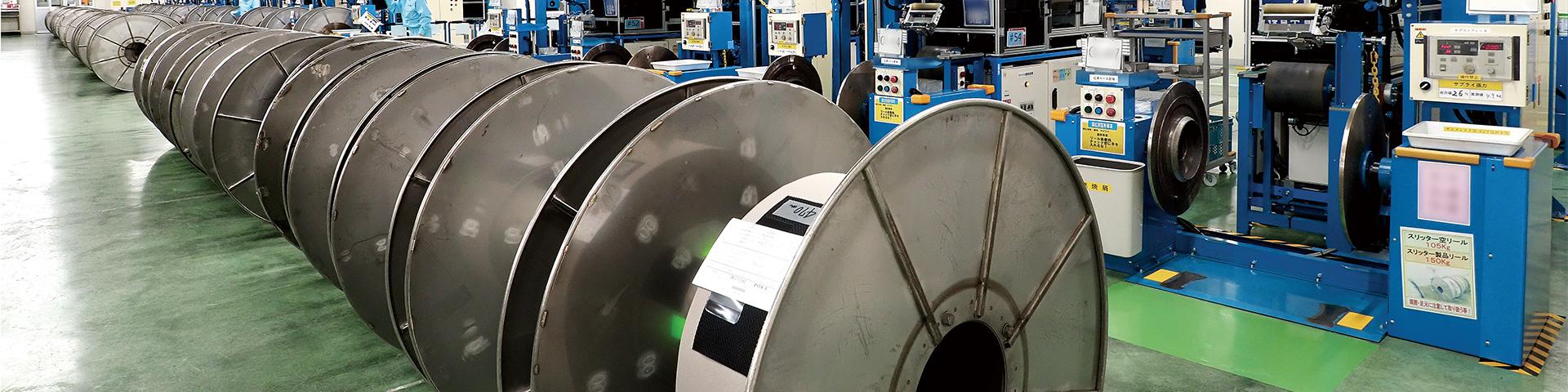
Manufacturing Site with the World's Largest Production Capacity for Celmet™
Sumitomo Electric Toyama’s commitment to manufacturing
Realizing high productivity and quality
Located near Shinminato Port, Toyama Prefecture, Sumitomo Electric Toyama was founded in 1973 with the operation of its aluminum continuous casting and rolling equipment. In the following year, the electric wire plant of Sumitomo Electric Toyama was completed, and it started the manufacture of aluminum high-voltage transmission lines. The company started the manufacture of CelmetTM in 1985 and reinforced the production system in 1994. With CelmetTM being increasingly used for HEVs, the company started to expand its production equipment in 2007. The current production capacity is 800,000 m2 (average monthly production per year), which is the largest in the world.
CelmetTM is manufactured by electroplating nickel on urethane foam, which is the base material. Sumitomo Electric Toyama ensures both productivity and quality by using a two-step plating method, in which a high-speed uniform plating process is followed by a high-quality plating process. Subsequently, urethane and carbon are removed by heat. The thickness is then adjusted, and cutting is performed on the product width. This is how the products are finished. Appearance inspections are conducted to check the total length before shipment.
Realization of innovative “roll-to-roll” equipment
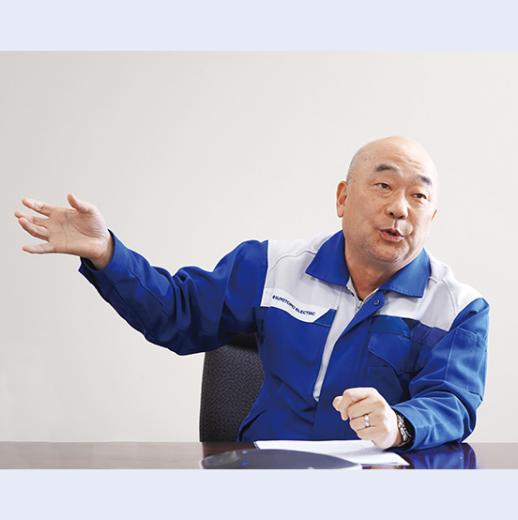
One of the innovative approaches in the series of manufacturing processes was the realization of “roll-to-roll.” Ryuichi Yoshikawa, who is currently a director and the manager of the Manufacturing Department, was involved in this project. He engaged in research on CelmetTM at university. He was told, “If the research is successful, a cell phone will be made to fit into your pocket.” He asked about the manufacturer, and learned that CelmetTM was manufactured by Sumitomo Electric Toyama. Anticipating that demand for CelmetTM would grow, he became motivated to join Sumitomo Electric Toyama.
