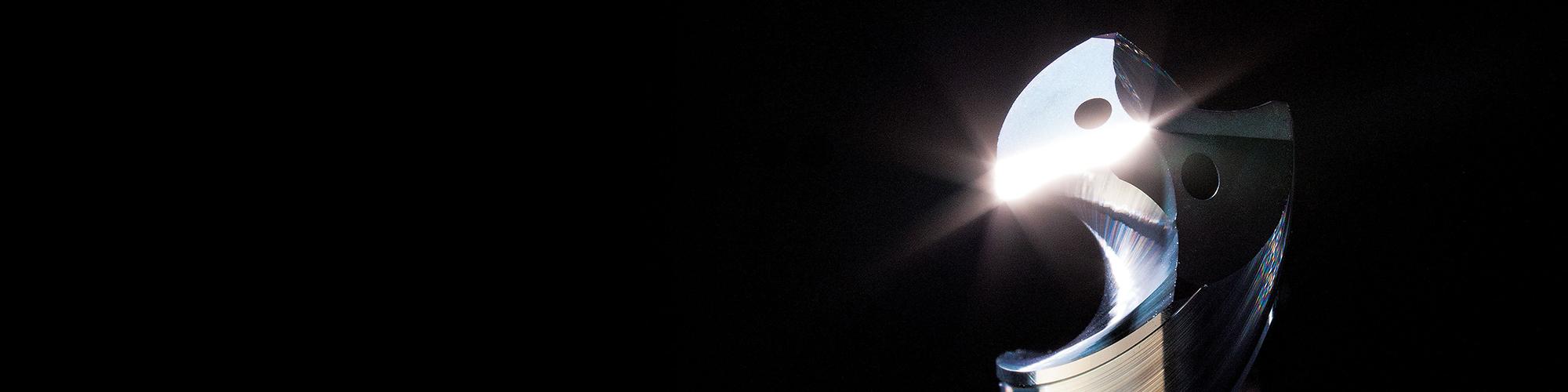
Evolution of the Multidrill
Multidrill Entering Chapter 2
Collateral Development of Cemented Carbide and Coating
The development of the drill design progressed concurrently with the development of a new cemented carbide substrate and coating. Cemented carbide is very hard and is therefore, at the same time, poor in flexibility and brittle. More specifically, the Multidrill was subjected to chipping on the cutting edges and breakage of the body depending on the operating settings. To overcome these challenges, the ideal composition of tungsten carbide and cobalt has been studied. Moreover, titanium carbide and other additives have been researched to develop cemented carbide for drills and evolve them to be more resistant to breakage.
The development of coating technology was promoted with the aim of additionally extending the tool life of the Multidrill. In short, this coating is intended to form a thin ceramic film on the surface of the drill for high durability. One key point was the material composition of the thin ceramic film. Cutting tools including drills are constantly required to improve in wear resistance and heat resistance. The coating applied to the first Multidrill was made from titanium carbonitride developed by optimizing the composition of titanium carbide and titanium nitride. In the 1990s, Sumitomo Electric developed ZX Coating, applying the world’s first multilayer nanotechnology and improved the performance of its cemented carbide drills drastically. Subsequently, the coatings evolved steadily.
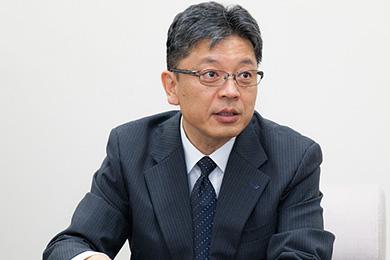
“Coatings are evolving still today through the supplementation of new ingredients such as chromium and silicon to the multilayer nanotechnology that produced ZX Coating. We will continue to work on coating development following specific product conception, concurrently with the deployment of the Multidrill in diverse applications.” (Makoto Setoyama, Hard Materials Development Dep., Sumitomo Electric Hardmetal Corp.)
The bold challenge in collaborating the trinity of design, cemented carbide substrate and coating spurred the evolution of the Multidrill.
