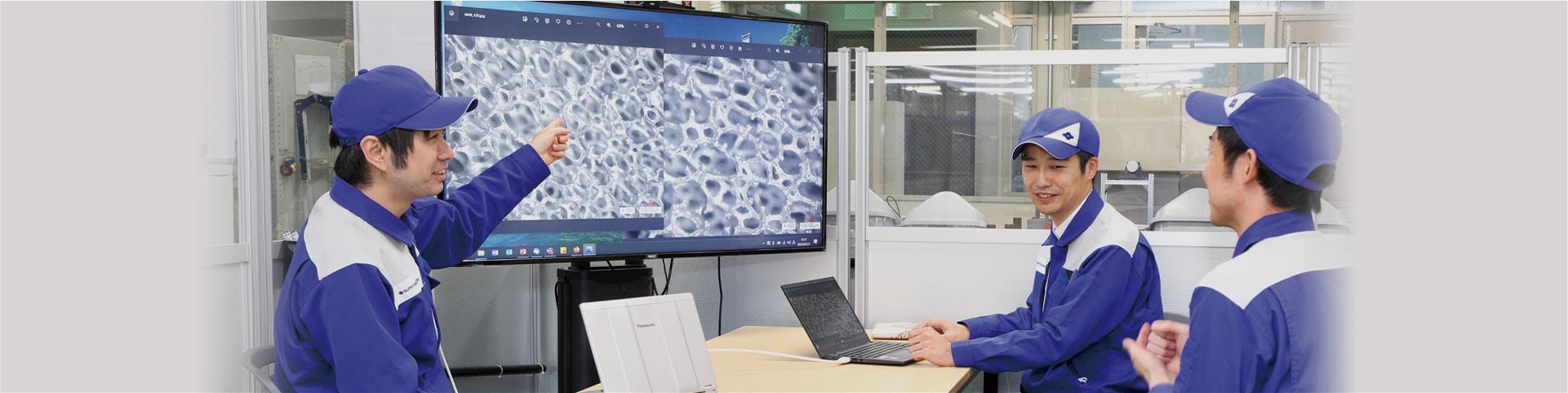
Taking on Challenges to Apply Celmet™ Porous Metal
To bring hydrogen society closer
Celmet™, which contributes to Ni-MH batteries for HEVs
A Japanese automaker became the first in the world to develop an HEV. Both a gasoline engine and an electric motor were installed to drive the vehicle, which was designed to use electricity as much as possible to improve fuel efficiency and reduce CO2 emissions. CelmetTM was used as the material for the Ni-MH battery installed in the HEV. The material contributed to the spread of environmentally friendly HEVs and the reduction of CO2 emissions. Ni-MH batteries are characterized by long service life when they are used in HEVs subject to many chargedischarge cycles. They are also resistant to low temperatures and ensure high levels of safety. The Sumitomo Electric Group has been working to develop hydrogen-based applications by harnessing technologies and production capabilities refined in the development of Ni-MH batteries.
