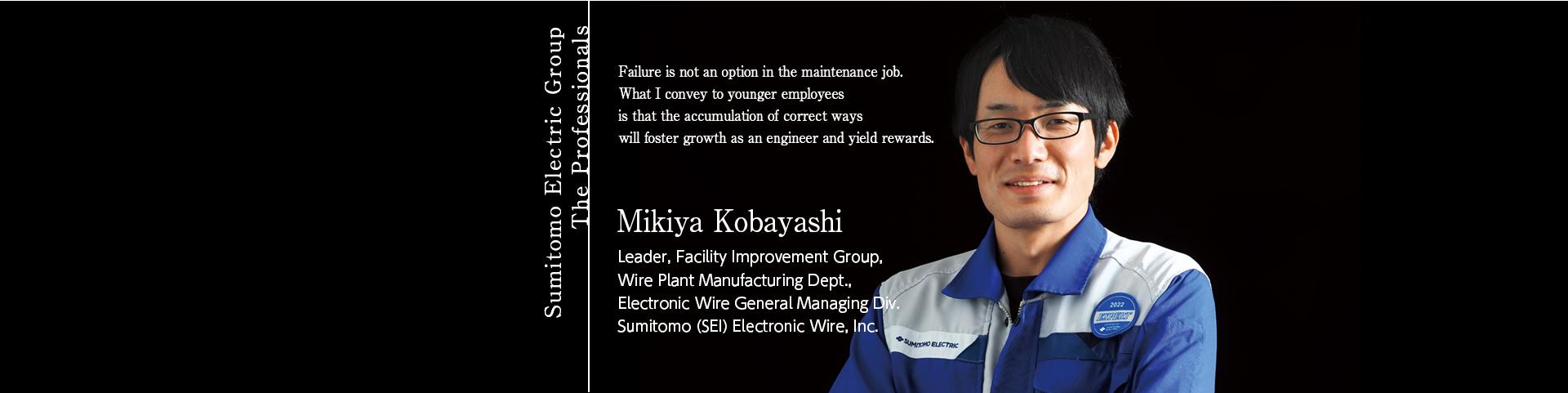
Appeal of maintenance I felt through an internship
Since my father worked in machining, I was surrounded by machines and tools in my childhood. I naturally became interested in manufacturing and went to an engineering high school. After graduation, I searched for a job at a manufacturing company. To understand actual worksites, I participated in an internship at Sumitomo (SEI) Electronic Wire in my hometown of Kanuma, Tochigi. This experience determined my career path. On a plant tour, I saw workers working on the repair of large facilities wearing coveralls and helmets as black as coal. Their attitude was so cool. I wanted to do a job like that and I determined to enter Sumitomo Electric, hoping to become a worker like those who thoroughly understood their facilities and machines. When I was asked where I wanted to be assigned after the induction training, I clearly requested the Maintenance Group, where I had learned how to repair facilities and machines during my internship. Since then, I have engaged in troubleshooting and maintenance of various facilities and machines at all times.
Heart of the electronic wire business
Of various types of facilities and machines, the electron beam processing system (hereinafter, an “irradiator”) is the heart of the electronic wire business of Sumitomo Electric and the core of product development and production. An irradiator is a device that triggers a chemical reaction called cross-link bonding (strong intermolecular bonds) by irradiating high-energy accelerated electron beams on polymer materials. This attains excellent characteristics, such as heat resistance and wear resistance, and products derived from this process are used in various fields, including home appliances and automobiles. One of our important missions is to achieve stable operations with this irradiator. Since an irradiator works under an extreme environment of high vacuum and high voltage, sudden failures and troubles are inevitable. When that happens, we check an electronic chart that visualizes the conditions of the irradiator using current, voltage, and vacuum waveforms, to determine which part is in trouble. We aim to identify the cause and achieve recovery as soon as possible. For example, a power supply tank consisting of an irradiator treats an ultra-high voltage of 20,000 V, so a problem in electrical discharge tends to become serious. We examine the cause of a problem by developing a hypothesis based on the acquired knowledge; however, ultimately visual checks are required. We collect environmentally hazardous insulation gas in a power supply tank, and enter the tank after checking the oxygen concentrations. Then, we check the problematic portion and troubleshoot the problem. This is a job that puts the value of maintenance engineers to the test.
