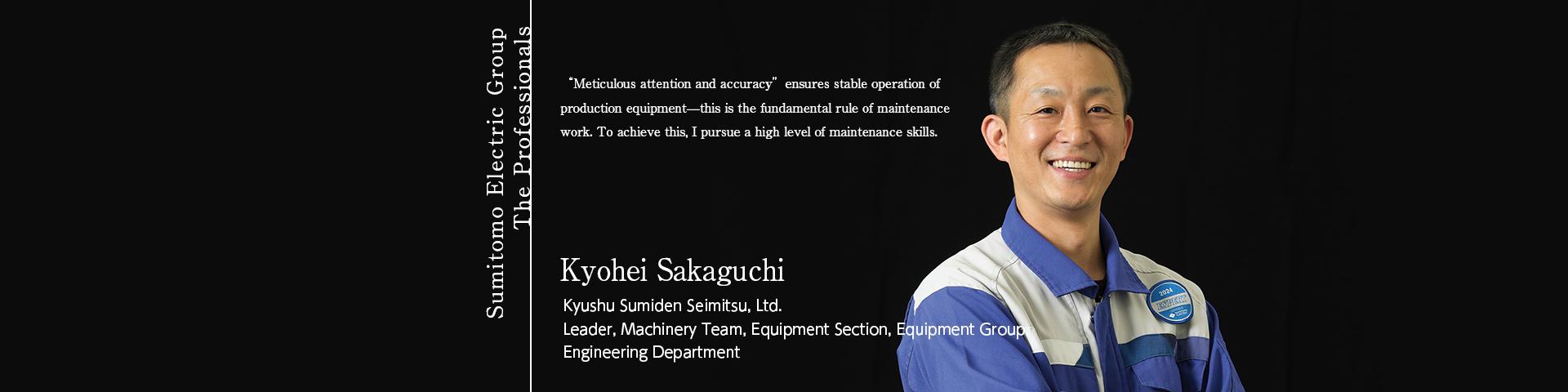

The Impact of the Micro Drill, Thinner Than a Hair
I loved making things when I was a child, so I went to a technical high school. When I was in my second year of high school, I visited Kyushu Sumiden Seimitsu—where I currently work—as part of the curriculum. The tour included observing the manufacturing process for various cutting tools made of hard metals, or cemented carbide alloys. During the tour, I came across a product called a micro drill. This is a drill capable of fine, high-precision hole drilling. I was amazed at the world of precision machining and honestly thought it was great. I was strongly attracted by the technical capabilities of the company in producing high-precision cutting tools and also to its stability, being a member of the Sumitomo Electric Group, so when the time came to look for a job, I applied to join the company. My wish came true and after joining the company, I was assigned to the Production Department. Four years later I was transferred to my current position in the Machinery Team, Equipment Group, Engineering Department. Since then, I have been involved in the maintenance and management of production and utility facilities.
To Achieve Manufacturing Precision in the Micrometer Range
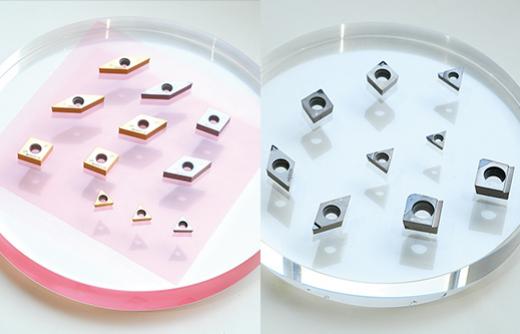
Kyushu Sumiden Seimitsu supplies customers with products that enable them to achieve high precision and performance, such as turning tools, milling tools, end mills, and drills, which underpin the foundations of manufacturing. There are approximately 400 pieces of equipment used to produce these products. My role is to ensure that these production facilities operate smoothly and continuously. My daily work involves quickly and accurately identifying and understanding the causes of any malfunctions that occur in production equipment, and quickly restoring the equipment. Additionally, major events include overhauls, which require the equipment to be shut down for periods ranging from three days to a week, depending on the size of the equipment. The products are required to be extremely precise in the micrometer range. Therefore, the production equipment used to make this possible must also maintain a high level of precision, and overhauls are carried out for this purpose. We disassemble the equipment, repair or replace any damaged parts, and then reassemble it. This is work that requires extreme precision and accuracy, and it is no exaggeration to say that overhauls are the key to maintaining and improving the productivity of the factory.
When carrying out these maintenance tasks, we make sure to communicate closely with operators in the production department. We believe that communication is important in order to build relationships that allow them to speak up immediately if they detect any abnormalities. And when the equipment is restored, the words of gratitude from the operators give us a sense of accomplishment that is beyond compare.
