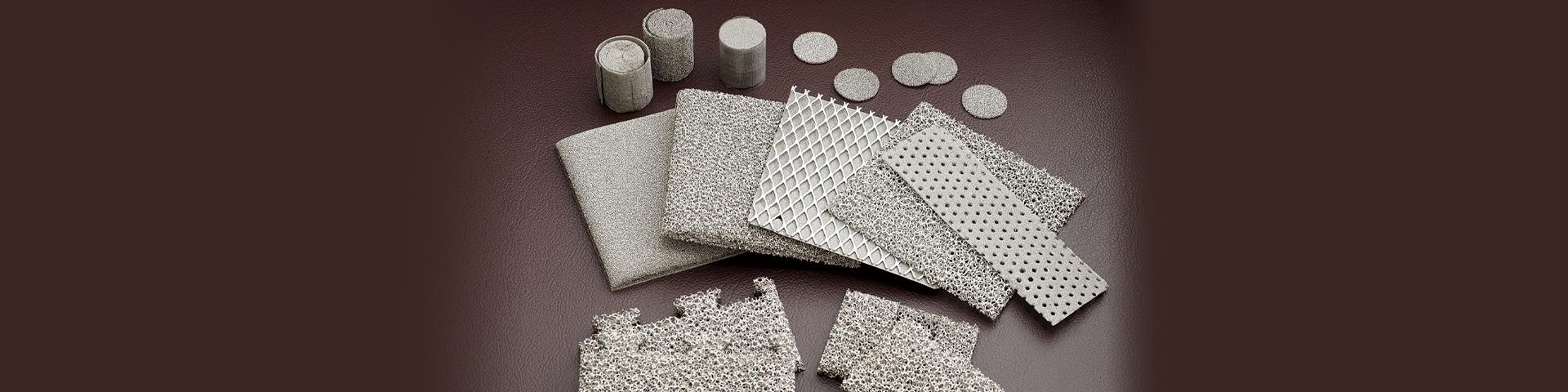
住友電工グループが蓄積してきたモノづくり技術~PC、携帯電話、HEVなど、時代の要請に応じたセルメット®~
気孔率98%の金属多孔体、進められた用途検討
1967年、英国・ダンロップ社で開発された発泡金属が住友電工に紹介された。後に商標登録されるセルメット®である。それは骨格が3次元の網目状の構造になった金属多孔体だった。それまでの構造や製法では気孔率に限界があったが、最大98%の気孔率(全体積に占める空間の割合)という大きな特徴を持っていた。そのため気体や液体が流れやすく、孔の中に大量の物質を充填でき、接する面積も大きい。また、目的に応じた大きさで製造が可能であり、軽量で強度が高いことも従来にはない特徴だった。技術陣は大きな可能性を感じ、1970年から研究開発を開始した。この材料は何に適用できるのかが問題だった。電池や触媒担持体への応用が有望と考えられたが、最初に商品化されたのは、1974年の灯油気化器用部品だった。その後、自動車排気ガス浄化装置触媒担持体としての開発や電池用電極材としての研究開発が進められた。
「連続めっき」の実現、ニッケル水素電池への適用
1976年、家電メーカー向けに電池用電極材を長尺で作るための試作機を導入し、本格的に連続めっきの技術開発がスタート。現在も原型は同じ連続めっき装置が稼働しているが、大小さまざまな改善がされている。設備の稼働により、大幅なコストダウンを実現したことはセルメット®の歴史の中でも画期的だった。
ノートPCや携帯電話の普及に伴い、小型で高エネルギー密度型の充電池(二次電池)開発も活発になっていった。電子機器向けとして、比較的早い段階から使用されるようになったのはニッケル-カドミウム電池であった。当初、ニッケル- カドミウム電池の正極は焼結法で製造された金属多孔体が使用されており、気孔率は最大でも80%程度であった。しかし、電池の高容量化に伴い電極内部になるべくたくさんの活物質を充填する必要が生じたことから、1981年に気孔率の高いセルメット®が初めて採用され、以降順当に置き換えが進展した。
そして、電池の高容量化に伴いニッケル水素電池の電極にもセルメット®が採用され、普及が拡大した。
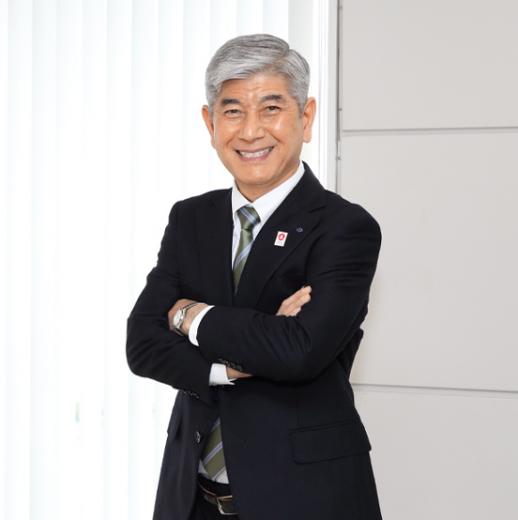
この時期、グループ会社である富山住友電工(株)(以下、富山住友電工)がセルメット®の量産を担うようになる。自動車業界ではエコカーの需要が高まり、1997年、国内自動車メーカーが世界初の水素電池モジュールを搭載したHEVを発売、ニッケル水素電池の集電体としてセルメット®が採用された。この頃、バス・トラックのディーゼル排気ガスフィルターの開発担当だったのが、現在、常務執行役員の斉藤英敏だった。
