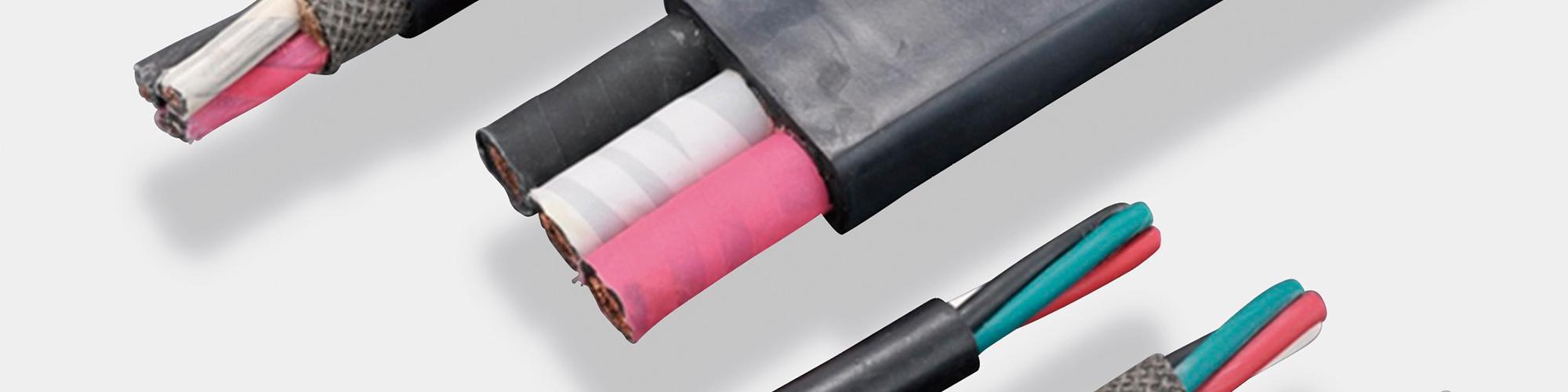
Develop Flexible, Strong and Stress-Free Electric Wires & Cables①
Story behind the development of S-FREE™
Accommodating diversified and advanced user needs
Industrial electric wires and cables used to be handled by the Power Cable Division as a part of its product category; however, the team in charge was separated as an independent division since the range of customers was highly diverse and the required quality and properties were becoming increasingly diversified in response to changes in society. A major turning point came in 2014. Among various industrial wires and cables, Sumitomo Electric focused on traveling cables and insulated wires in electric equipment and panels, which had been handled by its affiliated companies, restarting the business of the products under a new brand. “Behind this decision were changes in society and user needs,” says Takahisa Hiura, President of Sumitomo Electric Industrial Wire & Cable Inc.
“Since the start of the 21st century, the need for improved productivity and efficiency has been growing more than ever; as a result, reformation of manufacturing sites and technical innovation are accelerating. In particular, the on-site needs of traveling cable users are highly diversified; therefore, it was a good business chance as well as an important mission for the Sumitomo Electric Group to develop and provide products that can flexibly and quickly accommodate their needs,” says Hiura.
What are the “on-site needs,” Hiura mentions? For example, traveling cables are used at sites with harsh environmental conditions. In addition, they are used as power cables for moving objects, not as fixed wiring, so the cables themselves are prone to suffer external damage. For that reason, traveling cables have been required to possess various properties, such as wear resistance, shock resistance, water resistance, heat resistance, flexibility and fire retardancy. Meanwhile, the development of a new brand, afterward named “S-FREE™,” had started.
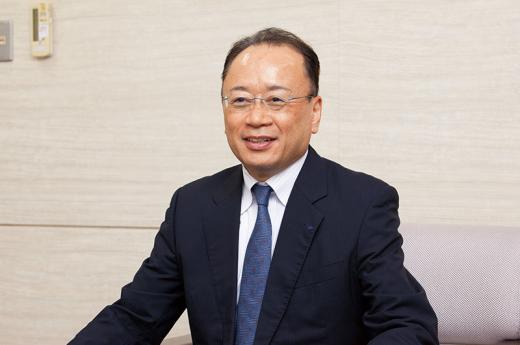
“Since the start of the 21st century, the need for improved productivity and efficiency has been growing more than ever; as a result, reformation of manufacturing sites and technical innovation are accelerating. In particular, the on-site needs of traveling cable users are highly diversified; therefore, it was a good business chance as well as an important mission for the Sumitomo Electric Group to develop and provide products that can flexibly and quickly accommodate their needs,” says Hiura.
What are the “on-site needs,” Hiura mentions? For example, traveling cables are used at sites with harsh environmental conditions. In addition, they are used as power cables for moving objects, not as fixed wiring, so the cables themselves are prone to suffer external damage. For that reason, traveling cables have been required to possess various properties, such as wear resistance, shock resistance, water resistance, heat resistance, flexibility and fire retardancy. Meanwhile, the development of a new brand, afterward named “S-FREE™,” had started.