“After joining the company, I was put in charge of design of the manufacturing equipment. I found that the width of the production equipment was narrow and that the products were manufactured sheet by sheet. I told my supervisor that the productivity was low and loss was high. I proposed launching an “innovative project” to solve the problem, and the prototype of the current equipment configuration was developed. The objective was to expand the width of the raw material to one meter and develop “roll-to-roll” equipment, from plating to heat treatment to the inspection process. It was extremely difficult to design the continuous winding of CelmetTM, a lightweight material, on a reel. Increased width would result in breakage, resulting in unsmooth flow. I asked for advice from other members, and spent about two years trying to achieve a stable product flow,” said Yoshikawa.
Various measures were implemented to achieve low-tension transfer, design a system with fewer bends, and develop control to achieve low-tension regular winding and high-speed meandering. These efforts enabled us to build equipment capable of continuous production of the entire process.
Allocating resources to enhance the BCP to avoid the risk of disruption of operations
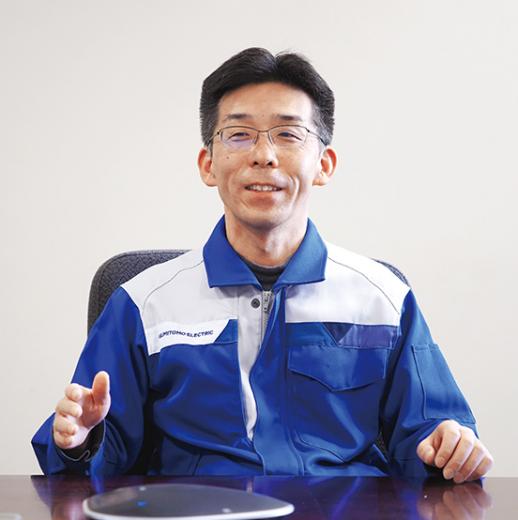
Tadashi Omura, who is currently the manager of the Quality Assurance Department, has been in charge of production engineering of CelmetTM since he joined the company. Omura, who was also in charge of customer relations, took the initiative to implement measures against contamination with metallic foreign matter.
“We implemented exhaustive measures to minimize contamination with metallic foreign matter in production equipment and prevent dust from being brought into the plant. We removed all possible risks, and the number of defects caused by contamination decreased steadily. I hope to ensure stable delivery of highquality CelmetTM to customers through in-house cooperation and collaboration with raw material manufacturers,” said Omura.
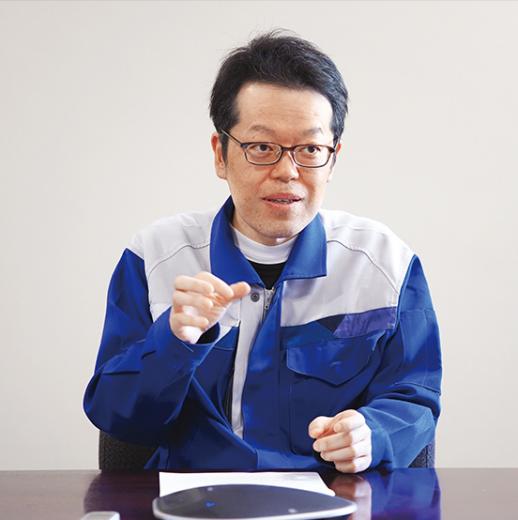
Junichi Nishimura, who is currently the manager of the Electronic Materials Plant (CelmetTM Plant), started to work on CelmetTM when this material came into use for in-vehicle batteries.