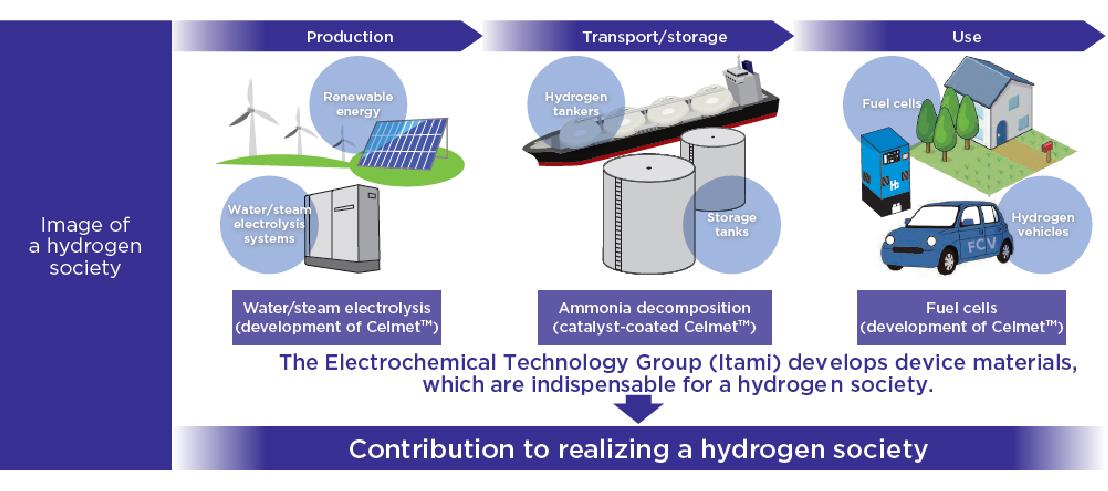
Application to solid oxide fuel cells (SOFCs)
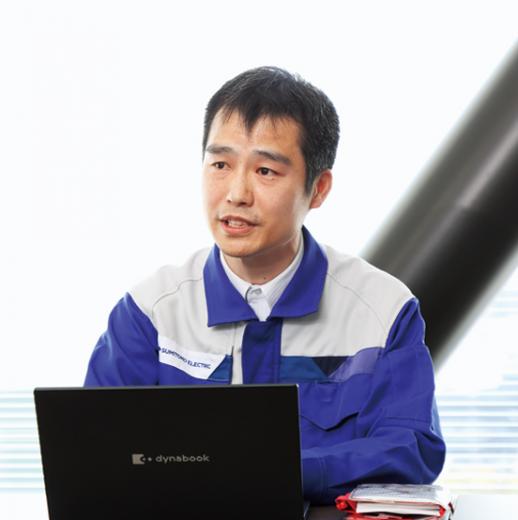
R&D on CelmetTM is conducted by the Electrochemical Technology Group, Metals & Inorganic Materials Dept., Energy & Electronics Materials Laboratory of Sumitomo Electric Industries, Ltd. Kazuki Okuno has been working on the development of CelmetTM for nearly 20 years since he joined the company.
“I started working on CelmetTM in 2005 when defects were occurring due to contamination with metallic foreign matter. After the problem was solved, the use of CelmetTM for HEVs increased rapidly. However, we already had a sense of crisis over the decreasing demand at that time. We started to study new applications in 2008. One of the possible applications was fuel cells to generate electricity using hydrogen,” said Okuno.
There are two ways to generate electricity using hydrogen. One is to use the thermal energy generated during the combustion of hydrogen, and the other is to directly convert hydrogen and oxygen into electrical energy. The latter is the process used in fuel cells, which have attracted public attention due to their high energy conversion efficiency. Home fuel cells are already widely used, and commercial and industrial fuel cells have also started to spread. High expectations are placed on further applications since fuel cells are clean with their only reaction product being water. Notably, solid oxide fuel cells (SOFCs), which operate at high temperatures over 700°C, offer an advantage of eliminating the need for expensive rare materials, including platinum catalysts. Koma Numata works on R&D to apply CelmetTM to current collectors.
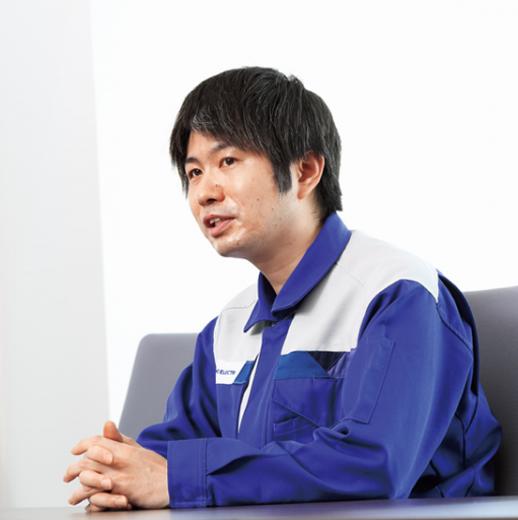
“Flexible current collectors are preferable for SOFCs, so the application of CelmetTM is expected to improve their performance. One problem is that oxidation deterioration is caused by the air that is fed into SOFCs. Development of CelmetTM using nickel-cobalt alloys is under way. The physical properties of cobalt prevent functions such as electrical conduction and gas diffusion from being affected even after oxidation,” said Numata.