Grasping “true” needs through communication with users
What issues should be addressed by the development of new brand products? Finding the answer to this question is a task of the sales staff, who closely communicate with users on the front line of the market. Hiroshi Omi of the Engineering Department, Industrial Wire & Cable Division is one of the staff members who support sales staff from the aspect of engineering. Omi has endeavored to grasp “true needs” by frequently analyzing market trends and communicating with users.
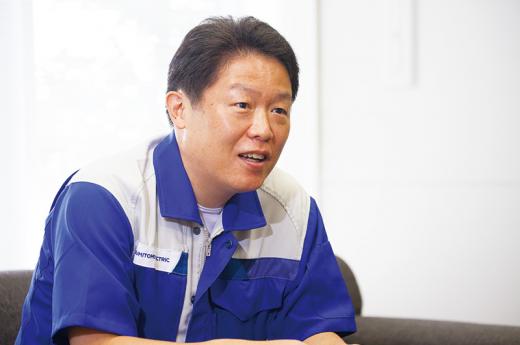
“We are always looking for clues about product development and modification. Naturally, the products developed or modified must provide a solution to an issue that users face. We often find a clue about product development by hearing requests from site workers or observing their work. I realized that requests from users were not constant but variable, depending on their work environments and personnel organization,” says Omi.
For example, after the Great East Japan Earthquake, the standards required for cables used at power plants became stricter. Fire retardancy was one of the raised standards. As a result, it became necessary to develop a sheathing material for traveling cables that can pass the vertical tray flame test, one of official flame test methods. Sheathing materials are made of chloroprene rubber (CR). To satisfy the required fire retardancy and other properties such as tensile strength at the same time, it was necessary to determine the optimal material formulation. How has this kind of issue been addressed?
Fostered formulation technologies
Even for sheathing materials, the Sumitomo Electric Group conducts all operations, from the research and development of material formulation to production, within the Group. Therefore, in order to develop easy-to-use electric wires and cables, all component materials, from conductors to sheathing materials, are thoroughly examined. Material technologies owned by the Group, including those for product categories other than industrial wires and cables, are fully utilized.
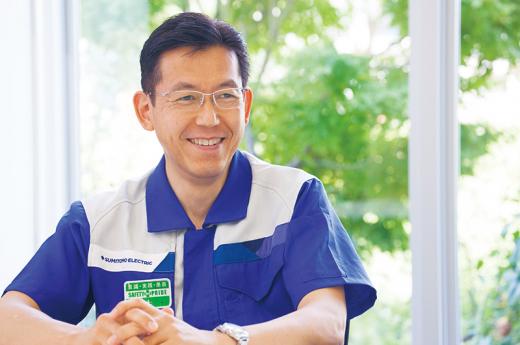
“The sheaths of traveling cables and insulated wires in electric equipment and panels are made of polymer composite. Material development is an activity intended to create a new formulation, or the optimal “recipe” of materials and additives. The Sumitomo Electric Group owns advanced formulation technologies based on technical know-how accumulated over the years in various industries, such as electric power, automotive, information communication and electronics. Such technologies serve as our driving force to create products that meet customer needs. Of course, they were utilized to improve the fire retardancy of traveling cables,” says Shinya Nishikawa, Manager of Polymer Materials Department, Energy and Electronics Materials Laboratory.
Features required for S-FREE™
Besides the required properties, what consideration was given to the design of traveling cables and insulated wires in electric equipment and panels released under the brand “S-FREE™”?
As a latest development, technologies for traveling cables were applied to cables for charging electric vehicles (EVs). EV charging cables are frequently dragged on hard ground surfaces such as concrete due to the repeated action of connecting and disconnecting the charging connectors, so they need to have resistance to drag (wear resistance). However, in general, as the wear resistance increases, the material becomes harder, consequently making the cable less flexible.
Sheathing materials for these cables were developed by the Polymer Materials Department, a team specialized in the research and development of polymer composite at the Energy and Electronics Materials Laboratory of Sumitomo Electric. Taro Fujita and Shigeyuki Tanaka of the Electronic and Electric Materials Group are core members of the development team.
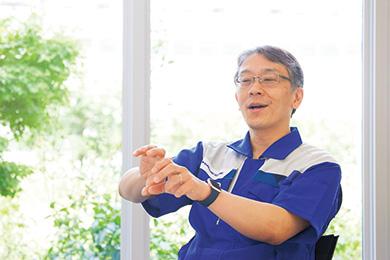
“The primary requirement for EV charging cables was wear resistance, but considering handling by the public, the flexibility of the sheath was also important since it has an influence on the flexibility of the cable itself. However, as the wear resistance increases, the material usually hardens. It was important to realize a good balance between these trade-off properties,” says Fujita.
