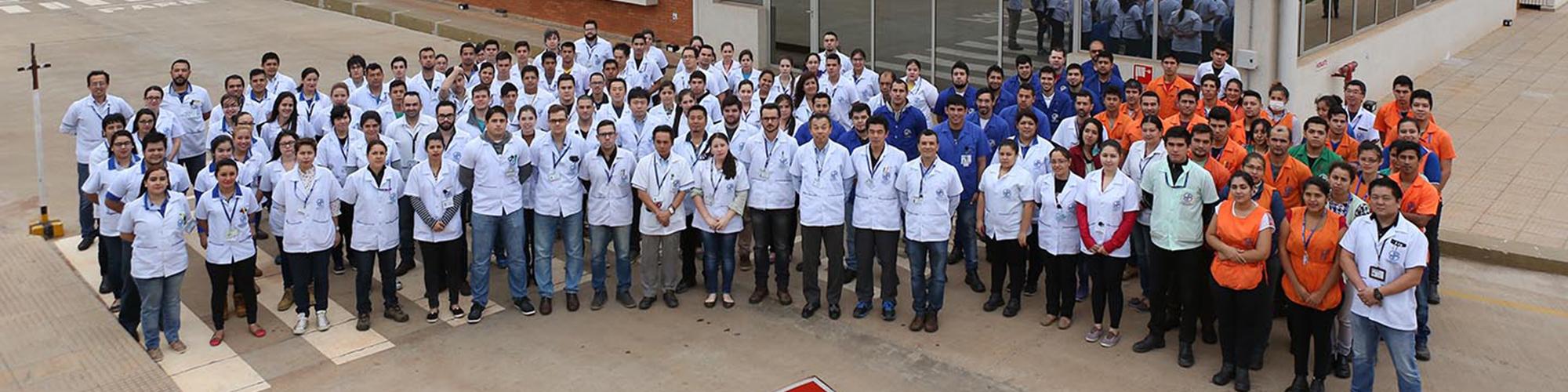
Manufacturing Relying on Human Resources
Approximately 250,000 employees in about 30 countries around the world
Here, we introduce the production system of aluminum and other types of wiring harnesses that serve as Sumitomo Electric Group’s bread-and-butter products. (The company in charge of production is Sumitomo Wiring Systems, one of the Group companies.) The Group’s technological prowess is not the only reason for the high reliability of the Group’s wiring harnesses in the global market. The reliability could not have been attained without the establishment of a manufacturing system in which quality products are handmade in a steady, consistent manner.
In addition, this article covers the present state of the newest location for the production of wiring harnesses in Paraguay (South America), or Sumidenso Paraguay S.R.L. (SDP).
Global motto: Pika Pika Activity
The most distinctive feature of wiring harnesses in terms of manufacturing is the fact that they are mostly-handmade, labor-intensive products. At worksites, “human resources” play a central role in manufacturing. Therefore, people are the main determinant of product quality. It is no exaggeration to state that product quality hinges upon individual employee’s skills. The Group has its production sites in about 30 countries around the world and approximately 250,000 employees in total. Under this production system, the Group is always aiming to achieve globally common best quality.
“Our basic corporate mission is to deliver products of the same high quality from every production site around the world. What underlies this idea is the philosophy that ‘manufacturing relies on human resource development,’ which serves as a driving force in the creation of a globally common best quality” (Akihiro Komori, Manager, Global PIKAPIKA Center, Wiring Harness Operations Planning Group, Sumitomo Wiring Systems). The philosophy is embodied in the Pika Pika Activity unique to Sumitomo Wiring Systems. This project has been well established as an activity to achieve “pika pika (brilliant) manufacturing” through “pika pika mind, actions, and skills” and “pika pika equipment and worksites.” The term “Pika Pika Activity” now serves as a motto of the company’s employees around the world.
