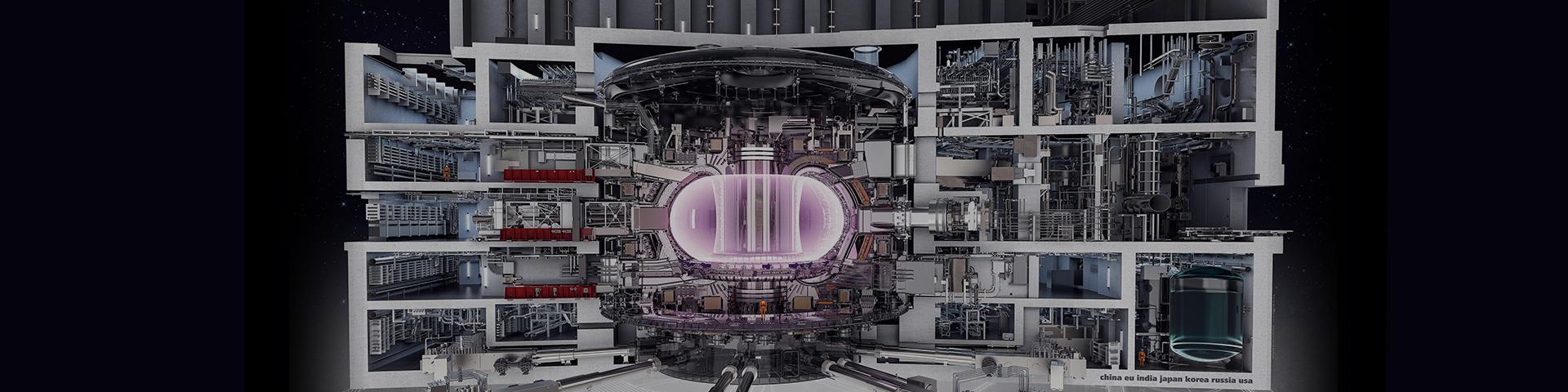
ITER as a Step to Nuclear Fusion Reactors Around the World
Operating ITER and its overview (conceptual) ©ITER Organization
Nuclear fusion evolves toward the business phase
Never give up once you decide to do it
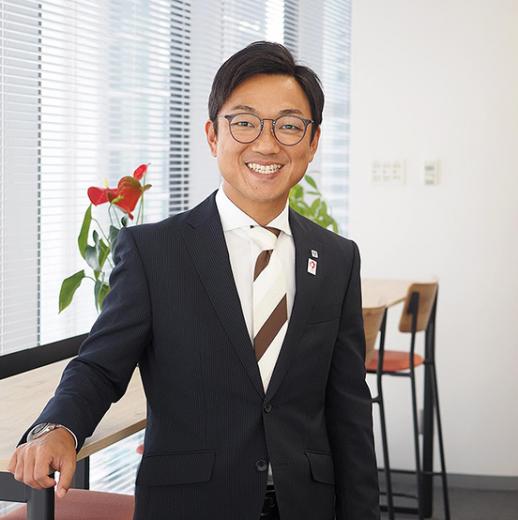
Kadokura’s efforts to advertise tungsten monoblocks to European manufacturers are beginning to steadily produce favorable results. Currently, European manufacturers must procure tungsten monoblocks only from A.L.M.T. Corp. and a Chinese company, which together have started delivering about 65,000 units since October 2022. About half of them are to be delivered by A.L.M.T. Corp. To satisfy the demand in Europe, new facilities have been introduced to the production site of the Sakata Works. Shinpei Yamamoto works for the Thermal Management Sales Department as a leader of domestic and foreign sales activities. Yamamoto took on the assignment of sales for the in-house ITER project in 2019. Since then, he has been busily engaged in the development of tungsten monoblocks mainly as a liaison with QST.
“I took over the role just before the bidding of tungsten monoblocks for actual ITER equipment. When I heard that I would play a part in an international megaproject, I had mixed feelings of pleasure and pressure. My role is to secure the delivery of products that satisfy the requirements of the ITER Organization and QST, and to help find a perfect solution acting as a bridge between the ITER Organization, QST, and the Works on every occasion. Tungsten monoblocks are entirely original products that have no standard specifications. There are many hurdles, such as unfeasible specification changes and requirements, and I will earnestly address and overcome all of them with our members,” said Yamamoto.
