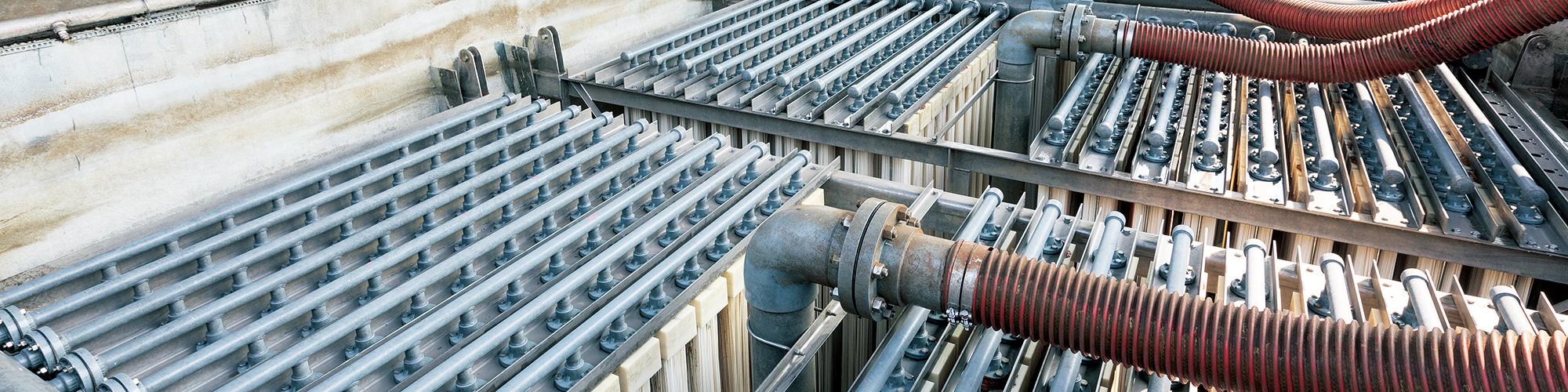
Purify Wastewater from a Large-scale Oil Refinery in a Water Shortage Area
CPC Corporation Wastewater Purification Project in Taiwan
Started our activities to use high-performance porous materials for water treatment
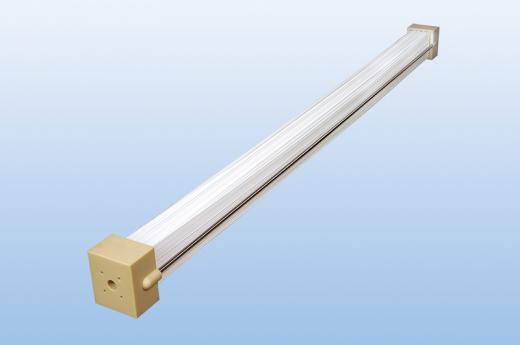
The Sumitomo Electric Group developed epoch-making water treatment membrane modules. Before explaining about the modules, it is necessary to refer to the details of water treatment. There are several water treatment methods. Among them, the so-called membrane bioreactor (MBR) method has been attracting considerable attention in recent years. This is one of the “active sludge methods,” which are considered effective for sewage and industrial wastewater treatment. In this treatment, wastewater is degraded and treated by microorganisms (active sludge), and then organic matter and fine particles are separated from the water using filtration membranes (hereinafter referred to as “membranes”).
Not only turbidity but also dissolved organic matter can be removed, allowing the discharge of the water to rivers, which is regulated by strict standards, as well as the reuse of the water. The membranes used for this MBR are POREFLON™ hollow fiber membranes. These membranes have a material separation function because they are made of tubes of about 2 mm in outer diameter with a microscopic porous structure. POREFLON™ is a porous material developed by Sumitomo Electric and made of 100% polytetrafluoroethylene (PTFE) resin. With attention focused on the various excellent characteristics of POREFLON™ developed in the 1960s, such as high chemical resistance, high durability, high water permeability, and high heat resistance, hollow fiber membranes suitable for water treatment were developed. Toru Morita, General Manager of the Water Processing Div. successfully put the membranes into commercial use. “Conventionally, materials such as polyethylene (PE) were used for hollow fiber membranes but problems with durability and chemical resistance were pointed out. We focused our attention on POREFLON™ that uses PTFE to solve these problems. We were convinced that competitiveness would be adequately enhanced by promoting price reduction through refining product design and manufacturing technology and started our activities to commercialize POREFLON™ modules for water treatment use.”
