
Warm Sizing Technology combined both strength and accuracy
Warm Sizing is a technology that reduces heat treatment distortion by restraining the part in a die during the quenching process. In this way, the product can obtain the same strength as going through a hardening process, while still maintaining dimensional accuracy. Sumitomo has independently developed and proven this technology over many years of mass production experience.
Proposed applications : Rotors, cam rings, gears
1. How It Works
First, the product is heated by induction until it reaches the temperature range in which austenite (also known as gamma-phase iron, γ) forms (fig. 1).
Next, the product is immersed in oil and quenched (fig. 2). When its temperature drops to just above the MS point (the temperature at which martensitic transformation begins to occur), the product is quickly placed into a die where it is restrained (fig. 3).
To complete the process, the product remains in the die as it cools through the range of martensite formation and finishes hardening.
By undergoing these steps, the product gains both precision and strength.

2. Advantages of Warm Sizing
Sizing and quenching have conventionally been performed as separate processes, after which products needed to be machined to restore dimensional accuracy. Warm sizing achieves high dimensional accuracy by combining sizing and quenching into one process, thereby eliminating the need for further processing, which reduces machining costs.
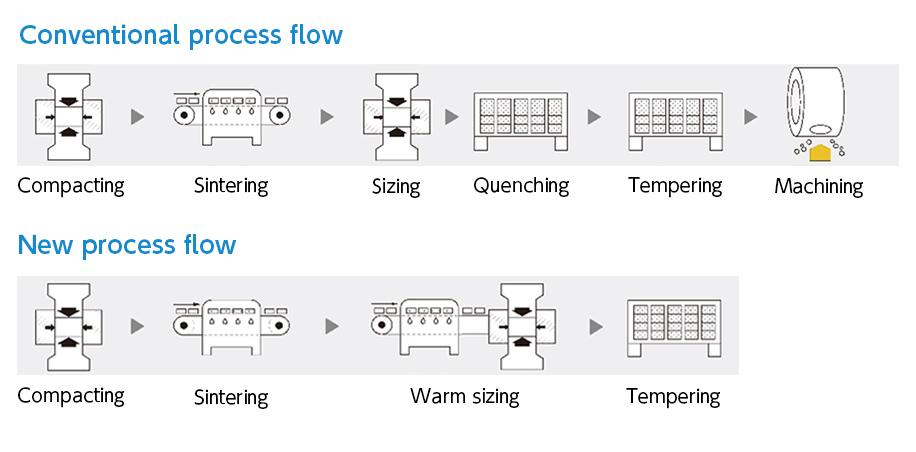