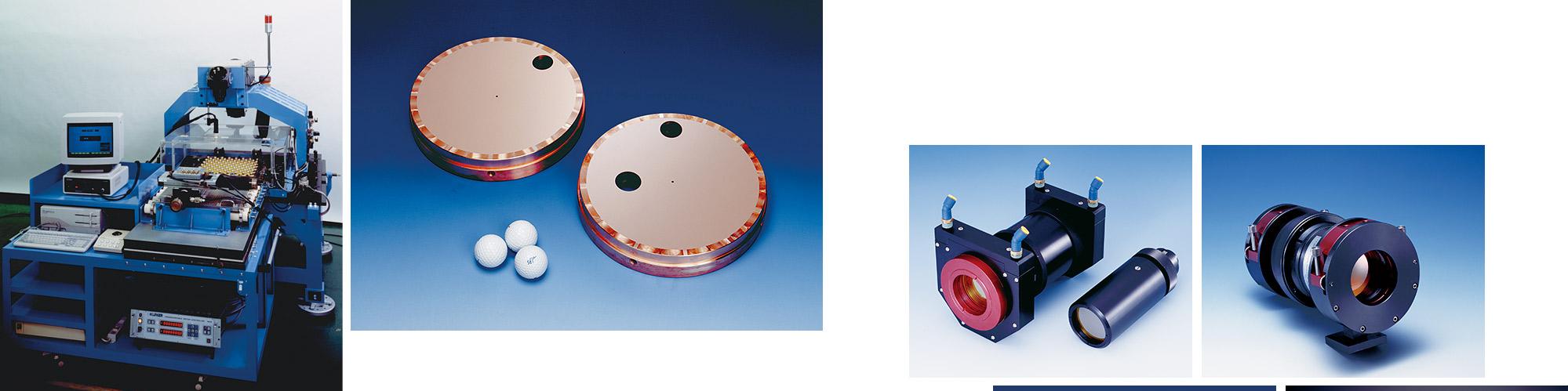
~レーザーの普及を促した国家プロジェクトへの参画~ 超高出力レーザーに耐えるレンズを開発せよ!
CO2レーザー加工用 ZnSe集光レンズの開発
1979年から1984年にかけ、通産省(現 経済産業省)の国家プロジェクトの一つとして「超高性能レーザー応用複合生産システム」の研究開発が実施された。レーザー発振器、メカトロニクス、システムなど担当ごとに多彩な企業が招集され、住友電工グループも参画した。住友電工グループのミッションは光学材料(ZnSe)の開発であった。
当時、レーザー加工に使えるほどの大きな出力が得られたのはCO2レーザー*1のみであった。そのレーザービームを利用する上で必須となるのが、高いエネルギー密度を得るためにビームを小さく絞る集光レンズである。そして、その高出力ビームに耐えうる透過素材の開発であった。CO2レーザーの波長10.6µm(マイクロメートル)で透過率の高い候補材が、人工結晶であるZnSe(ジンクセレンまたはセレン化亜鉛)だった*2。
*1 : CO2(二酸化炭素)ガスを媒体としたレーザー発振器。金属、樹脂、布地、ガラス、木材、コンクリート、紙などの幅広い材料の加工(切断、溶接、穴あけ、マーキング、表面改質など)に早く実用化された。レーザー加工機の中で、最も稼働台数が多い。
*2 : 現在ではさまざまな波長のレーザーがあり、レンズは波長ごとに透過性の高い材料を採用する必要がある。波長10.6µmのCO2レーザー用にはZnSe、波長が1.07µmのファイバーレーザー用には、合成石英ガラスが代表的。
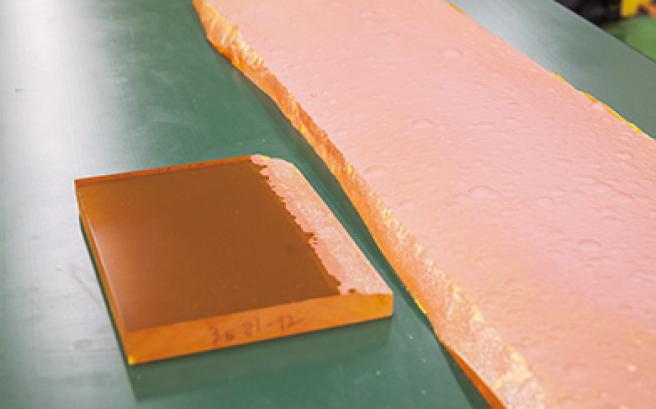
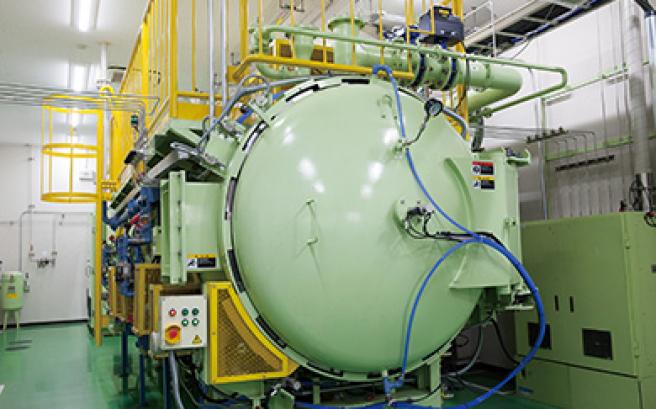
「ZnSe」の合成技術を確立
1980年からZnSe合成技術開発を担当したのが、当時住友電工の研究開発本部に所属していた難波宏邦だった。それまでの超電導材料、光学結晶材料など材料研究に取り組んできた経験を生かし、セレン化水素ガスと亜鉛蒸気を化合させるCVD(Chemical Vapor Deposition=化学気相堆積)法によるZnSe合成に取り組んだ。CVD法とは、反応炉内に配置した基板上に、原料ガスを供給し化学反応によって膜を徐々に堆積させる、いわば薄膜の形成技術で、この堆積を延々数週間継続し、レンズをつくるのに十分な大きさと厚さのインゴット(板状結晶)を得るのは、極めてチャレンジングな課題であった。
