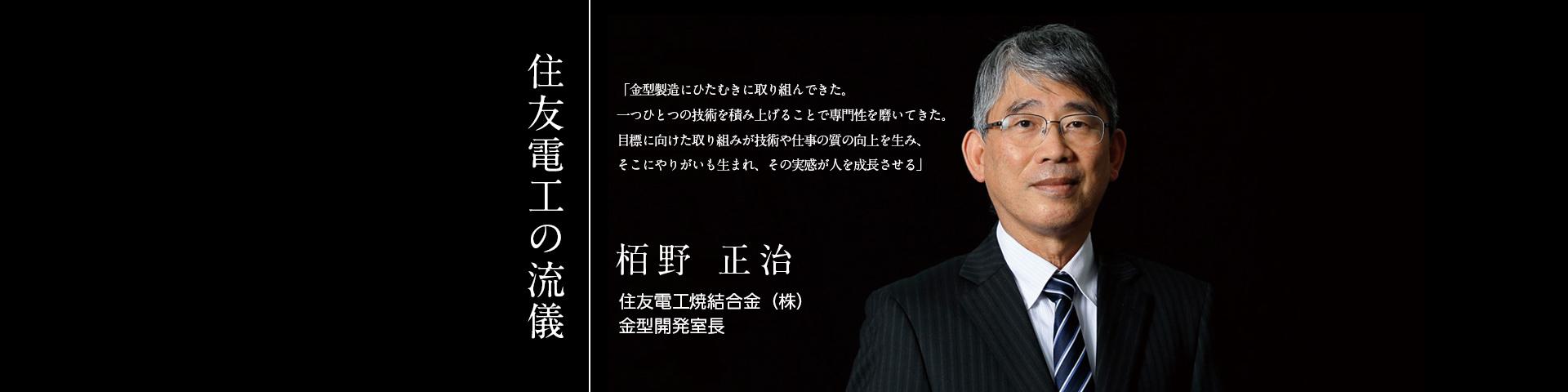
金型——焼結部品製造過程の要
私は入社以来、一貫して金型製造に取り組んできました。金型とは、人々の生活を支える工業部品を、プレスなどの加工を行って精密かつ大量に作り出すために使う金属製の型。金型次第でそれらの品質や性能が左右されるので「モノづくりの原点」とも言われています。私が取り組んできた金型は、社名の一部にもなっている「焼結部品」を製造するために用いられます。焼結部品は鉄を中心に複数の金属を微細な粉末の状態で圧縮成形し、1000℃以上の高温で焼き固める「粉末冶金法」で製造します。焼結部品は高い寸法精度が得られることなどから、自動車部品をはじめ、農機、事務機器、家電製品などに主要部品として広く採用されています。
かつて当社は、金型製造は外注していましたが、私が入社した1984年当時、内製化する動きが始まり、入社早々そのメンバーに任命されました。金型内製化の1期生ということになります。大学では溶接を専攻していたため、金型に関する知見は皆無。技術・ノウハウを得るために約1年間、伊丹にある住友電工の金型部門で実習し、翌1985年から本格的な金型の内製をスタートさせました。先に述べたように、金型自体の品質が製品に大きく影響しますから、金型製造は極めて高い精度が求められます。一つの金型を完成させるのにかかる時間は約1ヶ月、失敗は製品納期に大きく影響します。金型内製は一大プロジェクトであり、ミスが許されない緊張感のある中で事業を開始しました。
チャレンジすることにこそ意味がある
金型製造は専門性の高い世界であり、最先端の設備・技術が求められます。私自身も、着実に技術・ノウハウを吸収することで専門性を高めてきました。そうした中で印象深い出来事があります。金型は設計の段階で強度などの十分な検証をしていますが、粉末の圧縮成形時に、折れ、割れ、欠けなど想定外の破損トラブルが発生することがあります。
