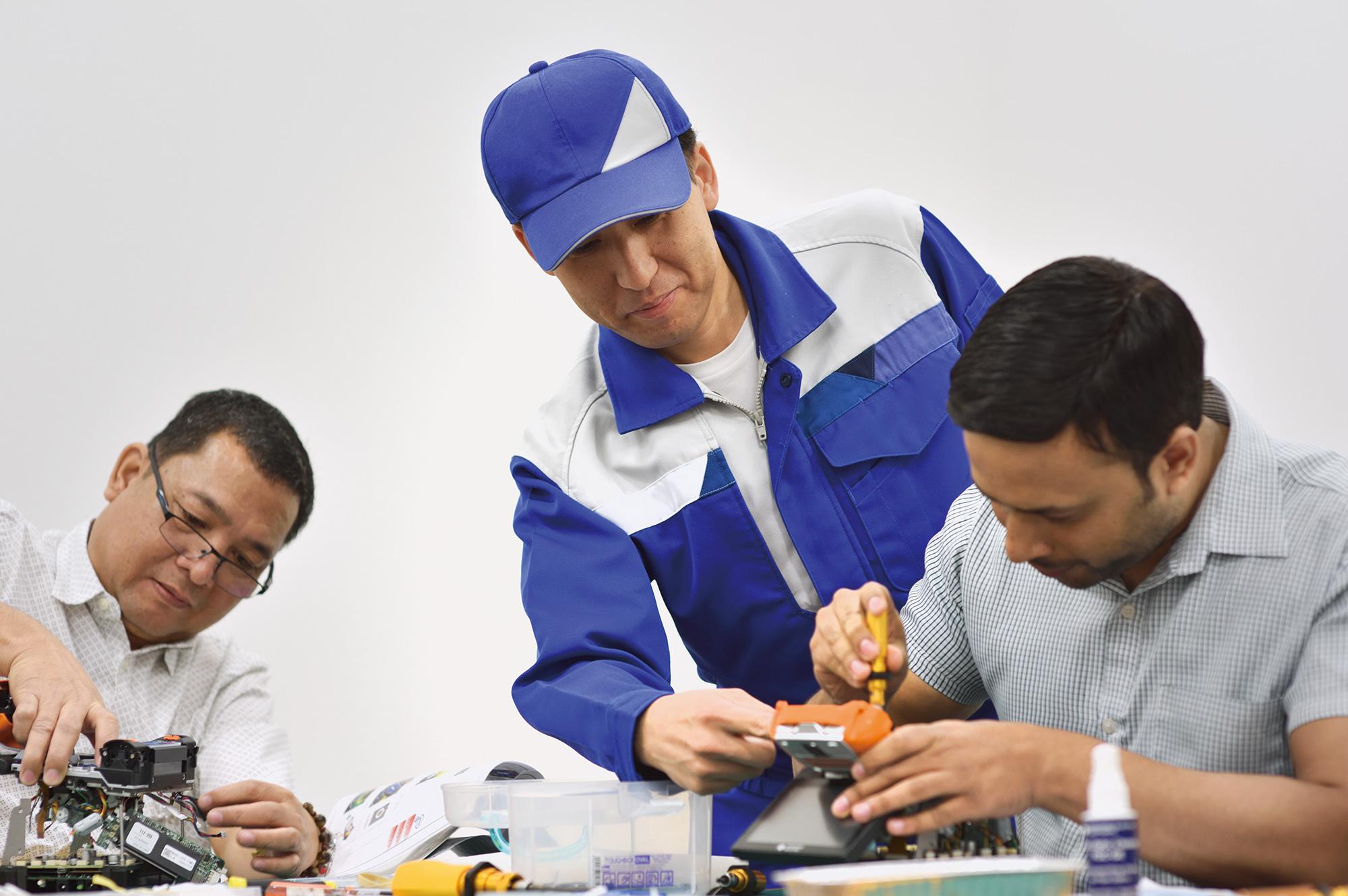
Production Frameworks and Flawless After-sales Follow-ups
Developing human resources to meet user expectations
Production frameworks established to precisely respond to market needs
The Shonan Works of Sumitomo Electric Optifrontier Co., Ltd. is a fusion splicer production base located in Chigasaki, Kanagawa Prefecture. Its flagship fusion splicer models consist of the TYPE-72C+ family, which is used to connect the long-distance and large-capacity trunk lines mentioned earlier; the TYPE-72M family used for multicore mass splicing at, among others, data centers in North America; and the TYPE-201 family, which features the world’s smallest and lightest units that are efficient in limited work spaces when installing fibers on customer premises or between utility poles. In addition to these products, the works produces optical fiber cutters that come with the Sumitomo Electric Group’s proprietary self-rotating blade mechanism and light and compact jacket removers used to remove the jacket for fusion splicing. These products are highly regarded around the world. The production base is overseen and managed by Kensuke Ito, Works General Manager. Ito points out that fusion splicers are exceptionally high-precision products.