The application of CelmetTM to SOFCs is a new challenge in the fuel cell market. Practical application is close at hand due to the cutting of costs through minimization of cobalt use and by optimizing the composition ratio between nickel and cobalt and the CelmetTM structure for gas diffusion.
Application of Celmet™ to hydrogen production systems
Meanwhile, Okuno is responsible for the application of CelmetTM to hydrogen production systems. In these systems, water is electrolyzed to produce hydrogen. R&D is under way to apply porous metals to electrodes for water electrolysis.
“Application of CelmetTM-based electrodes with a high specific surface area will further increase the efficiency of water electrolysis. The bottleneck in water electrolysis is high power consumption. Application of CelmetTM is expected to reduce power consumption for hydrogen production. We hope to lower the water electrolysis voltage by developing nickel surface modification technology,” said Okuno.
As Okuno pointed out, it is an important engineering challenge to increase the efficiency of water electrolysis. High power consumption also affects the running cost and poses a stumbling block in realizing, expanding, and spreading a hydrogen society. In this context, cost reduction in hydrogen production using CelmetTM has attracted much public attention. In Japan, a demonstration project using hydrogen production systems has just begun. The market is expected to start growing rapidly between 2025 and 2030, with market size expanding by factors of ten in the following 20 years. New applications of CelmetTM will emerge in the not-sodistant future.
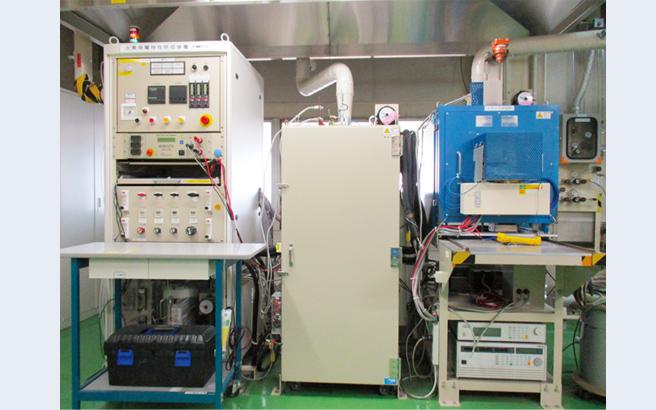
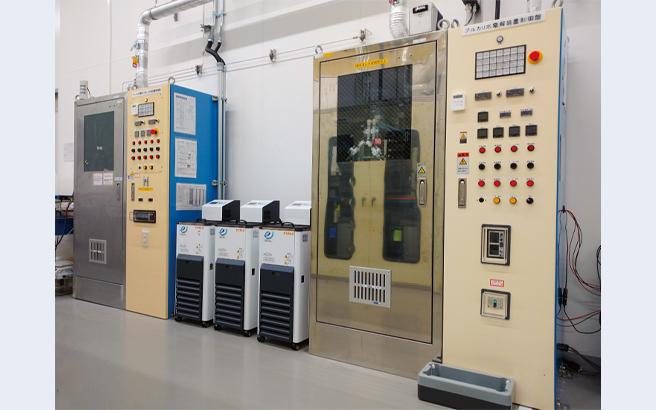
NEXT
Celmet™ Contributing Significantly to the Realization of a Decarbonized Society
– Focusing on “fuel cells” and “hydrogen production systems” –