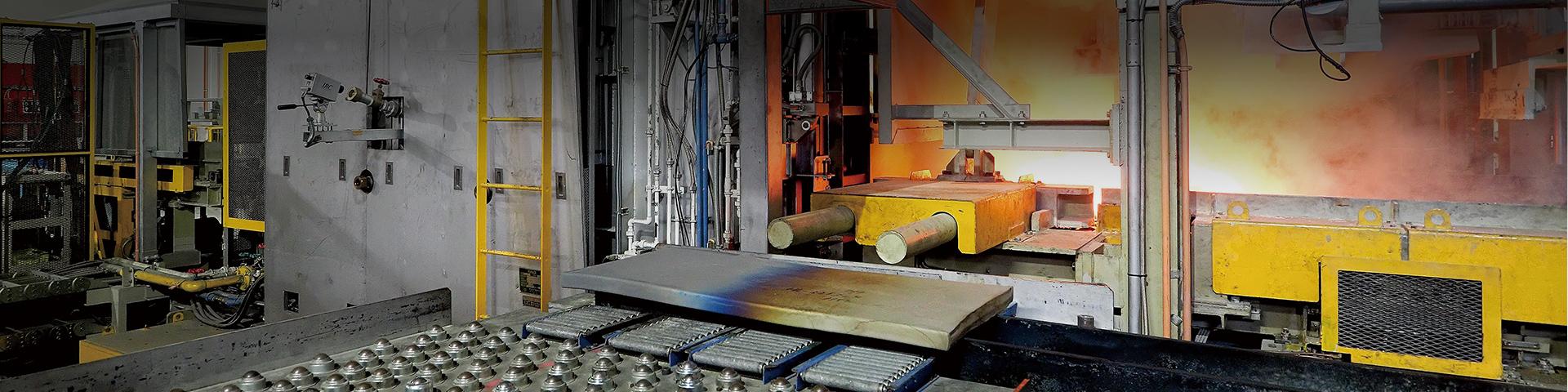
Optimizing Production of Monoblocks and Tungsten Material
Accelerating the buildup of the supply system for the world
Units developed through coordination with other companies
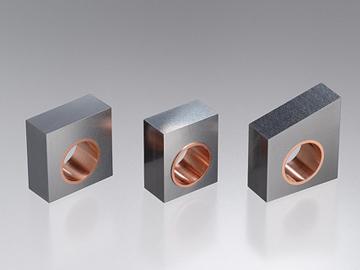
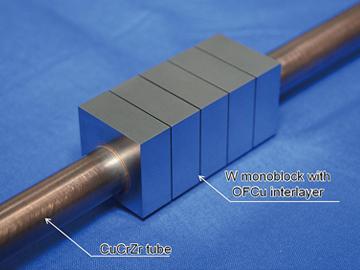
At the first bidding by QST, A.L.M.T. Corp. won a contract to supply 12,000 monoblocks in 2019, received an order of 120,000 monoblocks under an optional contract in 2021, and plans to manufacture 200,000 units in the end. Evidently, its dominant presence results from its achievement of producing unbreakable tungsten. Another important role of monoblocks is to remove heat using the high thermal conductivity of tungsten. A unit of the heat receiving surface of a divertor consists of a monoblock with a skewered cooling tube. Satoshi Suzuki pointed out that there were many hurdles to completing the monoblock, and we have made progress in clearing them.
“We made a hole at the center of a monoblock to skewer a cooling tube and attached a layer of pure copper around the hole to form a cushion. Due to the different thermal expansion coefficients of tungsten and copper, we failed to bond them. I encouraged A.L.M.T Corp. to cooperate with a competitor that has an excellent bonding technique, and we finally overcame the highest hurdle,” said Suzuki.
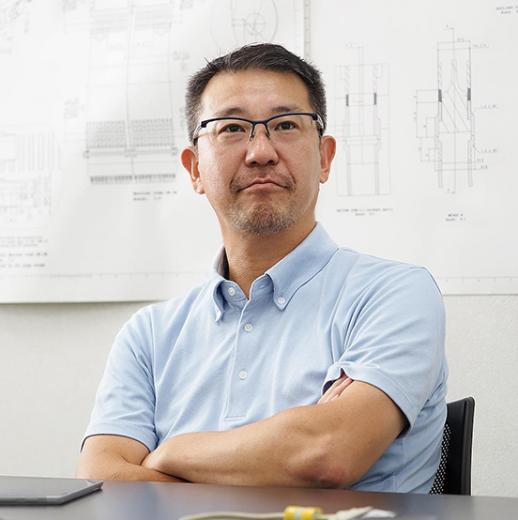
Group Leader Koichiro Ezato of the Plasma Facing Component Technology Group, Department of ITER Project, has been engaged in the development of divertors with Suzuki. He has conducted research on divertors since his graduate school days, and has great passion to achieve self-sufficiency in energy through nuclear fusion in the future.