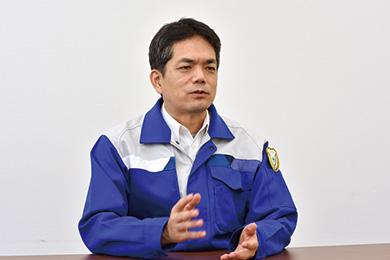
“Optical fibers are spliced in order of submicrons. This means that fusion splicers are produced with high precision. That level of precision can only be accomplished with human hands. Of course, automation has been positively incorporated, but the final intricate adjustments require an expert’s skills. For this reason, the challenges that the works addresses include training of personnel to inherit expert skills. Another important thing is that market needs are shifting quickly and are becoming more diverse.
Changes in supply and demand are also significant. Meanwhile, competition is becoming fierce due notably to emerging Chinese manufacturers. We plan to shift from the make-to-stock style to the make-to-order style. Additionally, we intend to build a novel production framework that can swiftly coincide with market demands and benefit from cost advantages,” says Ito.
Training maintenance personnel from different countries
Fusion splicers are high-precision products and, as such, it is extremely important to ensure proper maintenance for them. This involves after-sales follow-up in addition to developing and manufacturing the product. The point is to quickly respond to defects or malfunctions when they occur. The Sumitomo Electric Group has established nine service centers around the world (the United States, the United Kingdom, China, India, the Philippines, Thailand, Singapore, Brazil and Dubai) for providing prompt maintenance services and has built a framework for training maintenance staff. The staff members then provide instructions to the affiliated agents. Hiroshi Sadaki of the Production Engineering Group of Sumitomo Electric Optifrontier Co., Ltd. has long been in charge of the above-mentioned maintenance enhancement efforts.
“In the training sessions, trainees disassemble failed products, replace or adjust parts, and inspect the products to gain maintenance know-how based on a maintenance manual. Coinciding often with the launch of a new model, one person from a sales company participates in a thorough three-day program. They return to their home countries after receiving a certificate of achievement by passing a three-stage skill test. They transfer the skills that they have acquired in Japan to their respective home countries. In maintenance, it is important to swiftly determine which part is abnormal and identify the cause of the failure. Acquisition of the required expertise paves the way to developing human resources capable of swiftly providing on-site support to detected failures,” says Sadaki.
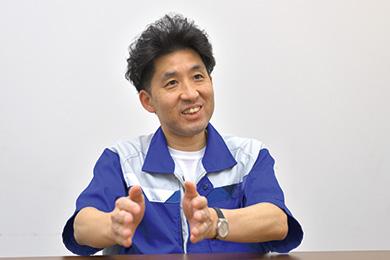
“In the training sessions, trainees disassemble failed products, replace or adjust parts, and inspect the products to gain maintenance know-how based on a maintenance manual. Coinciding often with the launch of a new model, one person from a sales company participates in a thorough three-day program. They return to their home countries after receiving a certificate of achievement by passing a three-stage skill test. They transfer the skills that they have acquired in Japan to their respective home countries. In maintenance, it is important to swiftly determine which part is abnormal and identify the cause of the failure. Acquisition of the required expertise paves the way to developing human resources capable of swiftly providing on-site support to detected failures,” says Sadaki.
A sense of fulfillment in contributing to sales expansion
One of the participants in the training was Tang Chen, manager of the fusion splicer maintenance center at Sumiden Asia (Shenzhen) Co. Ltd., which also serves as a sales company in China. Tang offers guidance on maintenance to agents and repair shops across China.
Tang says, “I have participated in the training more than 10 times. The sessions are always very easy to understand. The logical explanation of the cause and effect relationship in failures helps deepen one’s understanding. At first, mainly inexpensive products were sold in China. Recently, there has been a growing need for higher-value-added and higher-quality products due to the increase in data centers. I place high expectations on SumiCloud fusion splicers. Since on-site data can now be accumulated on fusion splicing, connecting this data with the system helps increase the accuracy of defect analysis and achieves more sophisticated solutions.”
