15 January 2025
Development and Sales of Round Chipbreaker RE type for Exotic Alloy and Steel Turning
Sumitomo Electric Industries, Ltd. (Head office: Chuo-ku, Osaka, President: Osamu Inoue; hereafter "our company") has developed and launched the round chipbreaker RE type for exotic alloy and steel turning, for sale as of January 2025.
Round inserts are used to increase efficiency in the machining of heat-resistant alloys used in aerospace components, as well as the machining of bearing parts used in wind power generation and general machinery. There is a growing need for such inserts to achieve higher machining quality and stability.
In response to these needs, our company has developed the round chipbreaker*1 RE type for exotic alloy and steel turning, which achieves high machined quality and stable machining through excellent chip evacuation when turning with round inserts. In addition, we have also expanded the SEC-External Holders SRGC type/SRDC type, which can take ø8mm size inserts with RE type chipbreaker.
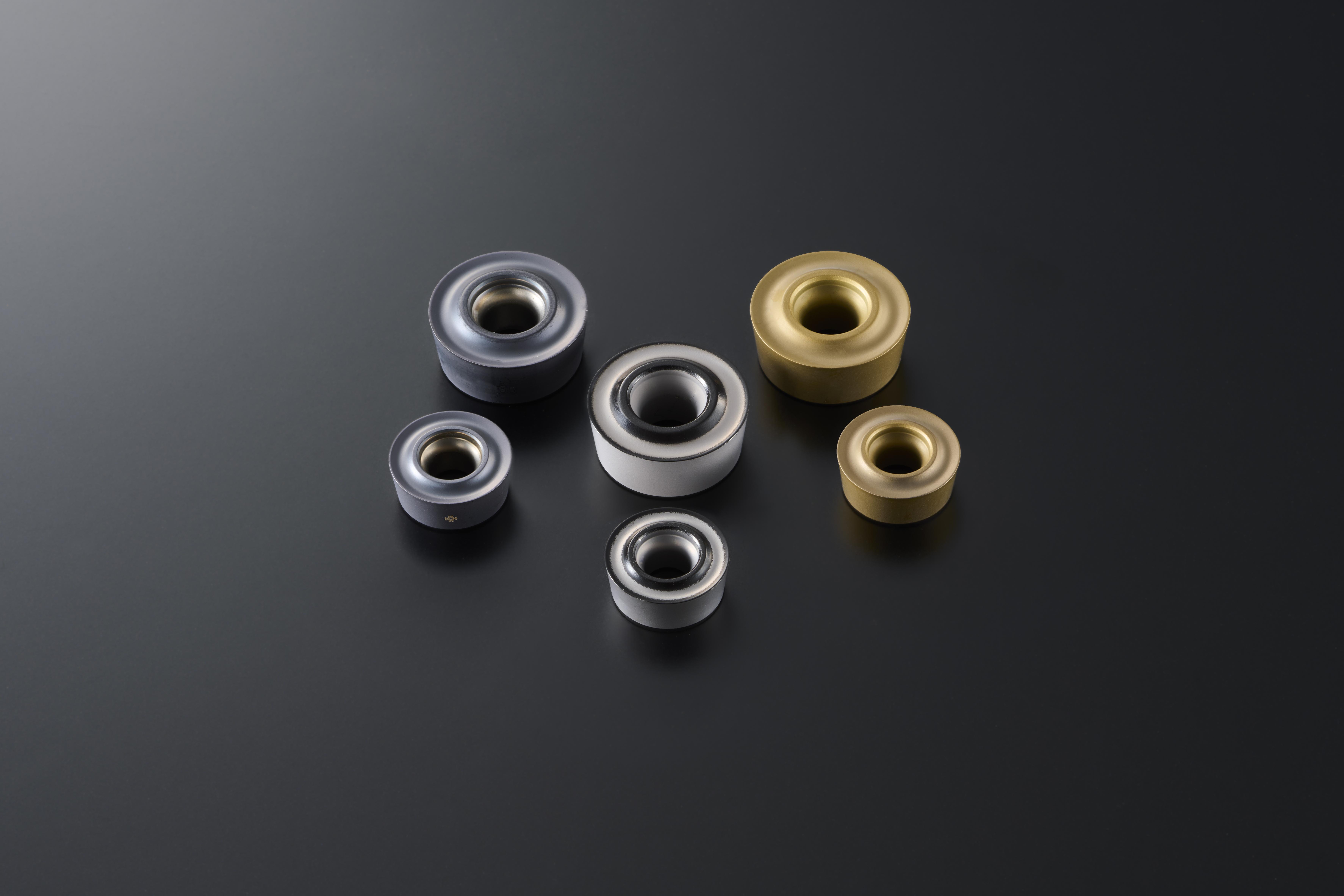
1. Features
(1) Excellent chip evacuation in machining of exotic alloys and steel
The wide and steep chipbreaker shape enables excellent chip evacuation when machining exotic alloys and steel at depths of cut of 4.0mm or below. In the machining of exotic alloys or in low depth of cut machining of steel, which are prone to elongated chips; chips are smoothly curled and broken, preventing issues such as chip wrapping or jamming around the workpiece or tool, thereby ensuring stable machining.
(2) Low-resistance cutting edge shape reduces chatter*2 and machining noise
The cutting edge design and rake have been optimised to suppress resistance, reducing chatter and machining noise, resulting in high machining quality. This contributes to solving problems with machining quality that tend to occur when machining aircraft components, which require high quality standards, and when using inserts with shapes that emphasize strength.
(3) Lineup includes CVD and PVD grades applicable to a wide range of work materials
Lineup includes the AC5000S series, ideal for exotic alloy machining, and the AC8000P series, ideal for steel machining, with both series utilizing our proprietary PVD*3/CVD*4 Absotech™ coating technology, creating a balance of excellent chip control and long tool life.
2. Lineup
M Class Positive Inserts for Turning: 21 Cat. Nos.
SEC-External Holders SRGC type/SRDC type: 6 Cat. Nos.
3. Sales Plan
17 million JPY/year in the first year, 33 million JPY/year after 3 years
4. Standard Price
M Class Positive Inserts for Turning: 820 to 2,210 JPY (excluding tax)/pc
SEC-External Holders SRGC type/SRDC type: 14,100 to 26,100 JPY (excluding tax)/pc
*1 Chipbreakers
Grooves or barriers at the cutting tip to control chips generated during machining.
*2 Chatter
Vibration generated between the tool and the workpiece during machining. Likely to occur when the equipment, work material, or tool has low rigidity or the cutting resistance is high.
*3 PVD (Physical Vapor Deposition)
A method of depositing a thin physical coating on the surface of the target material in the vapor phase.
*4 CVD (Chemical Vapor Deposition)
A vacuum deposition method which uses a gas reaction to form a thin layer of coating. In this method, raw material gas containing the ingredients of the target coating is supplied to the heated substrate material within a reaction chamber, forming the coating through a chemical reaction in gas phase on the substrate surface.
more
Keep Reading
05 August 2025