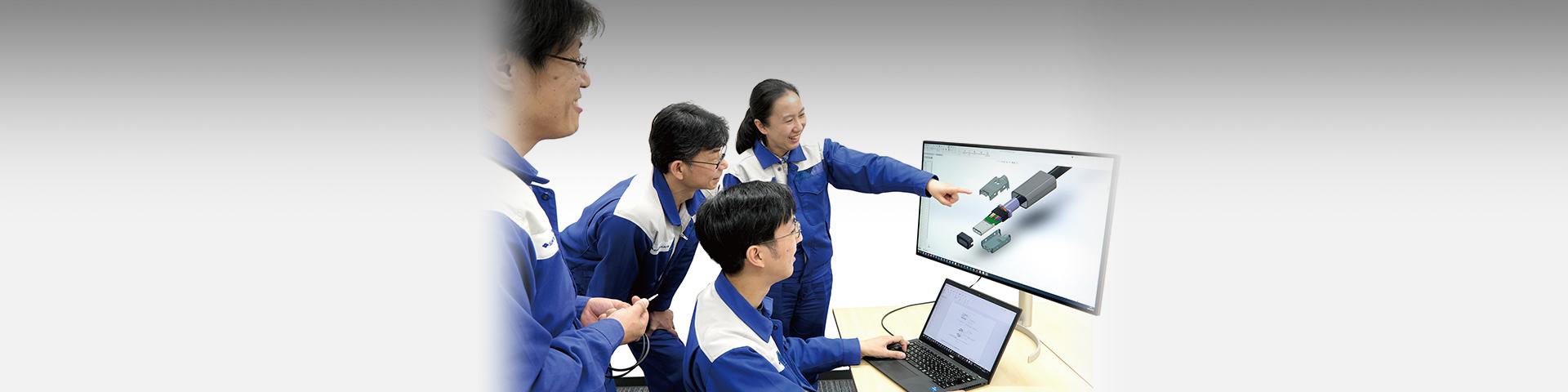
Achieving New Heights for High-Speed Data Transmission Cables
Using CG for designing (SEIW)
Acting as a Bridge Between Intel and the Development Team in Japan
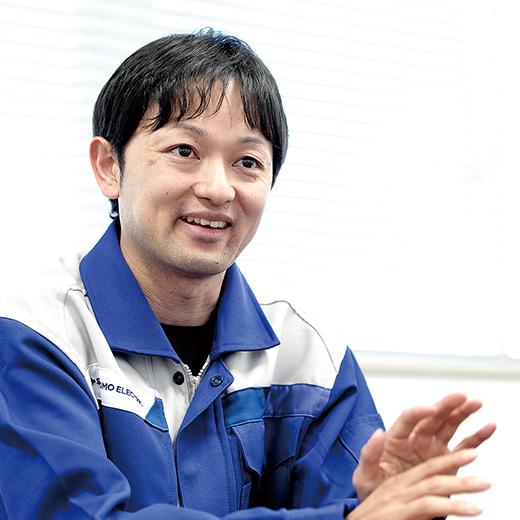
In 2011, the Thunderbolt™ Project was launched within SEIW. One of the members who took part in this project is Toru Takahashi.
“When creating Thunderbolt™, we worked with Intel to develop the specifications, including the optimum cable length and diameter, reducing transmission loss, and microtechnology for connecting cables and connectors. I felt like I was at the forefront of bringing Thunderbolt™ to the world, acting as a bridge between Intel and our developers in Japan, and creating and evaluating samples.” (Takahashi)
Takahashi then worked at a factory in Shenzhen, China to ramp up mass production of Thunderbolt™ 3 cables. He is currently leading the development team for Thunderbolt™ 5, the next-generation protocol. Yunfei Zhu, a member of that team, has been involved in the development of Thunderbolt™ 4 since 2018.
