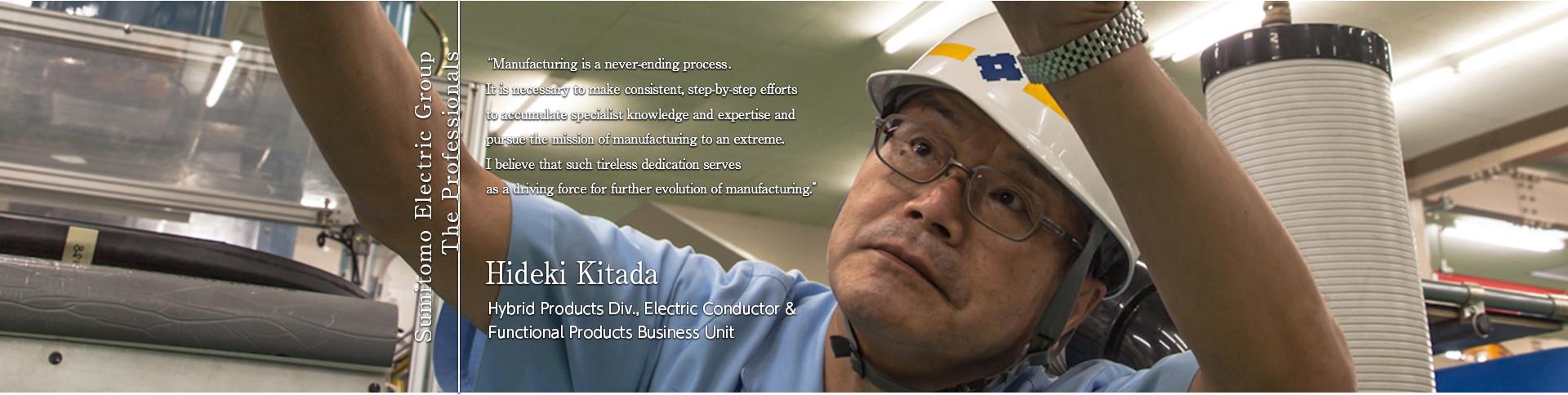
Air springs that serve as the backbone of the evolution of the Shinkansen
After graduating from university with a degree in mechanical engineering, I entered Sumitomo Electric with a strong desire to play an active role as an engineer in supporting fundamental manufacturing technology. Since then, I have dedicated my efforts to the development of air springs. An air spring, consisting of rubber reinforced with tough fibers and metal components, refers to a suspension system to suppress vibration by taking advantage of air compressibility. Air springs employed for railroad vehicles, for instance, are an important security component to significantly alleviate vibration transmitted from wheels to the vehicle body and improve ride quality.
In the 1980s, further increases in the speed of the Shinkansen bullet train were a challenge to overcome in order to win a competitive battle with aircraft for passengers, and were, at the same time, a strong demand from a society with invigorated economic activity. To achieve this, it was essential to reduce vehicle weight. For train bogies into which air springs are incorporated, it was also an important challenge to eliminate the heavyweight bolster. The bolster installed between the bogie and the vehicle body is responsible for buffering the lateral motion and recovering the relative displacement when traveling on a curved railway. We worked on a new structural design and finally developed a bolster-less bogie featuring an air spring that functions as a conventional bolster (Fig. 1). Moreover, many of the metal components of the air spring were replaced with aluminum alloy to reduce the bogie weight. Our design to optimize spring characteristics depending on traveling conditions also enabled Shinkansen trains to provide a truly comfortable ride. Since then, bolster-less bogies have been employed for Shinkansen vehicles.