Started a big project under tough business circumstances
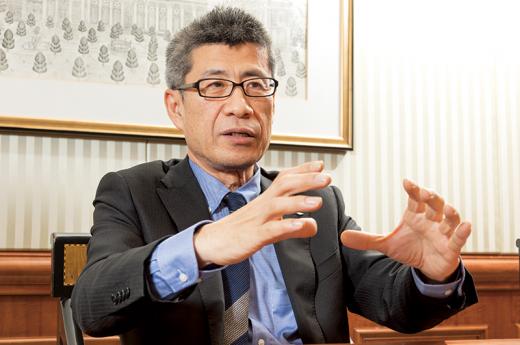
The development of POREFLON™ modules was started as stated above and successfully completed in 2003 following the production of a number of prototypes and mass-production was started in China in 2004. However, this was the beginning of facing severe difficulties. Soon after the start of the production, significantly negative reactions to POREFLON™ modules were received from markets both domestic and abroad. The key complaint was the extremely high price of the PTFE material. It was when withdrawal from the market was considered that Morita met an agent handling industrial materials in Korea and obtained information on the water treatment market in Korea.
Morita and other members, who recognized the potential of the high water treatment performance of POREFLON™ modules, cooperated with the agent that was enthusiastic about sales of the modules and promoted sales activities in Korea and finally introduced the modules to a sewage treatment plant. However, the sales of the modules were down again due to the change in the market environment. In order to break through such a situation, Morita and his team focused on the needs for water treatment in East Asia as well as in Japan and steadily continued proposal activities of POREFLON™ modules. Consequently, a big project was triggered by a certain meeting. Generally speaking, an engineering company contracted for the construction of water treatment facilities has the right to decide on the introduction of membranes to the facilities. Therefore, an approach to such a company is a key to promote the sales of POREFLON™ modules. In 2008, Morita’s team displayed POREFLON™ modules at a water treatment exhibition held in Guangzhou, China. There, they met CTCI Corporation, one of the most prominent engineering companies in Taiwan.
Built a strong relationship of trust with the engineering company
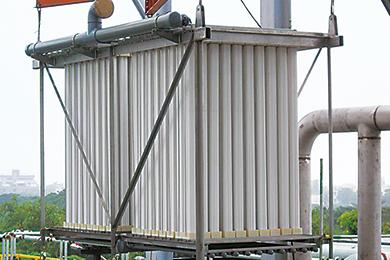
In Taiwan, even though POREFLON™ modules were being gradually adopted mainly for the use in water treatment facilities of the factories of electronic products, membranes provided by major US companies were dominant in the water treatment market in Taiwan and we were not really in a favorable situation. Morita was trying to participate in a project that could make an impact on the market and show our presence. Meanwhile, CTCI had experience of constructing a plant for CPC Corporation, Taiwan, a major oil refinery company in the country, and was conducting a study on membranes to be adopted for the water treatment facilities newly introduced by CPC at that time.
In addition, since the southern part of Taiwan, where CPC is located, was suffering a chronic water shortage, the public administration regulated water discharge and made it compulsory particularly for companies that discharge a large amount of industrial wastewater to reuse the water. Under such circumstances, POREFLON™ caught the attention of the staff of CTCI in the exhibition. At that point of time, CTCI had already started design on condition that it would use competitor’s membranes. However, Jeff Zhang of the Taiwan branch of Sumitomo Electric Interconnect Products (Hong Kong), Ltd. strongly approached CTCI to reconsider the decision.