「性能とコストの面で目途が立たずフィルター開発からは撤退。2001年富山住友電工の技術部に配属されました。当時セルメット®は、主力であった携帯電話やデジカメ用のニッケル水素電池がリチウムイオン電池に置き換わっていき、需要が急減、事業は赤字に転落していました」(斉藤)
事業撤退の声も聞こえる中で、斉藤ら富山住友電工のメンバーが着手したのが徹底したコスト低減プロジェクトだった。携帯電話やデジカメ以外の民生用途でニッケル水素電池は需要があり、海外競合に打ち勝ち、生き延びるにはコスト低減しかなかったのだ。
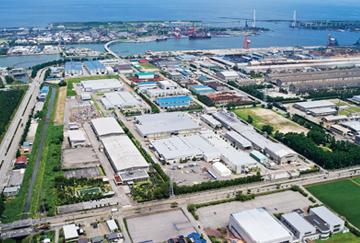
「とにかくみんなからアイディアをもらった。項目を200に細分化し、地道なコスト低減の取り組みを積み重ね、目標を達成することができました。この時の取り組みがセルメット®事業自体の体質を強化し、後年リーマンショック時や東日本大震災時でも継続して黒字を維持することに繋がっていきました」(斉藤)
金属異物の徹底した排除という課題解決の取り組み
当時HEV 向けの1stベンダーは技術面でも優勢、住友電工は2ndベンダーだった。そうした中、セルメット®への金属異物混入が大きな問題となった。セルメット®が採用されている電極に金属粉塵などの異物が付着すると、ショートを起こし電気機能は損失する。製造工程において金属異物を徹底して排除する――富山住友電工一丸となった取り組みが開始された。工場入り口でのエアシャワーおよび手洗い、手袋を作業ごとに取り替えるルール化、確認の見える化を進めた。さらに設備の全部品を総点検、部品の一つひとつまで分析器を用いた成分分析によるチェックを行うなど、徹底した工場管理を実施した。
「このような活動が富山住友電工の強みとなり、お客様から高い評価をいただきました。また工場管理のみならず、MFA(Monozukuri Fundamentals Assessment=製造基盤評価)などの客観的指標で住友電工グループの中でもトップクラスのモノ作り力も高く評価され、コスト削減も奏功しました」(斉藤)
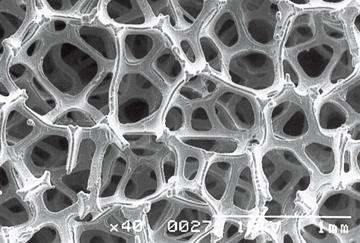
金属異物混入不具合問題において、文字通りお客様に寄り添い課題解決にあたったことで、富山住友電工が1stベンダーに置き換わった。他競合メーカーも撤退、競合が入ってくるたびに、異物対策とコストダウンを強化して入りこめる余地をなくしていった。セルメット®はピーク時の2019年、単月で月産100万㎡の生産を達成した。