
Optimization Proposals using CAE - Computer-Aided Engineering -
By using computer-aided engineering (CAE) technologies such as finite element method (FEM) analysis to provide customers with not only stress analysis and performance predictions of their product’s shape, but also stress analysis of potential tooling designs, we are able to proactively make adjustments to quickly reach the optimal product shape and material.
Our CAE technologies even allow us to reduce the number of components by integrating multiple parts into one, or design hollowed-out geometries that make parts lighter while maintaining all required customer specifications.
Proposed applications: Fatigue limit estimation using fatigue limit diagrams, thermal analysis, electromagnetic field analysis, topology optimization, linear/non-linear stress analysis, press-fit analysis
Flow of the Utilization of FEM analysis
In Design-in at the early design stage, FEM analysis is used to consider materials and shapes, which reduces prototyping time and shortens lead times.

Proposal for Weight Reduction using Topology Optimization Functions
By utilizing topology optimization functions to consider product shapes, we can propose lightweight shapes by removing unnecessary parts while still ensuring the required strength.
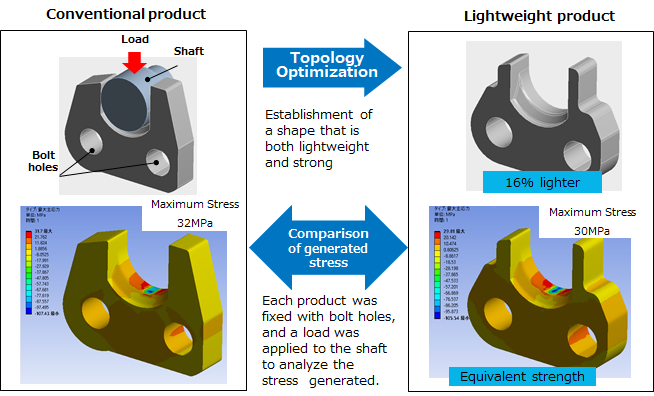
Analysis using fatigue limit diagram
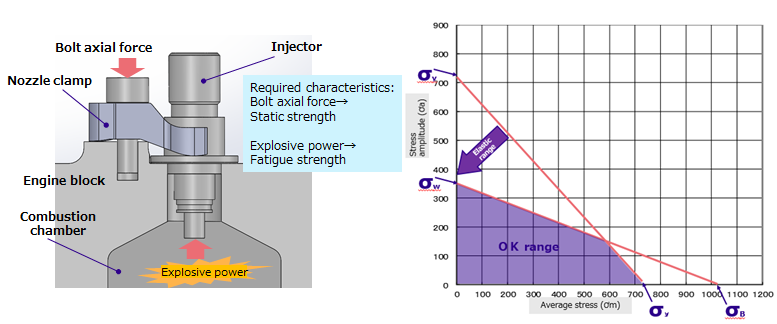
Press-fit analysis and material elastic-plastic stress analysis
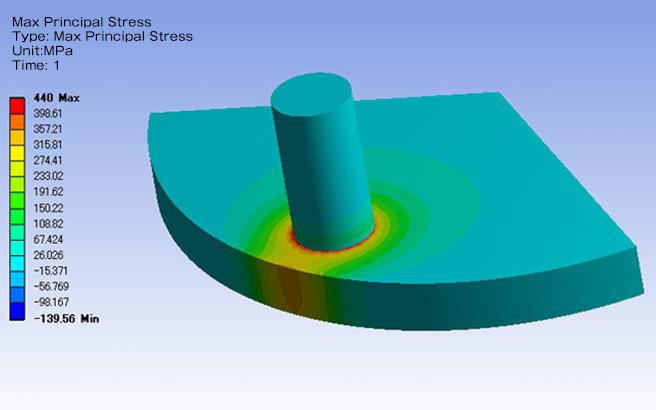
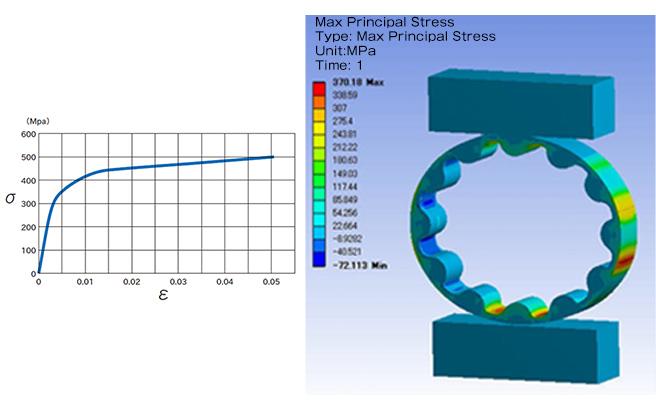
Thermal analysis and electromagnetic field analysis
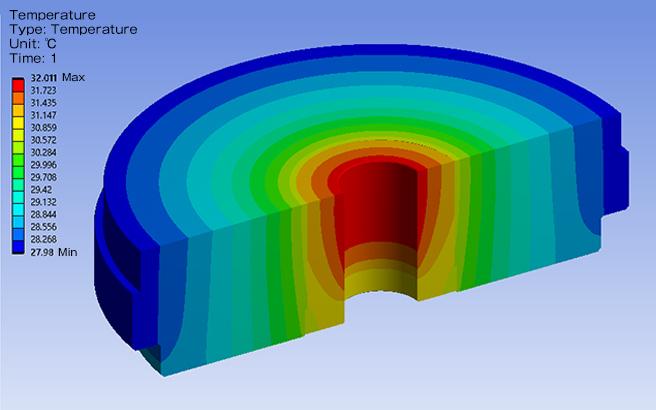
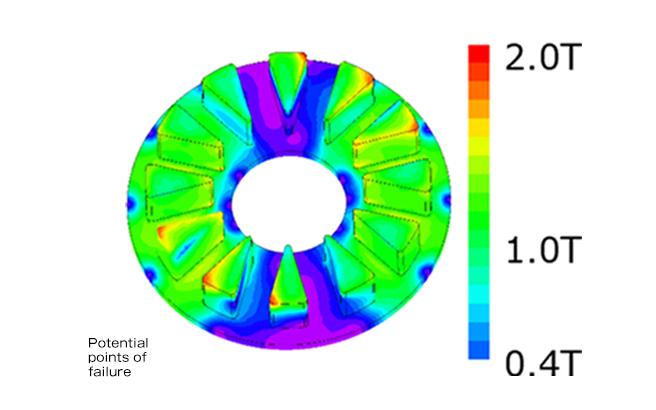