The sweet, spongy cookies we know as madeleines are uniquely identifiable for their seashell shapes. Bakers use recipes that draw on principles of baking science, combining specific ingredients at appropriate ratios, placing the resulting mixture into specially crafted molds and then baking them at high temperatures to create the final product.
These same steps can be found in manufacturing, as well. Specifically, manufacturers can draw on a technology called powder metallurgy to create parts. The process involves blending various metal powders at specific ratios to create a mixture that is poured and compacted in specialized molds. The metals undergo a heating process called “sintering,” similar to baking at high temperatures, which bonds the ingredients together. The resulting metal is a “sintered alloy” uniquely shaped for a specific purpose, most commonly as a component of products like automobiles or home appliances.
The use of molds to create identical items has major benefits, especially if they are complicated shapes or would otherwise require individual grinding or assembling pieces to achieve the same result. The process, the resulting parts, and the machines that use those parts, all represent the ingenuity that lies at the heart of monozukuri.
In Japanese, the word monozukuri literally means “manufacturing” or “production,” but it is also an important concept that embodies principals of innovation, expertise, and craftsmanship. For more than a century, Sumitomo Electric has lived up to the ideals of monozukuri, including through the use of powder metallurgy and cutting-edge technologies.
Modern monozukuri is built on centuries of innovation
For hundreds, potentially thousands, of years, cultures around the world have used principles of powder metallurgy to create objects. Nowadays, metal powder formulations and sintering procedures are highly sophisticated, capable of producing robust and precise parts. As a result, powder metallurgy supports the production of automobile parts but also monozukuri on a global scale.
Sumitomo Electric began developing its sintered alloy technology in 1939, when it decided to produce the specially shaped tools, called dies, that were used to draw out copper wires, a central element of its main wire manufacturing business. The company never stopped building on that experience and is now one of the largest sintered alloy parts manufacturers in Japan.
The die production technique used at the time required sintering tungsten powder. But Sumitomo Electric began to experiment with replacing the tungsten with iron powder, which was easier to work with—an effort that produced successful results.
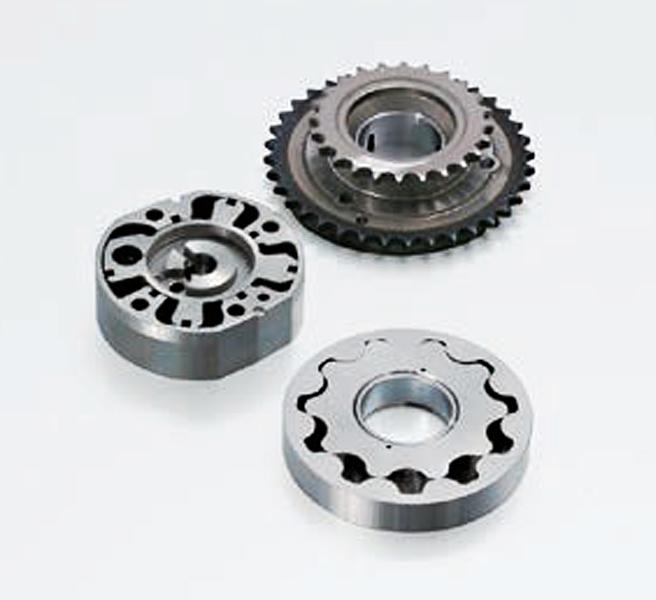
Sumitomo Electric’s initial research into dies and presses stretched about ten years. It built on that die-manufacturing experience to expand its scope to other industrial products and tools. In 1948, it began offering a variety of commercially available products, including oil-impregnated bearings, air conditioner parts, and automobile parts.
Alongside this early work in sintering technology, Sumitomo Electric began research and development into molds and presses. After 1948, it could manufacture both flat parts using molds, but also complicated molded structures made of sintered alloys.