例えば、超硬合金製の加圧成形部金型を外側からリング状鋼で拘束し予め圧縮応力を付与して強度を上げる焼き嵌め法にて製作していましたが、当時は経験に頼っており、強度も弱く頻繁に破損していました。工場には大変な負担をかけており、これを解決すべく、当時は創成期で難解であった有限要素法(FEM)解析と実証実験を重ね、強度最大最適の太鼓型焼き嵌め法を開発、画期的に製品寿命を延ばすことに成功しました。金型技術課題を源流の金型設計に遡り解決したことは当時の技術革新でした。
入社9年目の1993年、岡山県の技能検定委員に選任されたことは一つのターニングポイントになりました。技能検定とは、働くうえで必要とされる技能の習得レベルを評価する国家検定制度で、機械加工や建築大工など全部で130職種の試験があり、合格すると「技能士」を名乗ることができます。この技能検定における実施要領の作成や検定試験会場での採点、指導監督などを担うのが技能検定委員ですが、元々私は技能検定委員を目指していたわけではありません。当時、技能検定の職種に新たに機械加工や放電加工が加えられ、社員に検定にチャレンジさせようと思ったことで技能検定に関わるようになりました。それは技能士の資格を取ることで自信を持たせるという目的もありましたが、チャレンジすること自体に意味があると考えたからです。技能検定にチャレンジする人は、検定実施日に向けて地道な練習を続けます。本番では、文字通り顔色を変えて機械に向き合います。合格に向けたそれらの一連の取り組みが重要であり、それが技術や仕事の質の向上を生み、そこにやりがいも生まれると思っています。そうした社内活動をしている中、岡山県から会社に技能検定委員を推薦して欲しいとの要望が届き、私が選任されたというわけです。以来、約四半世紀にわたって技能検定委員を続けてきました。これまで、当社でおよそ50人の技能士が誕生しています。
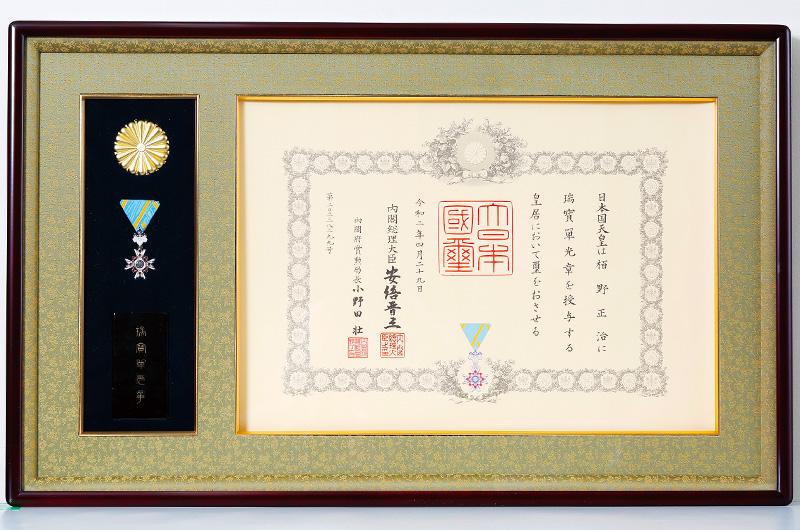
技能検定への功労などで「瑞宝単光章(ずいほうたんこうしょう)」受章
