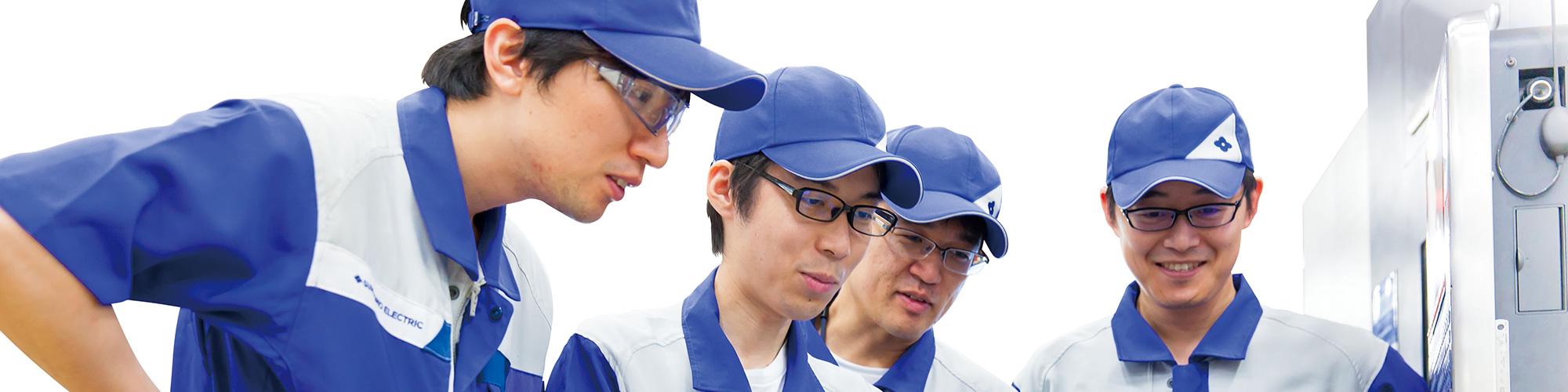
Next-Generation Manufacturing and the Multidrill
Toward the Age of Industry 4.0
4th Industrial Revolution originating in Germany
Since its launch to markets in Japan and abroad for about 35 years, the Multidrill has evolved in various ways and played a critical role in innovating the manufacturing site in terms of productivity improvement and cost reduction. Currently, the world is entering a new evolutionary phase of manufacturing. The 18th century saw mechanization enabled by steam power. Mass production began in the early 20th century through the use of electric power. In the 1970s, automation advanced thanks to the use of computers. What is considered to be as influential in scale as these milestones is “Industry 4.0,” an approach leading to the Fourth Industrial Revolution in the history of humanity. The concept is described as a “smart factory” and aims to minimize cost by radically boosting the digitization, automation, and virtualization of production processes. To realize this, IoT is considered to be an effective tool. This tool connects machinery and other equipment used at manufacturing sites via the Internet for the sending and receiving of data to optimize production, supply, and other elements of manufacturing performance. Originating in Germany, these government-led industry-academia-government initiatives have spread to other advanced countries. As an essential element for next-generation manufacturing, IoT is researched and discussed in various sectors in Japan as well.
Smart tools that give out a cry through sensing and big data
The Sumitomo Electric Group is taking various approaches which are led by the Advanced Materials Laboratory and the IoT R&D Center. The Laboratory creates new materials in the areas of metallic and inorganic materials and process innovation based on the Company’s proprietary ultra-high pressure and powder metallurgical technologies. Not only promoting material research but the Company is also working on processing technologies by collaborating with the IoT R&D Center to develop the “smart tool.”
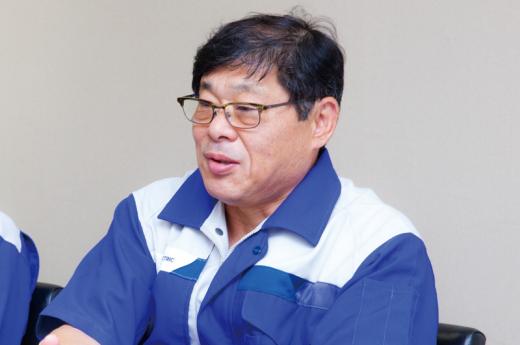
“The tool life of the Multidrill varies depending on its usage and the operating environment. At the end of its tool life, the Multidrill declines in drilling precision and is at high risk of drill breakage as its wear progresses. If a drill breaks during machining, various problems occur. The broken drill pieces are difficult to remove from the hole, the workpiece may be damaged and the following process is delayed. Users wish to use tools to the very end of their tool life, however, it is not possible to predict the end of a drill’s tool life because it depends on the usage and the operating environment. Consequently, it has become a common practice to replace the tool in service with a brand new tool at a safety margin, for example, with around 20% remaining life. As a solution to this challenge, we aim to develop a smart tool that “gives out a cry” to tell the user the end of its life. With this feature, the user can use the tool safely to the fullest extent,” explains Mitsuhiro Goto, General Manager, Advanced Materials Laboratory.
