
Additive Manufacturing
Since July 2021, we have been working in collaboration with Mitsubishi Corporation Technos to develop a mold-less prototyping and development service that can create metal parts using GE Additive's latest binder jet 3D printers. This service not only incorporates our existing sintering technology, but also expands the potential applications of using 3D printers to manufacture mass-produced parts.
Proposed applications : Manifolds, piping, thermal management parts, impellers
Characteristics of Binder Jet 3D Printing
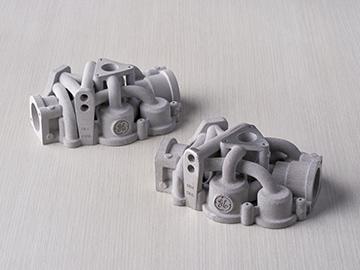
- ・Capable of handling lot-by-lot printing, high-speed printing, and mass production
(compare with powder bed fusion 3D printing)
- ・Able to create detailed 3D shapes
- ・Contributes to improved functionality and performance of end products thanks to the achievement of component designs that were previously impossible to build
Improved Product Functionality and Performance through Flow Path Optimization
・Fewer components: Integral manufacturing eliminates the need to weld or braze components
・Lightweight parts: Reduced weight without compromising strength
・Increased cooling efficiency: Useful in creating parts designed with a lattice structure to improve heat dissipation

What is Binder Jet Sintering?
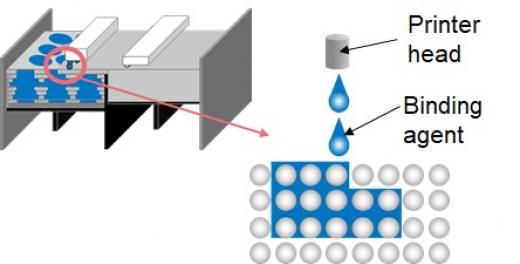
Binder jetting, also known as binder injection, is an additive manufacturing (AM) process that forms a part by repeatedly depositing thin layers of powder while selectively applying a binder, solidifying these layers into a green compact in a drying furnace, and then sintering this green compact into a finished part. In this way, binder jetting is able to create three-dimensional products.
Process and Advantages of Binder Jet Sintering
<Process>
1. Forming
Parts (green compacts) are formed in stacked layers created by repeatedly spreading a thin layer of powder and applying a binding agent.
2. Curing
The resulting green-compact-containing layers are cured in a drying furnace.
3. Powder removal
Loose powder is removed from around the green compacts.
The surrounding metal powder that has not been formed into parts can be reused.
4. Sintering & removal of binding agent
The green compacts are placed in a furnace and sintered, solidifying the parts and removing the binding agent.

<Advantages>
・Compared to laser/electron beam technologies, binder jet 3D printing is better positioned to handle mass production thanks to its high speed of printing and ability to lay down multiple levels of parts (vertically).
・Since binder jetting does not require molds or tooling, customers can be flexible in their requests, from small quantities to large volumes.
・Unlike the laser/electron beam methods, binder jetting does not require the powder to undergo rapid heating or cooling, meaning you receive higher quality parts, with less distortion and fewer cracks forming in complex shapes or between support materials.
・Since the strength of the binding agent used in the green compacts is high and the risk of breakage during powder removal is low, binder jetting allows us to manufacture large products and products with complex geometries, giving you an even wider range of shape options.
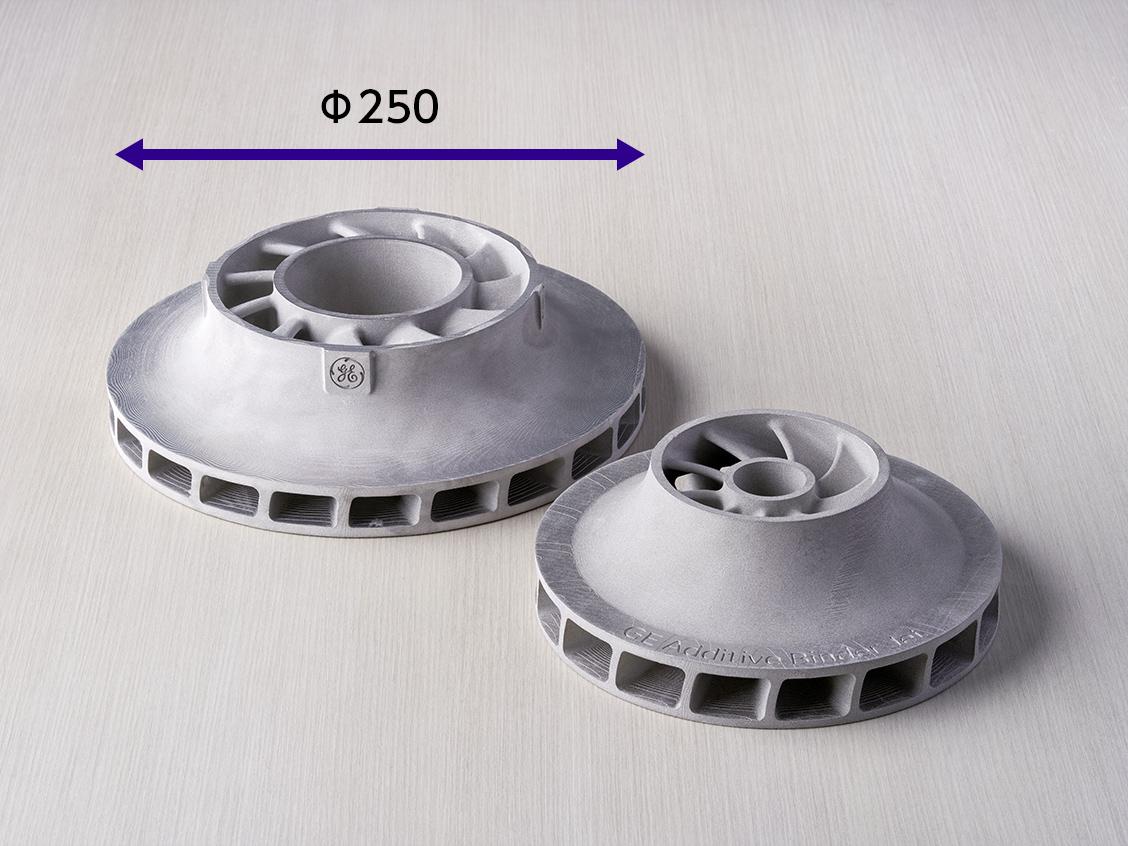