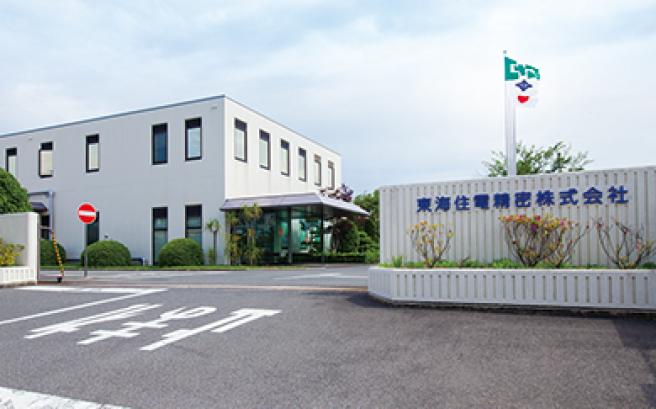
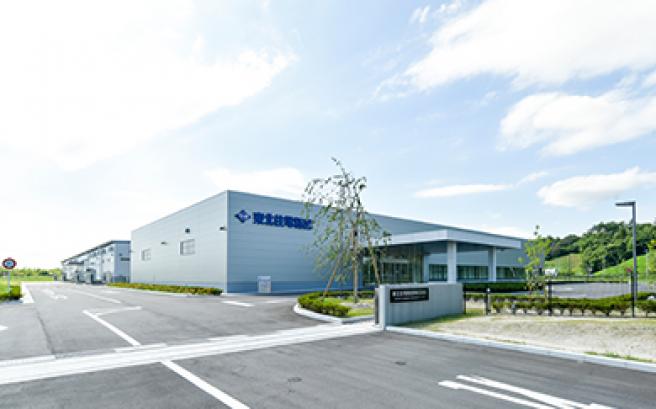
Responding to Diversified and Sophisticated User Needs
While the Multidrill evolved steadily in line with the needs of the market and the times, the first breakthrough was the Multidrill with coolant holes created in the 1990s. This Multidrill had holes running through its body to allow cutting fluid (water or oil) to pass through. One important point of the Multidrill was the achievement of smooth evacuation of chips. Holes at the tip of the drill allow cutting fluid to spray out, further improving the chip evacuation capability of the Multidrill and enabling the drilling of deeper holes to a depth of 5 to 10 times the hole diameter with higher machining efficiency. This evolution helped expand the applications of the Multidrill at a stroke. The next evolutionary milestone was the deep hole drill, which emerged in 2000. As its name suggests, this model of the Multidrill produced very deep holes 20 to 30 times the hole diameter, which had been believed impossible. These evolutions were the results of efforts in responding precisely to the diversified needs of the user.
In the course of these responses, various initiatives were promoted. For example, there was a response to weight reduction accompanying demand for reduction in fuel consumption in a car. One symbolic way of reducing the weight of an automobile was to replace steel with aluminum. In line with this trend, although the Multidrill was developed as a tool for steel machining, they developed another version of the Multidrill tailored for aluminum drilling to further improve machining efficiency. To meet the demand for part size reduction as a way of reducing the weight, they endeavored to reduce their drill bit diameters to a minimum of 0.03 mm. Furthermore, the Sumitomo Electric Group has responded to diversifying drilling needs precisely and promptly, including the challenge of machining titanium and other hard-to-cut materials used in aircraft parts.
To Tap New Markets Taking Advantage of Sumitomo Electric’s Seamless Production System
After the expiration of the design patent, competitors followed suit. However, the Multidrill’s market supremacy reputation in Japan and abroad has been outstanding to date. This is backed by the fact that Sumitomo Electric is the pioneer in cemented carbide drills and has a fully equipped integrated production system.