To meet this challenge, IoT is absolutely necessary. The concept is to monitor the conditions of the cutting tool by using sensors that detect abnormal force, temperature, and vibration during machining and to predict the end of the tool’s life by collecting these data via a wireless network and storing and analyzing them as big data. This concept when realized is expected to substantially reduce the machining and production cost and improve the yield. Daisuke Murakami, Chief Engineer at the Hard Material Research Department points out that, due to their nature, drills have many more difficulties to overcome than other tools.
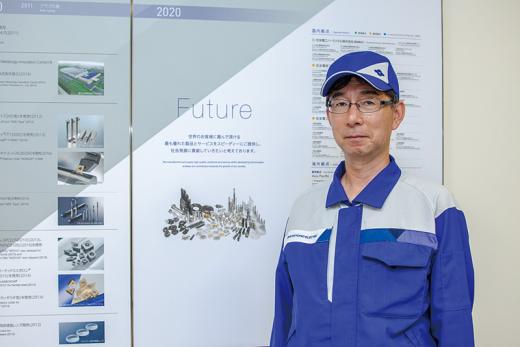
“A drill works at the bottom of a hole. How it is working is not visible from the outside. What is happening there? We are currently working on making it visible. In short, the goal is to visualize it, making full use of sensing and image processing technologies. Visualizing how a drill is working makes it possible to predict the end of its tool life. This in turn reduces waste in production in a smart way,” says Murakami.
In more than a few cases, the tool life of a Multidrill has been estimated relying on the senses and intuition of the user. While the high reliability of this kind of estimation is widely known, smart tools digitalize and automatize the estimation process for further productivity improvement, fulfilling demand in the age of Industry 4.0.
“Drilling is an indispensable part of all kinds of manufacturing. It enables parts to be fitted into an object. Starting with its use in steel machining, the Multidrill has been adapted to diverse materials. Drilling will remain in need in various manufacturing scenes. I hope that the Multidrill will continue to be effective, essential and the first to be selected. The Sumitomo Electric Group aims to be one of the world’s top three players in the cutting tool industry within five years. I believe the Multidrill will play the role of a strong engine to make it true,” says Atsushi Murayama, General Manager, Hardmetal Div.
There is no doubt that Sumitomo Electric’s Multidrill will continue to evolve in the future, help innovate production sites in every part of the world and play a role in paving the way for next-generation manufacturing.
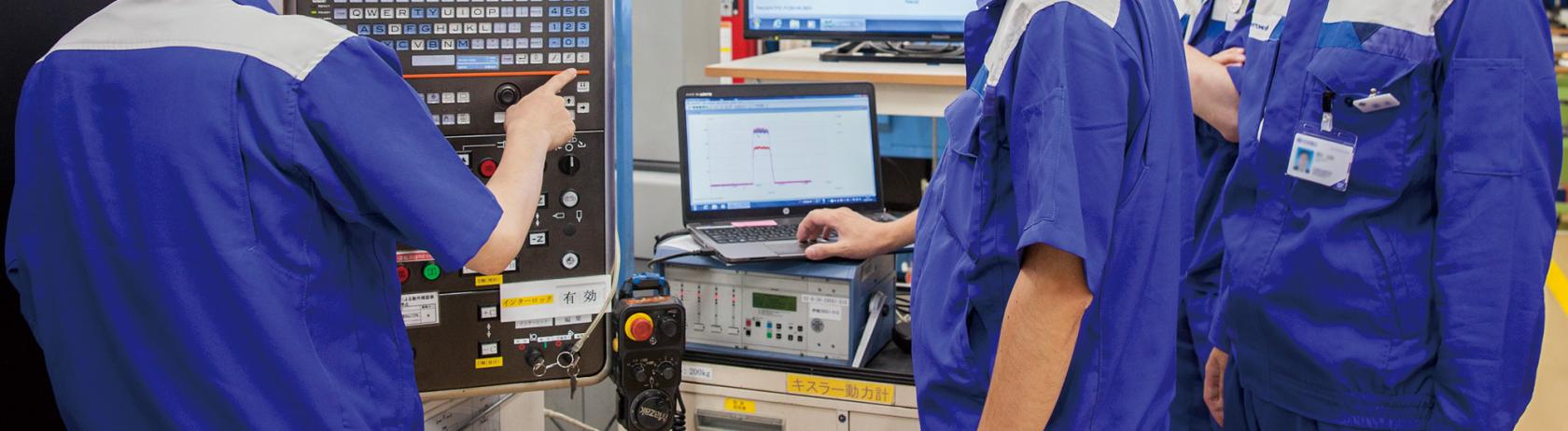