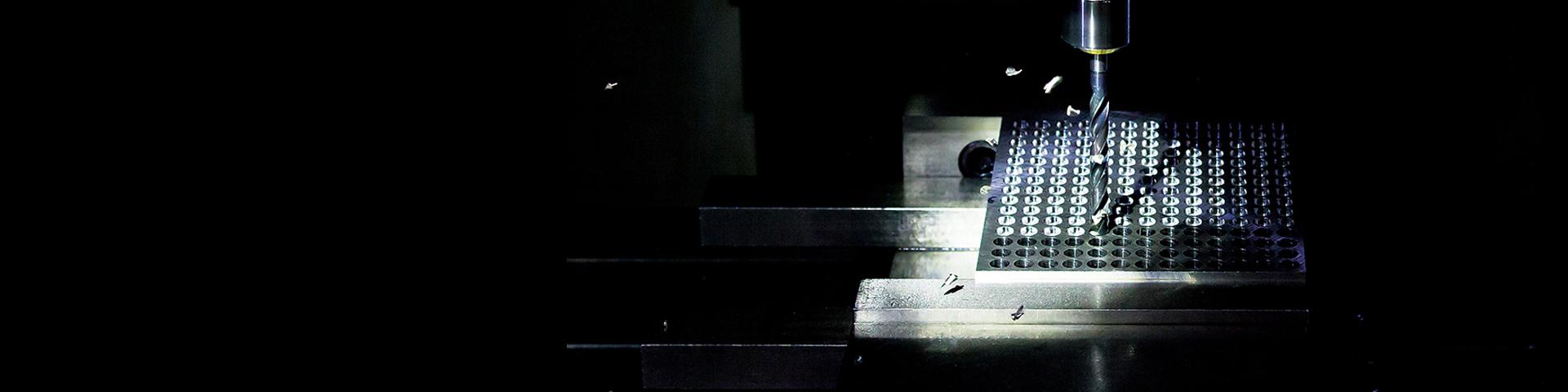
製造現場革新への挑戦〜次世代ものづくりへの社会的要請〜
製造現場は、古くから生産性向上、コストダウンを最重要課題の一つとしてきた。そのエンジンとなったのが、急速に進展したICT*1 による技術革新だった。そして今、一層の高能率化や省力化、さらには環境負荷の低減も視野に入れた製造現場革新の試みが始まっている。そのキーワードが「IoT(Internet of Things)*2=モノのインターネット」だ。たとえば、工場の設備や機器などのモノがインターネットにつながり、データを収集・解析することで生産性の向上を実現するという取り組みが加速している。いわば「IoT」による「つながる工場=スマートファクトリー」の実現であり、「インダストリー4.0」= 第四次産業革命とも呼ばれている。
住友電工グループは、超硬合金をはじめCBN(Cubic boron nitride)焼結体およびダイヤモンド焼結体切削工具など、幅広い切削工具製品を提供し生産性向上やコスト低減に貢献してきた。これら製品の中でも今回の特集では「マルチドリル」をクローズアップする。1984年に市場に投入したマルチドリルは世界の製造現場に革新をもたらした画期的製品だった。そのマルチドリルの開発秘話や現在、そして今後の取り組みを紹介する。
*1 Information and Communication Technology:情報通信技術
*2 あらゆる「モノ(物)」がインターネットにつながり、情報のやり取りをすることで、モノのデータ化やそれに基づく自動化などが進展し、新たな付加価値を生み出すというもの。
それはイゲタロイ®から始まった
〜マルチドリル開発の軌跡〜
切削工具に革命をもたらし製造加工現場を変えた超硬合金
かつて切削工具材料のほとんどは高速度鋼(ハイス)が採用されていたが、ドイツで超硬合金が開発されたことで切削工具の超硬化が進展した。