“I clearly remember the days when a problem occurred at a raw material supplier. We worked on site at a different supplier to start production. We demonstrated teamwork, which developed as we took measures against contamination with metallic foreign matter. This reminded me of the importance of business continuity planning (BCP). As the plant manager, I allocate resources to enhancing our BCP while always keeping in mind the risk of disruption of operations due to contingency,” said Nishimura.
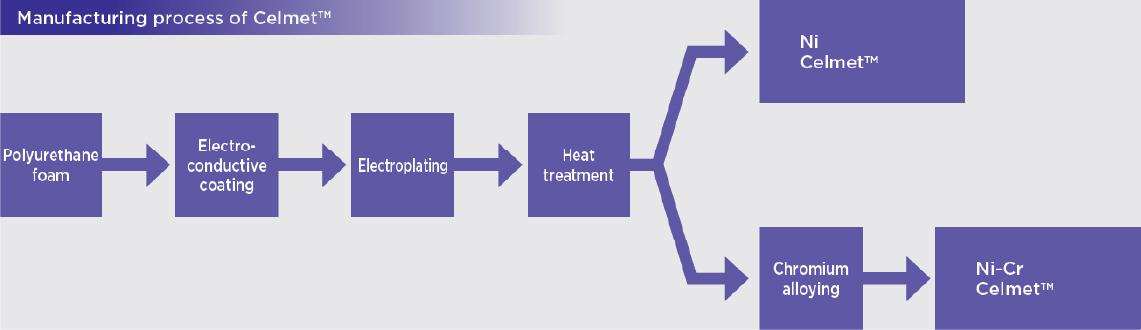
Raising the global profile and establishing a unique presence
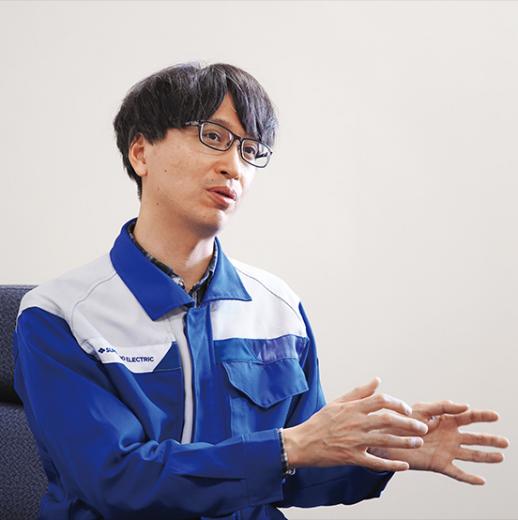
Efforts have been made to develop new technologies for CelmetTM for HEVs. The person in charge is Kengo Tsukamoto, who is the chief of the Electronic Materials Engineering Section. He works with Sumitomo Electric to develop a new CelmetTM for Ni-MH batteries.
“I am currently working on a project to improve the performance of CelmetTM, whose mass production will start in two years. We also make proposals by offering samples for fuel cells and hydrogen production systems. The CelmetTM business is at a turning point, which we hope to leverage as an opportunity,” said Tsukamoto.