“The divertor is an essential component for making nuclear fusion energy a reality. Since it is always exposed to high temperature, cooling the device is very important. Therefore, the development of cooling tubes was a significant theme. However, we did not know a manufacturer that could produce copper alloy with high reliability, for example, with no water leakage under the high and widely fluctuating temperatures of ITER conditions. Finally, we found a company that possessed a required manufacturing technique. I felt confident of success when the cooling tubes were completed,” said Ezato.
The fusion of techniques from A. L.M.T. Corp. and other companies in Japan enabled us to complete the unit for a divertor.
Introducing automation and IoT to secure high quality
Iikura was then transferred from the Toyama Works to the Sakata Works in Yamagata Prefecture. By that time, they had delivered monoblocks to QST as samples; however, after receiving the contract to supply 12,000 units in 2019, they had to establish a new mass-production system. Until then, they had been producing each monoblock by hand. Iikura thus started establishing a new automated production line.
“Needless to say, tungsten monoblocks installed in nuclear fusion reactors are without precedent. I aimed to achieve absolutely high precision and traceability. Since problems are inherent in manufacturing, I inscribed QR codes on monoblocks to clarify the production history in the production system by using IoT and QR codes assigned to monoblocks,” said Iikura.
At the beginning, however, the system did not work well. The yield rate was very low and defects were frequently detected. Automation does not always lead to stable quality. The machining requires high precision in the order of 10 μm, but it nevertheless produced errors due to heat and contact with each monoblock. Precision requirements were not to be compared with conventional ones. To solve the problems, Iikura and other members improved the precision of the jigs used for machining, and even developed new jigs. Their efforts bore fruit and stabilized the quality, bringing the production on track. After QST ordered monoblocks for actual equipment in 2021, new production lines started full-scale mass production from 2022. He always keeps in mind how to address unforeseeable problems. His pursuit of keeping high quality through stable operation of facilities will never end.
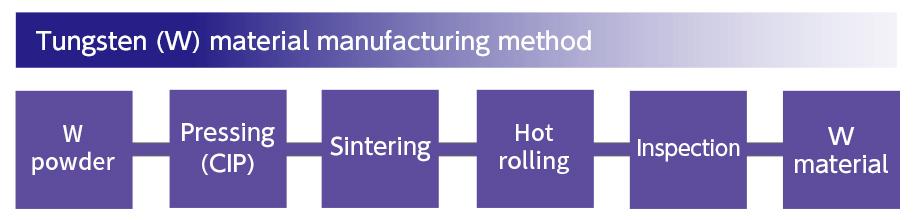
For adoption of our tungsten in Europe’s inner vertical targets
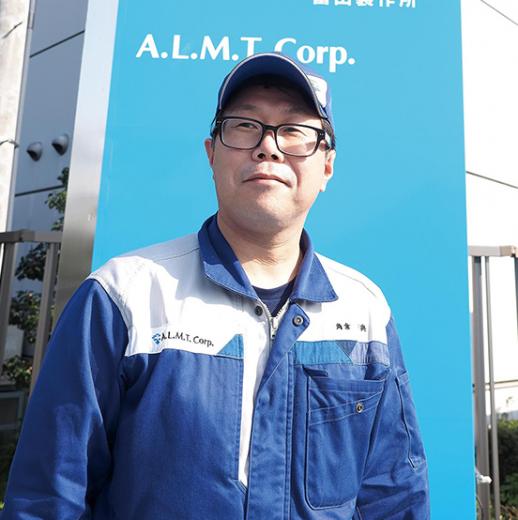
Tungsten plates, a material of monoblocks, are manufactured at the Toyama Works. Takanori Kadokura, Deputy Manager of the Engineering Department, is engaged in production engineering. Kadokura has worked in the development of tungsten and molybdenum at the research and development division for 20 years since his first year at the company. He participated in the ITER project in 2018. He also took charge of developing unbreakable tungsten with Iikura. One of his missions now is securing stable quality in tungsten plate production like the monoblock production.
“Tungsten plates are manufactured through the processes of pressing tungsten powder and rolling a sintered body, and optimum balance of these processes produces the unbreakable feature. I focused on raising awareness and improving the motivation of workers. To achieve higher quality, I have united the Works,” said Kadokura.
Kadokura has another mission. A.L.M.T. Corp. has now supplied tungsten monoblocks for outer vertical targets. Kadokura’s other mission is to advertise the tungsten monoblocks to European manufacturers that undertake inner vertical targets for order-taking.
“I contacted three European manufacturers. One of them completed prototype evaluations, and our material successfully passed the acceptance criteria. Our tungsten monoblocks were also certified by Fusion for Energy, a joint undertaking that is responsible for the EU’s contribution to the ITER project. Their adoption process differs from our domestic process in many respects, so I have promoted activities of asking companies to evaluate our tungsten monoblocks. Furthermore, I am investigating the demand for monoblocks for divertors used for nuclear fusion reactors developed by other research institutes in Europe, aside from the ITER project, to expand the business,” said Kadokura.
NEXT
ITER as a Step to Nuclear Fusion Reactors Around the World
– Nuclear fusion evolves toward the business phase –