Fujita focused on creating a composite of CR and mineral-based particles (filler). Hard filler dispersed into rubber prevents damage caused by drag, increasing the wear resistance. Fujita created an optimal recipe (formulation) that can realize satisfactory wear resistance and flexibility by discovering a special filler that does not harden the material.
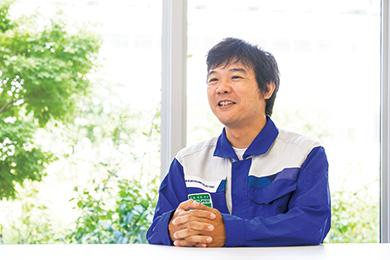
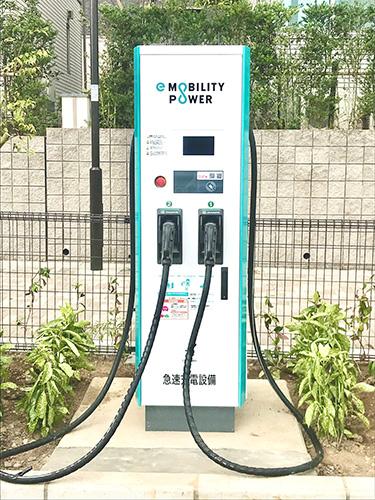
As a latest trend, an increasing number of companies proactively adopt eco-friendly cables as a means of achieving the SDGs, initiatives to realize a sustainable society. Use of eco-friendly materials is also proceeding in the category of traveling cables; however, eco-friendly materials have the disadvantage that, in general, they are harder than conventional sheathing materials.
“CR used for conventional traveling cables produces harmful gas such as hydrochloric gas in the event of a fire. For eco-friendly traveling cables, ethylene propylene rubber (EPR), an olefin-based synthetic rubber, is used. Required fire retardancy and other properties such as mechanical strength can be satisfied by using halogen-free fire retardant, but there is inevitably a trade-off with flexibility,” says Tanaka.
Tanaka focused on the molecular structure of EPR. A large part of rubber has a non-crystalline molecular structure, and the remaining small part has a crystalline molecular structure. The flexibility can be increased by reducing the hard crystalline structure, but the strength decreases. Therefore, Tanaka increased the mechanical strength by extending the chain of EPR molecules and enhancing the molecular entanglement. In this way, he developed eco-friendly traveling cables that are as flexible as conventional traveling cables and easy to handle.
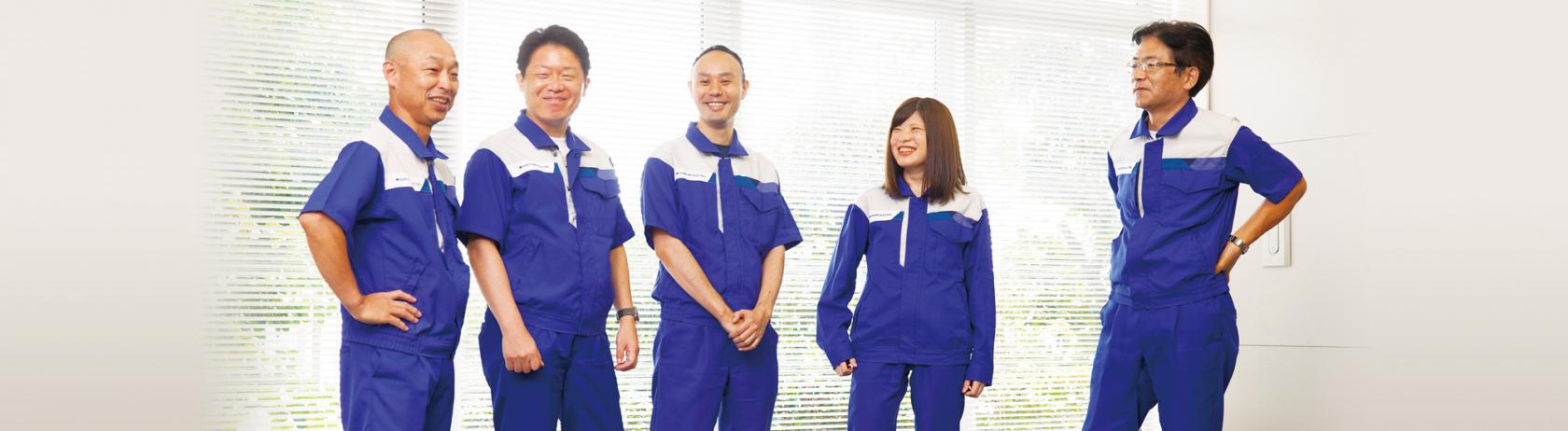
NEXT
Develop Flexible, Strong and Stress-Free Electric Wires & Cables Story behind the development of S-FREE™②
(3)