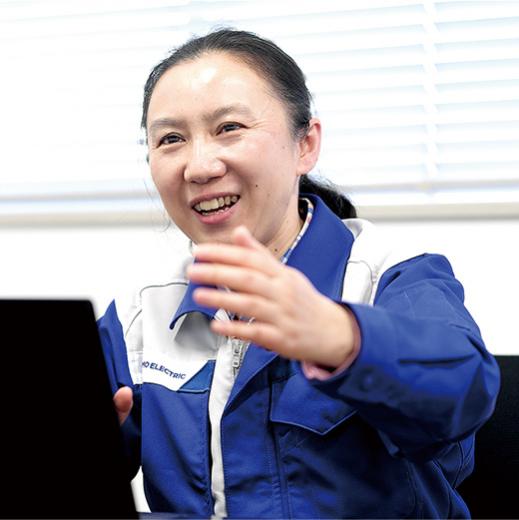
“The Thunderbolt™ 4 cable was required to be USB4 compliant while offering ultra-high speeds of 40 Gbps. An ultra-high-speed cable is a composite cable made up of a variety of wires. Each cable in a composite cable is required to be thin. My task was to change the internal structure of the cable to its optimal shape. This has made high-speed transmission possible.” (Zhu)
Takahashi and his team are expected to take the lead with regard to Thunderbolt™ 5.
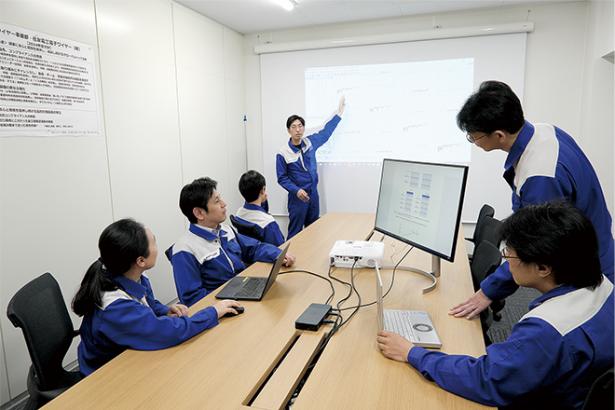
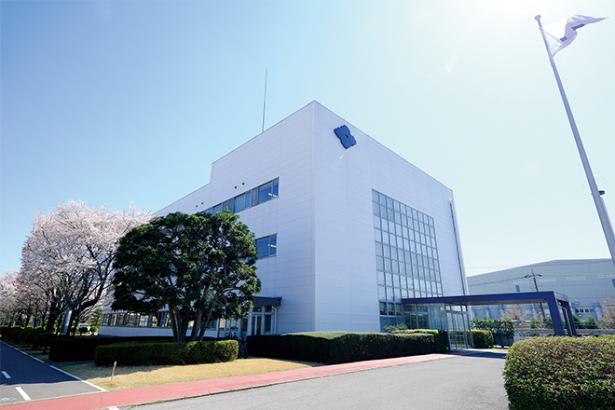
Development of Transmission Lines Compatible with High-Frequency Bands
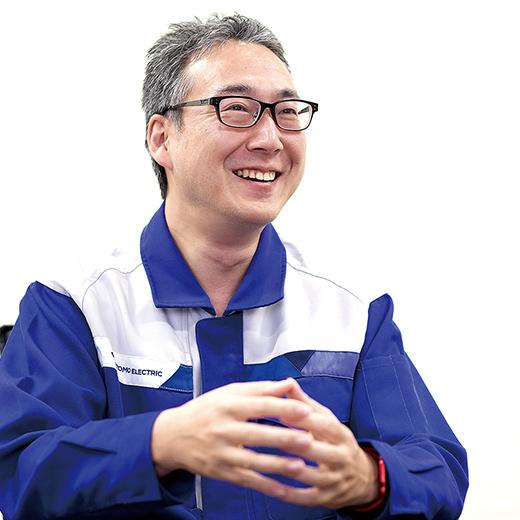
Optical Communications Laboratory at Sumitomo Electric has been collaborating with SEIW to develop Thunderbolt™ cables. Takeshi Inoue describes the laboratory's role as follows:
“Thunderbolt™ cables differ from conventional ones in that they require both circuit design and software development to occur in tandem. The question was what protocol would be suitable for exchanging data. Since this was the first time we had handled this product, we started by understanding not only Thunderbolt™ but also the history of consumer communications standards.” (Inoue)
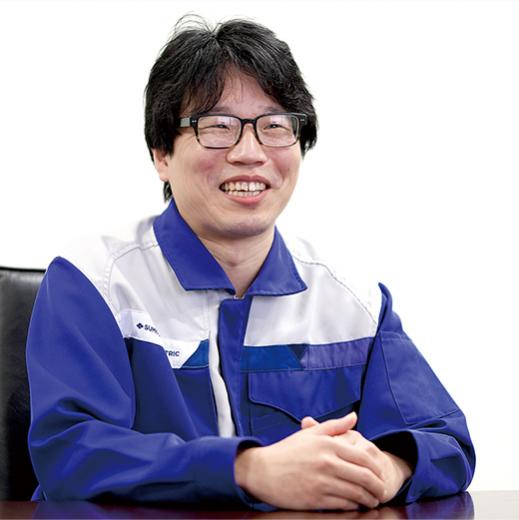
Masaki Suzuki says that when he first joined the development team, it was a trial-and-error process.