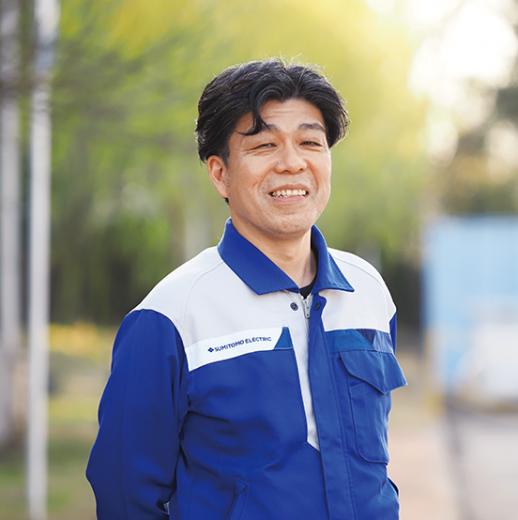
Hitoshi Tsuchida, who is a director and the manager of the Engineering Department, led the CelmetTM production at Sumitomo Electric Toyama from an early stage.
“CelmetTM has various functions, including shielding performance and sound absorption. These functions are integrated into a single material. However, it is difficult to match such versatile functions with customers. Our predecessors underwent twists and turns until the material was used for batteries. CelmetTM has achieved success because we were able to overcome difficulties with reliable partners and suppliers. It is essential to build good relationships to share a vision to deliver good products. We have strengths in such overall capabilities. There are many challenges in the new deployment to hydrogen, but I hope to raise the global profile of CelmetTM and establish its dominant and unique presence,” said Tsuchida.
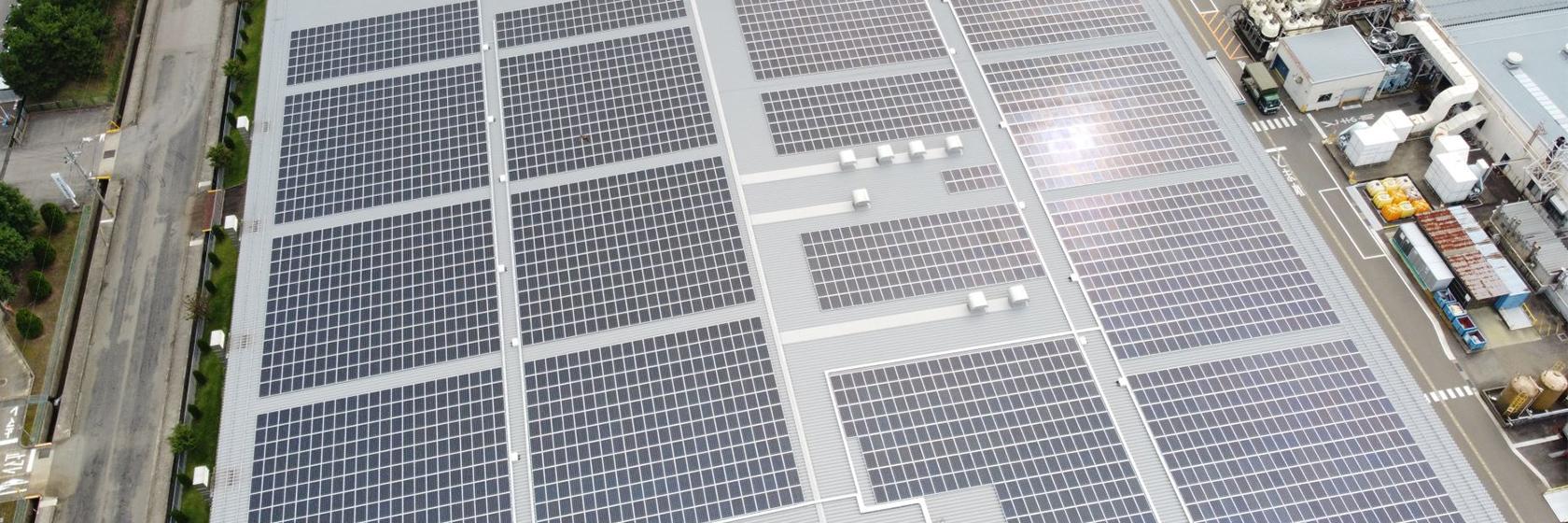