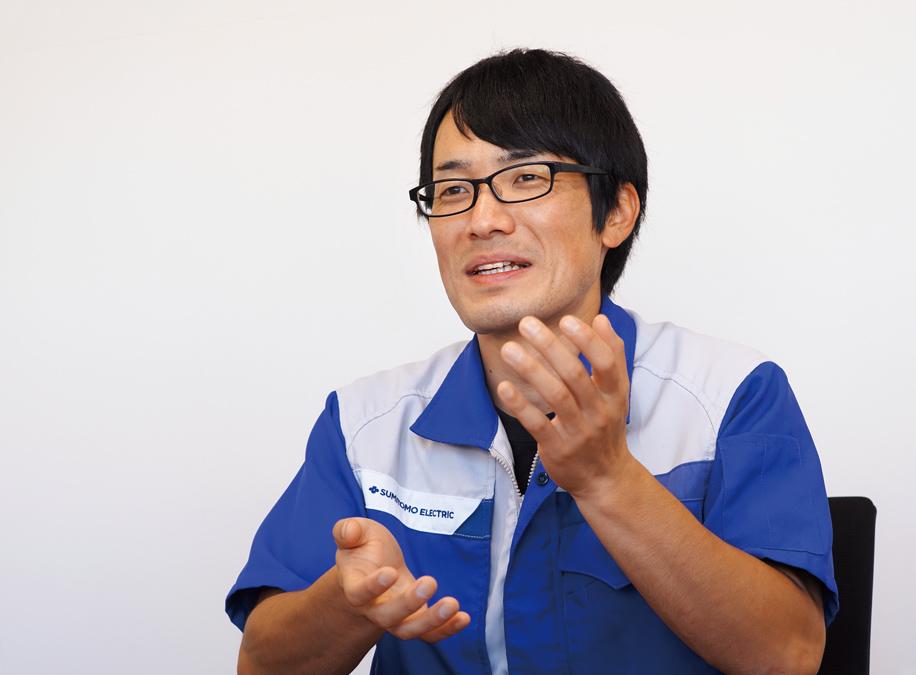
My turning point: experiences in Suzhou, China
I gained knowledge and skills concerning irradiators through training from my passionate seniors. I felt their passion in wanting me to make an immediate contribution. I sought guidance from specialists of irradiator manufacturers during regular inspections, collected information by myself, and assimilated knowledge through every opportunity. However, I often made mistakes at first. I wrongly arranged the elements installed in the power supply tank, or damaged the lid of the vacuum device during operation, which required the reproduction of a high vacuum. Thanks to the support of my seniors, these mistakes did not turn out to be serious but at that time I became acutely aware of my inexperience, and worked to improve my expertise.
One of my turning points was my first overseas business trip to China. I was in charge of installing new irradiators in response to the start of mass production in Suzhou, where Sumitomo Electric has production sites for electronic wire and fine polymer. I also installed auxiliary facilities, while utilizing the comprehensive knowledge I had accumulated in Japan. Perplexed by the language barrier and differences in culture and business practices, I overcame the problems through good communication with local staff members. Since it was a new installation project, I checked and examined all the machines and parts that comprised an irradiator. I gained invaluable experience through this. As a construction supervisor, I focused on securing complete safety. After returning to Japan, I enhanced my awareness of Safety First. My experience in Suzhou helped me mature a lot.
The youngest-ever certified Expert
The plant is conducting failure reduction activity, which has continued since I entered the company. Currently, as part of the implementation of IoT, we are shifting from our previous reactive maintenance to proactive maintenance, such as the use of sensors and maintenance boards for failure prevention, with the help of technological innovation in order to minimize failures. In the spring of 2022, I was certified as the youngest Expert, highly regarded for my skills in troubleshooting irradiators. From now on, my role in training and fostering the younger generation will become more important. I strive to hand down correct knowledge and methods to improve facilities in the proper manner. An irradiator in particular, which works under high vacuum and high voltage, is a very dangerous facility and must be treated with extreme care and reliability. Wrong treatment will complicate the cause of a failure and can be hazardous to workers. Therefore, correctness must come first. A restored facility may fail again. My experience confirms that this fact will strongly discourage maintenance workers. However, another try will help them grow as an engineer. I try to hand down this important attitude to the younger generation.
