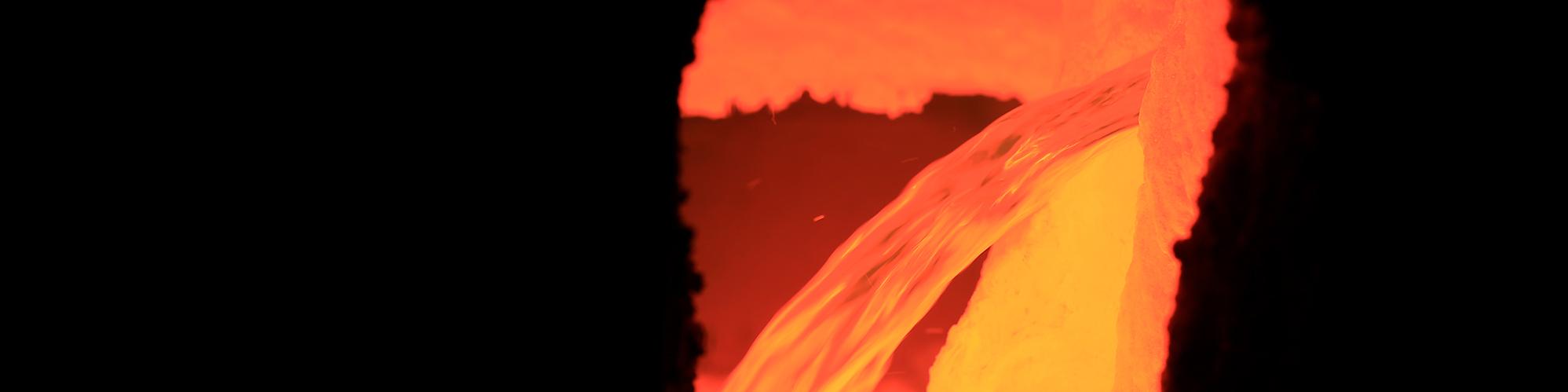
Manufacturing Site Fulfills a Set of Exacting Requirements.
Contact wires delivered through strong collaboration between sales and engineering staff
Request for Improved Performance Specifications
At the climax of contract negotiations, L&T presented us with new product specifications based on the latest engineering design change. The point was to improve the electrical conductivity of the contact wire. The project required Sumitomo Electric’s product to be highly wear resistant, because it must endure contact with the pantographs made at high speed. However, there is a tradeoff between wear resistance and conductivity. Taichiro Nishikawa, a member of the Technology Development Group of the Osaka Electric Conductor Division at the time, addressed this challenge.
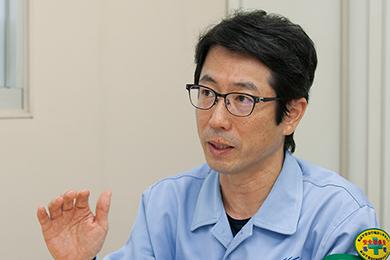
“The material we proposed was an alloy of copper and tin. In India pure copper contact wire is primarily used, while in Europe it is an alloy of copper and silver. We thought that an alloy of copper and tin would be ideal because we had used it for the Taiwan High Speed Rail, therefore improving the conductivity of the contact wire meaning reduced wear resistance. Nevertheless, we fulfilled the client’s request, making the best use of our various experiences, knowledge and expertise,” said Nishikawa.
The negotiations were in the final phase of discussing the specifications and price. The person who gave the sales staff a big push forward was Kazuhiro Nanjo, the general manager at the time of the Electric Conductor Division, which was producing contact wires. He told the sales staff that it was most important for them to have unwavering conviction, even if they failed in the negotiations. Both Hardesh and Kato were aware that it could be the last opportunity to negotiate the specifications and price. Then, in the evening, L&T contacted Hardesh to say that they wanted to meet the next day. Upon hearing that, Hardesh was convinced it was highly likely they would conclude the contract. Thus, in October 2016 Sumitomo Electric won the order for approximately 3,000 t of contact wires to be supplied in Phase 1.