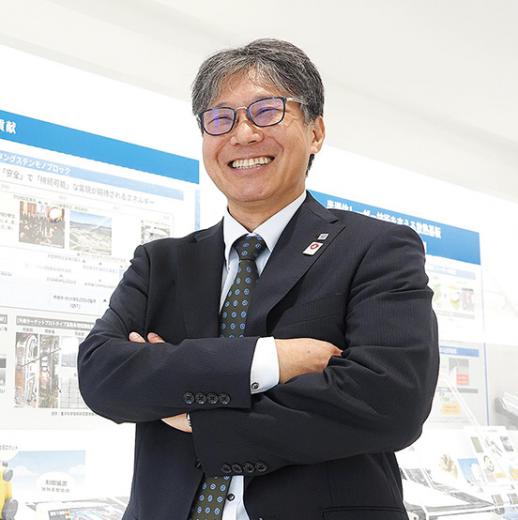
After the ITER Organization determined to adopt tungsten in divertors in 2013, Yoshitake Fukaya, a director and the manager of the Thermal Management Division, has been engaged in the project. He managed the material development to achieve unbreakable tungsten using the fine recrystallization grain control method as a manager of the Engineering Department at the Toyama Works. After 2016, he ran the business end as a manager of the Sales Engineering Department. Now he is coordinating the overall in-house ITER project from engineering to sales.
“Honestly, I was delighted with the decision on mass production. I thought that the order of 120,000 tungsten monoblocks under an optional contract was proof of trust in us. Looking back over those 10 years, we faced many difficulties. However, all project members share the company’s DNA: there is no way forward if you think you cannot do it, and you must never give up once you decide to do it,” said Fukaya.
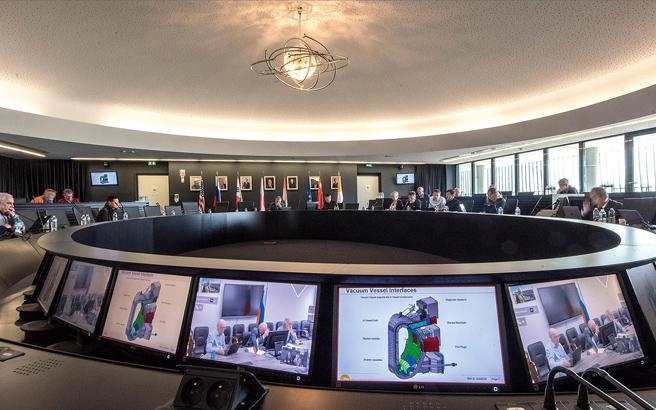
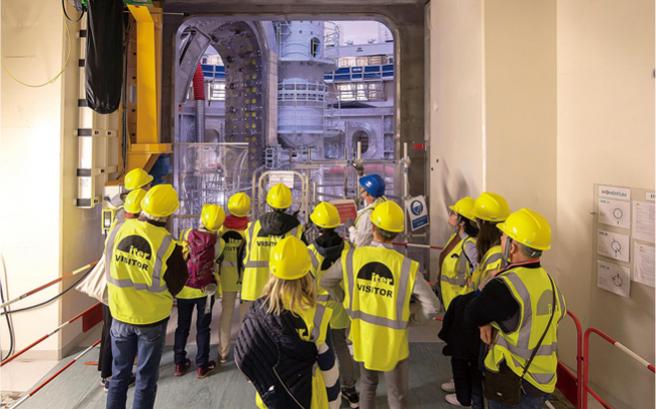
Expanding international nuclear fusion market
Nuclear fusion is moving into the business phase and moves by countries around the world are accelerating. Yamamoto at the business end says that he is strongly conscious of the moves.
“National and private research institutes have mainly conducted research and development of nuclear fusion until now. But the situation is rapidly changing. Start-ups around the world are gaining momentum. I am gathering and processing every piece of information on them to expand our business. Our tungsten is adopted in divertors because of its high durability. This feature can be applied to materials for not only nuclear fusion reactors but also other components of reactors in other industries. I will further cultivate new needs,” said Yamamoto.
Unbreakable tungsten monoblocks produced by A.L.M.T. Corp. are highly regarded. However, it won’t be until around 2030 when they are installed in nuclear fusion reactors, and by then the environment and technology around nuclear fusion might be different.
“The demonstration fusion reactor for demonstration power generation, which is planned to be constructed around 2035, will require higher durability against heat load than ever before. Under such an environment, will current tungsten monoblocks maintain this unbreakable feature? With our eyes focused on the future, we have started developing new tungsten plates with higher hardness and durability than current tungsten plates. We must have other products as a selling point other than pure tungsten plates when taking on the world,” said Kadokura.
Nuclear fusion power generation casts a bright light on the future
In this article, we learned that members of A.L.M.T. Corp. and QST share the lofty ideals of “for the future world,” contribution to society, and pride in their jobs. Their yearning for the day when nuclear fusion power generation becomes a reality, no matter how far into the future, is infused with a great depth of meaning.
