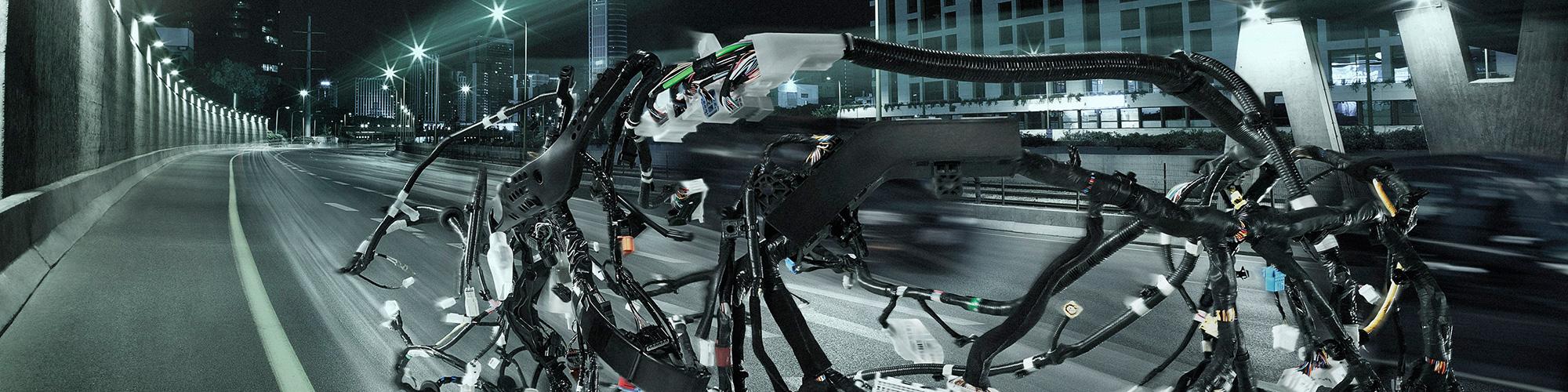
Creating the Future of Automobiles
New automotive era conceived by Sumitomo Electric
Step toward “complete replacement with aluminum wiring harness”
Before explaining the anti-corrosion technology developed by Yamano, it is necessary to describe the corrosion mechanism of aluminum. An aluminum wiring harness has a portion where aluminum wires connect with a copper-based terminal.For connections between copper and aluminum, the adhesion of salt water or other electrolytic solution causes galvanic corrosion, resulting in intense leaching of aluminum. This corrosion issue was one of the major factors that had long hindered the realization of aluminum wiring harnesses. Thus, to create aluminum wiring harnesses for vehicles, galvanic corrosion was a crucial issue to be resolved. To that end, Yamano launched a field research for vehicles used under severe environments.
“The largest environmental concern in terms of corrosion is the adhesion of salt water or other electrolytic solution. Therefore, I conducted surveys on aging vehicles used in regions where the adhesion of electrolytic solution is often observed, more specifically, the Middle East, where the adhesion of chlorides is a common issue; North America, where corrosion issues caused by the adhesion of snow-melting salt have come to the fore; and Southeast Asia, where the intrusion of water into vehicles often occurs due to sudden showers. By quantifying the concentration of salt, I clarify the relationship between the occurrence of corrosion and the concentration of salt” (Yamano).
Yamano’s research has revealed another fact that vehicles have portions where the adhesion of salt water cannot be avoided, causing corrosion to terminals there. Corrosion occurs at the crimped portions of terminals connected to wiring harnesses. The challenge to be tackled became obvious: the establishment of anti-corrosion technology for crimped portions connecting wires to terminals. After thorough study, it turned out that, to prevent corrosion, complete protection needs to be applied not only to exposed aluminum conductors but also to the rear end of a terminal. Thus, a method whereby resin molding is applied to the whole, including the rear end of a terminal and the crimped portion, was employed.