The Frustration Felt Following a Power Recovery and the Sense of Accomplishment as a Leader
After being transferred to the Equipment Group, I absorbed the knowledge and skills of maintenance work under the strict but warm guidance of my senior colleagues. It took two years to memorize the structures of approximately 400 pieces of production equipment and acquire the skills to accurately assemble them during overhauls. At that time, I was working the night shift by myself. A power outage occurred that doesn't normally occur. As a matter of course, all facilities stopped and needed to be restored quickly. But I had no idea what to do. I called my supervisor at 3 am. He told me how to restore the facilities. I felt very frustrated that I was unable to carry out the restoration myself, which wasn't particularly difficult. This experience motivated me to work harder than ever to acquire new knowledge and skills.
I then became the Leader of the Equipment Group's mechanical team and had a number of subordinates. It was around this time that we undertook an overhaul, and I approached it with a completely different mindset than I had before. As a leader, I needed to guide my subordinates to complete their work. Unlike before, however, I was no longer receiving instructions from my seniors but was expected to take the initiative in managing the site. Although I found it difficult to provide guidance, I successfully completed the overhaul and improved the precision of the production equipment. As a leader, I gained a sense of accomplishment unlike anything I had ever experienced before. For me, it felt like I was entering a new phase in my career.
Develop the Next Generation of Employees and Become a Person Who Is Trusted by People Around Me
In April 2023, I was recognized as an expert. I feel very honored. I believe that this recognition reflects my thorough knowledge of approximately 400 pieces of production equipment and my skills, such as the ability to respond appropriately when equipment malfunctions occur. Additionally, I believe that becoming an indispensable member of the Machinery Team was also a factor in my evaluation. My senior colleagues will be retiring in a few years. This means I will be the only maintenance engineer with the required knowledge and experience. As a maintenance expert, I now feel a stronger sense of responsibility than ever to ensure the stable operation of our equipment so that the factory runs efficiently.
My key mission is to train the next generation. The most important thing in training is to thoroughly implement safety first. For example, during an overhaul, safety cannot be ensured without an understanding of the structure of the equipment. The same goes for everyday repair work. Following the wrong procedure can be dangerous. Each piece of equipment and the nature of each problem requires a different response. To avoid danger, we make sure that the switches are turned off and there is no residual energy before starting work. We also provide danger prediction training. Meanwhile, I have made it my policy to adopt a positive approach without fear of failure. I would like to pass on this attitude to my juniors. It is also important to approach everything with curiosity. Being curious makes work more fun. While enjoying my work, I hope to grow into a person who is trusted by my younger colleagues, my peers, and the operators in the production department.
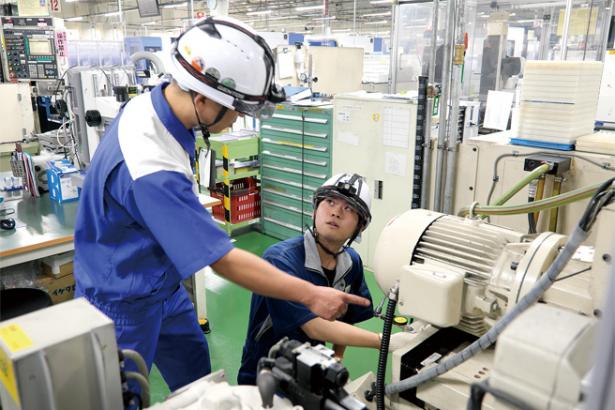
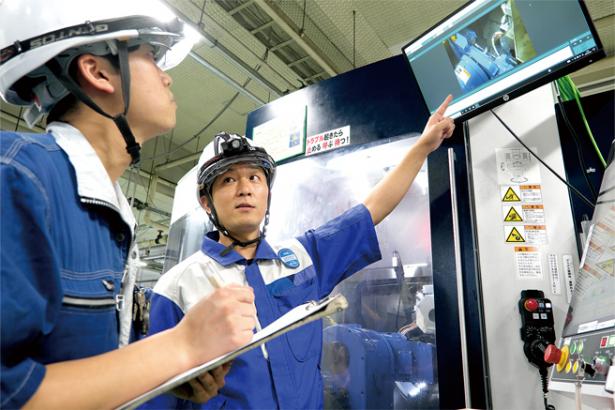
PROFILE
Kyohei Sakaguchi
April 2006
Joined Kyushu Sumiden Seimitsu, Ltd.
October 2006
Assigned to the Micro Drill Section of the Production Department
October 2009
Assigned to the Machinery Team, Equipment Section, Equipment Group, Engineering Department
April 2022
Promoted to Leader of the Machinery Team, Equipment Section, Equipment Group, Engineering Department
April 2023
Recognized as expert* (in general maintenance of equipment and machinery)
* Expert: Sumitomo Electric places importance on the skills that underpin the foundations of manufacturing and recognizes employees who have critical skills as experts in order to maintain, improve, and pass on these skills.