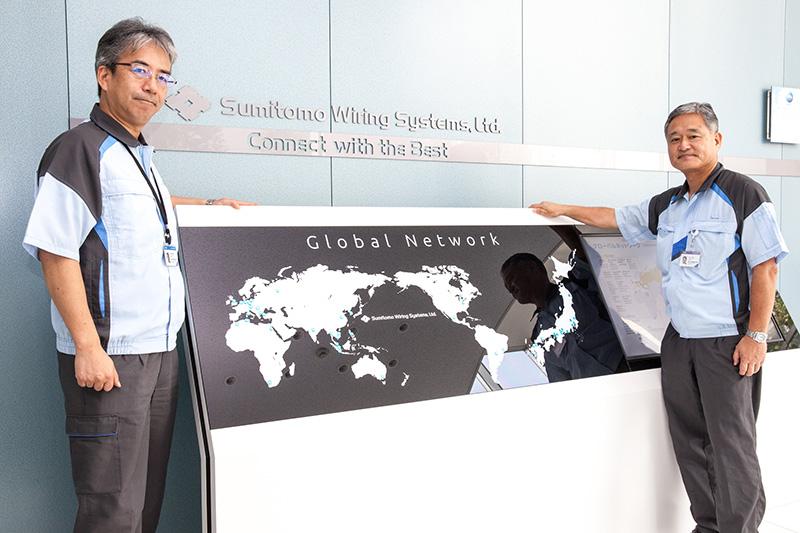
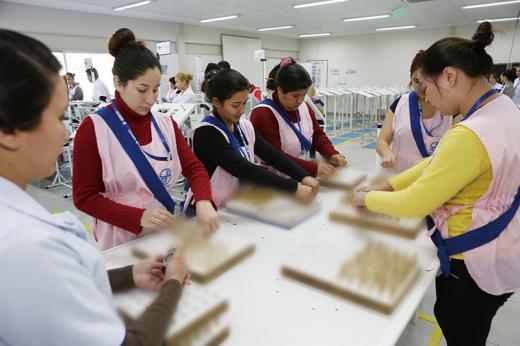
The first step of the Pika Pika Activity is to measure and evaluate skills using the Global Skill Training and Recognition System (G-STARS). Skills are rated on a scale of 1 to 5 so as to motivate workers and improve their skills in terms of, for example, working speed and quality control. Another program of the Pika Pika Activity is the PK Evaluation to evaluate factory management levels. In recent years, judging from the fact that more than 90% of all factories score 80 or higher out of 100, high pika pika levels have been achieved on the whole. In addition, the Skill Olympic Games, in which employees around the world strive to participate, is held. Delegates from each country annually gather together in Japan to compete against each other to win first place in the skills required for each work process. “Although these programs are designed to evaluate skills, they all function as part of education, in other words, human resource development, providing the power to create a globally common best quality” (Tetsuji Maruyama, Executive Officer, Sumitomo Wiring Systems).
Struggle to achieve a globally common best quality
Located near the center of South America, Paraguay is one of the farthest countries in the world from Japan. Among Latin American countries, Paraguay has recently become a focus of attention. One of the reasons for its popularity is the country’s economic policy, which provides tax exemptions for importing components and exporting products. In this country, the Sumitomo Electric Group launched the production of wiring harnesses in 2016. “Paraguay adopts a forward-looking attitude to attracting foreign businesses so that it can achieve resultant job creation and further economic growth. Meanwhile, having a high ratio of young people, the country provides businesses with the advantage of access to a large, young workforce. This attractiveness of Paraguay made the Group consider the country an optimally suited location for increased productivity and decide to establish a production site there” (Masayoshi Morii, President, SDP). SDP was established as an affiliate of Sumidenso do Brasil Indύstrias Elétricas Ltda. located in Brazil, by relocating part of the production lines from Brazil. The ceremony to celebrate the opening of SDP was attended by the President of Paraguay, major ministers, and the Japanese ambassador. The Minister of Industry and Commerce visited SDP three times in total before and after the ceremony. This indicates high expectations for SDP. At present, the company has created as many as 1,400 jobs, and is now one of the top-ranked businesses in Paraguay in terms of the number of employees and the amount of sales.

However, efforts made at the time of the factory’s commencement of operations were far from easy. Looking back on those days, Vice President Hiroshi Kuroda described difficulties at that time as follows: “Most people in Paraguay are engaged in agriculture. Therefore, almost all SDP employees had no experience in working for a company. In cooperation with trainers who had acquired skills in Japan or Brazil, I educated workers patiently and earnestly. The penetration of education and the progress of on-site improvement activities have now brought a stable product quality.” What measures were taken to achieve “globally common best quality” at the new factory in the early days of commencement of production?
“Wiring harnesses are mostly assembled manually. Thus, operational precision is a fundamental principle. As the basic management policy for Sumitomo Wiring Systems’ manufacturing, three types of management are thoroughly implemented: managing compliance with standard operating procedures (operational compliance); checking changes in people, things and equipment (change point management); and checking abnormalities (anomaly management). We believe that the steady implementation of these three types of management and education leads to the achievement of a globally common best quality” (Kuroda).