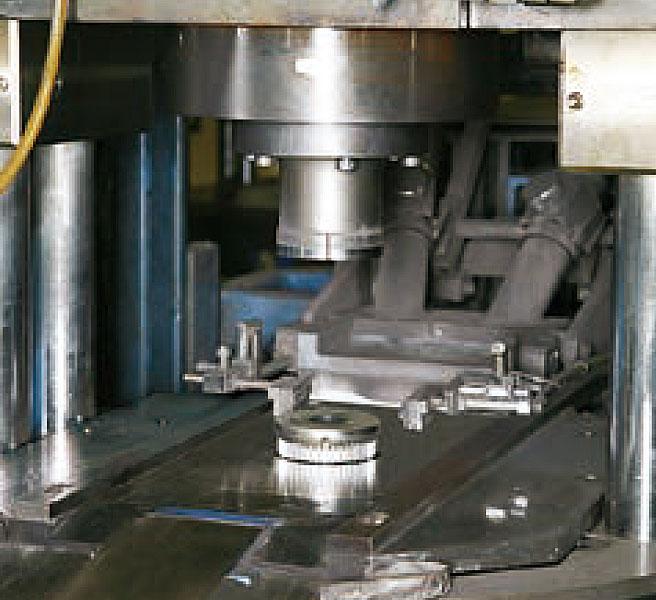
Today, the company manufactures a number of items that draw on advances in sintering and die and mold manufacturing. For example, it employs a sintered brazing technique to create planetary carriers with a sophisticated hollow structure (brazing adds a molten filler metal to the sintered alloy). These planetary carriers are a key component of the multi-gear mechanisms in transmissions. And Sumitomo Electric produces parts with even more complex shapes using a multi-stage molding technique. This practice of building on fundamental techniques in creative and unique ways is central to Sumitomo Electric’s ability to live up to the principle of monozukuri.
Sintered alloys enable the fast production of identical items in large quantities—think thousands, or tens of thousands, of items each month. But one key challenge inherent in this technology is the need to ensure the strength of the final product.
A relentless pursuit of strength
Strength and hardness are crucial traits for sintered alloy parts. These parts are often exposed to high stresses, such as in automobiles, so must be durable and wear-resistant to maintain their quality and reliability. But sintered alloys are made using compacted powders, meaning that they can have tiny internal air pockets. This tends to make them less strong than materials made from Molten metals. While improved metal powder formulations have resulted in higher strength, Sumitomo Electric’s engineers understood that their sintered alloy components needed to be stronger to better resist impact forces.
Sumitomo Electric embarked on improving multiple aspects of the powder metallurgy process to address this need. One key step was increasing the density of the mixture and blending additive metals to increase the base material strength and hardenability during heating. It also developed a new furnace using high-temperature sintering technology to strengthen the bonds between particles.
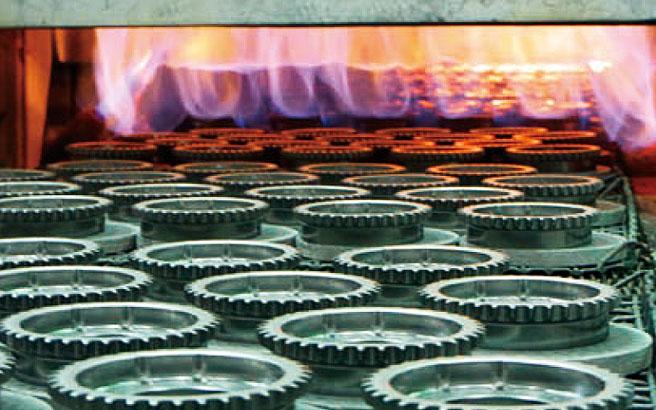
Advances like these are possible because Sumitomo Electric combines R&D innovation with production expertise. Its research and manufacturing divisions collaborate to find the best ways to improve products and ensure that discoveries made in the laboratory can be effectively translated to mass production. The strength of sintered alloys is an area that will always benefit from improvements and Sumitomo Electric remains focused on this goal.
Infinite combinations and infinite possibilities
The virtually infinite ways that we can combine ingredient varieties, ratios, and sintering conditions like temperature and pressure open up the potential for designing important new sintered alloys. While sintering technology may seem old fashioned and low-tech, it is foundational to realizing monozukuri in the modern world. And as a decarbonizing society looks to create more efficient manufacturing processes, powder metallurgy results in less waste material and higher yields when compared to other methods; thus, sintered alloys represent an opportunity for better sustainability.
This technology can also benefit customers of Sumitomo Electric , which is committed to giving them the best possible outcomes. We manufacture parts to meet their specific requests, but also take the extra step of investigating and proposing solutions that capitalize on sintered alloy technology to lower costs and produce parts that will, in turn, improve the quality of their own products.
Our engineers expect sintered alloy technology to become even more central to advanced technologies in the years to come, in areas like industrial robotics and medical technology. In the automotive industry, it is anticipated to expand from the manufacturing of peripheral parts in engines to the production of motors for electric vehicles. Sintered alloy technology has proven its importance time and time again, and it will continue to be fundamental to new innovations far into the future.