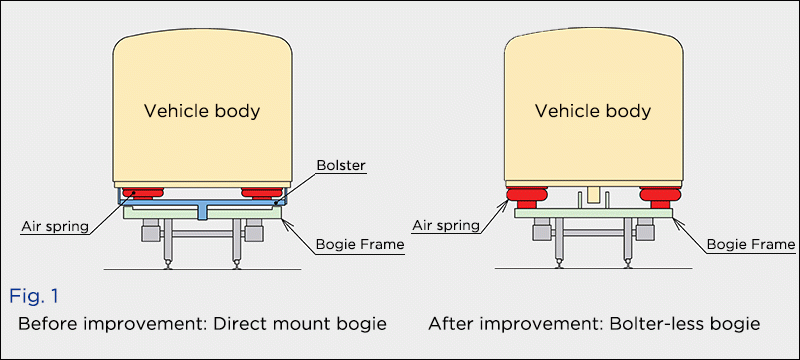
Development of an industry-standard air spring
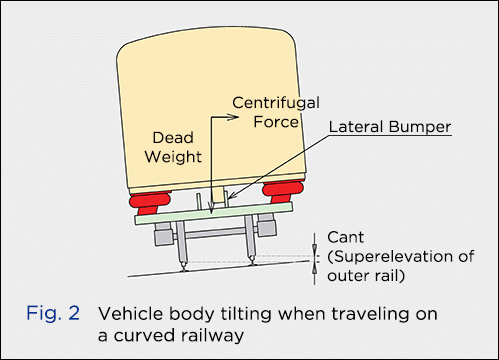
In 1993, we were requested to develop a new air spring technology to improve ride quality when Shinkansen trains travel on curved railways at higher speeds. The Japanese archipelago is made up almost entirely of steep mountain areas with very few plains. This means there are a lot of curves on railway tracks. On the curve of a railway, a certain level of cant (the difference in height of the inner and outer rails) is created, so that the vehicle body can be tilted inwards due to its weight to offset the force by which the body tilts outwards on a curved railway due to centrifugal force.
When a train passes through a curved railway with an insufficient level of cant at a higher speed, excess centrifugal force is generated, pushing the carriage outwards to its maximum possible position. To prevent this, lateral bumpers (stoppers) were installed between the vehicle body and the bogie. However, such bumper collisions led to a significant decrease in ride comfort (Fig. 2). We needed to develop a new technology to eliminate bumper collisions caused when trains pass through curved railways.
Our challenge was to develop an air spring whose reaction force is equivalent to the centrifugal force. We repeatedly visited our customer and made technological proposals, but we were not able to get to the point where our proposal was accepted. We, together with our customer, made steady efforts through a lot of trial and error. We faced various hardships, but we never gave up. As a result of tenacious efforts, we finally succeeded in developing an air spring that can react to the excess centrifugal force created by increased speeds. This technology improved ride quality without bumper collisions even when trains pass through curved railways at higher speeds. A full five years were spent on the development and introduction of the new air spring technology, but this gave me, as an engineer, a lot of valuable experience and a great sense of achievement.
This technology became the standard structural technology for Shinkansen air springs. Later, further increases in speed when passing through curved railways were achieved by developing a body tilting system that makes optimal use of the characteristics of air springs. For a series of new Shinkansen models introduced later, we made steady efforts to improve air springs to ensure better safety and comfort of passengers.
Advancement into the Chinese market was an epoch-making event for me. In 2010, I was transferred to China to establish a plant from scratch, together with two local staff members, and then I was able to put local production of air springs for China Railway High-speed (CRH) on track. After my return to Japan, air springs saw a drastic increase in sales and grew to a core product of the Hybrid Products Division. Our products have been employed for about half of the CRH trains.
Sumitomo Electric’s engineer DNA handed down from one generation to another
I feel incredibly lucky to have been able to develop air springs into a successful business with the help of colleagues and other people around me. In retrospect, it was a tough road. The history of air spring technology goes back half a century, and air springs went through many improvements. I myself diligently persisted in efforts to repeatedly improve the structural design of air springs. I believe that my strong desire to play an active role as an engineer in supporting fundamental manufacturing technology was materialized in the form of the air springs that serve as the backbone of the evolution of high-speed rail trains.