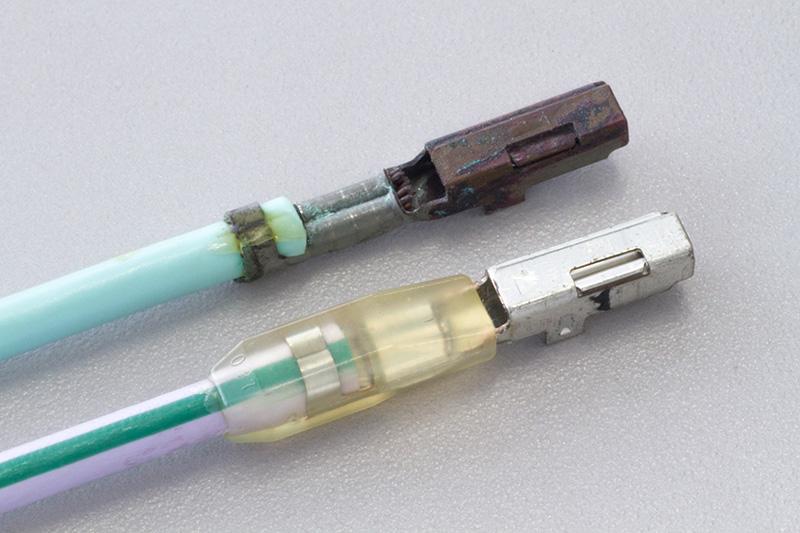
This aluminum wiring harness, created as a “make-or-break product” for the Sumitomo Electric Group, came to be installed on automobiles in 2010. The Group was considered to enjoy superiority in its comprehensive technological prowess over its competitors due to its total manufacturing, which begins with the development of materials and ends with mass production. At present, Sumitomo Electric Group’s aluminum wiring harnesses are delivered to many automobile manufacturers in and outside Japan, and used all over the world, including Europe and the United States. The product is highly regarded for its excellent reliability, making a great contribution to the achievement of the original objective, or the reduction of vehicle weight. Significant strides forward have been made in reducing CO2 emissions.
Furthermore, the Sumitomo Electric Group developed a plan for the complete replacement with aluminum wiring harnesses at an early stage. Under this plan, the Group has conducted research and development on aluminum wiring harnesses of its own accord. One of the fruits of this effort is high-strength aluminum wires that were installed on vehicles for the first time in 2015. Before that, the application of aluminum wiring harnesses to the vicinity of an engine had been hindered by vibration issues. The Group strove to develop aluminum wiring harnesses that could endure vibration-induced bending, resulting in the realization of a product that was the same size as a copper wire, with excellent strength and conductivity, embodying the Group’s high degree of engineering expertise.
When we cast our eyes to the foreseeable future of automobiles, it is expected that more wiring harnesses will be installed in response to further progress in electronization. In the near future, aluminum wiring harnesses, which can reduce vehicle weight, will become increasingly important. Meanwhile, aluminum wires are required to conform to application to electric vehicles, which will become the global mainstream. Electric vehicles require high current. As the next logical step, enlargement of the diameter of aluminum wires is inevitable. “The development of aluminum wires that conform to high current with a minimum diameter enlargement is also a significant challenge.” (Yasuyuki Otsuka). Moreover, as electric vehicles consume huge amounts of electricity, the development of aluminum wires that can cope with heating is another major challenge.
Be a trailblazer and create new era of automobiles
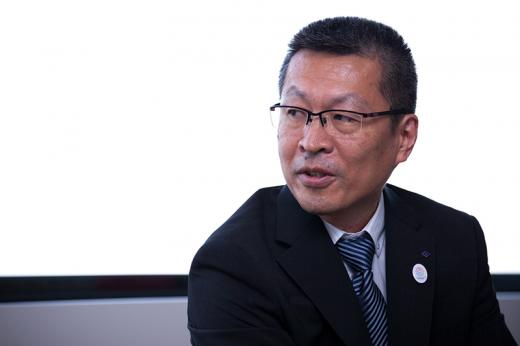
The Sumitomo Electric Group has already begun taking measures with an eye to the automobile society to come. A strategic, cross-organizational task force has also been established. “Automobiles are entering a new phase, namely electrification observed in hybrid and electric vehicles, and intellectualization caused by progress in information and communications technology, lowering barriers to entry in the auto industry. As for users, ownership will be replaced by car sharing. The provision of new added value by new players and the creation of new business models may arise. Under these circumstances, we would like to tackle the challenge of creating an original added value conforming to a new era of automobiles in a timely manner” (Masataka Inoue, Executive Officer, Sumitomo Electric).