技能検定への功労としていくつかの賞をいただきましたが、今回、春の叙勲として「瑞宝単光章」をいただいたことは、嬉しさより驚きが先にきました。身の引き締まる思いです。技能検定委員としての後進の指導・育成や、粉末冶金業界の技術水準向上に寄与したとの評価も得ましたが、振り返ると、多くの上司・先輩から指導を受け、また同僚・部下の支えがあってここまでやってくることができたと感じています。その意味で、諸先輩、後輩も含め、仲間の代表として頂いた章であると捉えています。
粉末冶金技術を駆使した金型製造は、「ウサギとカメ」の話にたとえれば「カメ」の世界です。ウサギのように一飛びで事を成し遂げることはできません。カメのように一歩一歩コツコツと技術やノウハウを積み上げていくことでしか、金型製造の技術者として大成できません。「地道に、コツコツと」、それが技術者としての私のスタイルであり、流儀といえます。若い人にも「地道に、コツコツと」の大切さを伝えていきたいと思っています。一方で、私が着手した当時と現在の金型製造技術は天と地との開きがあります。それまで人手が必要だったことが、最先端の設備で制御が可能です。今後、AI などの活用で一層の機械化、自動化が進むと思われます。だから若い人たちには形式にとらわれず、自由な発想で取り組んでもらいたい。今後は、恩返しとして、金型製造の魅力、面白さを訴求する中で、若い人や女性が活躍する場を作り、サポートしていきたいと考えています。
PROFILE
栢野 正治 Masaharu Kayano
1984年
旧岡山住電精密(株)入社
新規の取り組みであった金型開発に携わる。
1991年
住友電工焼結合金(株)に社名変更
1993年
岡山県技能検定委員に選任
2004年
岡山県知事感謝状(技能検定功労)
2006年
中央職業能率開発協会会長表彰(技能検定功労)
2014年
厚生労働大臣表彰(技能検定功労)
2015年
製品開発部 技師長
2016年
金型開発室長
2020年
瑞宝単光章受章、現在に至る。
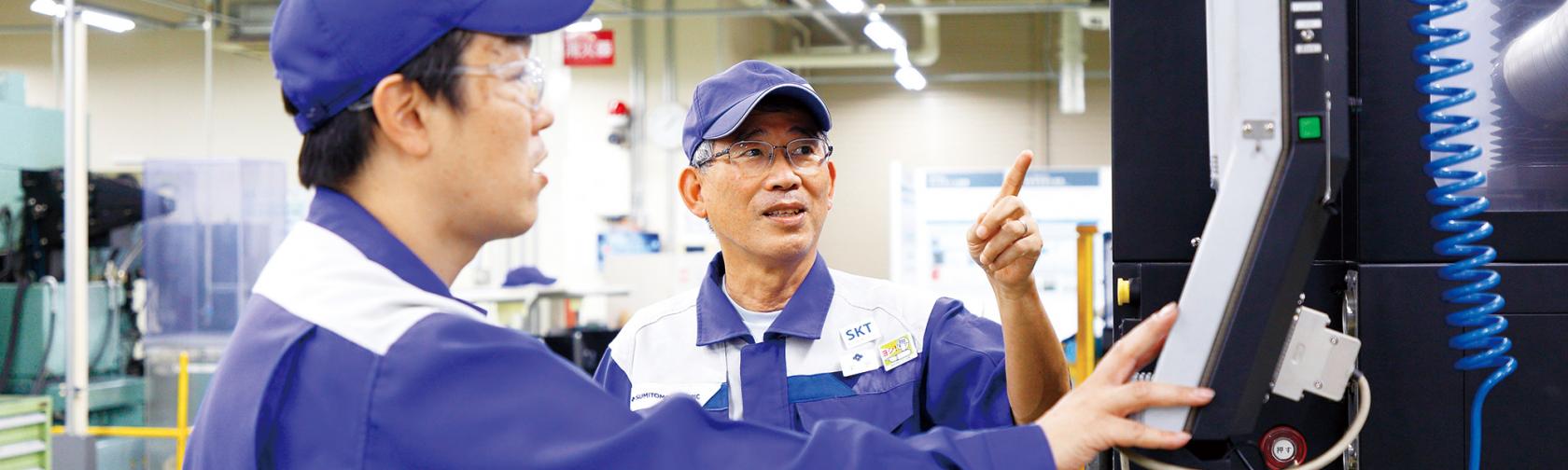