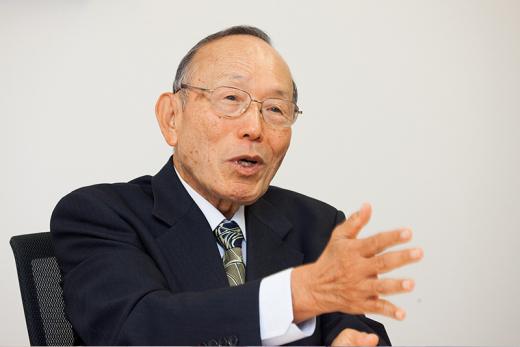
「幸い、当社には先行して化合物半導体であるガリウムヒ素研究の技術集積があり、遊休の小型CVD実験装置を借用して予備実験を行い、本格研究用の反応炉の設計などに、知見を生かせました。まず、安定的に結晶を得るためガスの乱流を抑えることができるガス導入流路設計が重要でした。しかし、温度、流速、ガス圧力など制御パラメーターが多岐にわたる上、一つひとつ実験するというようなコスト、時間は許されませんでした。合成した結晶を徹底的に観察、分析、評価して、関係者の材料物性的な知識、知恵を総動員して、次の実験のための条件を考え抜く極めてハードな日々でした。そして、ようやく1984年に十分な大きさと厚さで高出力レーザーに耐えうるZnSeのインゴット(板状結晶)を作ることができたのです」(難波)
1985年、合成から研磨、コーティングまで一連の製造設備を整備し、ZnSeレンズを市場投入し、1990年代には本格的に事業化を進めた。だが、それでは満足できる成果は得られなかった。当時すでに鋼板の切断にCO2レーザー加工機が普及し始めていたとはいえ、需要は小さく、ZnSeレンズだけでは、ビジネスとして大きな成果が得られなかったのだ。この状況にめげず、顧客訪問を繰り返し、その目的、用途を聴取して、光学部品メーカーとして真摯に対応を続けていった。その結果、その後の住友電工グループの光学部品ビジネスを形作るスタイルへと結実していった。それが、カスタムメードで付加価値の高い製品をソリューション提案していくという考え方だ。鉄鋼メーカー向けに大出力レーザー用放物面鏡や水冷ミラー、自動車メーカー向けにボディ鋼板溶接用スキャナ、発振器メーカー向けに透過率や光の偏光特性を制御するコーティング製品など、さまざまな製品開発を積み重ねていった。
事業拡大に向けて模索を続け、満足できる結果を得ることができたのは、1996年の「CO2レーザー用ZnSe製Fθ(エフシーター)レンズ」開発の成功まで待たなければならなかった。
「このCO2レーザー用Fθレンズは、他社の追随を許しませんでした。そこにあるのは我々の進取性と独創技術の賜物でした。新しいニーズに対応する光学部品の開発から設計、加工までの当時の一連の技術は世界一と自負できるものでした。それは現在も変わっていないと思いますので、今後のファイバーレーザー他さまざまなレーザー用光学部品にも応用できるものと期待しています」(難波)
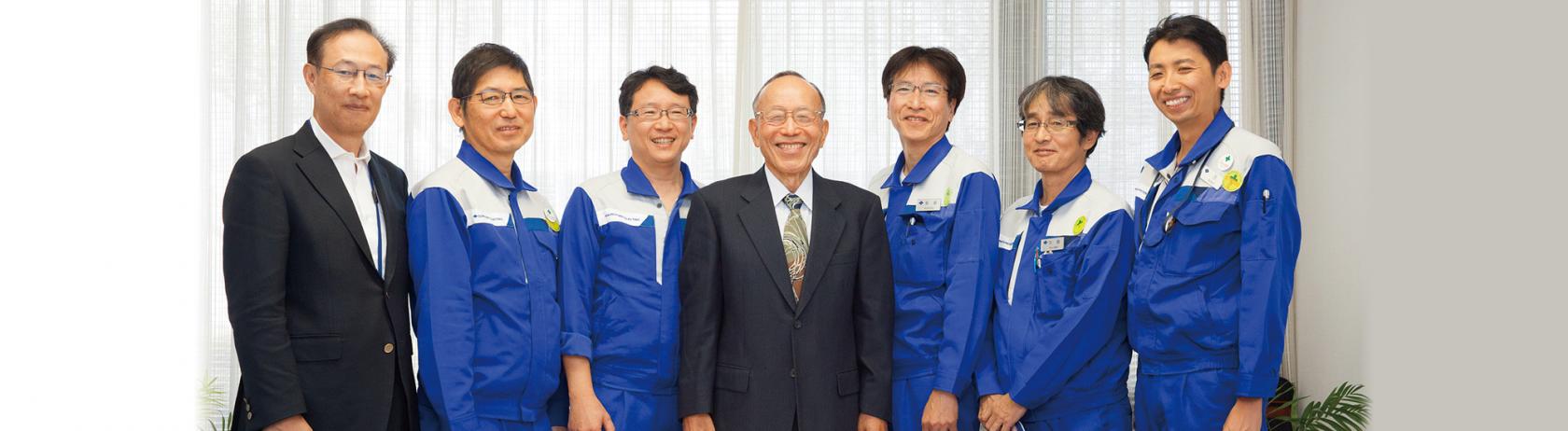