Inoue describes automotive services by comparing them to music services as follows: Today, music has become portable, and you can enjoy music services in the form of sharing. Greater importance is placed not on ownership, but on how to use services and what services can be provided. In the future, similar change is expected to occur in automotive services. Automobiles may serve as a mobile space where you can enjoy a wide variety of services.
Regardless of changes in the role and structure of automobiles, wiring harnesses, which transmit electric power and information in vehicles, will definitely continue to serve as “infrastructure deployed in vehicles” (Shimizu), even as their form changes. There is no doubt, however, that a departure from the present-day supply style, whereby suppliers deliver components to meet car makers’ needs, will be required. “Although the Sumitomo Electric Group has run business as one of the Tier 1 automotive suppliers (prime contractor), it is necessary for us to aim to be a Tier 0.5 supplier. We should consider what changes we want and what proposals we will make. I believe that this is our mission: changing the role of automobiles on our own initiative” (Inoue).
One of the strengths of the Sumitomo Electric Group lies in the fact that the Group can work together not only with car manufacturers but also with businesses in various fields, including electricity and communications. By making the most of its strengths that these other companies lack, the Group intends to take the initiative in proposing and providing new added value and services. The Group’s enthusiasm and attitude are creating the new future of automobiles.
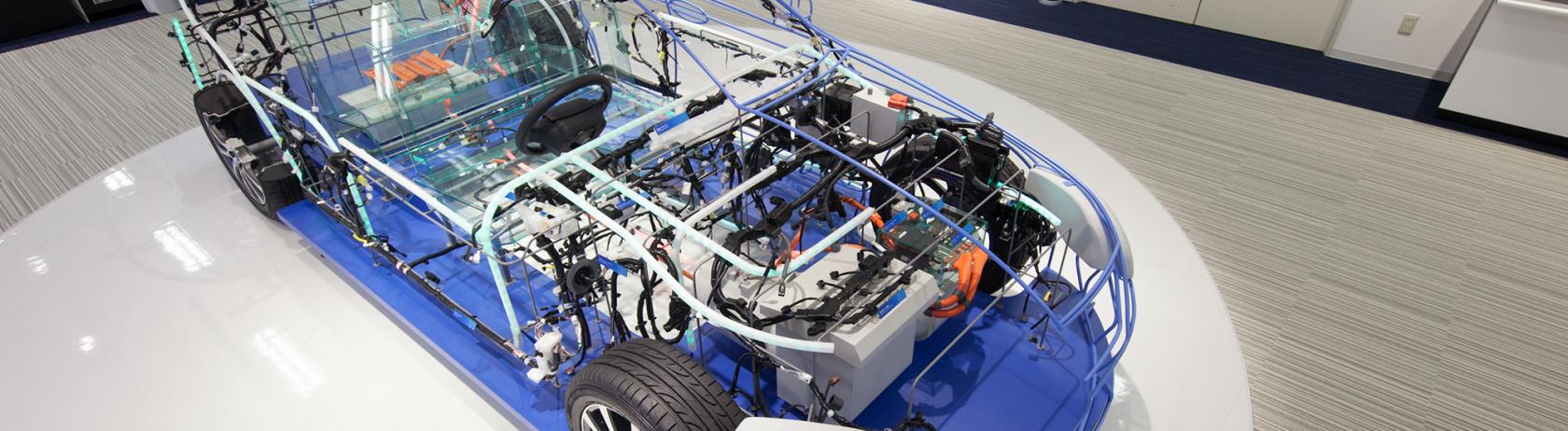
NEXT
Manufacturing Relying on Human Resources
Approximately 250,000 employees in about 30 countries around the world