“With Thunderbolt™ as a product built to a new standard, we started without any tacit knowledge and had to go through a process of trial and error to deepen our technical understanding and proceed with development in an environment of undetermined specifications. During this process, we started from scratch, collecting data and verifying factors such as board design and transmission characteristics.” (Suzuki)
The Sumitomo Electric Group's copper cables support the world's infrastructure in the fields of electricity and communications, while its diverse optical cable products underpin the field of cloud computing. By combining the technical capabilities and knowledge of copper and optics that have been built up over a long history of development, the company was able to meet Intel's needs. In particular, adapting to new versions was one of Inoue and his team's most important missions.
“The upgrade from Thunderbolt™ 4 to Thunderbolt™ 5 doubles the communication speed. The trend towards higher speeds will continue into the future. The goal is to develop a signal transmission line that can handle greater bandwidth. We need to rethink the coaxial cable structure we have used up until now and constantly seek out and develop new solutions.” (Inoue)
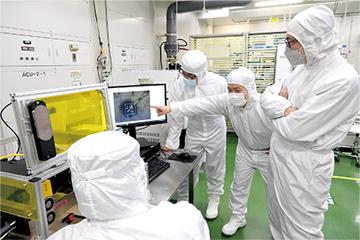
High-speed communication, in other words, a higher frequency band, means increased transmission loss. There is a constant demand for transmission lines that minimize this loss.
“Thunderbolt™ connections use connectors and circuit boards. For them, cables are essential. It feels like a never-ending battle to advance the development of technology as transmission speeds increase.” (Suzuki)
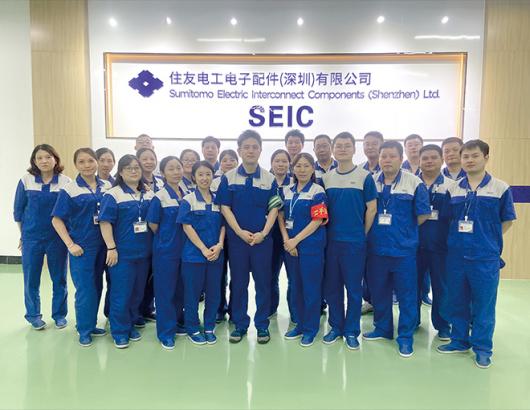
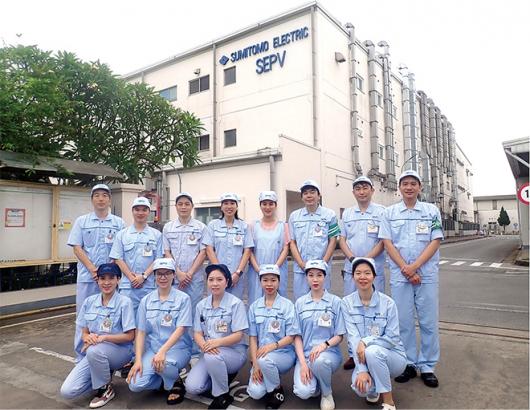