a controller that enables efficient and highly accurate power control of the six zones (SumiTune Controller). The features are as follows.
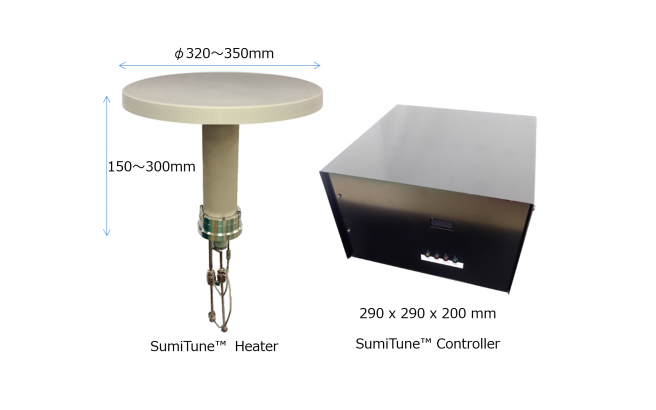
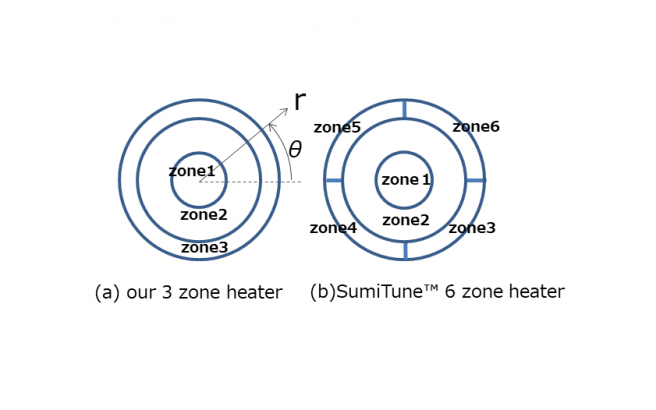
● Features of SumiTune™
(1) Capable of achieving various temperature distribution control patterns
SumiTune™ can attain temperature distribution uniformity of a ±0.5°C level (at 500°C) on the entire wafer surface. It can also be used for various temperature-sensitive deposition processes by enabling various temperature distribution pattern.
(2) Achieving fine adjustment of deposition distribution by power adjustment of respective zones on a 1-watt level
SumiTune™ can adjust the power for respective zones on the 1-watt level, which was not possible in conventional heaters. Thus, it can fine-adjust the inhomogeneous deposition distribution attributed to asymmetry factors of systems and wafers.
(3) Reducing the development period and costs
SumiTune™ enables tuning in various environments, making it possible to significantly reduce the time required for the development and reduce the number of evaluations for trial and error using wafers. This helps customers reduce the development costs.
The above features of SumiTune™ help achieve high temperature uniformity depending on the chamber environment, attain both productivity and deposition film thickness uniformity, which was not possible using conventional batch deposition thermal processing systems, and meet the need for miniaturization and multilayer arrangement of circuit wiring.
Multiple semiconductor manufacturing system manufacturers and semiconductor device manufacturers have started evaluations to have started evaluation of SumiTune™ for their adoption to mass-production process.
Sumitomo Electric remains committed to developing high-value-added products by harnessing its unique material and process technologies and thermal simulation technologies and proposing optimal solutions that can contribute to next-generation semiconductor technologies.
● Reference
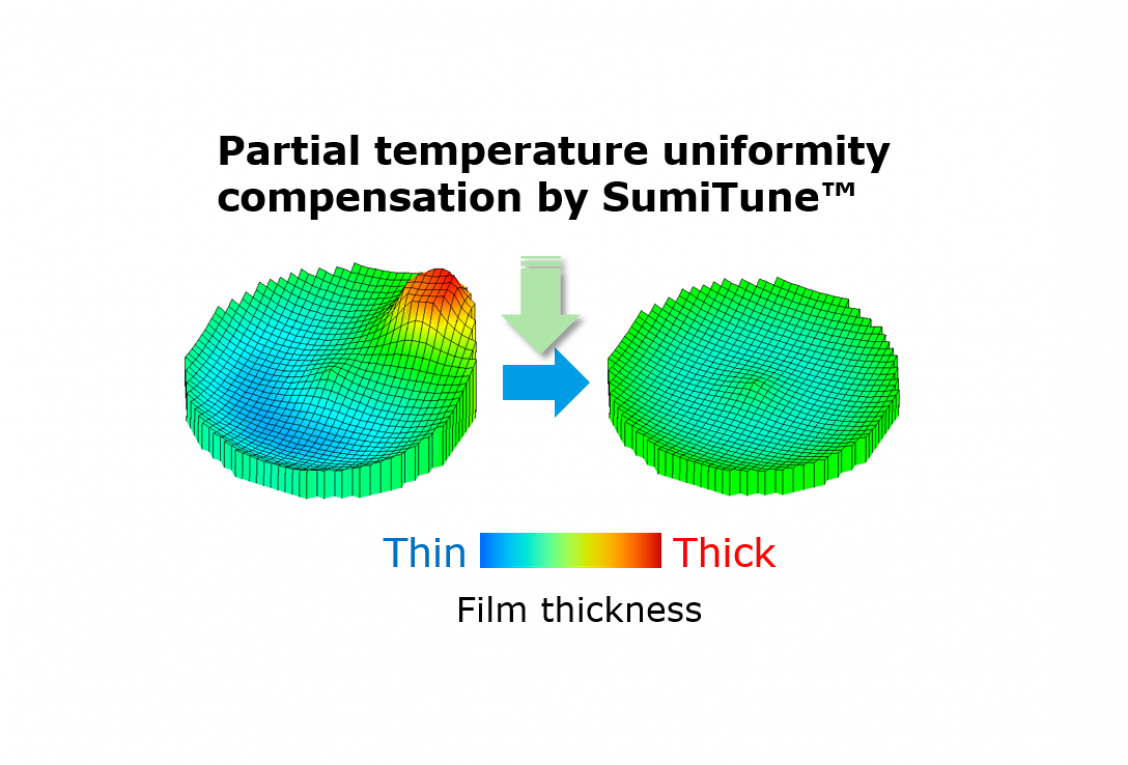