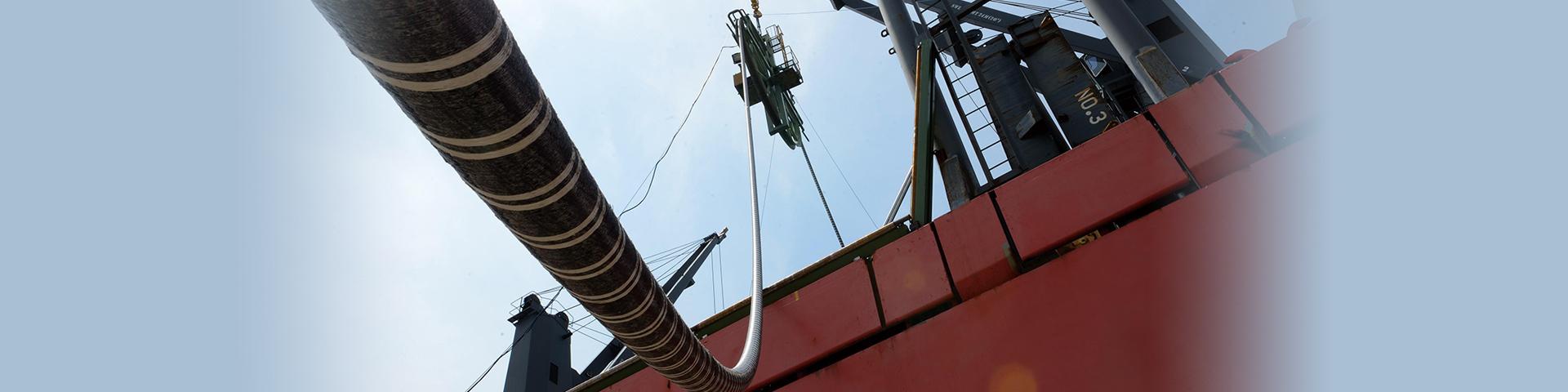
Submarine Cable
In 1921, Sumitomo Electric manufactured and supplied the first high voltage submarine cable in Japan, the world's longest cable system at that time. We have supplied over 6,000*km of submarine cables in the past 100 years.
Submarine cable is a vital component of offshore renewable energy (RE) projects such as wind farms. While submarine cables are sometimes installed in harsh environments that include currents, water pressure, high waves, or unforeseeable obstacles on sea beds. The installation of submarine cables requires much sophisticated technologies.
As one of the pioneers of the global submarine cable business, we Sumitomo Electric determines to deliver the world the comprehensive solution of design, production, installation and project management, for precisely and timely execution of complex installation projects.
*As of Aug, 2020
Project id
International Submarine Cable Project Installing the world’s highest voltage DC XLPE insulated cable across the English Channel
Read moreSubmarine Cable of Sumitomo Electric
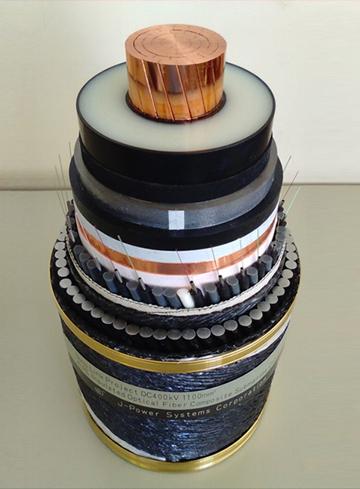
In order to obtain long-life cable performances, in general submarine cables shall have:
-
Longitudinal Water Barrier
Water-tight Conductor
-
Radial Water Barrier(for high voltage submarine cables)
Lead Sheath
-
Armour Protection
Steel Wire Armor, Steel Tape Armor, etc.