Yakeen Patel participated in the training from Europe. He is the manager of the UK Office service center of Sumitomo Electric Europe Limited. SEEL covers many regions: the whole of Europe, Russia, Africa, and the Middle East.
Patel says, “We have about 70 affiliated sales agents. I am in charge of offering guidance on maintenance to agents. Every time I receive training in Japan, I am impressed by the sophisticated training programs from a professional viewpoint. It is sometimes difficult to fully understand the maintenance manual, but the practical training helps me in the acquisition of skills. Sales of fusion splicers have been growing steadily in the markets in which SEEL operates. I am confident that our maintenance service has contributed to the sales increase. There are two issues. First, SEEL operates in many non-English-speaking regions, so we want to make the maintenance manual easier to understand by translating it into other languages and using many illustrations. Second, the number of repaired units has been increasing in line with the sales growth, so we would like to increase the number of repair personnel.”
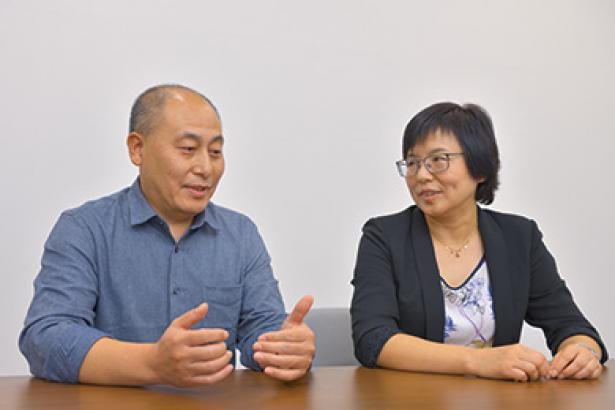
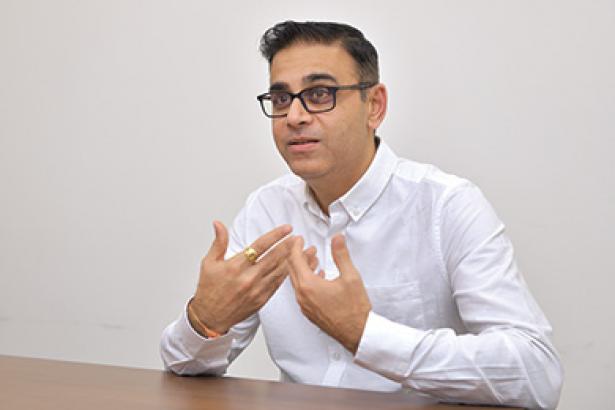
COLUMN
Support for Winning a Gold Medal at the 45th WorldSkills Competition
The WorldSkills Competition is held every two years with the aim of promoting vocational training in participant countries and international exchange and friendships between young professionals. The Sumitomo Electric Group has provided fusion splicers critical for network cabling for the past four consecutive competitions. At the 45th WorldSkills Competition held in 2019 in Kazan, Russia, the integrated facility engineering company Kinden Corporation representing Japan won the gold medal in excellent fashion in the Information Network Cabling trade. The gold medalist, Mr. Yuta Shimizu of Kinden, told us the following:
“During the competition I encountered a series of difficult situations, placing me in a state of constant tension. However, I tackled the task until the end without giving up. When I realized I was the gold medal winner, I was filled with too much joy for words and had a sense of exhilaration. The Sumitomo Electric Group’s T-400S fusion splicer and the FC-8R optical fiber cutter were so easy to use that I could demonstrate high performance during the competition. I am so grateful to those who gave me guidance, the companies that kindly supported me, and the people from the organizations involved.”
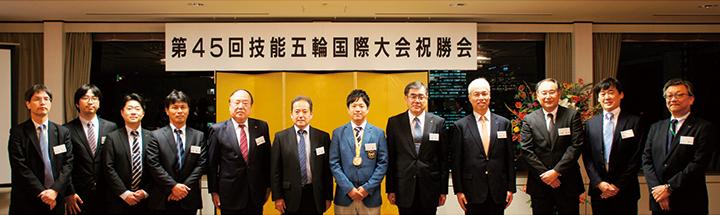

NEXT
MADE IN JAPAN Fusion Splicers Supplied throughout the World
Product innovations, solutions, and global sales and maintenance networks