Finally, let’s see the roadmap of the ITER project. The first milestone is the first plasma, scheduled for 2025, when the nuclear fusion reactor will initially be operated. Then the plasma control tests are planned to be completed around 2035. In the next phase, reaction control, engineering tests, and demonstrations using a demonstration fusion reactor for commercialization will be conducted, and then the reactor will be ready for commercialization around 2050. The roadmap is just a plan. It can be delayed due to problems or moved up due to technological advances. As mentioned above, the nuclear fusion business centering on start-ups is booming across the world. Nuclear fusion power generation, a sustainable energy source, must cast a bright light on the future society of humankind. To realize a Small Sun on Earth, A.L.M.T. Corp. and the Sumitomo Electric Group will continue to take on challenges.
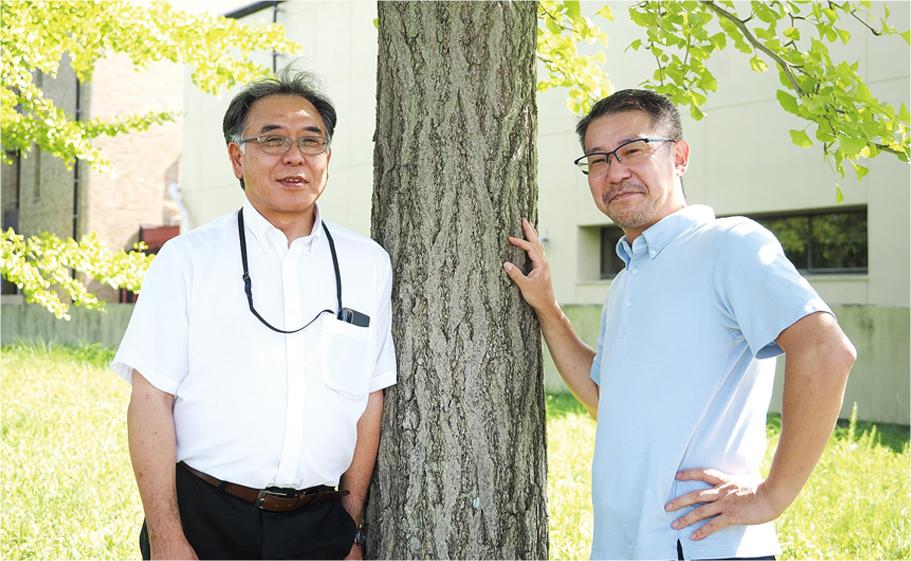
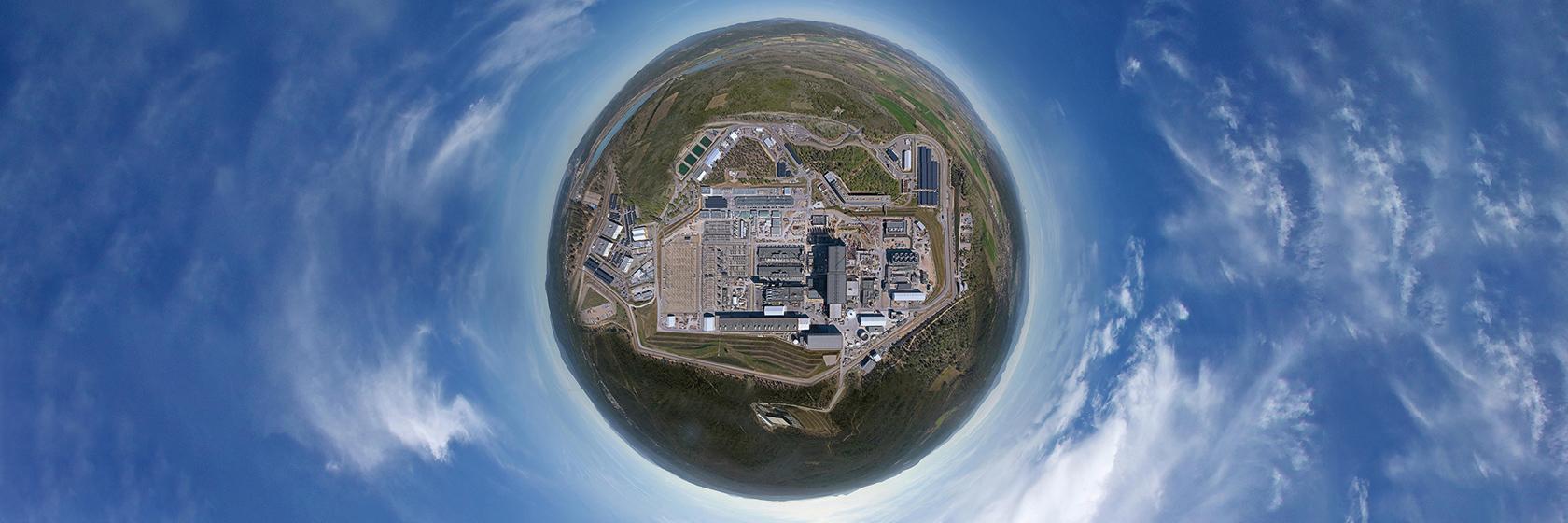