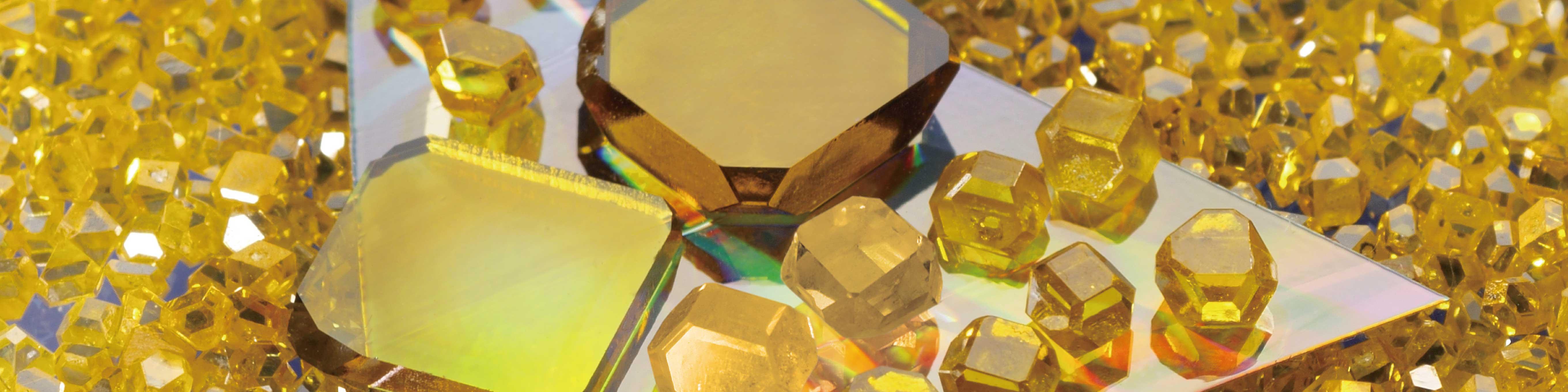
Synthetic Diamonds Strengthen Our Future
When most people think of diamonds, they imagine the sparkly gemstones cut into beautiful shapes. What many don’t realize is that diamonds are also an essential tool in laying the groundwork for a dynamic information economy.
The unique properties that make diamonds so useful are the result of being forged deep in the earth hundreds of millions of years ago. Intense temperatures and pressure arranged carbon atoms into tight tetrahedrons, each atom bonded to four others to produce an incredibly strong network—and the hardest substance found in nature.
Thanks to decades of innovation and technological advancements around the world, including at Sumitomo Electric, it is possible for humans to create diamonds. And we can engineer these synthetic diamonds to outperform their natural counterparts.
The Information Society is Built with Synthetic Diamonds
Synthetic diamonds quickly proved their value as tools: they were cheaper and possessed more uniform hardness and strength than natural diamonds. When crushed into a powder, industrial applications like cutting and polishing were more accurate and easier.
Now, synthetic diamonds are essential components of the machining tools needed to produce a variety of products, such as optical lenses and electronic elements. The compact camera lens in your smartphone may have been produced using molds that were precisely machined by tools with synthetic diamond tips. These diamonds are crucial to next-generation manufacturing that demands higher precision, improved strength, lower cost, faster speeds, and a smaller environmental footprint.
Innovating to Overcome Challenges
Sumitomo Electric began developing synthetic diamonds in the 1970s as a new tool material. The world’s first lab-grown diamonds were created in powder form in the United States in 1954. At Sumitomo Electric, engineers took on the task of producing larger and higher-quality single-crystal diamonds.
They saw remarkable success. Using its renowned ultra-high-pressure technology, in 1982, Sumitomo Electric produced the largest synthetic diamond at the time: 1.2 carats, or about 240 milligrams, and 5mm in size. The crystal even made it into the 1985 Guinness Book of World Records. Today, it’s possible to produce high-quality synthetic diamonds of about 10 carats in size, similar to those pictured below.
