Enabling Continuous In-site Measurement and Analysis of Products in Process
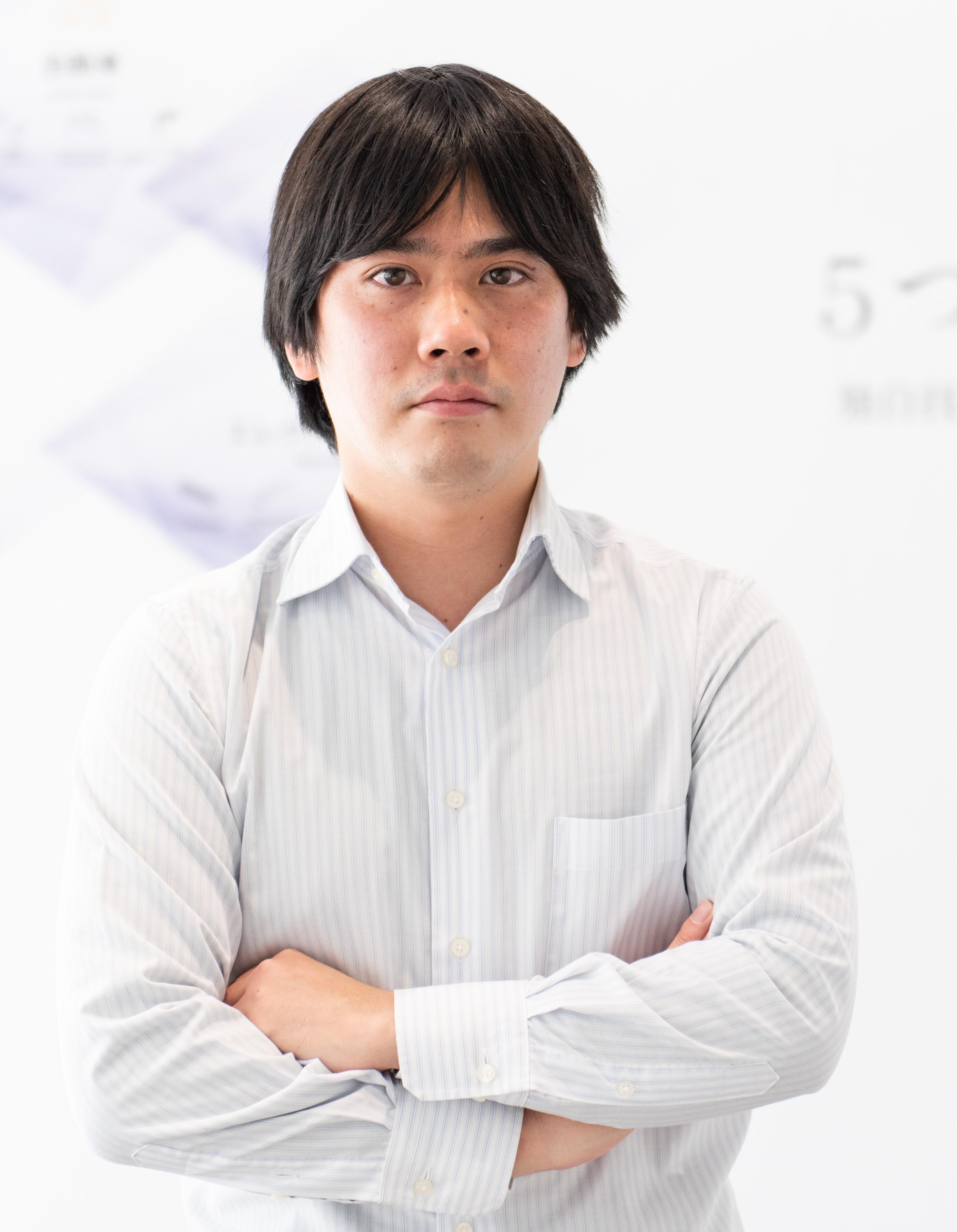
Analysis of Heat Treatment Process of Metallic Materials Using Synchrotron Radiation
Kazuya Tokuda,
Analysis Technology Research Center
The strength of metal products such as copper wire and aluminum wire is controlled by processing and heat treatment during manufacturing. How many degrees and minutes of heat treatment would be required to obtain the required strength in a copper wire of this thickness? To find the optimum conditions to bring out the characteristics of a metal product, we had to prepare a number of samples, heat treat them at different temperatures, and then analyze them in the laboratory using electroscopes and X-ray diffractometers.
In-situ measurement" is a method that allows measurement of product characteristics while the product is being heat treated. Specifically, using extremely powerful X-rays called synchrotron radiation, the product is continuously measured every few seconds during the manufacturing process. If the conventional measurement is compared to a still image of the processed product, in-situ measurement can be described as an atomic-level live video of the product during processing.
Significant breakthroughs dramatically save time and cost
In the past, in-situ measurements have been performed at shared facilities, but the number of cases was limited because of the long waiting time. For example, one of the world's largest synchrotron radiation facilities, SPring-8, is in Hyogo, but we have to wait for several months if we wish to use the facility.
To address this issue, in November 2016, the Company established its own dedicated beamline at the Kyushu Synchrotron Light Research Center, setting up an environment that allows us to perform in-situ measurements anytime.
Meanwhile, the time required for analysis was another issue. Measurement results are now made in the video, which means that the amount of data obtained has increased about 1,000-fold over the conventional still images. Even if we had an excellent facility for all-time measurements, it would be meaningless if we could not keep up with data analysis. Therefore, I have developed a program that automatically analyzes the data in parallel with the measurement. This allows data processing that previously took several weeks to be completed in as little as five minutes. These efforts have dramatically reduced time and cost, not only in optimizing manufacturing conditions but also in materials development and principle elucidation.
I am thrilled with the expectations inside and outside the company
The launch of a dedicated beamline was far larger in scale than the installation of a commercial analyzer, with significant investment and attention from both inside and outside the Company. Although its diameter is only 1/20th that of SPring-8, the SEI beamline is capable of performing a variety of experiments, including in-situ measurements. There are two beamlines running side by side, one for soft X-rays covering long wavelengths and the other for hard X-rays covering short wavelengths, making it possible to analyze the state of almost every elements. Now that we have successfully set up the facility and are able to conduct various experiments with high precision, we intend to address the major issue of how much we can improve our products using this facility.
Related information
・[Press release] Synchrotron Radiation Beamline for Exclusive Use by Sumitomo Electric Group Starts Operation
・[Project id] Expertise that underpins the manufacturing operations
SUMITOMO ELECTRIC TECHNICAL REVIEW
A journal of technical papers explaining the Sumitomo Electric’s technologies. Technical papers are available in PDF format.
Learn more