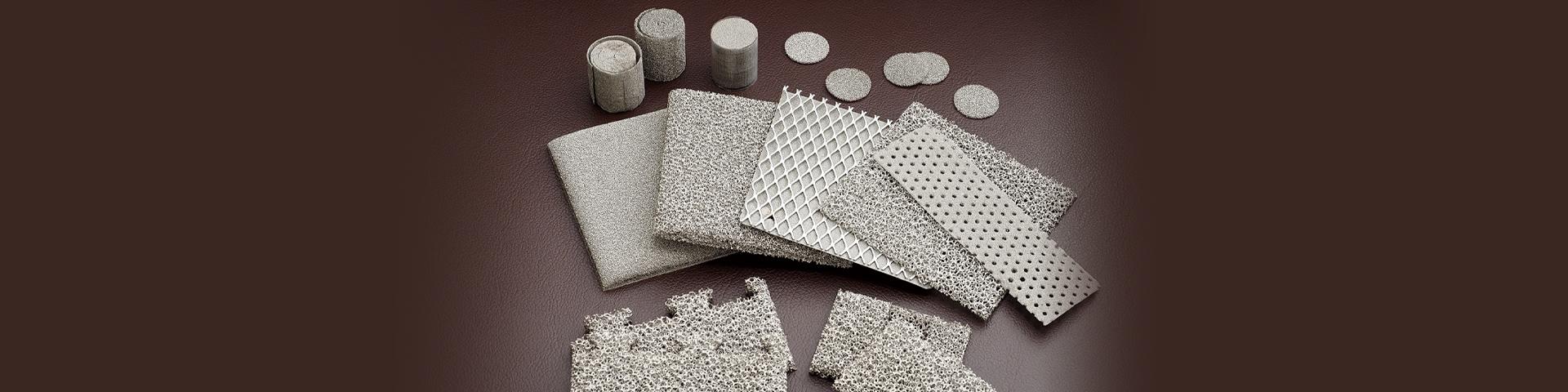
Development of Celmet™ Through Accumulated Manufacturing Technology
Celmet™ meeting the needs of the times, finding applications in PCs, cell phones, and HEVs
Study on applications of a porous metal with a porosity of 98%
In 1967, a metal foam developed by Dunlop, a UK company, was introduced to Sumitomo Electric. This was CelmetTM, whose trademark was later registered by Sumitomo Electric. The porous metal had a frame with a three-dimensional network structure. Conventional structures and manufacturing methods had limits to porosity. CelmetTM, on the other hand, featured porosity (the percentage of pores to the whole volume) of up to 98%. This enabled gases and liquids to flow smoothly, and large amounts of materials to fill the pores. The contact area was also large. Manufacturing in different sizes was possible depending on the purpose. Unlike conventional products, CelmetTM was lightweight and demonstrated high strength. The team of engineers recognized huge potential and started R&D in 1970.
However, there was a question: for what purposes should the groundbreaking material be applied? Amidst the promising outlook for applications in batteries and catalyst supports, in 1974, a component designed for kerosene vaporizers was first brought to market. Subsequently, catalyst supports for automotive exhaust gas purification systems were developed, and R&D efforts were also undertaken to advance electrode materials tailored for batteries.
Achievement of continuous plating and successful application to Ni-MH batteries
In 1976, a prototype machine was introduced to manufacture long electrode materials for batteries, which were delivered to home electronics manufacturers. Development of continuous plating technology was launched on a full scale. Continuous plating systems derived from the same prototype are still in operation, and major and minor kaizen activities have been carried out. Significant cost reduction achieved by the equipment operation was pivotal in the history of CelmetTM.
With the spread of notebook PCs and cell phones, the development of small and high-energy-density rechargeable batteries (secondary batteries) accelerated. For electronic devices, nickel-cadmium (Ni-Cd) batteries came into use at a relatively early stage. At first, porous metals manufactured by the sintering process were used for the positive electrodes of Ni-Cd batteries, but their porosity was only a maximum of around 80%. However, it was necessary to fill the electrodes with as much active materials as possible in line with the higher battery capacity. CelmetTM, which is characterized by high porosity, was used for the first time in 1981. Subsequently, conventional materials were increasingly replaced by CelmetTM.
CelmetTM was also used for the electrodes of Ni-MH batteries in line with the increase in battery capacity, resulting in widespread use of the material.