The nature of maintenance work requires us to be honest and earnest. This practice will contribute to productivity improvement and give us fulfillment. I will continue to acquire expert knowledge and skills concerning facilities including irradiators, to grow up to be a recognized professional to improve facilities. My goal is to become a maintenance worker who is relied on by those around me and required by worksites.
PROFILE
Mikiya Kobayashi
April 2009
Joined Sumitomo Electric Industries, Ltd.,
Trained at the Itami Works
October 2009
Joined Sumitomo (SEI) Electronic Wire, Inc.
Assigned to the Manufacturing Dept., Wire Plant,
Maintenance Group (currently Facility Improvement Group)
2017–2019
Traveled to Suzhou, China three times and experienced construction supervision of installation of new electron beam processing systems
January 2018
Promoted from an engineering position to a supervision position
2019–2021
Traveled to Johor Bahru, Malaysia three times and experienced construction supervision of installation of new electron beam processing systems
April 2022
Certified as an Expert*
* Expert: Focusing on skills supporting our manufacturing base, Sumitomo Electric has certified employees demonstrating important skills as an Expert to maintain, improve, and pass on skills. Kobayashi is the youngest-ever certified Expert.
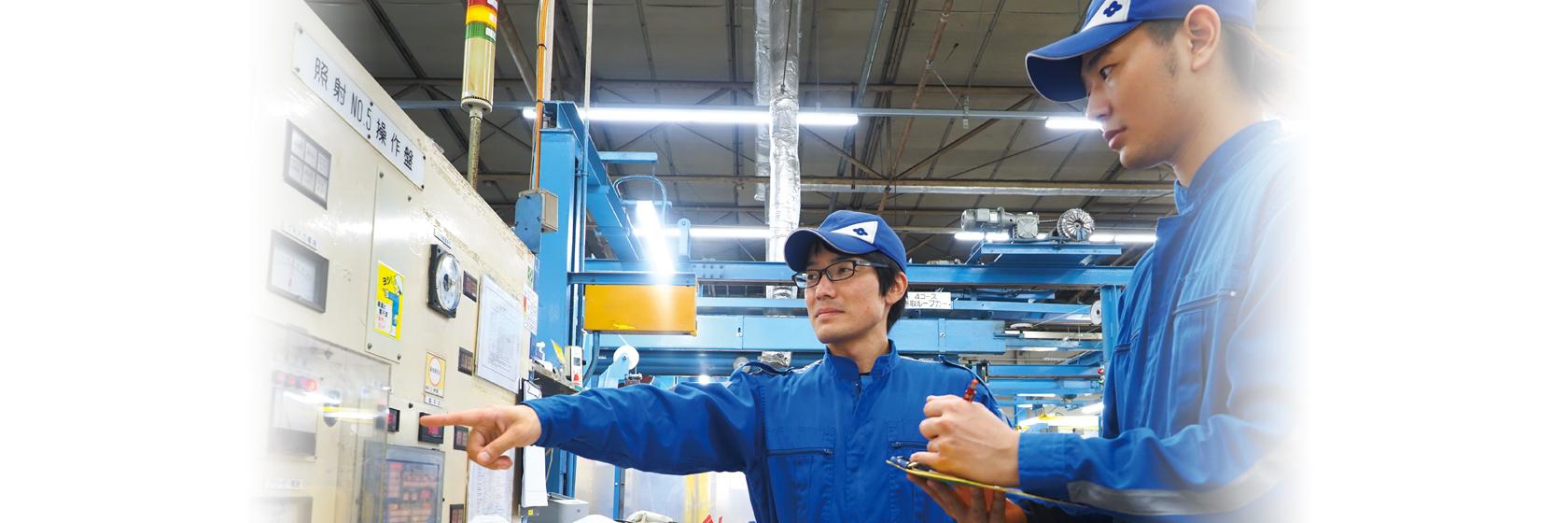