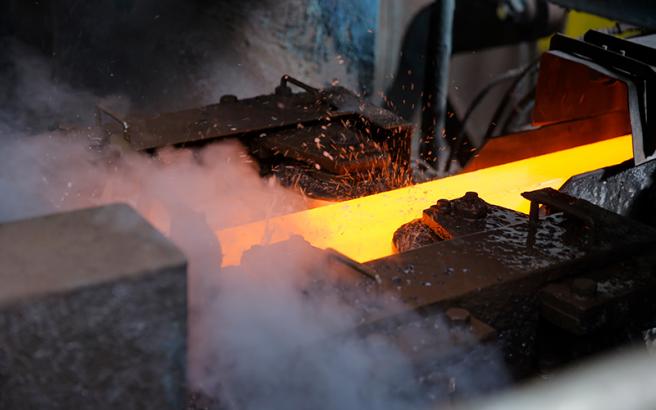

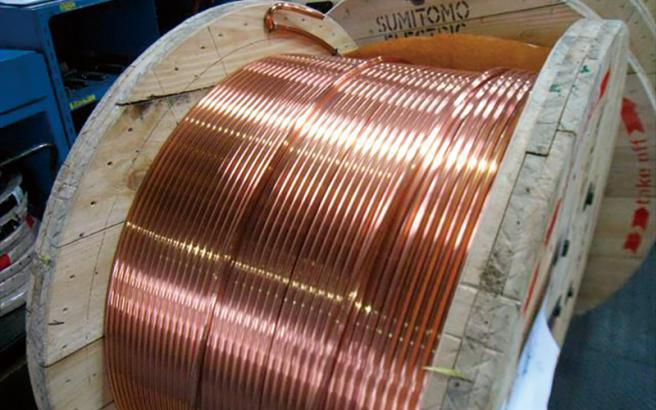
Japanese Standards (JIS) vs. European Standards (EN)
Later, Kato interviewed L&T and according to him, L&T selected the Sumitomo Electric Group most importantly because of the Group’s sincere attitude, as well as the price and delivery schedule. Moreover, the client described Sumitomo Electric as “a customer-friendly company.”
“It was a battle that required us to overcome tough negotiations. However, we gradually established a relationship built on trust, which is fundamental in business, and boosted mutual understanding. This appears to be the decisive factor in winning the order. When I knew that we had won the order, I felt a sense of relief and happiness, which, however, didn’t last long. My next task was to enable coordination between the Indian customers and our plant in Osaka,” said Kato.
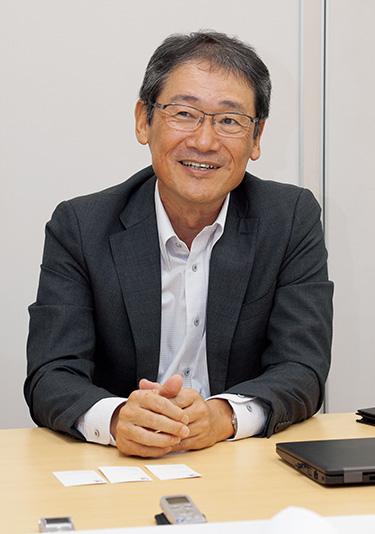
While Phase 1 required approximately 3,000 t of contact wires, the overall project required a total of approximately 5,000 t. This meant a huge, nearly four-fold, increase in production output comparted to when primarily meeting domestic demand. The challenge was to figure out how to achieve it. As a first step, Nanjo worked on improving the production framework. Among other things, it was very clear that the production framework would face a shortage of workers. He moved quickly in starting development of personnel required to provide the needed production capacity. Nanjo was confident due to his experience in carrying out production for the Taiwan High Speed Rail construction project. In early 2017, Phase 1 production commenced, followed by the building of a fully-equipped production framework in July of the same year. However, he faced an obstacle. There was a difference between India and Japan regarding the concept of quality.
“As with Sumitomo Electric, it was an important and mega-project for the Indian customer as well. So, their specifications were very detailed. They checked whether our product was accurate and strictly conformed to the specifications. Moreover, their requirements were based on European standards rather than Japanese, which were new to us. One major challenge for our production site was to establish manufacturing technologies and a quality assurance system for mass production to meet the new standards,” said Nanjo.
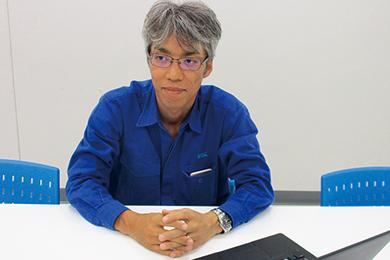
Minoru Nakamoto, Nishikawa's successor, tackled the difficulty. “At first, I was bewildered by the dissimilarities with Japanese domestic customer’s needs and by the client’s stringent requests. However, the Indian project was a test for the Electric Conductor Division to achieve subsequent leaps forward. I couldn’t fail. I identified problems by thorough studies and analyses. I became committed to shipping the bestpossible products to India and strived to develop, manufacture and assure the quality of the product as the client demanded,” recalled Nakamoto.
