
Green Machining
Our green machining technology significantly reduces cutting resistance and enables high-speed machining by cutting the pressed (green) compact before the sintering process, while the powder is still unbonded.
Green machining also opens up shape possibilities that are impossible to achieve with conventional tooling, such as horizontal grooves, horizontal holes, and thin wall shapes, which significantly increases the degree of design freedom when working with sintered parts.
Furthermore, green machining avoids the types of burrs that are created by conventional processes while machining cross holes, so the likelihood of pressure loss or contamination of flow due to foreign matter is significantly decreased by using this burr-free method.
1. The Green Machining Process
Compared to the conventional flow of sintering processes, machining before sintering gives the advantage of reduced cutting resistance, increasing machining speed and reducing tool wear. In addition, the powder cut away during green machining can be repurposed afterward as recycled powder.
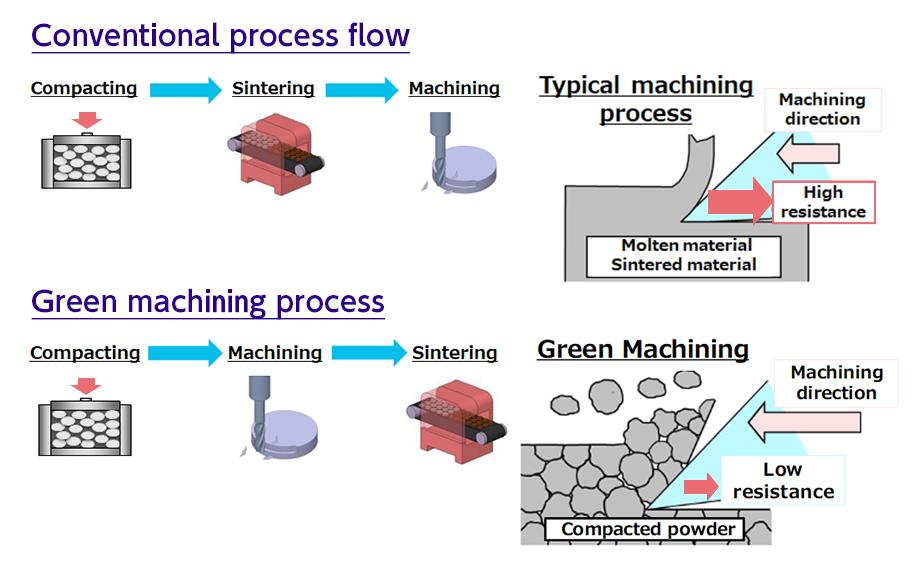
2. Machining Horizontal Grooves & Horizontal Holes
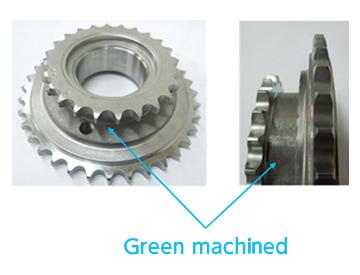
With green machining, it becomes possible to create horizontal grooves and horizontal holes that are impossible to form in the compacting process, dramatically increasing the freedom of design when it comes to the shape of sintered parts.
Utilizing green machining technology, we are able to take products that conventionally would have required two parts to be joined together, and now produce them as a single, stronger part.
3. Burr-Free Machining
Green machining eliminates the need to deburr difficult areas, such as machined cross holes.
Keeping these holes free of foreign matter helps prevent pressure loss that comes from hole clogging.
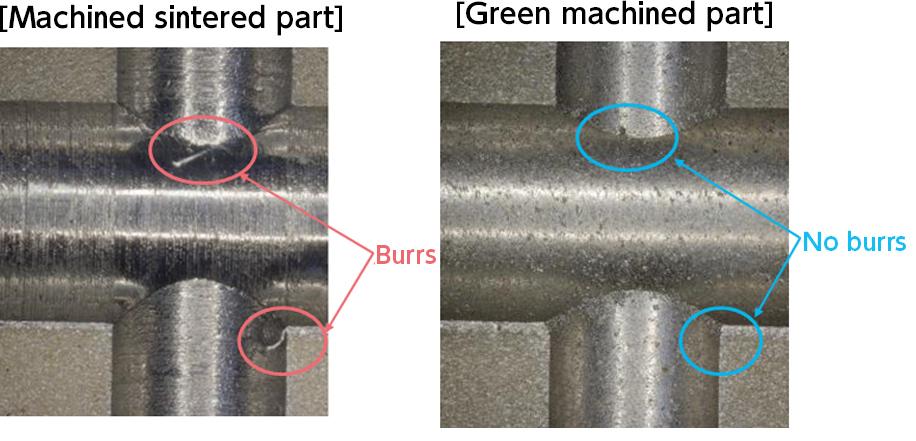
4. 100% Green Machining
We have developed the technology to form complete product shapes by applying green machining processes to high density blanks, taking advantage of the low cutting force achievable using this technology.
Although green compacts are brittle, which naturally raises concerns about chipping and similar issues, we have made full use of our years of experience developing this green machining technology for small holes and horizontal grooves to identify the optimal conditions for high-speed machining while maintaining the highest quality cut.
When products are created using 100% green machining, the final product shape can be achieved without the need for custom-ordered compacting tools, which is a clear advantage for low-volume production of a large part portfolio.