超硬合金(以下、超硬)とは、硬質の炭化タングステンとコバルトを混合し、焼結して作られる複合材料であり、高硬度、高耐摩耗性、高耐熱性を有することからハイスに比べて高速加工が可能であり、切削加工に革新をもたらした。世界最初の超硬は、1923年ドイツで誕生し、1927年に発売された。同年、住友電工でも研究が始まり、翌1928年、超硬線引きダイス(電線などを所定の寸法径に仕上げるために使用される工具)の試作に成功、1931 年に超硬切削用バイトを商品化し、ここに超硬切削工具ブランド「イゲタロイ®」が誕生した。以来、「イゲタロイ®」は進化を遂げ、現在は旋削加工、フライス加工、エンドミル、穴あけ加工など、機械加工のあらゆるニーズに対応する幅広い製品を提供している。
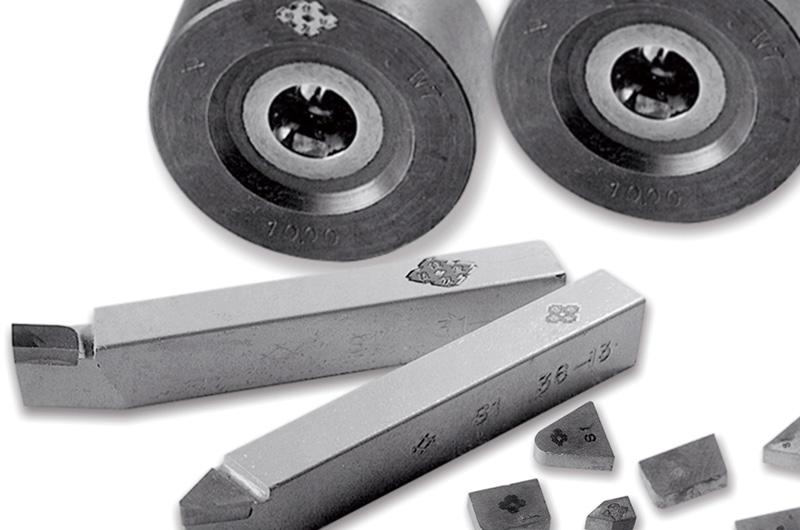
超硬ドリルの開発 切りくずをデザインする
80年以上にわたる歴史の中でも超硬ドリルの開発と市場投入は、製造加工現場に劇的な進化をもたらしたエポックメイキングな出来事だった。従来、穴あけ加工、すなわちドリルの分野は、強度確保などの面から超硬化が困難とされていた。その壁に果敢に挑んだのが、現在、住友電工ハードメタル(株)の主幹技師である森良克だった。1982年のことである。
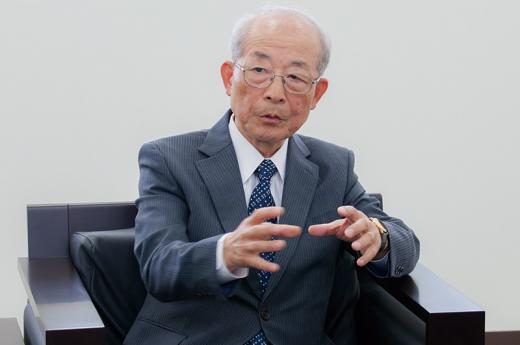
「超硬ドリルの開発は鋳物など、比較的穴のあけやすい材料から始まり、1970年代後半には鋼を加工できる超硬ドリルが普及し始めました。しかし、れらは工具の保持部やネジレ溝となる鋼シャンクに、切れ刃となる超硬合金をロウ付けしたもので、直径が12mm以上のものでした。しかし、ハイスドリルの使用状況を調査すると刃径10mm以下のものが圧倒的に多いことがわかりました。そこで、ドリル径の小さなものを開発し、それを大きな径に応用することを視野に入れて開発に着手しました」(森)
ドリルが他の切削工具と異なるのは、切削と同時に生成される切りくずを穴の底から排出する機能を併せ持つ必要がある点だ。これがドリルの超硬化を阻んでいた。製造加工現場でドリルに求められる最大の要素の一つが「折れない」ことだ。切りくずが排出されないとドリルが折れてしまう。切りくずをスムーズに排出するためには溝を広げなければならない。しかしその分、断面積が減るので強度が落ちる。すなわち、強度確保のためドリルの断面積を大きくし、狭くなった溝から、いかにして切りくずをスムーズに排出するか。最大の難問が立ちふさがった。