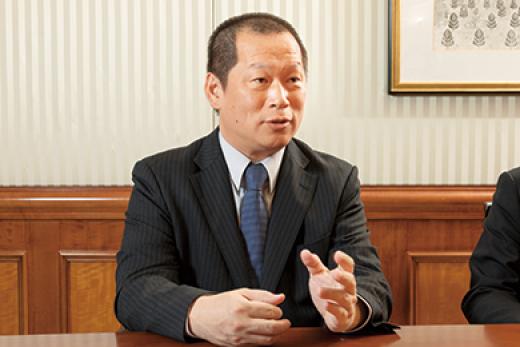
“I strongly stressed the advantages of POREFLON™. The CTCI staff highly evaluated the characteristics that show strength in treating wastewater containing oil and mineralized wastewater. We also focused on building a strong relationship of trust with the relevant staff. These efforts made it possible to start a pilot test.”
Started a pilot test Initiatives to solve the problem
A pilot test was started in 2009. However, a problem arose. A hollow fiber membrane has a number of fine pores to enable fine filtration, but clogging occurred due to the oil contained in the wastewater and consequently the purification performance decreased. The pilot test faced a difficulty. To solve the problem, two different approaches were taken. First, a thorough study was conducted on the fine structure of the membrane unlikely to cause clogging and the mechanism causing oil clogging was investigated to optimize the pore diameter for stable operation. Then the membranes were cleaned using strong chemicals to remove matter adhering to the surface. The cleaning was carried out using high-concentration acids and alkalis, which was possible only for POREFLON™ because of its high chemical resistance. Jeff, who was in charge of sales, also engaged in cleaning membranes at the site and recognized anew the high performance of the product of his own company. “We did what we had to do and obtained results. I believe that the repetition of this cycle impressed CTCI.” The pilot test lasted for about one year, and CTCI valued the good results in cleaning performance obtained in the treatment of oil-contaminated wastewater and durability and flow rate restoration after the cleaning of membranes with acids and alkalis, and finally decided to adopt POREFLON™ modules.
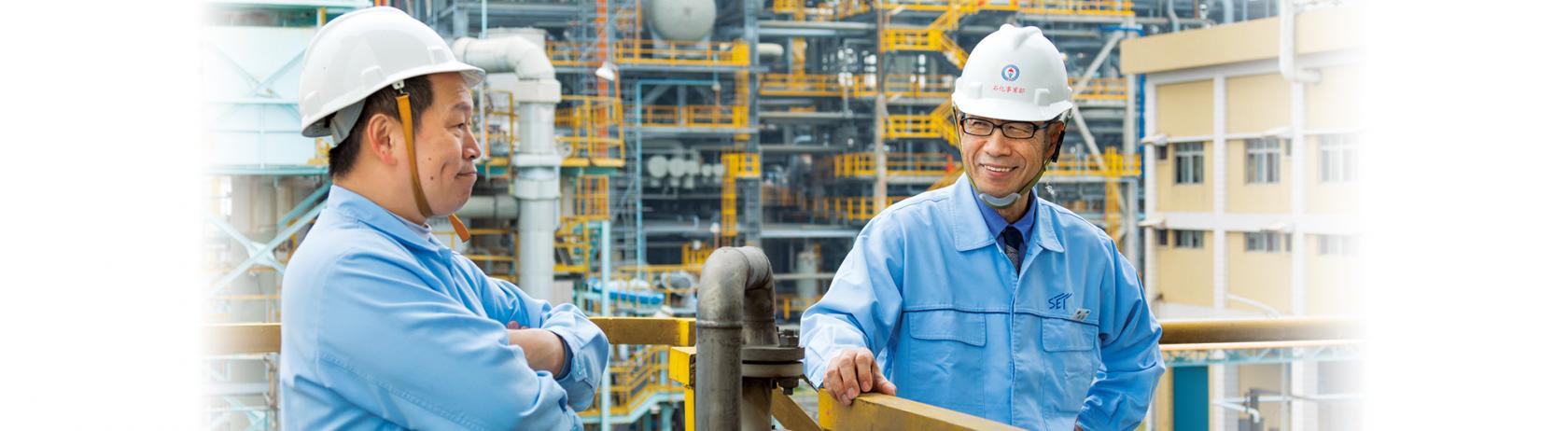