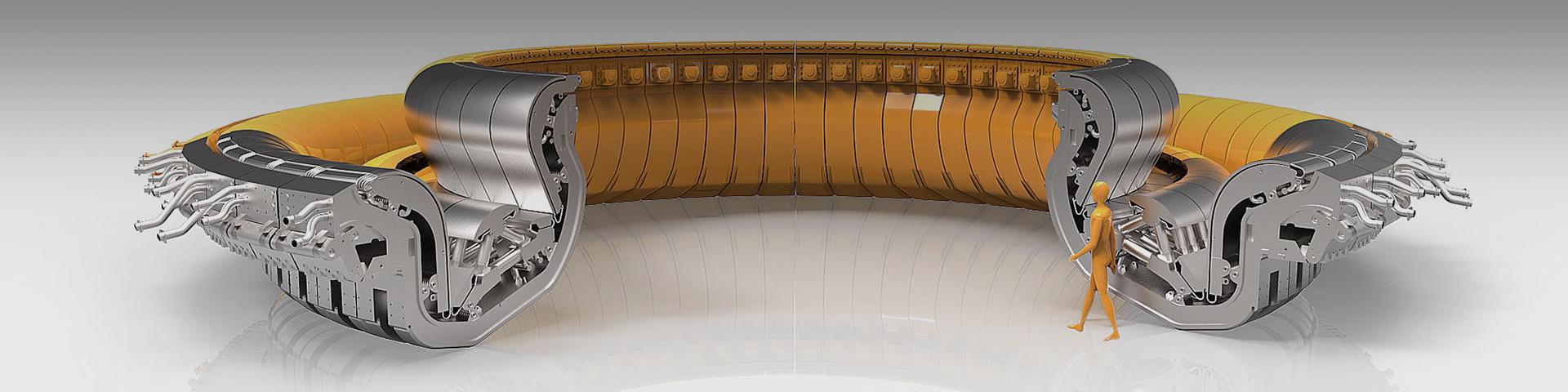
Unbreakable Tungsten Monoblock
Overview of a divertor (The connected units form a huge ring) ©ITER Organization
Efforts toward the one and only excellent durability
Nurtured powder metallurgy and hot working techniques
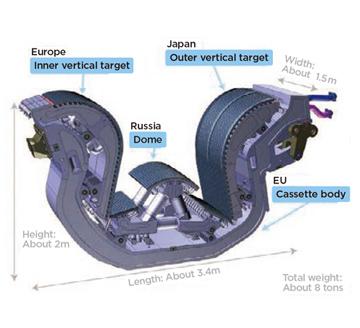
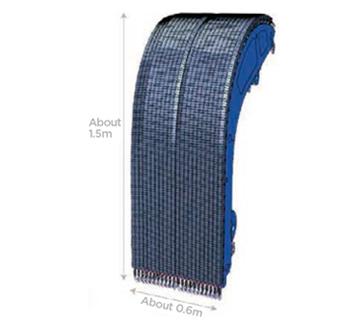
A.L.M.T. Corp. was formed through the merger of Tokyo Tungsten Co., Ltd. and Osaka Diamond Industrial Co., Ltd. in 2000. Since then, as a Sumitomo Group company in the industrial materials segment, it has been focusing on two businesses: the manufacture of high-melting-point metallic materials and of diamond precision tools. Regarding tungsten, its strength is sufficient to handle the entire process from refinement to final products. It has enjoyed a long business relationship with QST, and had a connection with the former Japan Atomic Energy Research Institute. Since 1999, it has researched and developed tungsten for ITER. Tungsten has the highest melting point among all metals and lower thermal expansion coefficient, and excellent shape stability even in ultrahigh- temperature environments. The powder metallurgy technique (powder pressing and sintering) and hot working technique nurtured by A.L.M.T. Corp. for a long time exploit the full potential. These techniques have produced unbreakable tungsten, leading to its adoption in divertors.