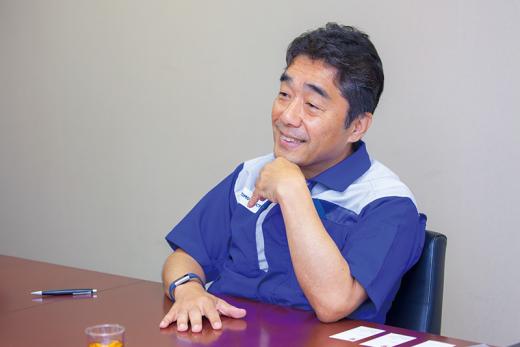
“The manufacturing of the Multidrill is completed within the Sumitomo Electric Group, from the production of raw material powders to machining and coating. This is the strongest engine that produces high quality and high performance. We also strive actively to achieve recycling. One raw material of the Multidrill is tungsten. Tungsten mines are located predominantly in China. Aiming to stabilize the supply of tungsten, we are accelerating our efforts to realize recyclable manufacturing,” says Atsushi Murayama, General Manager, Hardmetal Div., Sumitomo Electric Industries, Ltd.
The seamless manufacturing framework built within the Group has enabled us to take a flexible product development strategy. Moreover, a breakthrough initiative has begun in the history of the Multidrill.
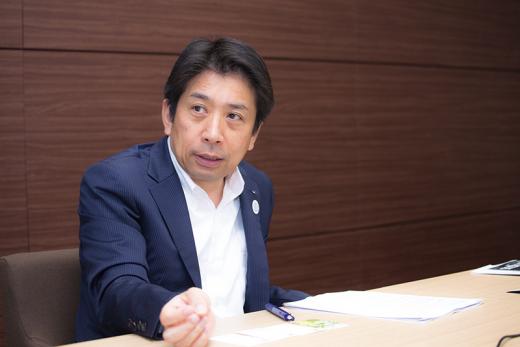
“For the Multidrill, we strive to differentiate ourselves from our competitors by aiming at higher efficiency, higher precision and greater depth. This is an unending pursuit. We will continue to aim to further high performance. At the same time, we have worked on the development of new products to acquire more Multidrill users and to place the Multidrill in new markets. From a long-term perspective, I think the Multidrill has completed Chapter 1 and is entering Chapter 2,” says Toshiyuki Sahashi, Executive Officer, Sumitomo Electric Industries, Ltd. and President, Sumitomo Electric Hardmetal Corp.
The challenge of developing new products was assigned to Masaaki Jindai, who had been almost continuously involved in the Multidrill at the Tool Designing Department at Sumitomo Electric Hardmetal Corp. since he joined the company.
Development of a new Multidrill in pursuit of goals ranging from high efficiency to high versatility
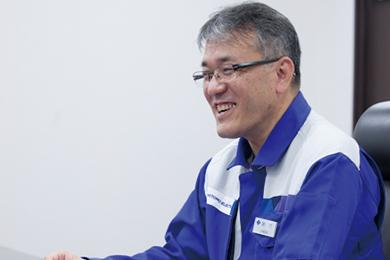
High-efficiency-oriented Multidrill has conventionally been used by mass-production manufacturers including automakers. New Multidrill products boldly departed from this way of thinking and targeted flexible machining manufacturers conducting machining primarily using high-speed steel drills.
“Flexible machining manufacturers constituted an extensive market. It was necessary to offer products adapted for selection by them. Therefore, we aimed to develop general-purpose drills to cover a wide range of applications. The key point was to extend their life in low-speed machining, even if their efficiency was compromised. It was a major challenge that required me to draw on all of my experience as an engineer involved in the Multidrill,” recalls Jindai.
Before working on the new product, Jindai had a successful experience in developing a Multidrill adapted to Chinese users’ needs and launching it onto the Chinese market. He used the knowledge that he had acquired through this experience, such as the optimization of cutting edge treatment, in order to develop the new product.
Thus the new Multidrill was created and its production began at Tohoku Sumiden Precision Co., Ltd., which was newly established in Fukushima Prefecture in 2017. Tohoku Sumiden has an IoT-based factory incorporating unprecedented methods of automation, quality control and data management. This was an attempt to tap into a new market for the highly versatile Multidrill. Presently, it is steadily growing in the new market.