「着目したのは切りくず。切りくずが大きいとドリルの溝の中に詰まってしまいますが、短く細かく切断されていれば排出はスムーズになります。試作評価を繰り返し、ドリルの切れ刃の形状を円弧状にすることで、切りくずが短く細く切断されスムーズに排出されることを発見しました。これが超硬ドリル誕生に向けた最大のブレイクスルーとなりました」(森)
市場を驚嘆させた “午前4時の製品”
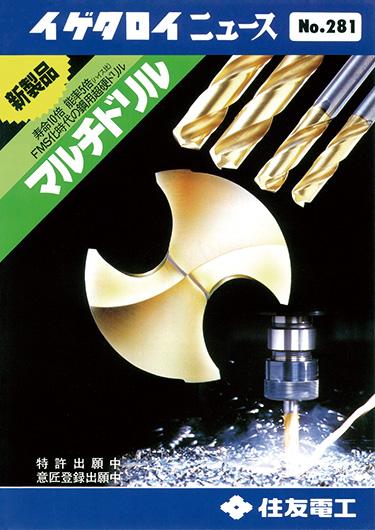
こうして2年を費やして生まれた「マルチドリル」は、1984 年に生産・販売を開始した。市場は絶賛、大手自動車メーカーを中心に採用が相次ぎ、需要は急速に拡大した。マルチドリルは従来のハイスドリルに比べ、4〜10倍の高能率加工を実現、製造加工現場に飛躍的な生産性向上をもたらした。ただドリルという切削工具は、使われる機械や条件設定、使用方法で本来有する性能を十分に発揮できないケースも発生する。課題解決に向け、ユーザー巡回、教育研修体制の整備、研修会などの啓蒙活動を実施、それらの取り組みが、マルチドリルの拡大普及に拍車をかけた。さらに重要なのが、サービスネットワークの構築だった。ドリルは、使用すると刃先が摩耗し削れなくなってしまう。再び使用するためには、刃先を元の状態に再研磨する必要がある。当然、新品同様の刃先品質が求められる。同時に安価なコストで、短い納期で対応することも要求される。それらに応えるため、全国各地の研磨加工会社と提携することで再研磨ネットワークという新たなモデルを構築した。併せて、再研磨設備開発、マシンメーカーへのプログラム提供も行っていった。
「かつて、マルチドリルは午前4 時の製品と言われました。夜明けはまだ遠いと。それも今となっては懐かしい思い出です。紆余曲折の中、仲間とともに夢を追いかけてきたという実感がありますね。今後、これまで蓄積してきた知見を多くの人に伝えていくことで、マルチドリルの進化に寄与していきたいと考えています」(森)
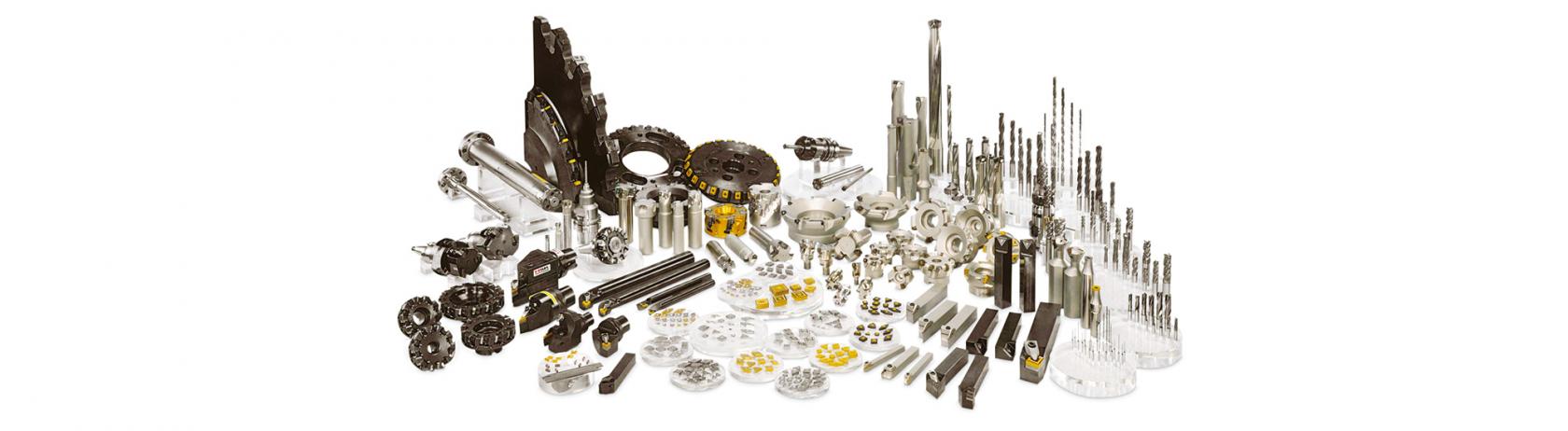