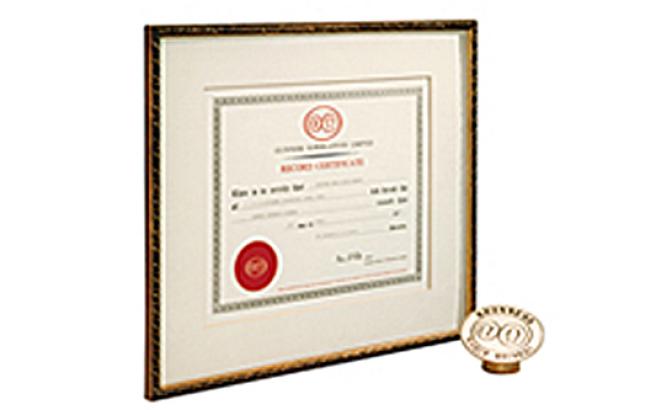
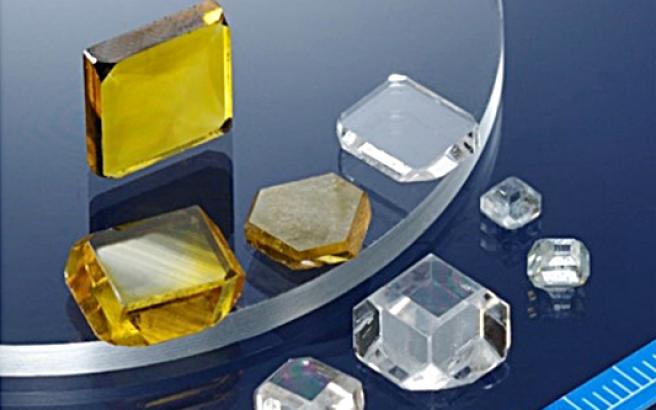
Despite this achievement, Sumitomo Electric’s engineers believed they could create something even stronger. With enough force from the right direction, crystals can break or split along planes of weakness, a property called cleavage. This is true of natural and synthetic single-crystal diamonds. The engineers built on an existing process of using heat to sinter diamonds to develop a new product: nano-polycrystalline diamonds. Nano-polycrystalline diamonds are fine diamond particles tightly and directly bonded together without any inclusions in the grain boundaries.
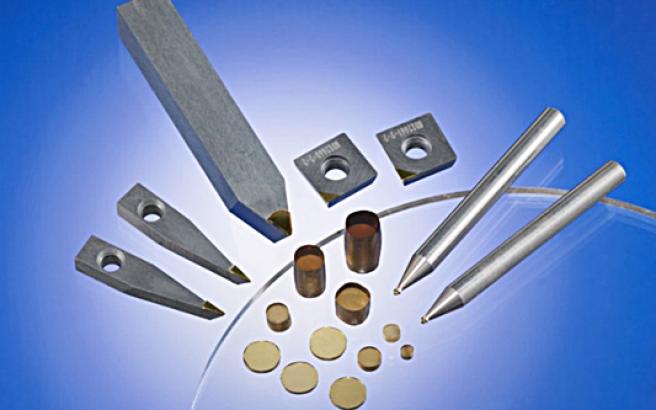
Getting to a nano-polycrystalline diamond wasn’t easy. It required creating extreme conditions: a sustained temperature of 2,700 degrees Celsius combined with ultra-high pressure equivalent to placing three Eiffel Towers on the palm of one hand. Sumitomo Electric accomplished this by putting a special graphite sample into a multi-anvil apparatus, a machine more typically found in specialized research institutions. A hydraulic press pushes the anvils together to create the conditions necessary to produce a nano-polycrystalline diamond.
This new polycrystalline diamond posed yet another challenge. While it’s relatively easy to cut and polish the surfaces of conventional natural diamonds, nano-polycrystalline diamonds are equally hard on all surfaces. In addition, they don’t have the cleavage properties of single-crystal diamonds. However, Sumitomo Electric developed new technologies that used electrical discharge machining and laser machining to make it possible to process nano-polycrystal diamonds.
Elevating Manufacturing to New Level
It took more than 20 years to develop a nano-polycrystalline diamond that outperformed a single-crystal diamond. But the efforts of Sumitomo Electric’s engineers have paid off, and nano-polycrystalline diamonds are fundamentally changing the way mold manufacturing is done.
The tools that use these diamonds do not wear away, enabling manufacturers to improve accuracy. And by incorporating this ultra-hard material into the machining center, it has made faster production possible—a mold that might have taken a craftsman 20 days to process can be made with high precision in a few hours.
The incredible hardness also means that the shavings produced when machining a mold remain uncontaminated by worn particles from the diamond tool. Those shavings can be reused to create more molds, reducing the environmental impact of production.
Even as Sumitomo Electric’s nano-polycrystalline diamonds revolutionize traditional manufacturing processes, we are investigating innovative new applications. For example, the diamonds may work as a biocompatible material for use in producing artificial joints and teeth. The possibilities for Sumitomo Electric’s nano-polycrystalline diamonds are endless.