Steady Production and Shipping of Contact Wires
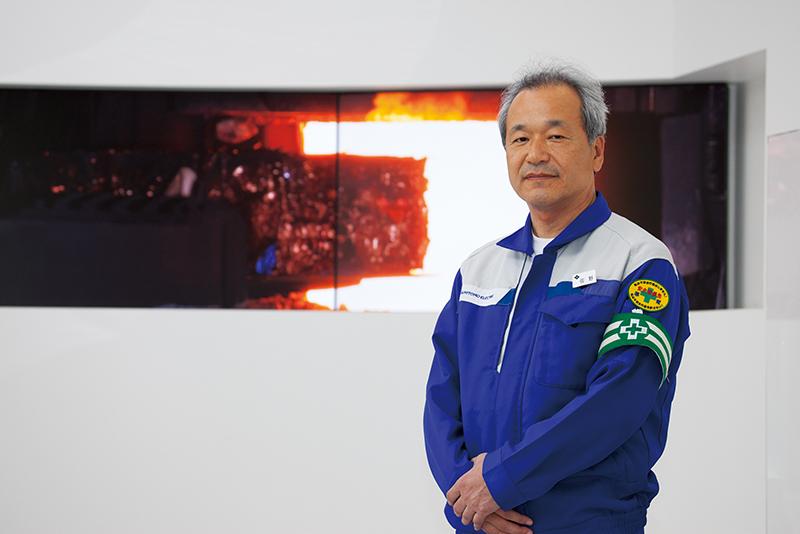
Tadanori Sano, the general manager of the Electric Conductor Division, took the post in January 2018 and began managing the production of contact wires.
“The Plant in Osaka manufactures pure copper wires used as general electric wires and copper alloy wires such as contact wires. It maintains steady production and shipping by suitably coordinating processes such as casting, wire-making and quality assurance. Moreover, it is a constantly important task to secure human resources. Accordingly, we direct our energies toward personnel development. In addition to the current project, India has concrete future plans for new projects, for which we are continuously striving to win orders. Furthermore, we intend to explore the railway business on a wider scale, for instance, in Southeast Asian countries,” said Sano.
Since 2017 to date, the plant has produced contact wires daily and shipped them at appropriate times, most of which, however, are dormant in a warehouse in India because the project has been delayed due to various factors. In early 2019, some of Phase 1 contact wires were installed. Unless rails are laid and poles are erected, it is not possible to install contact wires. The progress of the project is managed by DFC Corporation, and according to its official announcement, some sections of the railway are expected to open in March 2020, although whether or not this plan will be realized remains uncertain. Meanwhile, as Sano pointed out, a new project has been opened in India. Our course of future action depends on whether the Sumitomo Electric Group can make its presence felt in the new project.
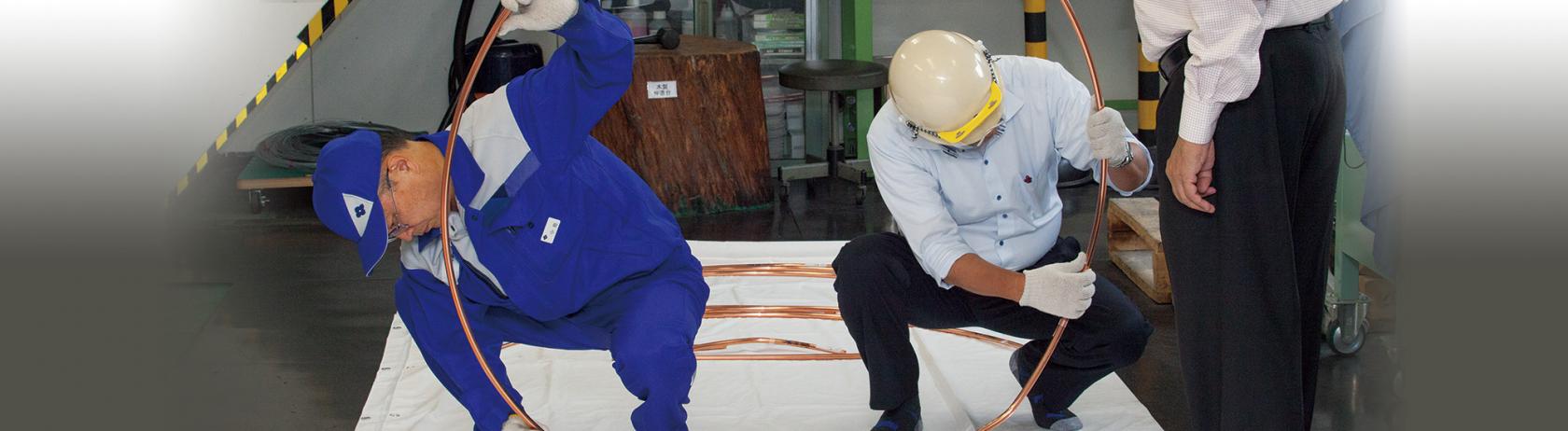
NEXT
Bring the Japanese Shinkansen to the land of India
–Vision for Sumitomo Electric Group’s railroad business–