The air spring has kept evolving in line with the times and social needs. With the advancement of system integration including control technology, we need to respond to new challenges, such as increasing running speeds, ensuring security and reliability, and improving environmental friendliness and ride comfort.
Based on the knowledge and experience acquired so far, I have also engaged in the nurturing of young engineers. I believe that my mission is to pass on the knowledge and skills imparted from my predecessors to younger engineers, and to aggressively pursue universal themes in manufacturing. Manufacturing is a process of efforts to pursue thorough optimization, and there is no end to the efforts. “Persistence and enthusiasm” is my creed as an engineer and, I believe, is also “DNA” handed down in Sumitomo Electric.
PROFILE
Hideki Kitada
1980
Entered Sumitomo Electric Industries, Ltd. Assigned to the Rubber and Plastic Products Div. (current Hybrid Products Div.)
1998
Manager, Vibration Control Products Group, Engineering Dept .
2007
Manager, Manufacturing Dept. of SEI Hybrid Products, Inc.
2010
President, KTS High-Tech Rubber Co., Ltd.
2013
Chief Engineer, Hybrid Products Div.
2016
Recognized as a Fellow*
* Sumitomo Electric selects several employees as a Fellow every year as a means for recognition of those equipped with high levels of rare specialized knowledge, skills and expertise. In 2017, the title of Fellow was awarded to eight employees, including Mr. Kitada, who was selected for the second consecutive year.
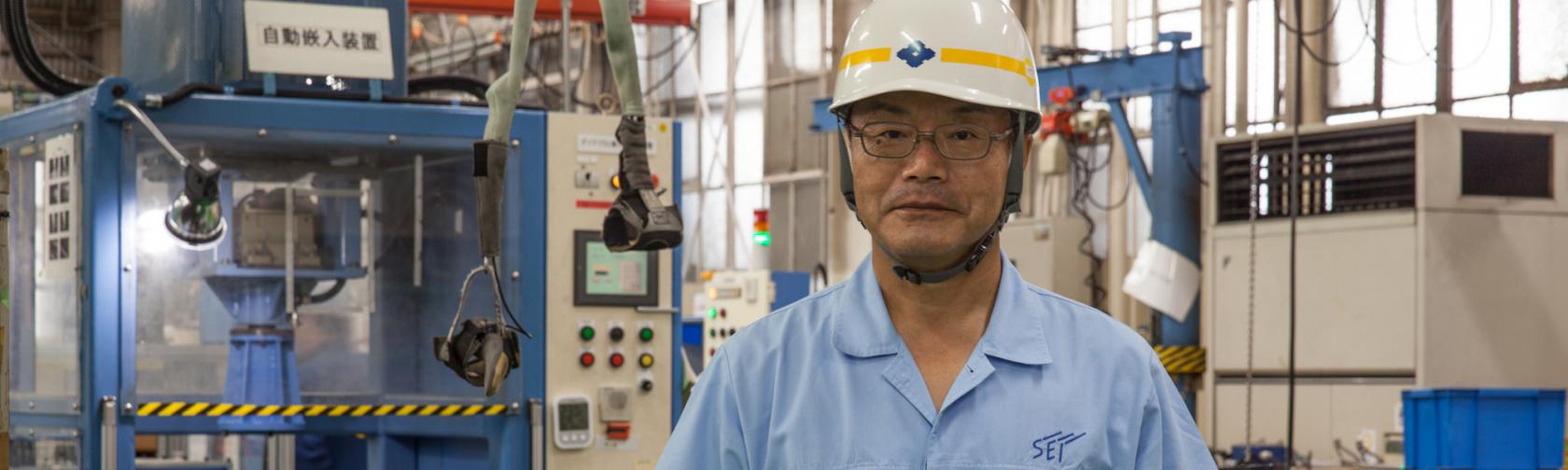