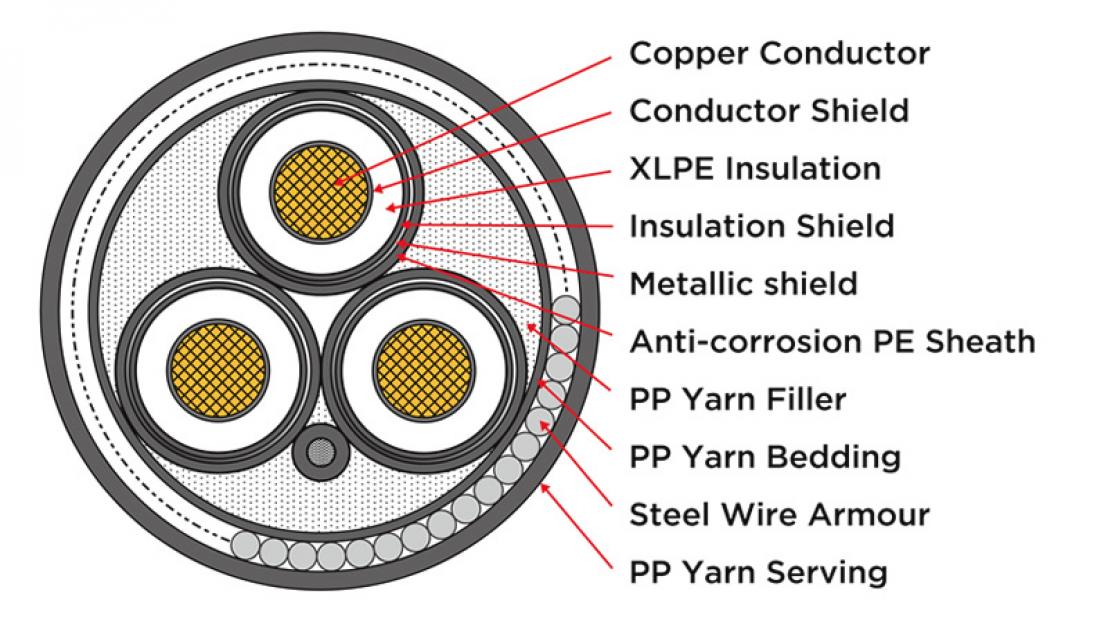
Why Longitudinal Water Barrier?
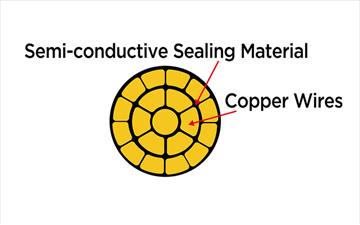
Longitudinal Watertight Conductor can limit the water migrate and minimize the repair length when cable is damaged on seabed. Semi-conductive compound or water swelling tape is applied in the interstices of copper wires of the conductor.
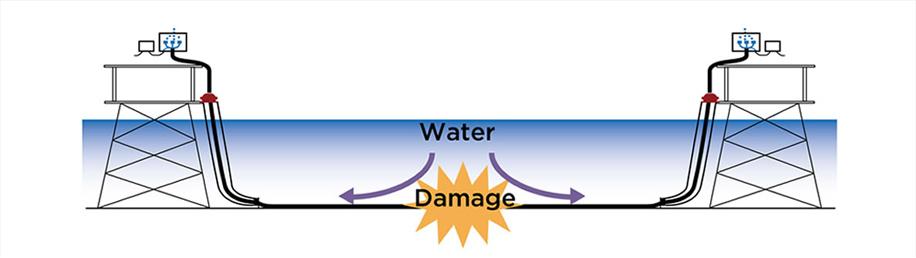
Why Radial Water Barrier?
Especially for high voltage cables, the existence of water molecules inside the insulation leads to insulation break down in the future. The radial water barrier contributes to reducing the risk of break down caused by the inclusion of water molecule. In order to achieve radial water barrier, lead sheath is applied to high voltage submarine cables. In case certain amount of water penetrates into XLPE insulation, electric field concentrates to water molecule. Then electric conductive path will be generated and get growing. When electric conductive path connects conductor shield and insulation shield, break down occurs.
Why Armour Protection?
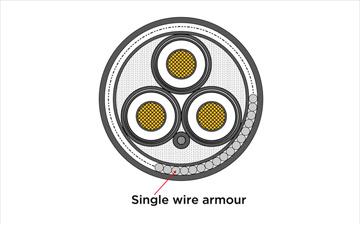
This contributes to withstand external damages and cable tension. Single, Double or Tape wire armour is applied to the outer side of the cable.
What is XLPE Cable?
XLPE stands for Cross (X)-Linked Polyethylene. Maintenance free, environmental friendly (No risk of water pollution). Currently XLPE cables are the most often used in AC cable systems. For submarine application, formerly paper insulated cables were used mainly for EHV classes, but recently XLPE cables become the main stream up to 230 kV classes. Even for DC application, DC XLPE compound has been developed and commercial operation has started.