Let's look at the structure of a divertor. A divertor consists of a cassette body (support structure) manufactured in Europe, an outer vertical target manufactured in Japan, an inner vertical target manufactured in Europe, and a dome manufactured in Russia. The heat-receiving surface of the outer vertical target is made of tungsten material, called a monoblock, with dimensions of around 30 × 30 × 10 mm. About 20 rows of monoblocks with skewered cooling tubes are arranged per cassette body. The total number of monoblocks of the outer vertical targets arranged on a total of 54 cassette bodies installed at the bottom of a vacuum chamber is about 200,000. If only one surface is melted due to the heat load, the cooling tube might break. This means that only the high durability of all of the monoblocks exposed to plasma for a long time can sustain a nuclear fusion reaction for a long time. A.L.M.T. Corp. has applied its strength of powder metallurgy technology to develop excellent thermal-shock-resistant tungsten material, or unbreakable tungsten.
Suppressing grain growth under high temperature
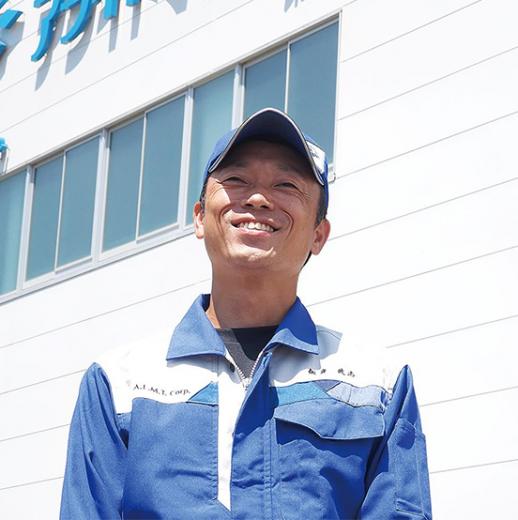
Takeshi Iikura, who is the manager of the ITER Engineering Group, Engineering Dept. and has been engaged in the production engineering of tungsten monoblocks in the Working Engineering Group, Thermal Management Div. (Sakata Works), has participated in the ITER project since his second year at the Company in 2013. At that time, he developed tungsten plates for monoblocks in the Material Engineering Group at the Toyama Works. The year 2013 was also the year when tungsten was determined to be adopted in divertors.
“To manufacture tungsten plates, tungsten powder is processed into a pressed body, sintering is performed, and then the obtained sintered body is subjected to plastic deformation. When a tungsten material after plastic deformation is exposed to a plasma temperature of above 2,000°C for a long time, new grains may be produced and grow (recrystallization), resulting in swells or cracks. To improve durability against heat load, it was considered effective to minimize the recrystallization grain growth. We aimed to maintain fine recrystallization grains,” said Iikura.
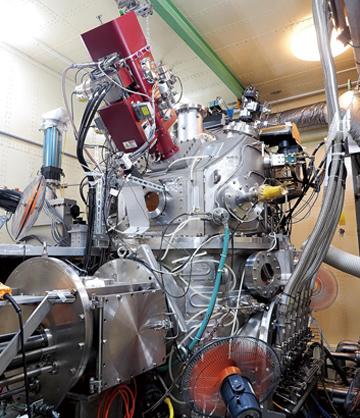
The key point was plastic deformation, in other words, the rolling process. The rolling process is to heat and pressurize material for deformation. Optimum conditions and parameters of heat and pressure were determined to maintain fine recrystallization grains after one year or more of trial manufacture, resulting in a new tungsten manufacturing method.
“We manufactured tungsten monoblocks for heat flux tests using the newly developed plates, and conducted heat flux tests using the equipment owned by QST. The tungsten monoblocks were exposed to an electron beam equivalent to about 2,300°C for 10 seconds, and cooled for 10 seconds. This cycle was repeated 1,000 times (over three times the number of cycles of the ITER design requirements). The monoblock fabricated from the conventional tungsten exhibited swells on the heat load surface, while no swells were observed in the newly developed products. By maintaining fine recrystallization grains, the monoblocks exhibited performance suitable for a divertor,” said Iikura.