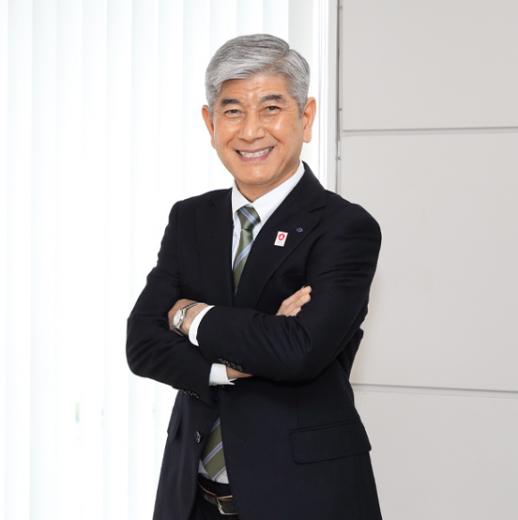
At that time, Sumitomo Electric Toyama Co., Ltd. which is one of the Group companies, started to undertake mass production of CelmetTM. In the auto industry, to meet the growing demand for environment-friendly cars, a Japanese automaker released the world’s first HEV equipped with a hydrogen battery module in 1997. CelmetTM was used for the current collector of the Ni-MH battery. At that time, Hidetoshi Saito, who is currently the Managing Executive Officer, was in charge of the development of diesel exhaust gas filters for buses and trucks.
“Sumitomo Electric withdrew from the development of filters because it was difficult to set a practical goal in terms of performance and cost. In 2001, I was assigned to the Engineering Department of Sumitomo Electric Toyama. At that time, Ni-MH batteries, which were mainly used for cell phones and digital cameras, were increasingly replaced by lithium-ion (Li-ion) batteries, causing demand for CelmetTM to plummet and the business to go into the red,” said Saito.
Despite growing momentum to withdraw from the business, members of Sumitomo Electric Toyama, including Saito, embarked on a project to drastically cut costs. There was demand for Ni-MH batteries in consumer applications other than cell phones and digital cameras. Cost reduction was the only solution to beat foreign competitors and survive.
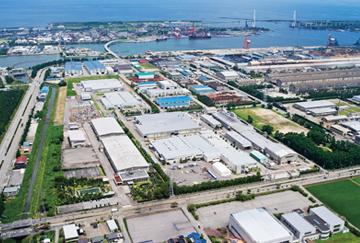
“We solicited ideas from other members anyway. We identified 200 items to be addressed and made steadfast efforts to cut costs. Finally, we were able to attain the goal. This initiative helped strengthen the operations of the CelmetTM business, making it possible to maintain a surplus even after the Lehman Shock and the Great East Japan Earthquake,” said Saito.
Efforts to completely eliminate metallic foreign matter
At that time, the first vendor of HEVs also had an advantage in terms of technology. Sumitomo Electric was the second vendor. Under these circumstances, contamination of CelmetTM with metallic foreign matter emerged as a major problem. Adhesion of foreign matter, including metallic dust, to CelmetTM-based electrodes caused short circuits and loss of electrical function. Sumitomo Electric Toyama launched all-out efforts to completely eliminate metallic foreign matter from its manufacturing process. Rules were established to use an air shower and wash hands at the entrance to the plant and replace gloves for each work step, and the checking process was visualized. In addition, all equipment parts were overhauled, and analyzers were used for component analysis of each part. In this way, exhaustive plant management was conducted.
“These activities gave strengths to Sumitomo Electric Toyama, which was highly evaluated by customers. In addition to outstanding plant management, Sumitomo Electric Toyama was among the best in terms of manufacturing capabilities in the Sumitomo Electric Group based on objective indicators, including Monozukuri Fundamentals Assessment (MFA). The cost reduction efforts were also successful,” said Saito.
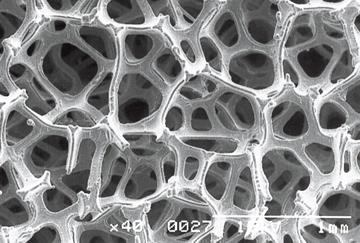
Sumitomo Electric Toyama carefully responded to the needs of customers to cope with defects caused by contamination with metallic foreign matter. The company rose to the top vendor position, causing competitors to withdraw. Each time a new competitor entered the market, Sumitomo Electric Toyama enhanced measures against foreign matter as well as its cost reduction efforts to prevent market penetration. In 2019, production of CelmetTM hit a record high of one million m2 in a single month.
NEXT
Manufacturing Site with the World's Largest Production Capacity for Celmet™
– Sumitomo Electric Toyama’s commitment to manufacturing–