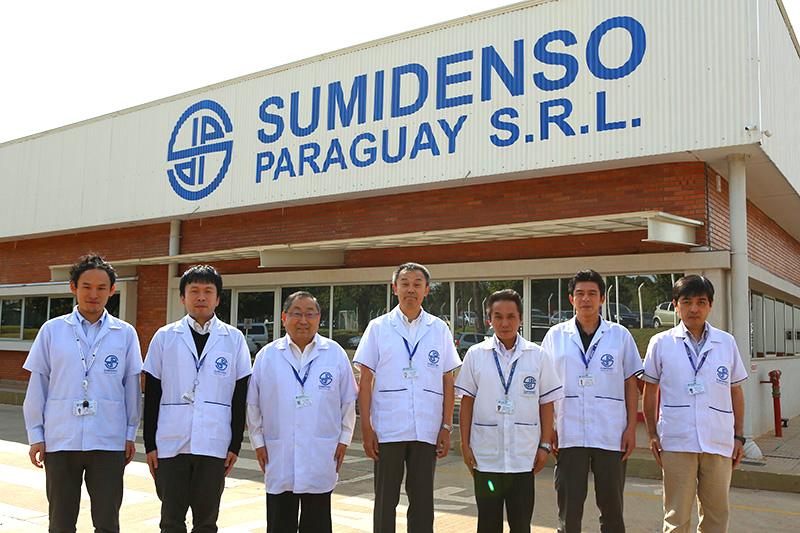
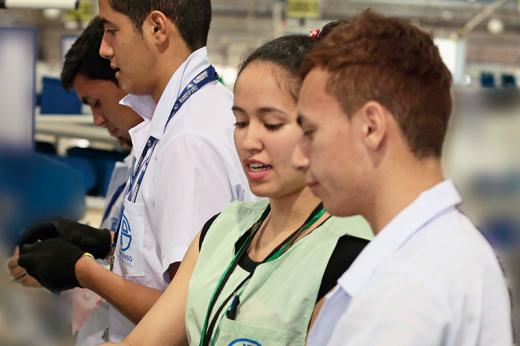
Here are some stories of SDP employees. Noelia Diaz, Line Leader, joined SDP concurrently with the establishment of the company. “Previously I worked as a cashier at a supermarket. I am pleased to have taken this job. My persistent efforts were recognized and I was appointed as leader, which has allowed me to grow mentally. I share what I have learned from Japanese trainers with my team members. I teach them the importance of completing a job right to the end with due care.” Noelia is immersed in training her subordinates.
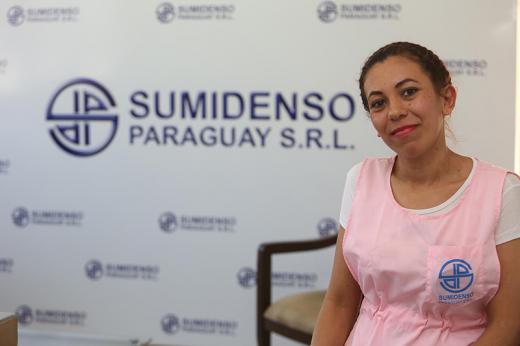
Minami Valeria, an operator, joined the company to take on a new challenge. She used to work as a babysitter and a nurse, but she wanted to have a steady job. “At the beginning, I was a slow worker, so I sometimes inconvenienced the people around me. However, as the leader and other operators encouraged me saying ‘You can do it,’ now I can do my job very quickly. I would like to acquire more skills and take on jobs other than that of an operator,” said Minami enthusiastically. In this way, the location for manufacturing wiring harnesses functions as a place that provides workers with the opportunity to acquire skills and grow mentally.
At present, in Paraguay, in response to increasing demand for automobiles in South America, a new production project is about to be launched. “By utilizing our experience and making a concerted effort, we want to start a new project successfully. I expect that success in this project will further improve the performance levels of our employees” (Morii). The Sumitomo Electric Group’s manufacturing philosophy has been passed down unbroken in a faraway land—Paraguay in South America.
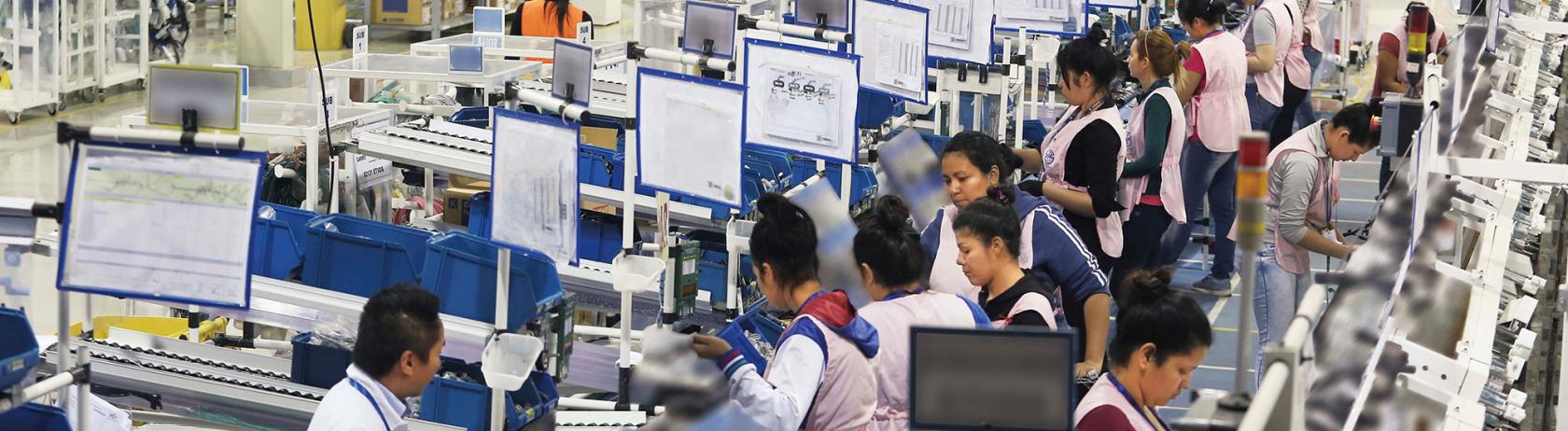