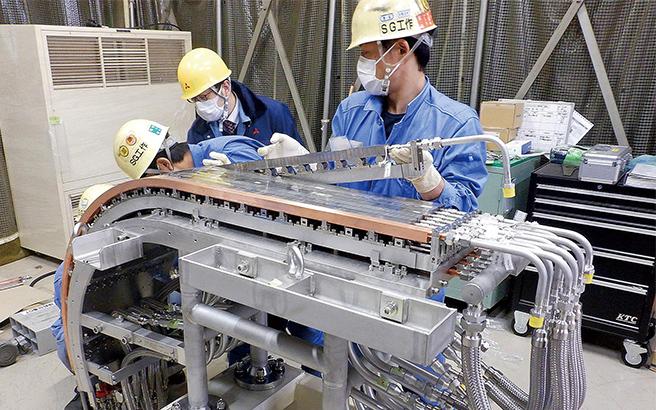
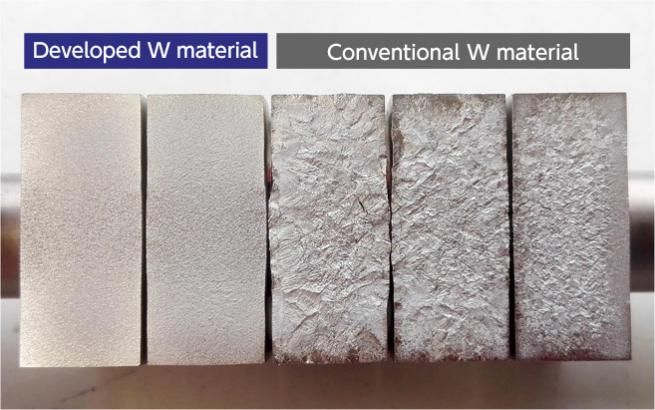
Globally evaluated unbreakable tungsten
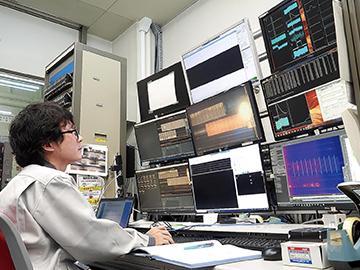
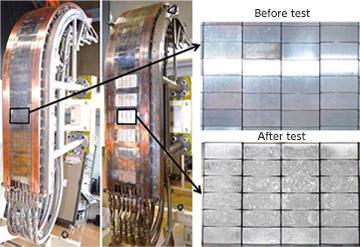
Then Iikura and the other members evaluated prototypes for outer vertical targets using developed tungsten monoblocks. The evaluation comprised highheat flux tests at the Efremov Scientific Research Institute in Russia, in the presence of staff of the ITER Organization and QST. The tests were conducted based on numbers of cycles far exceeding the ITER requirements, and no cracks were observed in any of the monoblocks, demonstrating superb durability. The material achieved the first international recognition as unbreakable tungsten and was certified as the tungsten material for divertors by the ITER Organization and QST. At this moment, only A.L.M.T. Corp. can supply unbreakable tungsten. The excellent working technique nurtured by A.L.M.T. Corp. is also used for the machining of the very complex shapes of the outer vertical target, which requires high precision in the order of 10 μm. Iikura, who is engaged in the production engineering of monoblocks at the Sakata Works, visited the ITER construction site in France in 2018.
“The ITER project is an international megaproject that involves many countries. It is certainly ambitious and could yield a potential solution to energy and environmental problems. I am happy and proud to be one of the engineers in charge, and am eager to solve any issues that arise,” said Iikura.
NEXT
Optimizing Production of Monoblocks and Tungsten Material
– Accelerating the buildup of the supply system for the world –