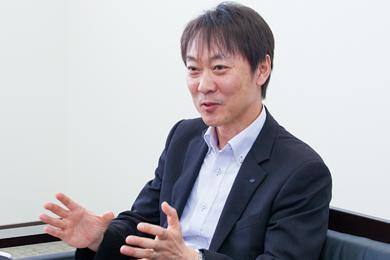
“High efficiency and high versatility. When these models of the Multidrill provided by the Sumitomo Electric Group replace the drills currently used in the manufacturing industry, the field of production will undergo further innovation. Envisioning the Multidrill’s evolution into smart tools in the near future enabled by IoT in the field of production, I wish to endeavor to provide dependable solutions in the realm of drilling.” (Makoto Abe, Deputy General Manager, Tool Designing Dep., Sumitomo Electric Hardmetal Corp.)
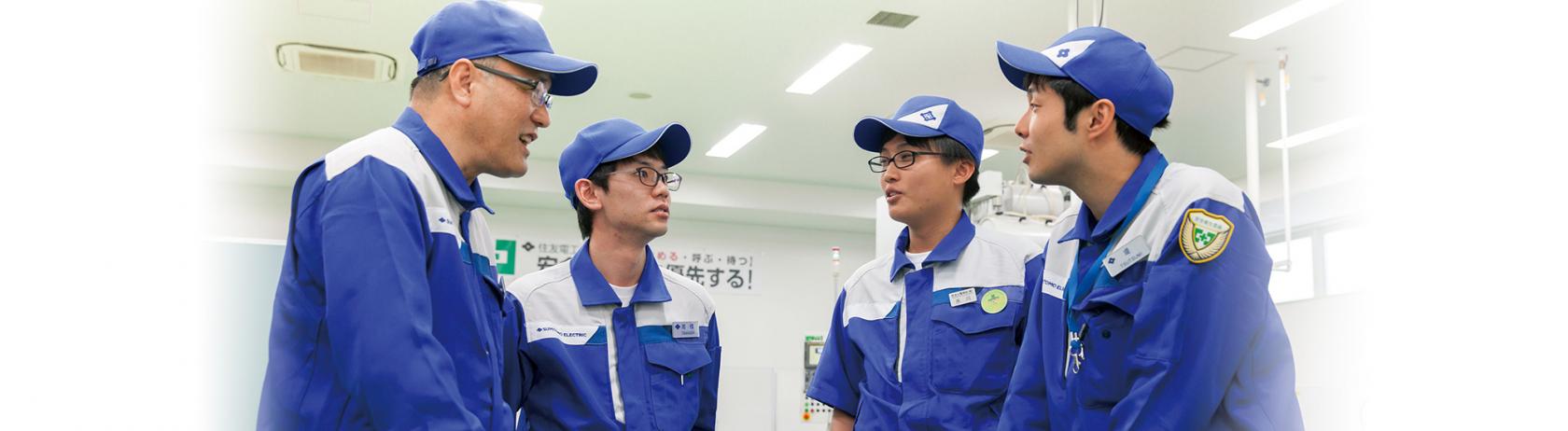
From left
Masaaki Jindai
Assistant Manager, Round Tools Development Group, Tool Designing Dept., Sumitomo Electric Hardmetal Corp.
Koji Takahashi
Round Tools Development Group, Tool Designing Dept., Sumitomo Electric Hardmetal Corp.
“I am in charge of the development of replaceable head drills. My current challenge is to create cutting edges with high durability. The present goal is to launch the drill that I am involved in into the market.”
Ryo Hikawa
Design & Engineering Section, Engineering Div., Tokai Sumiden Precision Co., Ltd.
“I am working as a troubleshooter to solve problems at our users. I would like to help our customers improve their machining efficiency by proposing optimal machining ideas according to their working environments and needs.”
Yuki Tsutsumi
Round Tools Development Group, Tool Designing Dept., Sumitomo Electric Hardmetal Corp.
“I am working on the development of new products. My current task is to improve the design of the Multidrill for even more accurate machining. I am geared to developing products that will demonstrate a significant presence in the world.”